- お役立ち記事
- Purchasing lead time management method essential for stabilizing production plans
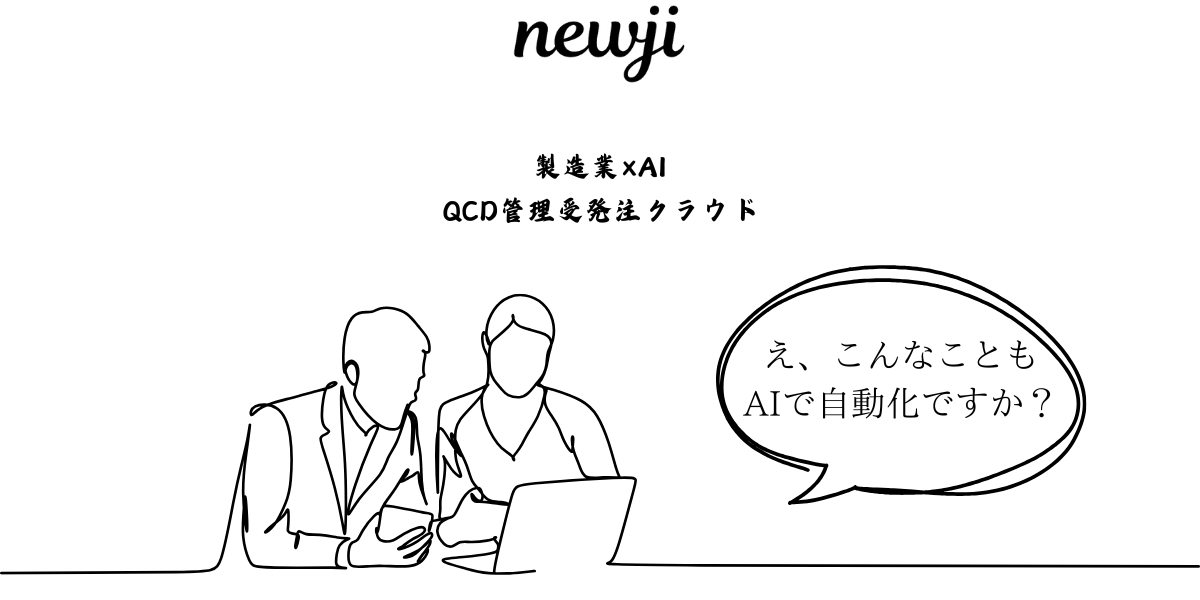
Purchasing lead time management method essential for stabilizing production plans
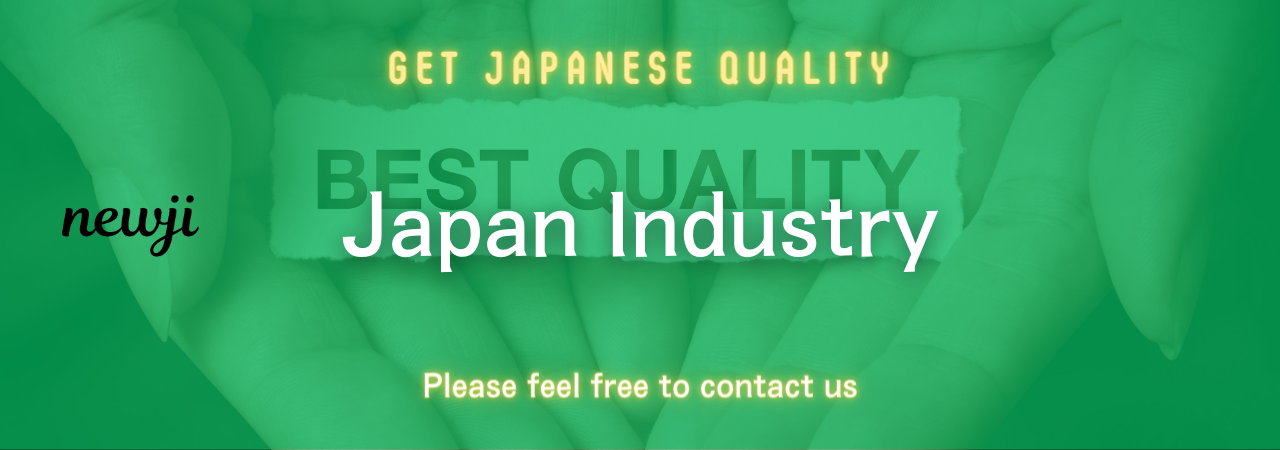
目次
Understanding Lead Time in Production
In the world of production and manufacturing, the term “lead time” is crucial.
It refers to the amount of time it takes from when an order is placed until it is received and ready for use in production.
Effective lead time management is essential for maintaining a consistent production flow and ensuring timely delivery of finished goods.
Lead time can significantly impact a company’s ability to meet its production goals.
It affects inventory levels, resource allocation, and even customer satisfaction.
Therefore, understanding and managing lead time is vital for any business involved in manufacturing.
The Importance of Purchasing Lead Time
Purchasing lead time specifically focuses on the period needed to acquire materials or components necessary for production.
This timeframe can vary greatly depending on several factors, including supplier location, order size, and current market conditions.
By accurately predicting and managing purchasing lead time, companies can avoid potential disruptions to their production schedules.
If not properly managed, purchasing lead time can lead to delays, increased costs, and lost revenue.
Companies might face stockouts or excess inventory, both of which can be detrimental to the bottom line.
For this reason, having a clear understanding of purchasing lead time is vital for maintaining efficiency in the production process.
Strategies for Effective Lead Time Management
To stabilize production plans, companies must implement effective strategies for managing lead time.
Here are some methods that can help in achieving this goal.
1. Building Strong Supplier Relationships
A solid relationship with suppliers is the cornerstone of effective lead time management.
By fostering open communication and trust with suppliers, companies can often negotiate better terms and more reliable delivery schedules.
Regular communication helps in anticipating potential disruptions and addressing them proactively.
Additionally, having multiple suppliers for critical components can provide flexibility and mitigate the risk of delays from any single source.
Diversifying the supplier base ensures that a company is not overly reliant on a single supplier, which can be a weak link in the supply chain.
2. Implementing Advanced Planning Systems
Technology plays a crucial role in lead time management.
Advanced planning and scheduling (APS) systems can predict lead times more accurately by analyzing historical data and current market trends.
These systems help in optimizing production schedules and inventory levels, ensuring that materials are available when needed without excess stock.
By integrating APS systems with the company’s existing enterprise resource planning (ERP) software, businesses can gain real-time insights into their supply chain.
This integration allows for quick adjustments to production plans to accommodate changes in lead time.
3. Using Data and Analytics
Data analytics is another powerful tool to improve lead time management.
By analyzing lead time data, companies can identify patterns, trends, and bottlenecks in their supply chain.
Understanding these elements enables businesses to make informed decisions and implement process improvements where necessary.
Predictive analytics can also be used to forecast future lead times based on various factors, such as seasonal demand fluctuations or economic changes.
Being proactive rather than reactive can significantly improve the stability of production plans.
4. Streamlining Internal Processes
Efficiency within internal processes also plays a crucial role in managing lead time.
Streamlining operations by reducing unnecessary steps or automating certain tasks can shorten the overall lead time, allowing production to commence more swiftly once materials arrive.
Conducting regular process audits can help identify inefficiencies or areas for improvement within the company’s operations.
By continually optimizing these processes, businesses can better control the variables that contribute to lead time.
Benefits of Effective Lead Time Management
Proper lead time management has numerous benefits that extend beyond the production floor.
It leads to increased customer satisfaction by ensuring that products are delivered on time and to specification.
Satisfied customers are more likely to become repeat buyers and recommend the company to others, driving growth and profitability.
Efficient lead time management also reduces costs related to storage, handling, and waste.
By aligning inventory levels more closely with production needs, companies can minimize the expense of excess stock or the penalties associated with stockouts.
Additionally, a well-managed lead time improves the predictability of production schedules, allowing companies to allocate resources more efficiently and reduce downtime.
This reliability enhances the overall competitiveness of the business in the marketplace.
Challenges in Managing Lead Time
Despite the strategies available, managing lead time does not come without its challenges.
Global supply chains are increasingly complex, and external factors such as geopolitical events, natural disasters, or pandemics can disrupt even the best-laid plans.
Companies must remain agile and adaptable to navigate these uncertainties.
Investing in risk management strategies and maintaining a crisis response plan are essential components of a robust lead time management approach.
Additionally, involving stakeholders from various departments—such as procurement, production, and logistics—in the planning process ensures that all aspects of the supply chain are considered and addressed.
Conclusion
Purchasing lead time management is essential for the stability of production plans.
By understanding the nuances of lead time and implementing effective management strategies, companies can enhance their operational efficiency and better serve their customers.
Through strong supplier relationships, advanced planning systems, data analytics, and streamlined processes, businesses can achieve a balanced and predictable lead time.
This balance ultimately leads to reduced costs, increased customer satisfaction, and greater market competitiveness.
In a world where time is of the essence, mastering lead time management is a key factor in driving success for any production-oriented business.
資料ダウンロード
QCD調達購買管理クラウド「newji」は、調達購買部門で必要なQCD管理全てを備えた、現場特化型兼クラウド型の今世紀最高の購買管理システムとなります。
ユーザー登録
調達購買業務の効率化だけでなく、システムを導入することで、コスト削減や製品・資材のステータス可視化のほか、属人化していた購買情報の共有化による内部不正防止や統制にも役立ちます。
NEWJI DX
製造業に特化したデジタルトランスフォーメーション(DX)の実現を目指す請負開発型のコンサルティングサービスです。AI、iPaaS、および先端の技術を駆使して、製造プロセスの効率化、業務効率化、チームワーク強化、コスト削減、品質向上を実現します。このサービスは、製造業の課題を深く理解し、それに対する最適なデジタルソリューションを提供することで、企業が持続的な成長とイノベーションを達成できるようサポートします。
オンライン講座
製造業、主に購買・調達部門にお勤めの方々に向けた情報を配信しております。
新任の方やベテランの方、管理職を対象とした幅広いコンテンツをご用意しております。
お問い合わせ
コストダウンが利益に直結する術だと理解していても、なかなか前に進めることができない状況。そんな時は、newjiのコストダウン自動化機能で大きく利益貢献しよう!
(Β版非公開)