- お役立ち記事
- Quality Assurance: Why Overseas Companies Rely on Japanese Standards
Quality Assurance: Why Overseas Companies Rely on Japanese Standards
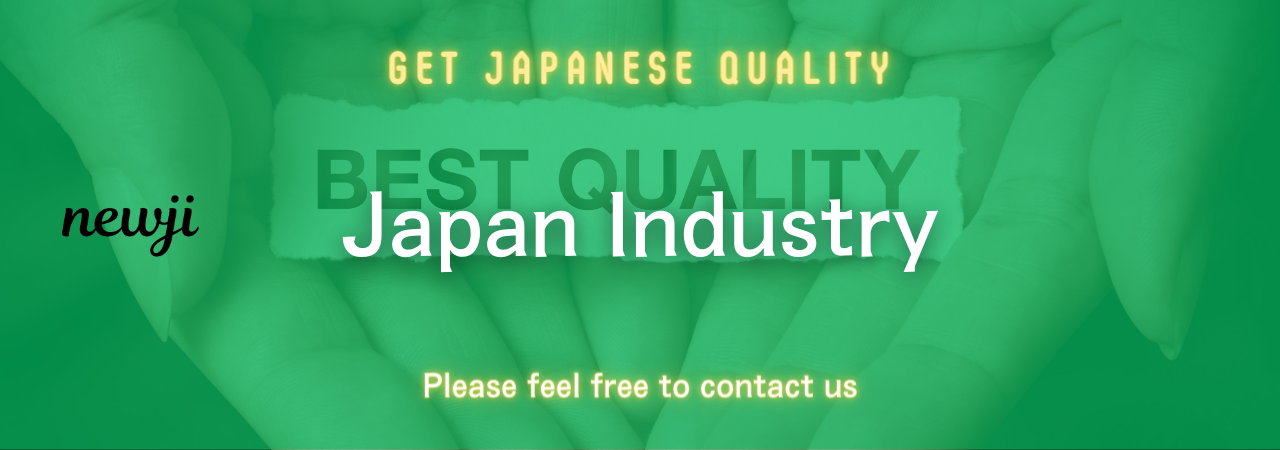
Quality assurance is a critical aspect for any company, ensuring that products or services meet certain standards of quality before reaching the customer.
Many companies around the world have recognized the high standards of Japanese quality assurance, prompting them to rely on Japanese methods and techniques to enhance their own processes.
In this article, we will explore why overseas companies have turned to Japanese standards for quality assurance.
目次
Understanding Quality Assurance
What is Quality Assurance?
Quality assurance is a process-oriented approach that focuses on preventing mistakes and defects during the production or service process.
It involves systematic activities and checks to ensure that the final product or service meets a predefined set of quality criteria.
This is achieved through rigorous planning, documentation, and a series of standardized procedures.
Importance of Quality Assurance
Quality assurance is essential for maintaining the reputation of a brand.
It minimizes risks and errors, leading to higher customer satisfaction and loyalty.
By ensuring consistent quality, businesses can reduce costs associated with rework, returns, or complaints.
Moreover, regulatory compliance often mandates stringent quality assurance protocols, making it a crucial aspect for global companies.
Japanese Standards in Quality Assurance
The Roots of Japanese Quality
Japan’s emphasis on quality can be traced back to the post-World War II era.
Facing the need to rebuild its economy, Japan adopted and refined several quality control methods.
Dr. W. Edwards Deming, an American statistician, played a significant role in this transformation by introducing statistical quality control techniques.
The Japanese integrated these techniques into their manufacturing processes, leading to remarkable improvements in product quality.
Key Principles of Japanese Quality Assurance
Several principles underpin Japanese quality assurance, each contributing to the country’s reputation for excellence.
Kaizen: Kaizen means “continuous improvement.” It is a philosophy that encourages all employees to look for ways to improve work processes continuously. Small, incremental changes, when consistently applied, lead to substantial improvements over time.
Total Quality Management (TQM): TQM is an organization-wide approach centered on quality. It involves everyone in the company, from top management to front-line workers, aiming for long-term success through customer satisfaction.
Six Sigma: This is a data-driven methodology designed to improve the quality of processes by identifying and removing causes of defects and minimizing variability. It uses statistical methods for fixing and controlling problems within the production and business procedures.
Why Overseas Companies Trust Japanese Standards
Proven Track Record
Japanese companies like Toyota, Sony, and Panasonic have long been synonymous with quality. Their global success serves as proof of the efficacy of Japan’s quality assurance standards. When companies around the world observe this consistent high quality, they are more inclined to adopt these standards themselves.
Comprehensive Approach
The Japanese methods focus not just on the end product but also on the entire process. This comprehensive approach ensures that every aspect of production or service delivery meets stringent quality criteria. Such holistic methods can drastically reduce the chances of defects and improve the overall efficiency of the processes.
Employee Involvement
One of the standout features of Japanese quality assurance is the involvement of employees at all levels. By encouraging input from every worker, companies can harness a wide range of perspectives and expertise. This inclusive culture often leads to innovative solutions to quality problems, making the processes more robust.
Implementation of Japanese Standards Globally
Training and Development
To implement Japanese quality standards, overseas companies often invest heavily in training and development. Employees are taught Japanese techniques such as Kaizen and Six Sigma, equipping them with the skills to apply these methods effectively.
Cross-Cultural Adaptation
While Japanese standards are highly effective, they may need to be adapted to fit different cultural and business environments. Companies often make minor modifications to suit local circumstances while retaining the core principles of Japanese quality assurance. This flexible approach ensures that the standards are applicable across diverse settings.
Technological Integration
With advancements in technology, many of the statistical methods and quality control techniques developed in Japan can be integrated into modern software solutions. This allows for more efficient monitoring and controlling of quality throughout the production process. Automation and real-time data analytics further enhance the capability to maintain high standards.
Case Studies and Success Stories
Toyota Production System
One of the most famous examples of Japanese quality assurance is the Toyota Production System (TPS). This system incorporates principles of continuous improvement, just-in-time production, and respect for people. It has been adopted by numerous companies worldwide, demonstrating how effective Japanese methods can be when properly implemented.
Electronics Industry
Japanese electronics firms such as Sony and Panasonic have set the benchmark for quality. Their meticulous attention to detail and rigorous testing procedures ensure that their products consistently meet high standards. Overseas companies in the electronics sector have followed suit, employing Japanese standards to enhance their own quality assurance processes.
Conclusion
As we have seen, the global trust in Japanese quality assurance standards is well-founded. The combination of historical success, comprehensive methodologies, and the involvement of employees at all levels makes the Japanese approach highly effective. By adopting these standards, overseas companies can achieve better quality, leading to increased customer satisfaction and competitive advantage in the market.
Whether through training, cross-cultural adaptation, or technological integration, the implementation of Japanese quality assurance standards offers a proven path to excellence.
資料ダウンロード
QCD調達購買管理クラウド「newji」は、調達購買部門で必要なQCD管理全てを備えた、現場特化型兼クラウド型の今世紀最高の購買管理システムとなります。
ユーザー登録
調達購買業務の効率化だけでなく、システムを導入することで、コスト削減や製品・資材のステータス可視化のほか、属人化していた購買情報の共有化による内部不正防止や統制にも役立ちます。
NEWJI DX
製造業に特化したデジタルトランスフォーメーション(DX)の実現を目指す請負開発型のコンサルティングサービスです。AI、iPaaS、および先端の技術を駆使して、製造プロセスの効率化、業務効率化、チームワーク強化、コスト削減、品質向上を実現します。このサービスは、製造業の課題を深く理解し、それに対する最適なデジタルソリューションを提供することで、企業が持続的な成長とイノベーションを達成できるようサポートします。
オンライン講座
製造業、主に購買・調達部門にお勤めの方々に向けた情報を配信しております。
新任の方やベテランの方、管理職を対象とした幅広いコンテンツをご用意しております。
お問い合わせ
コストダウンが利益に直結する術だと理解していても、なかなか前に進めることができない状況。そんな時は、newjiのコストダウン自動化機能で大きく利益貢献しよう!
(Β版非公開)