- お役立ち記事
- Purchasing planning and schedule management to achieve short lead time procurement
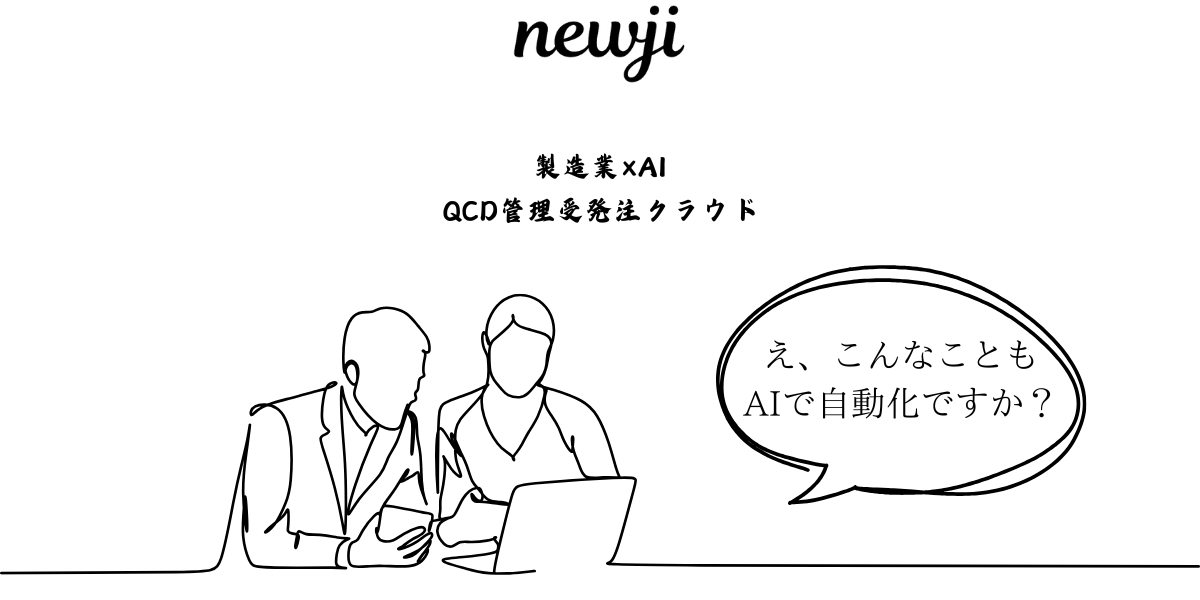
Purchasing planning and schedule management to achieve short lead time procurement
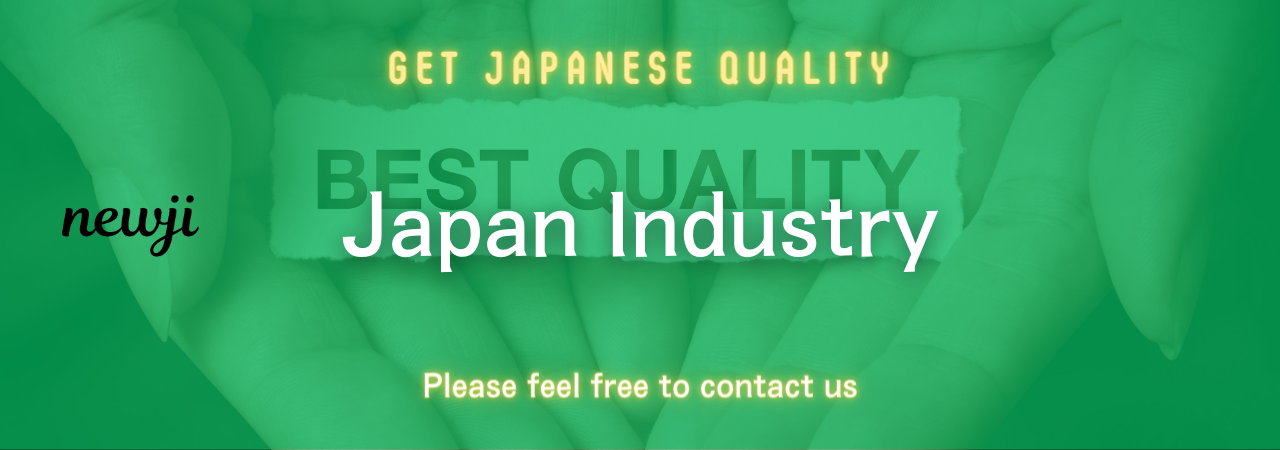
In today’s fast-paced business environment, achieving shorter lead times in procurement is crucial for companies aiming to stay competitive.
This involves effective purchasing planning and meticulous schedule management, two key components that can significantly impact a company’s operational efficiency and customer satisfaction.
In this article, we will explore the strategies and best practices for purchasing planning and schedule management that help achieve short lead time procurement.
目次
Understanding Lead Time in Procurement
Lead time in procurement refers to the total time required from placing a purchase order to the delivery of goods or services.
This time frame includes several stages such as identifying the need, selecting suppliers, negotiating terms, manufacturing, and shipping.
Understanding and managing each of these stages effectively can help in reducing lead times significantly.
Importance of Short Lead Times
Short lead times are critical for maintaining competitive advantage, especially in industries where customer demand can be unpredictable.
With shorter lead times, businesses can respond more quickly to market changes, reduce inventory costs, and improve customer satisfaction by meeting delivery expectations.
Moreover, efficient lead times help in minimizing storage needs and optimizing the supply chain.
Key Elements of Purchasing Planning
Purchasing planning involves a well-organized approach to buying goods and services necessary for the company’s operations.
Key elements include demand forecasting, supplier selection, and inventory management.
Demand Forecasting
Accurate demand forecasting is the foundation of effective purchasing planning.
By predicting future customer requirements, companies can plan their orders efficiently, avoiding overstocking or stockouts.
Utilizing historical data, market analysis, and advanced analytics can improve forecasting accuracy, leading to better purchasing decisions.
Supplier Selection
Choosing the right suppliers is crucial for reducing lead times.
Conducting thorough assessments of suppliers’ delivery performance, reliability, and quality are essential.
Building strong relationships and ensuring clear communication can enhance collaboration, resulting in more favorable terms and faster service.
Inventory Management
Effective inventory management is another critical component in purchasing planning.
Maintaining optimal inventory levels requires balancing carrying costs with availability to meet demand.
Implementing tech solutions like inventory management software can lead to more precise tracking and forecasting, further reducing lead times.
Schedule Management for Shorter Lead Times
Schedule management focuses on organizing tasks and activities to ensure timely completion of procurement processes.
Process Mapping
Process mapping involves a thorough analysis of all steps in the procurement cycle, identifying bottlenecks and inefficiencies.
Documenting each stage helps in understanding the flow and pinpointing areas that require improvement.
This understanding is vital for developing strategies that streamline operations, resulting in shorter lead times.
Prioritizing Orders
Not all orders are equal.
By prioritizing critical orders and projects, companies can allocate resources more effectively to ensure these key items are fulfilled promptly.
Implementing a priority matrix can help in determining which orders demand immediate attention.
Utilizing Technology
Incorporating technology into procurement processes is a powerful way to manage schedules more effectively.
Automation tools can handle routine tasks, reducing the manual workload and minimizing human errors.
Moreover, technologies like AI and IoT provide real-time data and insights, improving decision-making and responsiveness.
Continuous Improvement and Feedback
Regularly reviewing performance and outcomes can drive improvements in schedule management.
Gathering feedback from all stakeholders, including suppliers and customers, provides valuable insights into potential areas for enhancement.
Implementing a culture of continuous improvement encourages innovation and adaptability, essential for sustaining short lead times.
Challenges in Achieving Short Lead Times
While striving for short lead times is beneficial, several challenges can arise along the way.
Supplier Constraints
Suppliers may face their own constraints such as capacity limits or unexpected disruptions, impacting delivery times.
Maintaining an open line of communication and having contingency plans can mitigate these issues.
Quality vs. Speed Dilemma
Rushing procurement processes may compromise quality.
Balancing speed with maintaining high standards requires careful planning and adherence to best practices.
Changing Market Conditions
Volatile market conditions, such as fluctuating demands or economic shifts, can complicate lead time management.
Agility and flexibility in procurement strategies are vital to adapt to these changes swiftly.
Conclusion
Purchasing planning and schedule management are integral to achieving short lead time procurement.
By focusing on accurate demand forecasting, strategic supplier selection, efficient inventory management, and leveraging technology, companies can streamline their procurement cycles, reduce lead times, and improve overall operational efficiency.
Continuous improvement and adapting to market conditions are crucial for maintaining this efficiency and ensuring long-term success.
資料ダウンロード
QCD調達購買管理クラウド「newji」は、調達購買部門で必要なQCD管理全てを備えた、現場特化型兼クラウド型の今世紀最高の購買管理システムとなります。
ユーザー登録
調達購買業務の効率化だけでなく、システムを導入することで、コスト削減や製品・資材のステータス可視化のほか、属人化していた購買情報の共有化による内部不正防止や統制にも役立ちます。
NEWJI DX
製造業に特化したデジタルトランスフォーメーション(DX)の実現を目指す請負開発型のコンサルティングサービスです。AI、iPaaS、および先端の技術を駆使して、製造プロセスの効率化、業務効率化、チームワーク強化、コスト削減、品質向上を実現します。このサービスは、製造業の課題を深く理解し、それに対する最適なデジタルソリューションを提供することで、企業が持続的な成長とイノベーションを達成できるようサポートします。
オンライン講座
製造業、主に購買・調達部門にお勤めの方々に向けた情報を配信しております。
新任の方やベテランの方、管理職を対象とした幅広いコンテンツをご用意しております。
お問い合わせ
コストダウンが利益に直結する術だと理解していても、なかなか前に進めることができない状況。そんな時は、newjiのコストダウン自動化機能で大きく利益貢献しよう!
(Β版非公開)