- お役立ち記事
- Purchasing planning to “shorten lead time”—How to create an efficient procurement schedule
月間76,176名の
製造業ご担当者様が閲覧しています*
*2025年3月31日現在のGoogle Analyticsのデータより
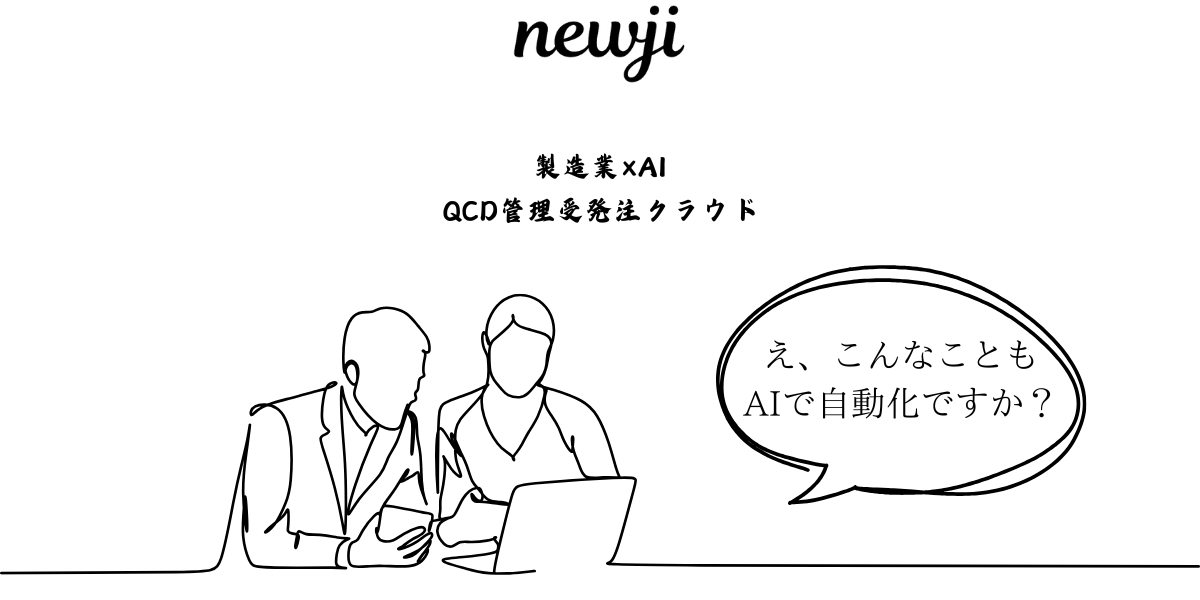
Purchasing planning to “shorten lead time”—How to create an efficient procurement schedule
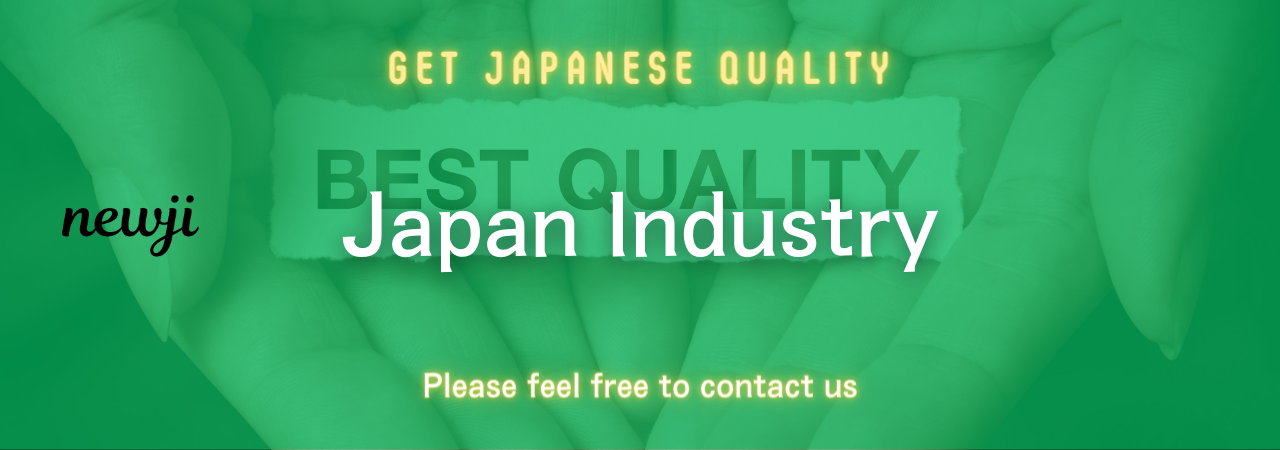
目次
Understanding Lead Time and Its Importance
Lead time is the total time taken from the initiation of a process to its completion.
In the realm of procurement, it refers to the time between placing an order and receiving the goods.
Reducing lead time is crucial for businesses aiming to improve efficiency and customer satisfaction.
A shorter lead time means that a company can respond more quickly to market demands and reduce inventory costs.
It also minimizes the risk of stockouts and enhances the company’s ability to adapt to changes.
Thus, efficient lead time management in procurement planning is essential for overall operational success.
Steps to Shorten Lead Time in Procurement
1. Clarifying Demand and Forecasting Accurately
The first step to shortening lead time is to have a clear understanding of demand.
Accurate forecasting helps in planning procurement schedules that align with production needs.
Using historical data, market trends, and analytics can significantly enhance forecasting accuracy.
Start by analyzing past sales data and current market conditions.
By doing so, you can identify patterns and predict future demand.
Incorporating technology like AI and machine learning can also improve forecasting by providing more precise insights.
2. Building Strong Supplier Relationships
Strong relationships with suppliers can accelerate the procurement process.
Communicate regularly and openly with your suppliers to ensure they understand your needs and constraints.
Work together to streamline and optimize delivery schedules, renegotiate terms, and decide on preferred shipping and packaging methods.
By establishing trust and transparency, you can create a more flexible and responsive supply chain.
3. Investing in Technology and Automation
Implementing technology solutions can dramatically reduce lead time by streamlining various procurement processes.
Use procurement software to automate tasks such as order processing, inventory management, and vendor management.
These tools offer real-time tracking of goods, transparent communication, and streamlined workflows.
Integrated systems enable quicker decision-making and help to identify bottlenecks in the supply chain.
4. Optimizing Inventory Management
Efficient inventory management helps reduce lead time by ensuring that you always have the right amount of stock at the right time.
Implement techniques like Just-in-Time (JIT) inventory systems to manage stock levels efficiently.
JIT systems help minimize inventory costs while ensuring that suppliers deliver parts just when they are needed.
Regularly analyze inventory levels and adjust reorder points based on current demand forecasts.
5. Improving Internal Processes
Look inside your organization for opportunities to enhance operational efficiency.
Streamline every step of your internal procurement process, from purchase orders to invoicing.
Encourage cross-departmental collaboration to ensure that all teams work together towards the same goals.
Implementing standard operating procedures (SOPs) and conducting regular process audits can identify inefficiencies.
6. Diversifying the Supplier Base
Limiting your reliance on a single supplier can pose risks and lengthen lead times.
Explore multiple suppliers who can meet your quality and delivery requirements.
A diversified supplier base can mitigate disruptions and provide leverage during negotiations.
When one supplier is unavailable or unable to meet demands, another supplier can step in.
7. Assessing and Managing Risks
Risk management is crucial in reducing lead time.
Identify potential risks in the supply chain and create contingency plans to mitigate them.
Consider risks such as geopolitical instability, transportation issues, and changes in regulatory requirements.
Regular risk assessments will prepare your business to handle sudden disruptions efficiently.
Benefits of Shortening Lead Time in Procurement
Reducing lead time results in numerous benefits.
First, it enhances customer satisfaction by enabling faster delivery of products.
Satisfied customers are more likely to return and become repeat buyers.
A short lead time also leads to better cash flow management.
By reducing the time goods are held in storage, companies can lower carrying costs and free up capital for other investments.
Additionally, a reduced lead time boosts a company’s competitive edge.
Companies can quickly adapt to changes in market demand and launch new products faster than their competitors.
Lastly, shortening lead time contributes to sustainability.
Optimized procurement processes mean less waste and more efficient resource usage, supporting environmentally friendly practices.
Conclusion
Creating an efficient procurement schedule is key to shortening lead time.
By focusing on demand clarity, fostering supplier relationships, investing in technology, and optimizing inventory, companies can significantly improve their procurement efforts.
Enhancing internal processes and managing risks further contribute to lead time reduction.
By prioritizing these strategies, businesses can consistently satisfy customer demands, improve their competitive position, and support sustainable practices.
資料ダウンロード
QCD管理受発注クラウド「newji」は、受発注部門で必要なQCD管理全てを備えた、現場特化型兼クラウド型の今世紀最高の受発注管理システムとなります。
ユーザー登録
受発注業務の効率化だけでなく、システムを導入することで、コスト削減や製品・資材のステータス可視化のほか、属人化していた受発注情報の共有化による内部不正防止や統制にも役立ちます。
NEWJI DX
製造業に特化したデジタルトランスフォーメーション(DX)の実現を目指す請負開発型のコンサルティングサービスです。AI、iPaaS、および先端の技術を駆使して、製造プロセスの効率化、業務効率化、チームワーク強化、コスト削減、品質向上を実現します。このサービスは、製造業の課題を深く理解し、それに対する最適なデジタルソリューションを提供することで、企業が持続的な成長とイノベーションを達成できるようサポートします。
製造業ニュース解説
製造業、主に購買・調達部門にお勤めの方々に向けた情報を配信しております。
新任の方やベテランの方、管理職を対象とした幅広いコンテンツをご用意しております。
お問い合わせ
コストダウンが利益に直結する術だと理解していても、なかなか前に進めることができない状況。そんな時は、newjiのコストダウン自動化機能で大きく利益貢献しよう!
(β版非公開)