- お役立ち記事
- Purchasing strategy to respond to raw material price fluctuations Long-term cost management perspective
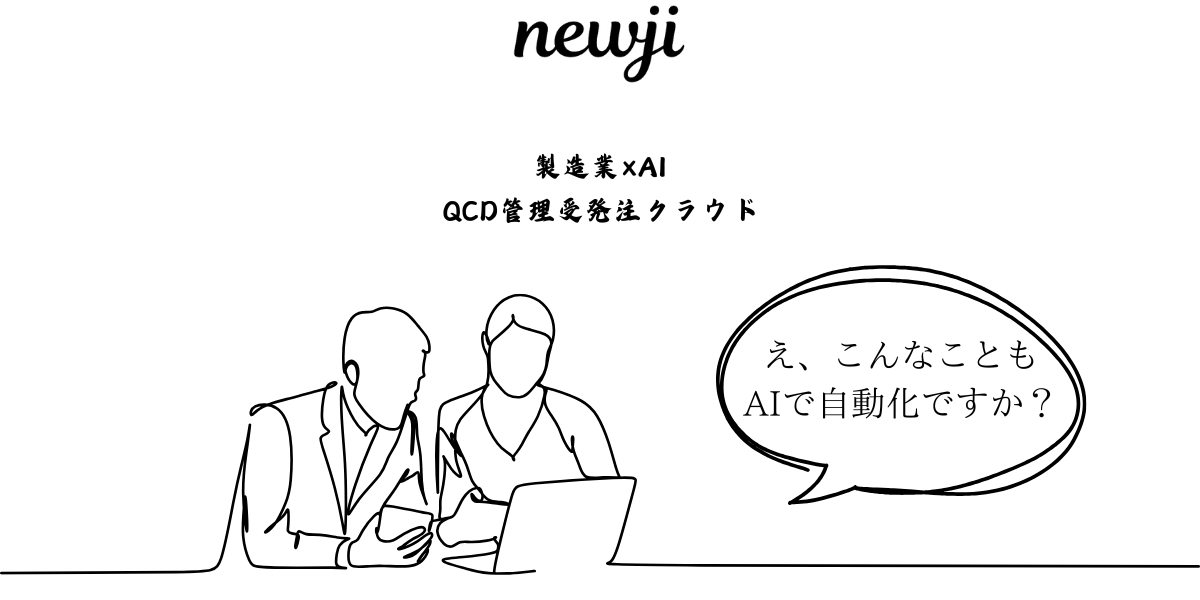
Purchasing strategy to respond to raw material price fluctuations Long-term cost management perspective
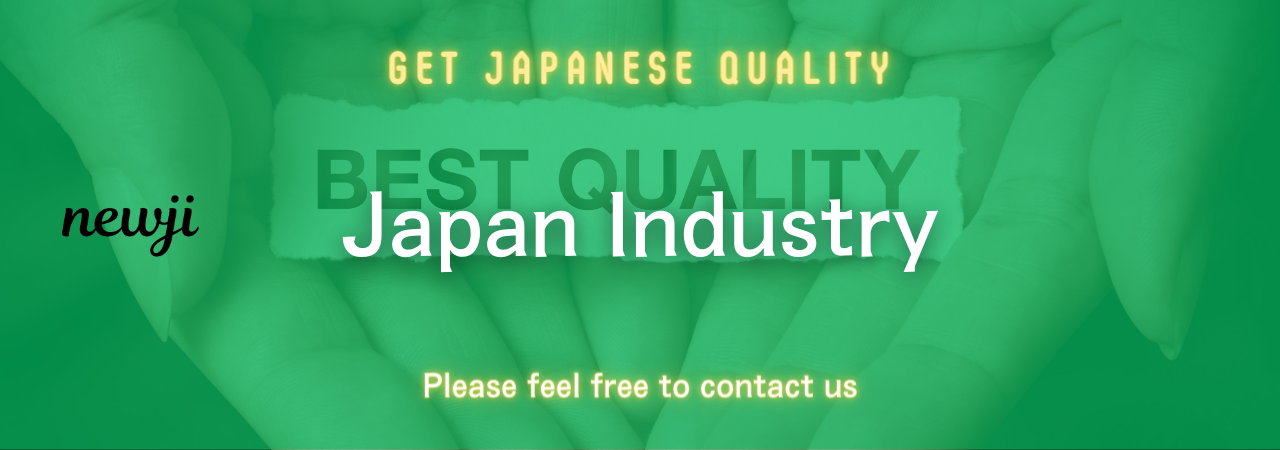
目次
Understanding Raw Material Price Fluctuations
Raw material price fluctuations are common and can significantly impact a company’s profitability.
These fluctuations can be driven by a multitude of factors, including geopolitical tensions, natural disasters, changes in government policies, and shifts in supply and demand dynamics.
For businesses that rely heavily on raw materials, such as manufacturers, it is crucial to have a strategy in place to respond effectively to these changes.
The key to managing raw material price fluctuations lies in understanding their root causes and potential impacts.
By doing so, businesses can not only mitigate risks but also identify opportunities for cost savings and competitive advantage.
Building a Robust Purchasing Strategy
A robust purchasing strategy is fundamental in responding to raw material price fluctuations.
This strategy should incorporate several elements that enable businesses to navigate through uncertain market conditions.
Diversifying Supply Sources
One of the most effective ways to manage price fluctuations is to diversify supply sources.
Relying on a single supplier can be risky, especially if that supplier is located in a region prone to instability.
By engaging with multiple suppliers across different geographies, businesses can reduce their exposure to regional disruptions and negotiate better terms.
Long-Term Contracts and Hedging
Long-term contracts can lock in prices for raw materials, shielding businesses from sudden increases.
These contracts can provide predictability in budgeting and planning.
However, it’s important to analyze market trends before committing, as long-term contracts can also lead to higher costs if prices decrease.
Hedging is another financial tool that can offer protection against price volatility.
By using instruments such as futures and options, businesses can set predetermined prices, thereby reducing uncertainty.
While hedging comes with its own costs and complexities, it can be a valuable part of a balanced purchasing strategy.
Investing in Inventory Management
Effective inventory management is vital for minimizing the impact of raw material price fluctuations.
Maintaining optimal inventory levels ensures that businesses have enough stock to meet demand without tying up excessive capital.
Advanced inventory management systems can provide real-time insights, helping companies make informed purchasing decisions.
Collaborating with Suppliers
Strong relationships with suppliers can be highly beneficial.
By working closely with suppliers, businesses can gain insights into market trends and negotiate better deals.
Supplier collaboration can also lead to joint initiatives that drive efficiency and innovation, ultimately reducing costs.
Implementing Cost Management Techniques
Beyond purchasing strategies, there are various cost management techniques that companies can use to offset the impact of raw material price fluctuations.
Cost Structure Analysis
Understanding the cost structure of products can provide insights into areas where cost reductions are possible.
By analyzing each component of the cost, businesses can identify which materials have the highest impact on pricing.
This knowledge allows for better decision-making in supplier selection and contract negotiation.
Value Engineering
Value engineering involves redesigning products to reduce material costs without compromising quality.
This approach encourages innovation in product development and can lead to significant savings.
Collaboration with R&D teams and suppliers is essential to identify alternative materials or processes that achieve the same functionality at a lower cost.
Continuous Improvement Programs
Adopting a culture of continuous improvement can help businesses consistently find ways to reduce costs.
Techniques like lean manufacturing and Six Sigma focus on eliminating waste and improving efficiency.
These programs can be applied not only to production processes but also to the supply chain and procurement activities.
Emphasizing a Long-Term Perspective
While addressing immediate challenges posed by raw material price fluctuations is crucial, having a long-term perspective is equally important.
Short-term fixes might provide temporary relief, but sustainable strategies require a broader vision.
Investing in Technology
Technology can play a transformative role in managing raw material costs.
Advanced analytics, artificial intelligence, and machine learning can provide insights into market trends and forecast price movements.
Automation tools can streamline procurement processes, making them more efficient and responsive to changes.
Sustainability and Resilience
Investing in sustainable practices can reduce dependency on volatile raw materials.
By seeking alternatives that are more readily available and environmentally friendly, companies can reduce risk while also meeting consumer demand for sustainable products.
Building resilience into the supply chain is also critical.
This involves assessing vulnerabilities and developing contingency plans to ensure continuity, even in adverse conditions.
Staying Informed and Adaptable
Keeping abreast of market developments is essential for anticipating changes in raw material prices.
Regularly reviewing market reports, engaging with industry experts, and attending trade events can help companies stay informed.
Adaptability is the ability to pivot strategies quickly in response to evolving circumstances.
Businesses that are flexible in their approach are better positioned to capitalize on opportunities and mitigate adverse effects.
Conclusion
Managing raw material price fluctuations is a complex but essential aspect of long-term cost management.
By developing a comprehensive purchasing strategy and implementing effective cost management techniques, businesses can better navigate the challenges posed by volatile markets.
A long-term perspective that emphasizes technology, sustainability, and adaptability can provide a competitive edge.
Through diligent planning and proactive management, companies can not only protect their bottom line but also seize opportunities for growth and innovation.
資料ダウンロード
QCD調達購買管理クラウド「newji」は、調達購買部門で必要なQCD管理全てを備えた、現場特化型兼クラウド型の今世紀最高の購買管理システムとなります。
ユーザー登録
調達購買業務の効率化だけでなく、システムを導入することで、コスト削減や製品・資材のステータス可視化のほか、属人化していた購買情報の共有化による内部不正防止や統制にも役立ちます。
NEWJI DX
製造業に特化したデジタルトランスフォーメーション(DX)の実現を目指す請負開発型のコンサルティングサービスです。AI、iPaaS、および先端の技術を駆使して、製造プロセスの効率化、業務効率化、チームワーク強化、コスト削減、品質向上を実現します。このサービスは、製造業の課題を深く理解し、それに対する最適なデジタルソリューションを提供することで、企業が持続的な成長とイノベーションを達成できるようサポートします。
オンライン講座
製造業、主に購買・調達部門にお勤めの方々に向けた情報を配信しております。
新任の方やベテランの方、管理職を対象とした幅広いコンテンツをご用意しております。
お問い合わせ
コストダウンが利益に直結する術だと理解していても、なかなか前に進めることができない状況。そんな時は、newjiのコストダウン自動化機能で大きく利益貢献しよう!
(Β版非公開)