- お役立ち記事
- Quality assurance in import contracts with suppliers Role and management method of purchasing department
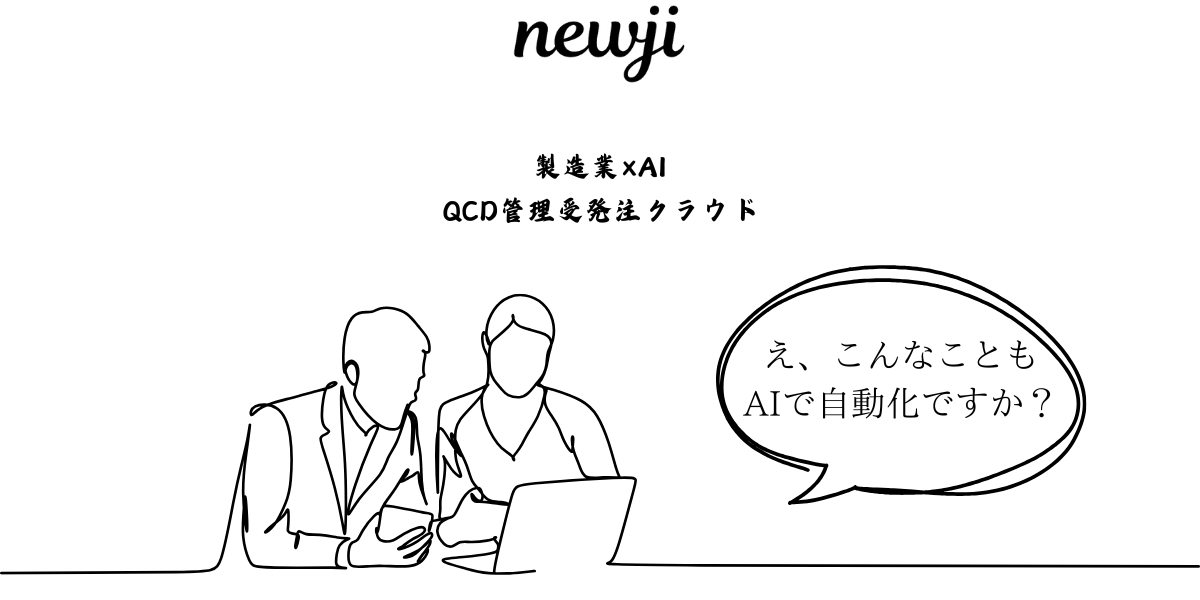
Quality assurance in import contracts with suppliers Role and management method of purchasing department
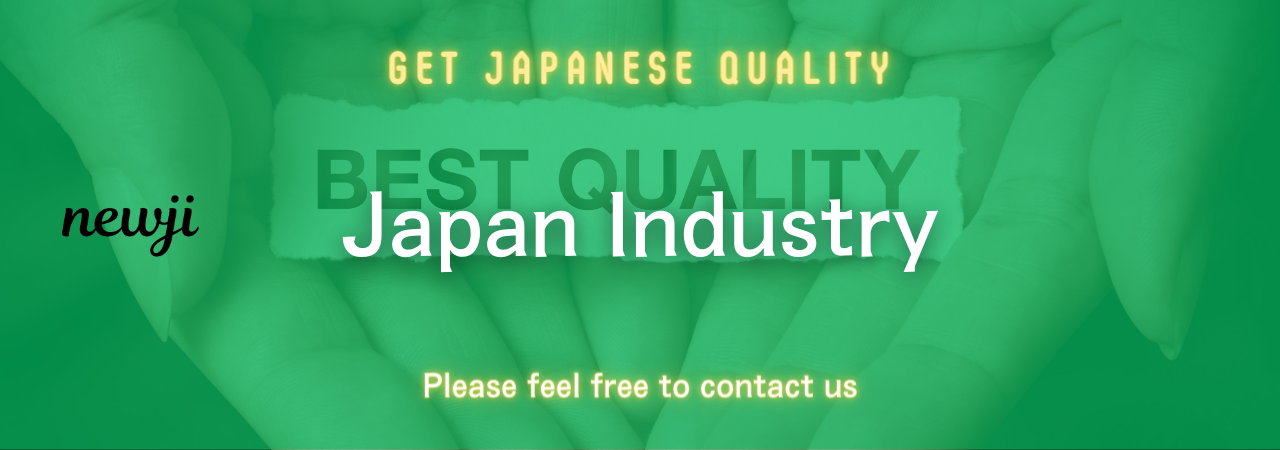
Understanding Quality Assurance in Import Contracts
Quality assurance is a vital component in business, especially when dealing with import contracts with suppliers.
It ensures that the products meet the required standards and specifications before they reach the consumers.
The purchasing department plays a crucial role in guaranteeing that quality assurance processes are maintained efficiently.
Import contracts are formal agreements between buyers and overseas suppliers.
These documents outline the terms and conditions for the procurement of goods, detailing everything from price to quality standards.
A well-drafted import contract will include clauses that cover quality assurance, specifying the responsibilities of each party involved.
This is where the purchasing department comes in.
The Role of the Purchasing Department in Quality Assurance
The purchasing department is responsible for the acquisition of goods and services necessary for a company’s operations.
They ensure that suppliers comply with quality standards outlined in import contracts.
This requires vigilance, expertise, and a well-coordinated strategy.
One of the primary roles of the purchasing department is supplier evaluation.
Before any agreement is made, potential suppliers must be assessed to determine if they can meet the quality requirements.
This evaluation considers factors like production capabilities, past performance, and overall reliability.
Furthermore, the purchasing department is responsible for quality control measures.
By conducting inspections and audits, they ensure that the products meet the agreed-upon standards before they are shipped.
They may visit supplier factories to monitor production processes, or employ third-party inspectors to carry out these tasks.
Managing Supplier Relationships
Effective supplier relationship management is crucial for maintaining quality standards.
The purchasing department negotiates and maintains long-term partnerships with suppliers who consistently deliver high-quality products.
Regular communication with suppliers is essential to address any issues that may arise.
By building strong relationships, the purchasing department can work collaboratively with suppliers to resolve potential problems and improve product quality.
The department also plays a key role in negotiating contract terms.
They need to ensure that quality assurance clauses are clearly defined and enforceable.
This includes specifying the quality specifications, inspection procedures, and the consequences of non-compliance.
Implementing Quality Assurance Systems
To manage quality assurance effectively, the purchasing department often implements structured quality assurance systems.
These systems help in streamlining processes, identifying potential risks, and ensuring continuous improvement.
One popular method is the use of ISO standards.
These standards provide guidelines for quality management systems and help organizations ensure that their products and services consistently meet customer and regulatory requirements.
Another approach is to adopt Total Quality Management (TQM).
TQM is a comprehensive system that involves every department, not just purchasing, in maintaining high quality.
It emphasizes the continuous improvement of processes, products, and services through feedback and collaboration.
Challenges in Quality Assurance
Despite the best efforts of the purchasing department, challenges in maintaining quality assurance can still arise.
These challenges may include cultural differences, communication barriers, and varying international standards.
Language differences can lead to misunderstandings and misinterpretations of quality specifications.
This is why precise and detailed documentation in import contracts is crucial.
Additionally, different countries may have different quality standards.
The purchasing department must be aware of these disparities and work to ensure compliance across borders.
Technology and Quality Assurance
Technology plays a significant role in enhancing quality assurance processes.
With advancements in data analysis, automation, and communication tools, managing quality in import contracts has become more efficient and accurate.
The purchasing department can utilize software to monitor supplier performance, track shipments, and analyze quality data.
This technology allows for real-time updates and alerts, minimizing the risk of sub-standard products.
Moreover, technology can assist in improving transparency and accountability across the supply chain.
With better data access and sharing, potential quality issues can be identified and addressed promptly.
Conclusion
In summary, quality assurance is an integral part of import contracts with suppliers, and the purchasing department plays a pivotal role in managing this aspect.
Their responsibilities encompass evaluating suppliers, conducting quality control, managing relationships, and implementing assurance systems.
By navigating the challenges and leveraging technology, the purchasing department can ensure that the products meet quality standards, thus securing the company’s reputation and customer satisfaction.
資料ダウンロード
QCD調達購買管理クラウド「newji」は、調達購買部門で必要なQCD管理全てを備えた、現場特化型兼クラウド型の今世紀最高の購買管理システムとなります。
ユーザー登録
調達購買業務の効率化だけでなく、システムを導入することで、コスト削減や製品・資材のステータス可視化のほか、属人化していた購買情報の共有化による内部不正防止や統制にも役立ちます。
NEWJI DX
製造業に特化したデジタルトランスフォーメーション(DX)の実現を目指す請負開発型のコンサルティングサービスです。AI、iPaaS、および先端の技術を駆使して、製造プロセスの効率化、業務効率化、チームワーク強化、コスト削減、品質向上を実現します。このサービスは、製造業の課題を深く理解し、それに対する最適なデジタルソリューションを提供することで、企業が持続的な成長とイノベーションを達成できるようサポートします。
オンライン講座
製造業、主に購買・調達部門にお勤めの方々に向けた情報を配信しております。
新任の方やベテランの方、管理職を対象とした幅広いコンテンツをご用意しております。
お問い合わせ
コストダウンが利益に直結する術だと理解していても、なかなか前に進めることができない状況。そんな時は、newjiのコストダウン自動化機能で大きく利益貢献しよう!
(Β版非公開)