- お役立ち記事
- Quality Audit and Procurement of Coating Defects: Product Quality Improvement and Problem Solving Perspectives
Quality Audit and Procurement of Coating Defects: Product Quality Improvement and Problem Solving Perspectives
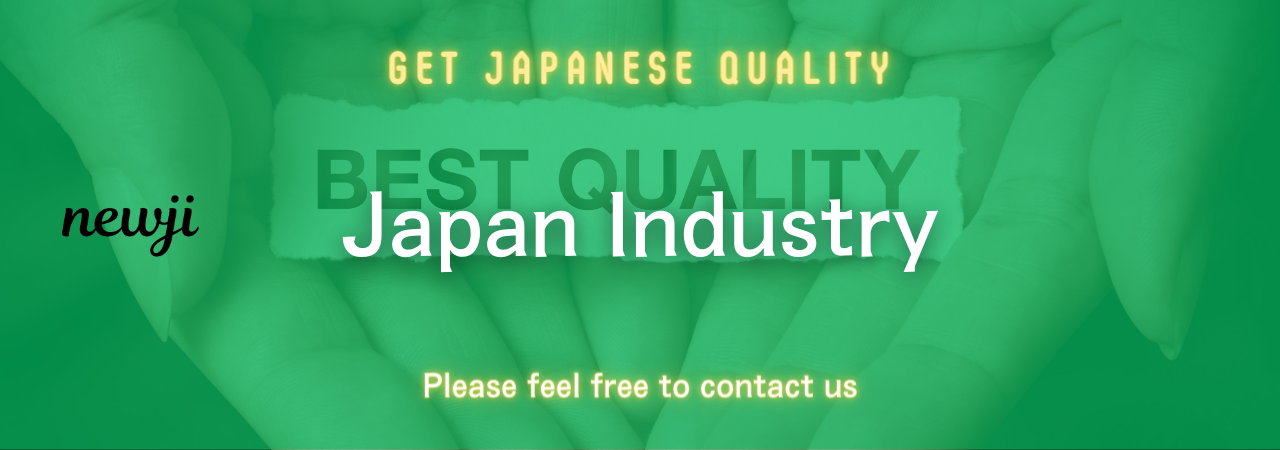
In today’s competitive market, ensuring the quality of your products is essential for maintaining customer satisfaction and loyalty. One of the key aspects to consider in manufacturing is the quality audit and procurement of coating defects. These processes are crucial in detecting potential issues and ensuring that the final products meet the highest standards. This article aims to provide insights into improving product quality through effective quality audits and defect management.
Understanding Quality Audits
A quality audit is a systematic and independent examination of a product, process, or system to determine whether it complies with specified standards and requirements. Quality audits help identify areas for improvement and ensure that the manufacturing processes are efficient and effective.
In the context of coating defects, a quality audit involves examining the surface finish of products to identify any imperfections that could affect their performance or appearance. These defects can result from various factors, including poor material quality, inadequate application techniques, or environmental conditions during the coating process.
Types of Coating Defects
To effectively address coating defects, it’s essential to understand the different types that can occur. Some common coating defects include:
1. **Orange Peel**: This defect appears as a rough, uneven surface that resembles the skin of an orange. It is often caused by incorrect application techniques or improper curing.
2. **Blistering**: Blisters are raised areas on the coated surface that can develop due to trapped air, moisture, or volatile substances within the coating.
3. **Cracking**: Cracks in the coating can occur due to excessive stress, poor adhesion, or improper curing. These cracks can compromise the integrity of the coating and lead to further issues.
4. **Peeling**: Peeling occurs when the coating loses adhesion to the substrate, leading to the separation of the layers. This can result from improper surface preparation or application.
5. **Fish Eyes**: These small, circular defects are caused by contamination of the coating material, often from oils, silicones, or other foreign substances.
Conducting a Quality Audit for Coating Defects
To effectively conduct a quality audit for coating defects, follow these steps:
1. **Prepare a Checklist**: Develop a comprehensive checklist that includes all the potential coating defects and their possible causes. This checklist will serve as a guide during the audit process.
2. **Inspect Using Various Techniques**: Utilize multiple inspection techniques to identify defects, such as visual inspection, microscopy, and non-destructive testing methods.
3. **Document Findings**: Record all identified defects, their locations, and possible causes. This documentation will be crucial for analyzing trends and implementing corrective actions.
4. **Analyze Data**: Review the documented defects to identify patterns or common issues. This analysis will help determine the root causes and prioritize corrective actions.
5. **Implement Corrective Actions**: Develop and implement corrective actions based on the findings of the quality audit. This could involve adjusting application techniques, improving material quality, or enhancing environmental controls.
Improving Procurement Processes
In addition to conducting quality audits, improving procurement processes is essential for preventing coating defects and ensuring high-quality products. Here are some strategies to enhance procurement:
1. **Select Reliable Suppliers**: Partner with suppliers known for their consistent quality and reliability. Conduct regular audits of suppliers to ensure they adhere to your quality standards.
2. **Specify Clear Requirements**: Provide detailed specifications for the materials and processes you require. This clarity will help suppliers understand your expectations and reduce the likelihood of defects.
3. **Evaluate Samples**: Request samples from suppliers before placing large orders. Evaluate these samples carefully to ensure they meet your quality standards.
4. **Implement Vendor Rating Systems**: Develop a vendor rating system to assess suppliers based on their performance, quality, and delivery times. This system will help you identify the best suppliers and incentivize them to maintain high standards.
5. **Foster Collaboration**: Establish open communication channels with suppliers to address any issues promptly. Collaborative relationships can lead to better problem-solving and continuous improvement.
Continuous Improvement and Problem Solving
Quality audits and improved procurement processes are crucial for enhancing product quality, but continuous improvement and problem-solving are equally important. Here are some strategies to foster a culture of continuous improvement:
1. **Train Employees**: Provide regular training for employees on quality standards, inspection techniques, and problem-solving methods. Well-trained employees are better equipped to identify and address coating defects.
2. **Use Quality Management Systems**: Implement quality management systems (QMS) such as ISO 9001 to standardize processes and ensure consistent quality. QMS can also help identify areas for improvement and track progress over time.
3. **Conduct Root Cause Analysis**: When defects are identified, perform root cause analysis to determine the underlying issues. Addressing the root causes will help prevent recurrence and improve overall quality.
4. **Encourage Feedback**: Foster a culture where employees feel comfortable providing feedback and suggesting improvements. Employee insights can lead to innovative solutions and better quality control.
5. **Monitor and Measure**: Continuously monitor and measure key performance indicators (KPIs) related to quality. Use this data to track progress, identify trends, and make informed decisions.
Conclusion
Improving product quality through effective quality audits and procurement of coating defects is essential for maintaining competitiveness in the market. By understanding the types of coating defects, conducting thorough quality audits, enhancing procurement processes, and fostering a culture of continuous improvement, manufacturers can ensure their products meet the highest standards and satisfy customer expectations. Investing in these quality measures can also lead to reduced costs, increased efficiency, and long-term success.
資料ダウンロード
QCD調達購買管理クラウド「newji」は、調達購買部門で必要なQCD管理全てを備えた、現場特化型兼クラウド型の今世紀最高の購買管理システムとなります。
ユーザー登録
調達購買業務の効率化だけでなく、システムを導入することで、コスト削減や製品・資材のステータス可視化のほか、属人化していた購買情報の共有化による内部不正防止や統制にも役立ちます。
NEWJI DX
製造業に特化したデジタルトランスフォーメーション(DX)の実現を目指す請負開発型のコンサルティングサービスです。AI、iPaaS、および先端の技術を駆使して、製造プロセスの効率化、業務効率化、チームワーク強化、コスト削減、品質向上を実現します。このサービスは、製造業の課題を深く理解し、それに対する最適なデジタルソリューションを提供することで、企業が持続的な成長とイノベーションを達成できるようサポートします。
オンライン講座
製造業、主に購買・調達部門にお勤めの方々に向けた情報を配信しております。
新任の方やベテランの方、管理職を対象とした幅広いコンテンツをご用意しております。
お問い合わせ
コストダウンが利益に直結する術だと理解していても、なかなか前に進めることができない状況。そんな時は、newjiのコストダウン自動化機能で大きく利益貢献しよう!
(Β版非公開)