- お役立ち記事
- Purchasing strategy to review transportation costs! Logistics risk and efficiency optimization guide
月間76,176名の
製造業ご担当者様が閲覧しています*
*2025年3月31日現在のGoogle Analyticsのデータより
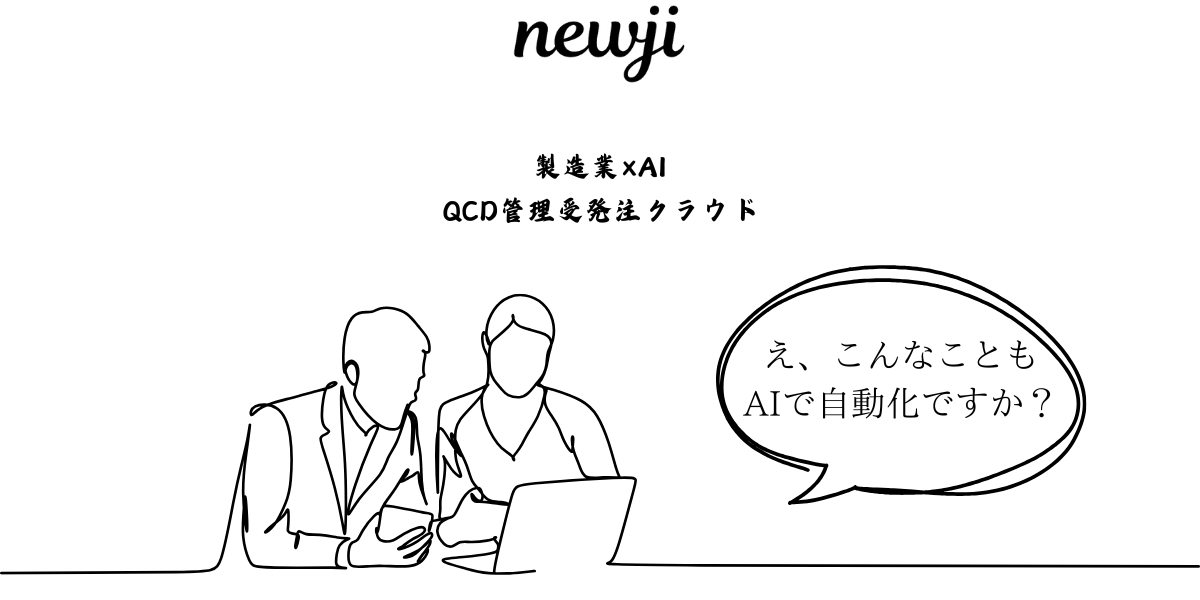
Purchasing strategy to review transportation costs! Logistics risk and efficiency optimization guide
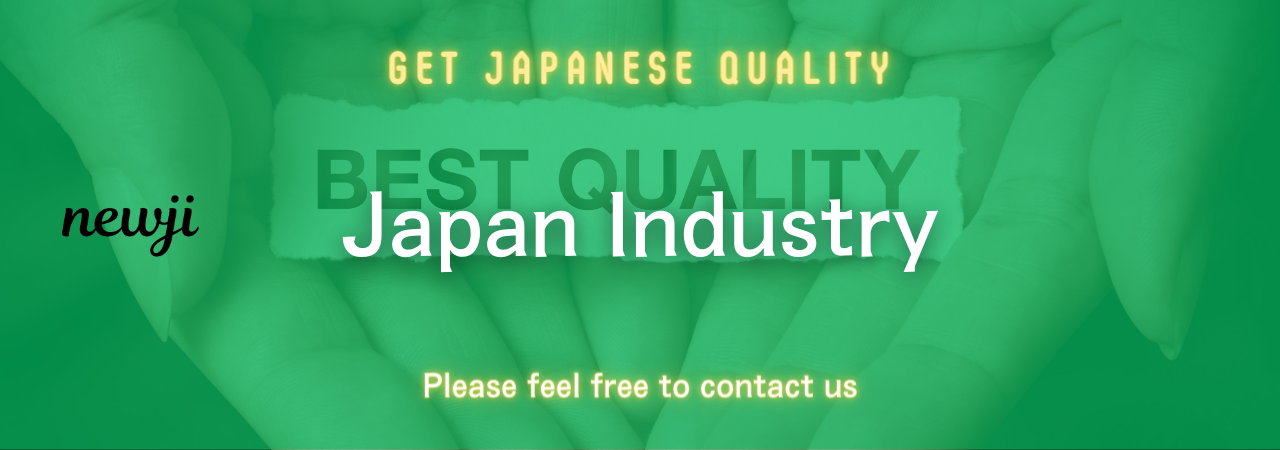
目次
Understanding Logistics Risks
In today’s fast-paced world, businesses often face various logistics risks that can significantly impact their transportation costs.
These risks include fluctuating fuel prices, regulatory changes, and unexpected disruptions like natural disasters or geopolitical events.
To effectively manage and mitigate these risks, companies need a comprehensive understanding and strategic approach.
Understanding these risks is the first step in optimizing logistics processes and minimizing unnecessary expenditures.
Common Logistics Risks
Common logistics risks can be broadly categorized into operational and external risks.
Operational risks involve day-to-day shipping and delivery challenges, such as vehicle breakdowns, poor route management, or inefficient loading practices.
External risks arise from factors outside the company’s control, like natural disasters, political instability, or sudden regulatory changes.
Each risk type demands a distinct approach, ranging from improving infrastructure to building more flexible supply chain systems.
Analyzing Transportation Costs
Transportation costs play a crucial role in a company’s overall logistics spending.
Analyzing these costs involves examining every cost component, such as fuel, labor, maintenance, and compliance with regulations.
By gaining detailed insights into each element, businesses can identify areas for potential savings.
For example, optimizing routes or scheduling can lead to significant fuel savings.
Tools for Cost Analysis
There are several tools available for a thorough cost analysis of transportation.
Transport management systems (TMS) help monitor and manage transportation operations efficiently.
These systems provide insights into fuel consumption, driver performance, and route efficiency.
Logistics analytics software can also offer predictive insights by analyzing historical data to forecast potential cost fluctuations based on varying factors.
Efficient Route Planning
One effective strategy to reduce transportation costs and optimize logistics efficiency is to improve route planning.
Efficient route planning not only cuts down on travel time but also reduces fuel consumption and vehicle wear and tear, thereby lowering maintenance costs.
Using advanced route optimization software can aid in creating the most efficient travel paths based on real-time traffic data, delivery deadlines, and vehicle capacity.
Benefits of Route Optimization
Route optimization has multiple benefits beyond cost reduction.
It enhances customer satisfaction by ensuring timely deliveries.
Improved route planning also contributes to reducing a company’s carbon footprint, enhancing its reputation for sustainability.
Furthermore, by minimizing driver hours, businesses can increase employee satisfaction and reduce turnover.
Implementing Technology in Logistics
Incorporating technology into logistics operations can significantly impact cost optimization and risk mitigation.
From real-time tracking systems to automated warehouses, technology provides various options to streamline operations and improve efficiency.
GPS tracking and telematics are crucial for real-time vehicle monitoring, allowing for proactive management of routes and delivery schedules.
Warehouse automation, on the other hand, can reduce operational costs by minimizing human error and maximizing storage efficiency.
Choosing the Right Tech Solutions
Choosing the right technology solution is essential for achieving the best results.
This involves carefully evaluating the specific needs of the business and the logistics challenges it faces.
Companies should consider scalability, integration capability with existing systems, and the level of support offered by the technology providers.
Negotiating with Carriers
Effective negotiation with carriers is another strategic approach to optimizing logistics costs.
Building strong relationships with transportation providers can lead to better pricing, more flexible contracts, and improved service levels.
Understanding the carrier’s pricing models and operational constraints can provide valuable leverage in negotiations.
Strategies for Successful Negotiations
Successful negotiation strategies include conducting thorough market research to understand industry pricing standards and trends.
Focusing on long-term partnerships rather than short-term contracts can also lead to more favorable terms.
Building a collaborative relationship with carriers allows businesses to negotiate mutually beneficial agreements that can help in managing costs effectively.
Enhancing Supply Chain Collaboration
Supply chain collaboration is crucial in optimizing logistics efficiency and reducing costs.
By fostering a collaborative environment with suppliers, carriers, and customers, businesses can streamline processes and enhance transparency across the supply chain network.
Effective communication and coordinated planning minimize delays, reduce stockouts, and optimize delivery schedules.
Collaboration Tools and Techniques
Utilizing collaboration tools can enhance communication and coordination along the supply chain.
Platforms for shared planning and forecasting enable real-time data sharing, improving decision-making and responsiveness.
Techniques such as joint ventures and strategic alliances with key partners can also strengthen supply chain collaboration, leading to cost reductions and improved service levels.
Continuous Improvement in Logistics
Logistics optimization is not a one-time effort, but a continuous process of analysis, adjustment, and improvement.
By regularly reviewing logistics strategies and performance metrics, businesses can adapt to changes in the market and logistics landscape.
This proactive approach helps in maintaining a competitive edge and ensuring sustainable cost savings.
Monitoring and Evaluation Methods
Effective monitoring and evaluation methods include key performance indicators (KPIs) and benchmarking against industry standards.
KPIs such as delivery time, cost per shipment, and error rates provide insights into operational efficiency.
Regular audits and feedback loops can help identify areas for improvement and ensure alignment with strategic objectives.
In summary, optimizing transportation costs through a strategic approach involves understanding logistics risks, analyzing costs, efficient route planning, leveraging technology, negotiating effectively, enhancing collaboration, and fostering continuous improvement.
By embracing these strategies, businesses can navigate logistics challenges successfully while achieving cost efficiencies and improving overall service levels.
資料ダウンロード
QCD管理受発注クラウド「newji」は、受発注部門で必要なQCD管理全てを備えた、現場特化型兼クラウド型の今世紀最高の受発注管理システムとなります。
ユーザー登録
受発注業務の効率化だけでなく、システムを導入することで、コスト削減や製品・資材のステータス可視化のほか、属人化していた受発注情報の共有化による内部不正防止や統制にも役立ちます。
NEWJI DX
製造業に特化したデジタルトランスフォーメーション(DX)の実現を目指す請負開発型のコンサルティングサービスです。AI、iPaaS、および先端の技術を駆使して、製造プロセスの効率化、業務効率化、チームワーク強化、コスト削減、品質向上を実現します。このサービスは、製造業の課題を深く理解し、それに対する最適なデジタルソリューションを提供することで、企業が持続的な成長とイノベーションを達成できるようサポートします。
製造業ニュース解説
製造業、主に購買・調達部門にお勤めの方々に向けた情報を配信しております。
新任の方やベテランの方、管理職を対象とした幅広いコンテンツをご用意しております。
お問い合わせ
コストダウンが利益に直結する術だと理解していても、なかなか前に進めることができない状況。そんな時は、newjiのコストダウン自動化機能で大きく利益貢献しよう!
(β版非公開)