- お役立ち記事
- Purpose of design review and how to utilize QFD
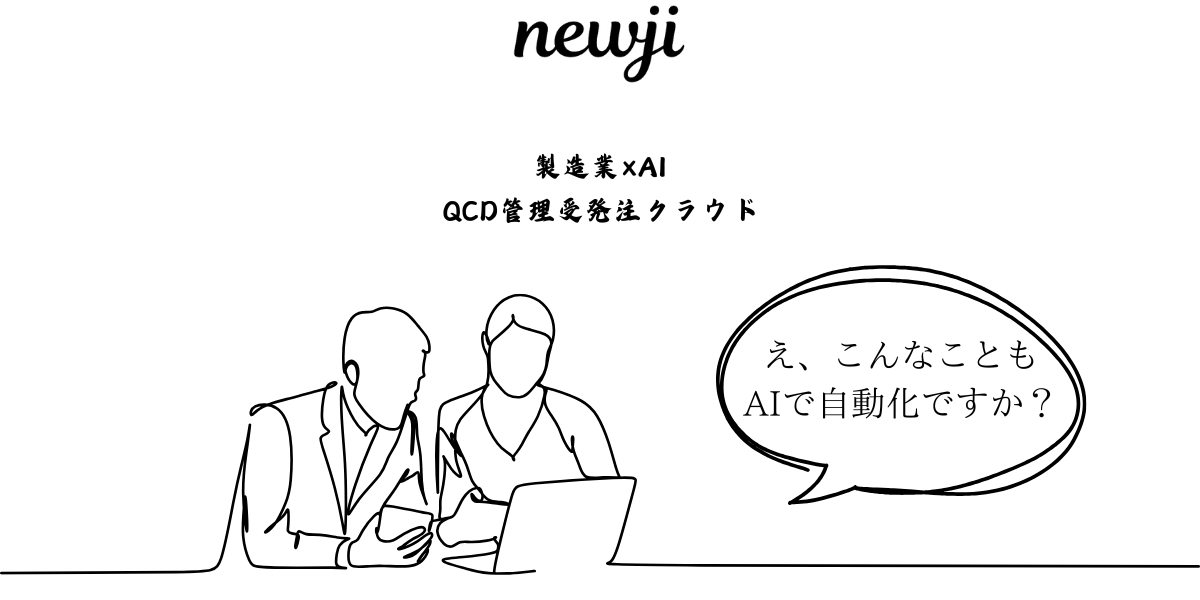
Purpose of design review and how to utilize QFD
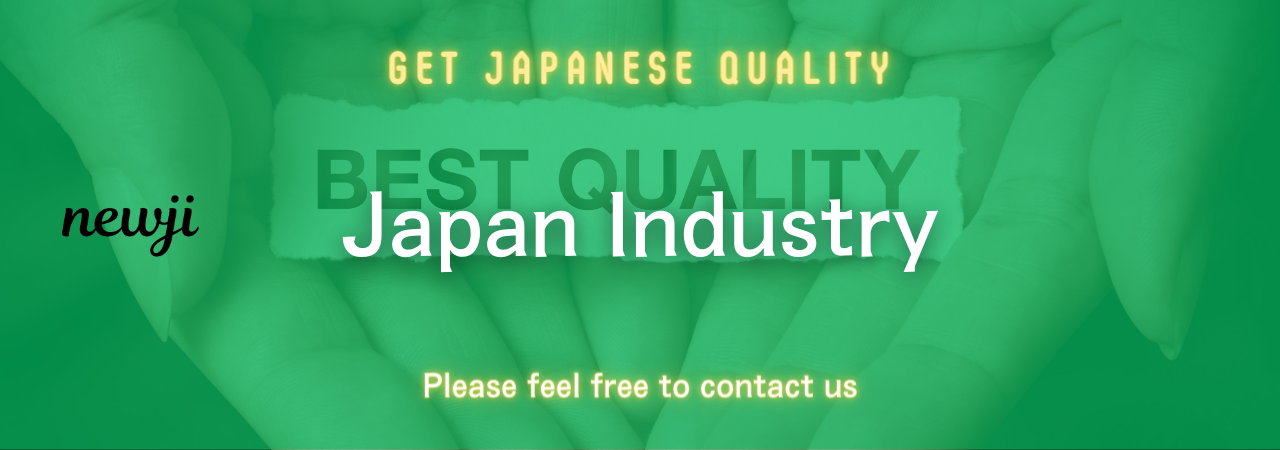
目次
Understanding the Purpose of Design Review
Design review is an essential part of the product development process, ensuring that a design is scrutinized before it moves forward.
The primary purpose of a design review is to evaluate a product’s design to guarantee it meets its intended requirements and specifications.
This process helps in identifying potential problems early, reducing errors in the later stages, and ensuring the design aligns with project goals.
By conducting a thorough review, teams can save time and resources, minimizing the need for costly changes after production.
Moreover, design reviews provide an opportunity for team collaboration, allowing diverse perspectives to influence the final outcome.
This collective insight can improve the product’s quality and functionality.
The Benefits of Design Reviews
Conducting design reviews offers numerous benefits.
Foremost, it enhances the overall quality of the design by integrating feedback from different stakeholders including engineers, designers, and end users.
This process enables a holistic examination of the design, addressing various functions and features that might otherwise be overlooked.
Design reviews also foster innovation by encouraging creative problem-solving among team members.
When diverse minds come together, it often leads to innovative solutions and improvements that a single person might not envision.
Furthermore, these reviews ensure that all team members are aligned with the design objectives, which promotes coherence throughout the project lifecycle.
Another significant advantage is risk management.
By identifying potential issues early in the development process, teams can mitigate risks effectively.
This foresight helps in minimizing delays and cost overruns, making the entire project more manageable and efficient.
Introduction to Quality Function Deployment (QFD)
Quality Function Deployment (QFD) is a strategic tool used in the design review process to enhance a product’s quality.
This methodology focuses on transforming customer needs into specific design requirements, ensuring that the final product aligns closely with customer expectations.
QFD integrates various aspects of product planning and design, making it easier to align team efforts towards a common goal.
The process involves creating a matrix, often referred to as the “House of Quality,” which visually maps customer needs against technical requirements.
This tool aids in prioritizing the features that hold the most value to the customer, translating customer desires into actionable engineering goals.
Steps to Implement QFD in Design Review
To effectively utilize QFD during a design review, a structured approach is necessary.
Here are the steps to implement QFD:
1. **Identify Customer Needs**: Begin with comprehensive research to understand customer needs and preferences.
Gathering this information involves surveys, interviews, and market analysis to capture a holistic view of what customers expect from the product.
2. **Translate Needs into Design Requirements**: Use the QFD matrix to convert customer needs into precise technical requirements.
This involves detailing how each need can be fulfilled through specific design features and functionalities.
3. **Prioritize Requirements**: Once the design requirements are established, prioritize them based on their importance to the customer and technical feasibility.
This aids in focusing efforts on the most critical aspects of the design.
4. **Evaluate Design Alternatives**: Explore various design alternatives that address the prioritized requirements.
The aim is to find optimal solutions that meet customer needs effectively while considering cost, time, and available resources.
5. **Review and Improve**: Conduct thorough reviews with the team to evaluate the proposed designs, seeking feedback and suggestions for improvement.
This collaborative effort ensures that all potential issues are addressed before moving on to the next phase.
6. **Continuous Monitoring**: As the design progresses, continuously monitor its alignment with the identified requirements.
This helps in making necessary adjustments to stay on track with customer expectations and project objectives.
Leveraging QFD for Practical Outcomes
Utilizing QFD in design reviews leads to tangible benefits and improved project outcomes.
Primarily, it ensures that the product development process is guided by a clear understanding of customer requirements, enhancing product relevance and satisfaction.
Additionally, QFD facilitates a streamlined communication process among team members.
By visualizing the relationship between customer needs and technical specifications, team members can easily collaborate and discuss potential solutions.
The methodology also supports better decision-making by providing a clear framework to evaluate trade-offs and prioritize features.
This strategic insight helps in balancing customer desires with technical limitations and budget constraints.
Furthermore, QFD can lead to faster product development cycles.
By clearly outlining customer requirements and design specifications from the onset, the project can proceed with fewer disruptions and less rework.
Conclusion: Embracing Design Review and QFD
Embracing design review, especially when integrated with QFD, provides a robust framework for developing successful products.
The dual focus on rigorous evaluation and customer-centric design places teams in a strong position to innovate and deliver high-quality results.
By engaging in detailed reviews and adopting strategic tools like QFD, organizations can significantly enhance their design processes, leading to successful project outcomes that meet customer expectations and achieve business goals.
Ultimately, effective design reviews and the implementation of QFD lead to products that are not only functional but also aligned with the nuanced needs of the market.
資料ダウンロード
QCD調達購買管理クラウド「newji」は、調達購買部門で必要なQCD管理全てを備えた、現場特化型兼クラウド型の今世紀最高の購買管理システムとなります。
ユーザー登録
調達購買業務の効率化だけでなく、システムを導入することで、コスト削減や製品・資材のステータス可視化のほか、属人化していた購買情報の共有化による内部不正防止や統制にも役立ちます。
NEWJI DX
製造業に特化したデジタルトランスフォーメーション(DX)の実現を目指す請負開発型のコンサルティングサービスです。AI、iPaaS、および先端の技術を駆使して、製造プロセスの効率化、業務効率化、チームワーク強化、コスト削減、品質向上を実現します。このサービスは、製造業の課題を深く理解し、それに対する最適なデジタルソリューションを提供することで、企業が持続的な成長とイノベーションを達成できるようサポートします。
オンライン講座
製造業、主に購買・調達部門にお勤めの方々に向けた情報を配信しております。
新任の方やベテランの方、管理職を対象とした幅広いコンテンツをご用意しております。
お問い合わせ
コストダウンが利益に直結する術だと理解していても、なかなか前に進めることができない状況。そんな時は、newjiのコストダウン自動化機能で大きく利益貢献しよう!
(Β版非公開)