- お役立ち記事
- Quality Control Issues and Countermeasures in Global Procurement for Manufacturing Companies
Quality Control Issues and Countermeasures in Global Procurement for Manufacturing Companies
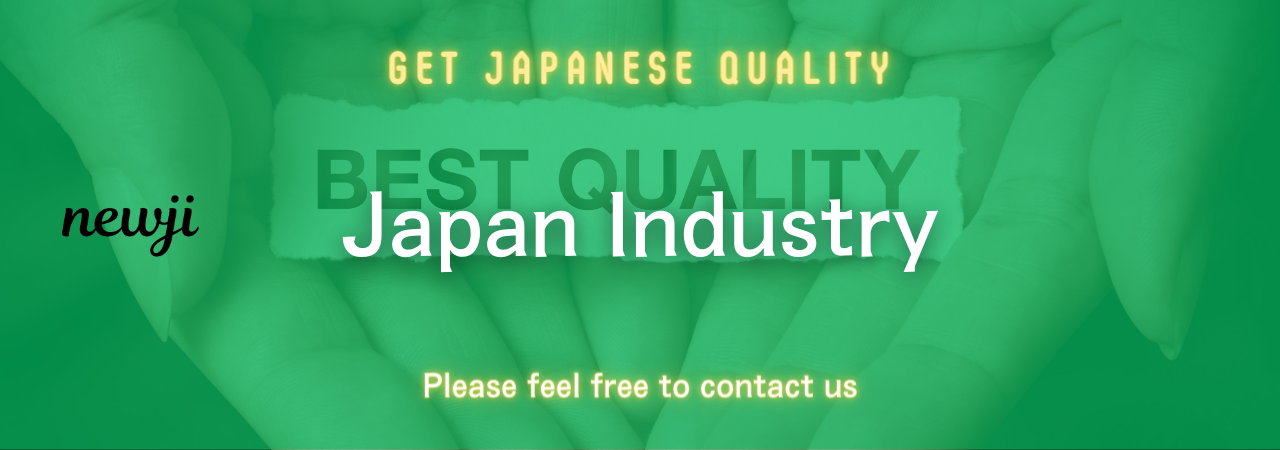
In the world of manufacturing, ensuring that products meet the highest standards is crucial.
But when companies source materials and components from across the globe, maintaining quality control can become a significant challenge.
Let’s explore some common quality control issues faced in global procurement and the countermeasures companies can employ.
目次
Common Quality Control Issues in Global Procurement
Inconsistent Standards
One of the primary issues in global procurement is the inconsistency in quality standards.
Different countries may have varying regulations and standards for the same material or component.
This can lead to discrepancies in product quality, which can be problematic for manufacturing companies aiming for uniformity in their products.
Communication Barriers
Another challenge is communication barriers.
Language differences and cultural nuances can lead to misunderstandings between suppliers and manufacturers.
Miscommunications can result in incorrect specifications, delays in production, and ultimately, sub-par products.
Logistical Challenges
Logistics also play a significant role in quality control.
If materials or components are damaged during transit, it can affect the final product’s quality.
Moreover, long lead times can result in delays, causing rushed production processes that may overlook quality assurance steps.
Lack of Supplier Oversight
When sourcing globally, it can be difficult to maintain consistent oversight of suppliers.
Without regular audits and inspections, manufacturers cannot ensure that suppliers are consistently meeting quality standards.
This lack of oversight can result in a decline in product quality over time.
Countermeasures for Quality Control
Standardizing Quality Requirements
To tackle inconsistent standards, manufacturing companies should establish clear and uniform quality requirements for all suppliers.
These requirements should be communicated effectively and regularly reviewed.
By setting a baseline standard, companies can ensure that all suppliers meet the same quality criteria.
Implementing Robust Communication Strategies
Effective communication is key to overcoming barriers.
Companies can employ multilingual staff or use translation services to bridge language gaps.
Regular and transparent communication channels should be established to prevent misunderstandings and ensure that all parties are on the same page.
Enhancing Logistics Management
To address logistical challenges, manufacturers can invest in robust logistics management systems.
These systems can track shipments in real-time, ensuring that any issues are promptly addressed.
Additionally, working with reliable logistics partners can minimize the risk of damage during transit and reduce lead times.
Conducting Regular Supplier Audits
Regular supplier audits and inspections are crucial for maintaining quality control.
These audits can help identify potential issues before they impact production.
By establishing a consistent audit schedule, companies can ensure that suppliers adhere to quality standards and make necessary improvements.
Investing in Quality Control Technologies
Leveraging technology can significantly enhance quality control measures.
Quality control technologies, such as automated inspection systems and quality management software, can provide real-time data and insights.
These tools can help identify deviations from quality standards early in the production process, allowing for prompt corrective actions.
Building Strong Supplier Relationships
Collaborative Partnerships
Building strong relationships with suppliers can foster collaboration and mutual understanding.
When suppliers feel valued and included in the process, they are more likely to adhere to quality standards.
Regular meetings and visits can strengthen these partnerships, ensuring that both parties work towards the same quality objectives.
Training and Development
Investing in training and development for suppliers can also improve quality control.
By providing training programs on quality standards and best practices, manufacturers can help suppliers enhance their operations.
This proactive approach can lead to consistent improvements in product quality.
Conclusion
Quality control in global procurement for manufacturing companies is undoubtedly challenging, but it is not insurmountable.
By recognizing common quality control issues and implementing effective countermeasures, companies can ensure that their products meet the highest standards.
Establishing clear quality requirements, enhancing communication, improving logistics, conducting regular audits, leveraging technology, and building strong supplier relationships are all essential steps in maintaining quality control.
Through these efforts, manufacturers can achieve consistency and excellence in their products, regardless of where their materials and components are sourced.
資料ダウンロード
QCD調達購買管理クラウド「newji」は、調達購買部門で必要なQCD管理全てを備えた、現場特化型兼クラウド型の今世紀最高の購買管理システムとなります。
ユーザー登録
調達購買業務の効率化だけでなく、システムを導入することで、コスト削減や製品・資材のステータス可視化のほか、属人化していた購買情報の共有化による内部不正防止や統制にも役立ちます。
NEWJI DX
製造業に特化したデジタルトランスフォーメーション(DX)の実現を目指す請負開発型のコンサルティングサービスです。AI、iPaaS、および先端の技術を駆使して、製造プロセスの効率化、業務効率化、チームワーク強化、コスト削減、品質向上を実現します。このサービスは、製造業の課題を深く理解し、それに対する最適なデジタルソリューションを提供することで、企業が持続的な成長とイノベーションを達成できるようサポートします。
オンライン講座
製造業、主に購買・調達部門にお勤めの方々に向けた情報を配信しております。
新任の方やベテランの方、管理職を対象とした幅広いコンテンツをご用意しております。
お問い合わせ
コストダウンが利益に直結する術だと理解していても、なかなか前に進めることができない状況。そんな時は、newjiのコストダウン自動化機能で大きく利益貢献しよう!
(Β版非公開)