- お役立ち記事
- Quality and safety checklist that should not be overlooked during supplier audits
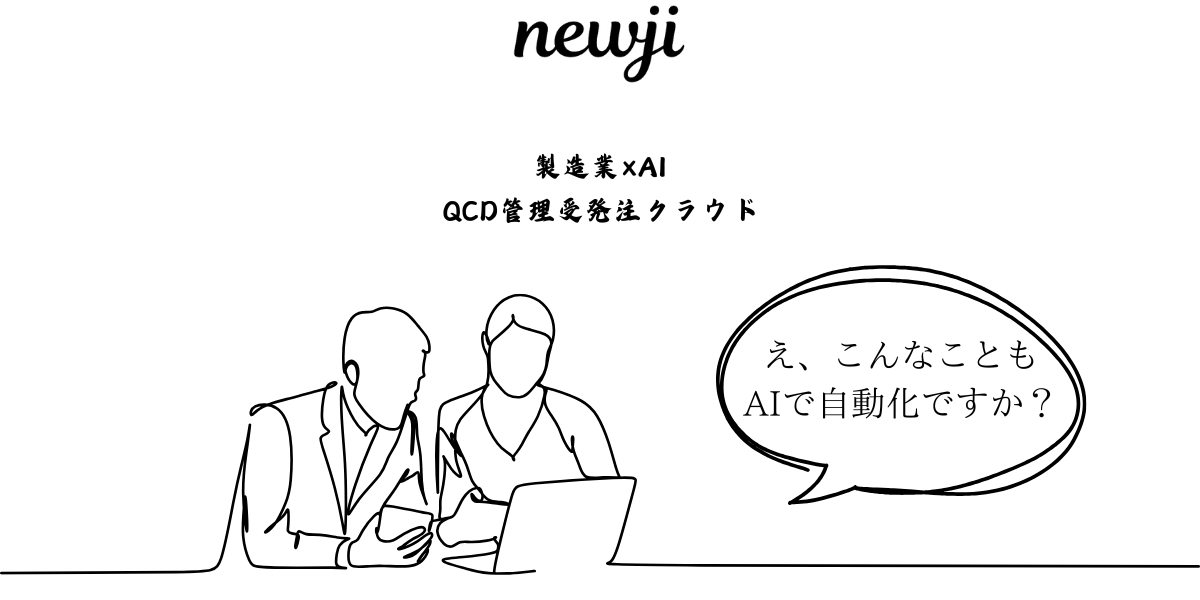
Quality and safety checklist that should not be overlooked during supplier audits
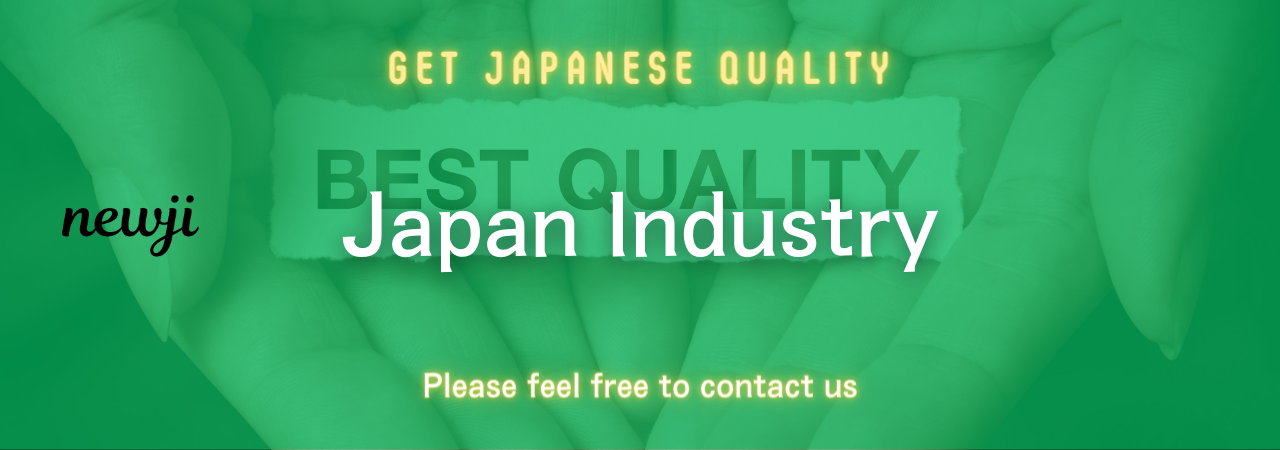
目次
Understanding Supplier Audits
Supplier audits are an essential component of the supply chain management process.
They are conducted to ensure that suppliers meet the required standards for quality and safety.
The purpose of these audits is not only to evaluate compliance with contractual agreements but also to identify areas for improvement.
Focusing on quality and safety during these audits is crucial because any oversight could lead to significant risks such as product recalls, legal liabilities, and reputational damage.
Why Quality and Safety Matter
Quality and safety are two critical aspects that affect both the end product and the consumer experience.
Quality ensures that products meet specified requirements, reducing the risk of defects and failures.
Safety, on the other hand, protects consumers from potential hazards associated with a product’s use.
Ensuring both quality and safety in supplier operations contributes to the overall success of a business, enhancing both customer satisfaction and brand trust.
Key Elements of a Quality and Safety Checklist
When conducting supplier audits, there are several key elements to include in a quality and safety checklist.
These elements help ensure no critical aspect is overlooked, thereby reducing potential risks.
Supplier Credentials and Certifications
Begin by reviewing the supplier’s credentials and certifications.
Check if they possess the necessary industry-specific certifications, such as ISO standards, that demonstrate compliance with international quality and safety regulations.
This verification not only ensures that the supplier meets minimum requirements but also indicates their commitment to maintaining high standards.
Manufacturing Processes
Evaluate the manufacturing processes used by the supplier.
Ensure that they follow established procedures that are both efficient and quality-oriented.
Examine whether standard operating procedures (SOPs) are in place and are being adhered to consistently.
This ensures that all production steps are aligned with best practices, minimizing the risk of defects.
Quality Control Measures
Assess the quality control measures implemented by the supplier.
This includes inspecting the frequency and methods used in quality checks during production.
Ensure that there are clear protocols for identifying, isolating, and correcting defects.
Adequate quality control measures help in maintaining product consistency and reliability.
Raw Material Inspection
Inspect the process of raw material selection and inspection laid out by the supplier.
Evaluate how they verify the quality and source of their materials.
This step is crucial, as poor quality raw materials can compromise the entire production process and lead to inferior end products.
Employee Training and Competency
Evaluate the level of training and competency among the supplier’s employees.
Check records of training sessions and whether they are regular and comprehensive.
Employees should be knowledgeable about safety standards and quality management processes, ensuring competency in executing their roles effectively.
Safety Protocols and Equipment
Safety protocols and equipment form the backbone of a safe working environment at supplier sites.
Safety Equipment and Personal Protective Equipment (PPE)
Verify that suppliers provide necessary safety equipment and Personal Protective Equipment (PPE) to their employees.
Inspect the condition and availability of safety gear such as helmets, gloves, goggles, and more.
Ensuring adequate safety equipment is crucial to protecting employees from potential industrial injuries.
Emergency Preparedness
Assess the supplier’s emergency preparedness plans.
Examine whether they have clearly outlined procedures for different emergency scenarios such as fire, spills, or equipment malfunctions.
Check for the presence and condition of emergency exits, and ensure that evacuation plans are well communicated to all employees.
Adequacy of Safety Certifications
Review the supplier’s safety certifications to ensure compliance with local and international regulations.
These certifications indicate the supplier’s dedication to maintaining a safe working environment, reducing workplace accidents and liabilities.
Continuous Improvement and Feedback
Continuous improvement processes and feedback mechanisms are crucial for sustaining quality and safety standards.
Corrective Action Plans
Inspect if there are structured corrective action plans in place for dealing with identified non-compliances.
These plans should outline specific steps and timelines for rectification and be monitored regularly for progress.
Feedback Mechanisms
Look into the supplier’s feedback mechanisms, which allow employees and customers to report issues related to quality and safety.
A robust feedback system is vital for continuous improvement and resolving issues before they escalate into larger problems.
Performance Monitoring
Ensure that performance monitoring systems are in place to track quality and safety metrics regularly.
This involves the analysis of audit results and identifying trends or recurring issues that may need attention.
Effective performance monitoring helps in maintaining and enhancing supplier compliance over time.
Conclusion
Incorporating a comprehensive quality and safety checklist during supplier audits is essential for ensuring high standards are met throughout the supply chain.
By systematically evaluating supplier credentials, processes, safety protocols, and improvement mechanisms, businesses can mitigate potential risks.
Priority should always be given to maintaining a balance between quality assurance and safety, as both are integral to business success and consumer protection.
Conducting thorough supplier audits can lead to stronger partnerships and help build a sustainable and reputable business ecosystem.
資料ダウンロード
QCD調達購買管理クラウド「newji」は、調達購買部門で必要なQCD管理全てを備えた、現場特化型兼クラウド型の今世紀最高の購買管理システムとなります。
ユーザー登録
調達購買業務の効率化だけでなく、システムを導入することで、コスト削減や製品・資材のステータス可視化のほか、属人化していた購買情報の共有化による内部不正防止や統制にも役立ちます。
NEWJI DX
製造業に特化したデジタルトランスフォーメーション(DX)の実現を目指す請負開発型のコンサルティングサービスです。AI、iPaaS、および先端の技術を駆使して、製造プロセスの効率化、業務効率化、チームワーク強化、コスト削減、品質向上を実現します。このサービスは、製造業の課題を深く理解し、それに対する最適なデジタルソリューションを提供することで、企業が持続的な成長とイノベーションを達成できるようサポートします。
オンライン講座
製造業、主に購買・調達部門にお勤めの方々に向けた情報を配信しております。
新任の方やベテランの方、管理職を対象とした幅広いコンテンツをご用意しております。
お問い合わせ
コストダウンが利益に直結する術だと理解していても、なかなか前に進めることができない状況。そんな時は、newjiのコストダウン自動化機能で大きく利益貢献しよう!
(Β版非公開)