- お役立ち記事
- Quality Audit of Electroless Plating Processes: Procurement’s Quality Assurance Perspective
Quality Audit of Electroless Plating Processes: Procurement’s Quality Assurance Perspective
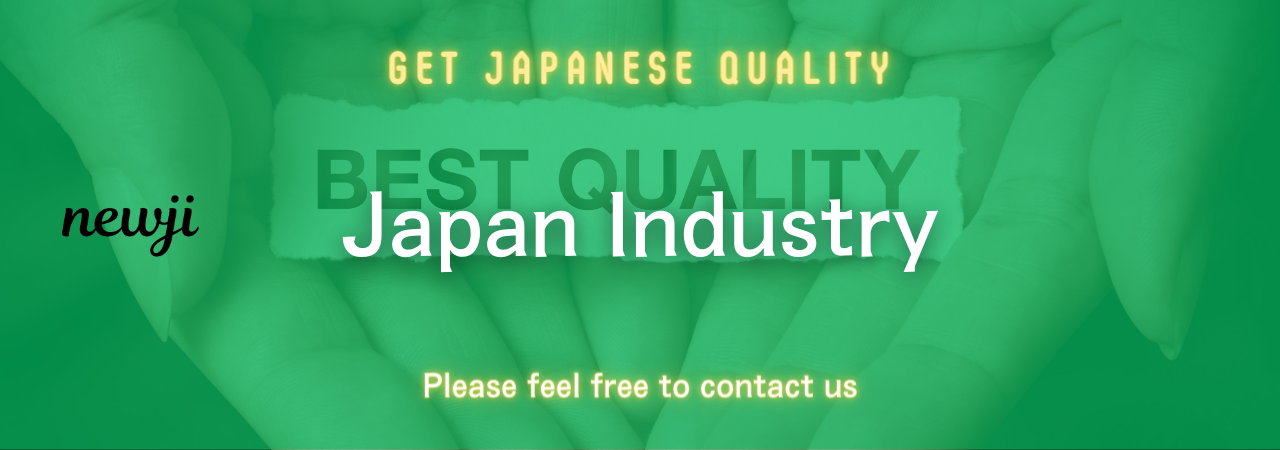
Electroless plating is a critical process in many industries, providing a durable and corrosion-resistant coating to various substrates.
Ensuring the quality of this process is imperative for maintaining product reliability and achieving customer satisfaction.
From procurement’s quality assurance perspective, this involves a rigorous quality audit of the electroless plating processes.
This article will explore the methodologies, key focus areas, and best practices for conducting an effective quality audit.
目次
Importance of Electroless Plating
Electroless plating, a chemical process that deposits a metal coating on a substrate without the use of an electric current, has wide-ranging applications in industries such as electronics, automotive, and aerospace.
The process delivers uniform coatings, even on complex geometries, enhancing wear resistance, corrosion protection, and electrical conductivity.
Given the critical roles these coated parts play, the quality of the electroless plating process directly impacts the end product’s performance and longevity.
Setting the Stage: Defining Quality Standards
Before initiating a quality audit, it is crucial to define the quality standards and acceptable criteria for the electroless plating process.
These standards should comply with industry regulations, customer specifications, and internal quality benchmarks.
Industry Standards and Compliance
The quality of electroless plating must meet industry standards such as ASTM B733 and ISO 4527.
These standards specify the requirements for the deposit characteristics, such as thickness, adhesion, and hardness.
Ensuring compliance with these regulations is the first step in a quality audit.
Customer Specifications
Each customer may have unique requirements for the electroless plating process.
These can include specific thickness, corrosion resistance levels, or visual appearance criteria.
Auditors must review and understand these specifications to evaluate whether the process meets the customer’s expectations.
Internal Quality Benchmarks
Organizations should have internal quality benchmarks based on historical data, process capabilities, and continuous improvement initiatives.
These benchmarks provide a reference point for assessing the current quality levels and identifying areas of improvement.
Quality Audit Methodologies
To effectively audit the electroless plating processes, a systematic approach and a range of methodologies are employed.
Process Mapping and Documentation Review
The audit begins with process mapping to understand the workflow, inputs, and outputs of the electroless plating process.
Reviewing documentation such as process control plans, standard operating procedures (SOPs), and past audit reports provides insights into the process controls and historical performance.
On-Site Inspection and Sampling
An on-site inspection is essential to verify the actual conditions and practices against the documented processes.
Auditors should observe the plating process, check equipment calibration, and ensure compliance with safety standards.
Sampling of plated parts for laboratory testing helps verify compliance with quality standards for thickness, adhesion, and other critical parameters.
Interviews with Key Personnel
Conducting interviews with operators, supervisors, and quality control personnel provides valuable insights into process understanding, training levels, and potential areas of improvement.
These discussions can reveal practical challenges and solutions that may not be evident from documentation alone.
Data Analysis and Trending
Analyzing process data, such as bath chemical composition, plating rates, and defect rates, helps identify trends and variability in the process.
Statistical process control (SPC) tools can be used to monitor process stability and capability, highlighting areas that require corrective actions.
Key Focus Areas in the Audit
Certain aspects of the electroless plating process warrant special attention during the quality audit.
Chemical Bath Management
The chemical bath is the heart of the electroless plating process.
Auditors should evaluate the procedure for bath preparation, monitoring, and replenishment.
Ensuring the correct concentration of chemicals, pH levels, and temperatures is crucial for consistent plating quality.
Regular analysis and filtration of the bath to remove contaminants and by-products is also important.
Surface Preparation
Proper surface preparation is essential for good adhesion and uniform coating.
The audit should review the cleaning, activation, and etching processes.
Checking for adherence to specifications for cleaning agents, grit sizes, and timings ensures that the substrate is ready for plating.
Plating Equipment and Maintenance
The condition and maintenance of plating equipment significantly impact the quality of the process.
Auditors should inspect equipment for wear and tear, proper calibration, and functionality.
Regular maintenance schedules and records should be reviewed to ensure that equipment operates optimally.
Quality Control Measures
The effectiveness of in-process and final quality control measures must be assessed.
This includes verifying the accuracy of thickness measurements, adhesion tests, and visual inspections.
Ensuring that quality control methods are robust and consistently applied helps in maintaining high-quality standards.
Training and Competence of Personnel
The skills and knowledge of personnel involved in the plating process are crucial for maintaining quality.
The audit should evaluate training programs, certification processes, and ongoing competency assessments to ensure that operators are well-equipped to perform their tasks.
Best Practices for Continuous Improvement
A quality audit is not just about identifying issues; it also aims to drive continuous improvement.
Root Cause Analysis
When non-conformities are detected, conducting a root cause analysis helps identify the underlying issues.
Using methodologies such as the 5 Whys or Fishbone Diagram, auditors can recommend effective corrective actions to prevent recurrence.
Implementing Corrective Actions
Implementing well-documented corrective actions is essential for resolving identified issues.
This includes updating SOPs, retraining personnel, or modifying equipment.
Regular follow-up audits ensure that corrective actions are effective and sustained.
Engaging Stakeholders
Engaging stakeholders such as operators, supervisors, and customers in the quality improvement process fosters a culture of quality.
Regular feedback loops, cross-functional teams, and transparent communication support continuous improvement initiatives.
Conclusion
A thorough quality audit of the electroless plating processes from procurement’s quality assurance perspective ensures that products meet the highest standards of reliability and customer satisfaction.
By adhering to industry standards, understanding customer specifications, and focusing on critical areas such as chemical bath management and surface preparation, organizations can achieve excellence in electroless plating.
Continuous improvement, driven by robust auditing practices and stakeholder engagement, is key to maintaining and enhancing process quality.
資料ダウンロード
QCD調達購買管理クラウド「newji」は、調達購買部門で必要なQCD管理全てを備えた、現場特化型兼クラウド型の今世紀最高の購買管理システムとなります。
ユーザー登録
調達購買業務の効率化だけでなく、システムを導入することで、コスト削減や製品・資材のステータス可視化のほか、属人化していた購買情報の共有化による内部不正防止や統制にも役立ちます。
NEWJI DX
製造業に特化したデジタルトランスフォーメーション(DX)の実現を目指す請負開発型のコンサルティングサービスです。AI、iPaaS、および先端の技術を駆使して、製造プロセスの効率化、業務効率化、チームワーク強化、コスト削減、品質向上を実現します。このサービスは、製造業の課題を深く理解し、それに対する最適なデジタルソリューションを提供することで、企業が持続的な成長とイノベーションを達成できるようサポートします。
オンライン講座
製造業、主に購買・調達部門にお勤めの方々に向けた情報を配信しております。
新任の方やベテランの方、管理職を対象とした幅広いコンテンツをご用意しております。
お問い合わせ
コストダウンが利益に直結する術だと理解していても、なかなか前に進めることができない状況。そんな時は、newjiのコストダウン自動化機能で大きく利益貢献しよう!
(Β版非公開)