- お役立ち記事
- Quality Control Secrets to Prevent Issues in Resin Processing
月間76,176名の
製造業ご担当者様が閲覧しています*
*2025年3月31日現在のGoogle Analyticsのデータより
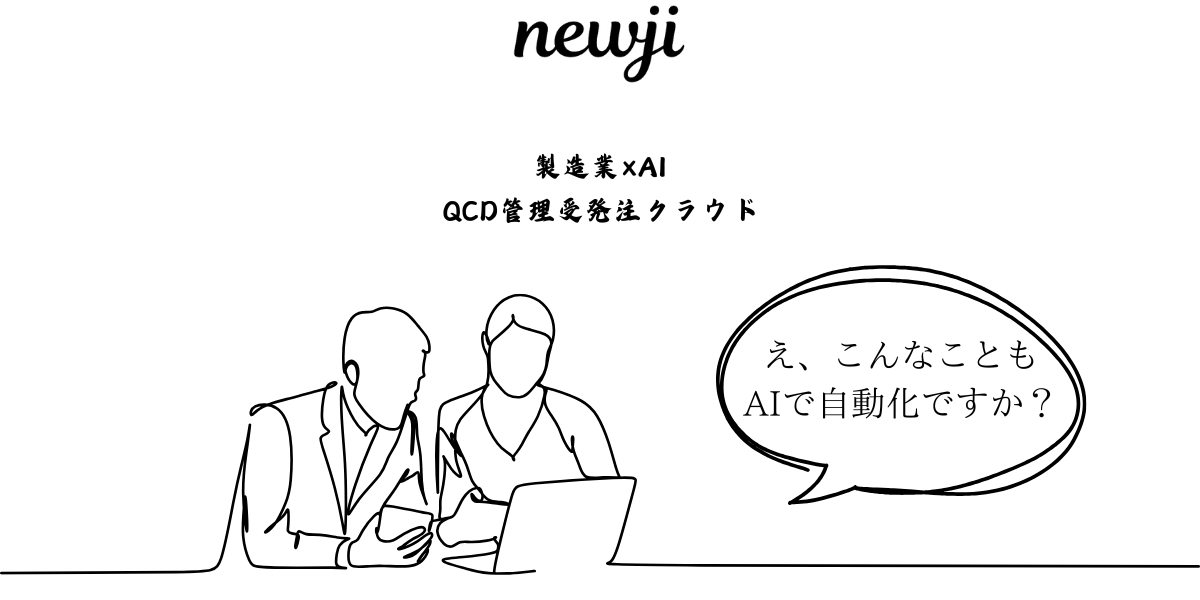
Quality Control Secrets to Prevent Issues in Resin Processing
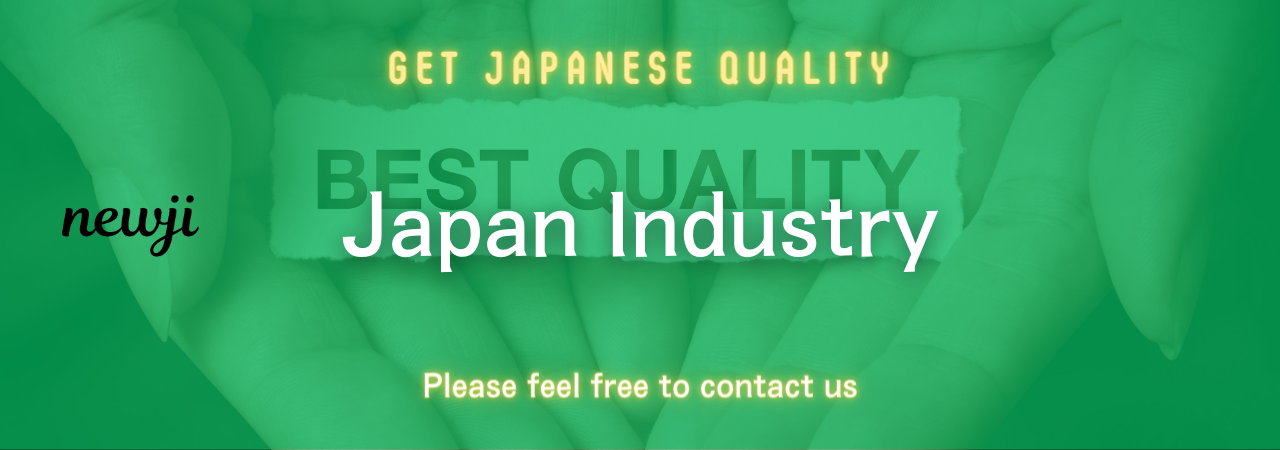
Resin processing is an intricate and vital step in manufacturing many products, from household items to complex automotive parts.
To ensure high-quality outcomes, maintaining stringent quality control measures is paramount.
This article delves into some crucial secrets to prevent issues in resin processing, enabling manufacturers to create superior products.
目次
Understanding Resin Types and Their Characteristics
Thermoplastic Resins
Thermoplastic resins are widely used due to their ability to be melted and molded multiple times without significant degradation.
Common examples include polyethylene (PE), polypropylene (PP), and polyvinyl chloride (PVC).
Understanding the specific characteristics of these resins, such as melting point and flow properties, is essential for effective quality control.
Thermoset Resins
Unlike thermoplastics, thermoset resins undergo a curing process that makes them infusible and unmoldable once set.
Examples include epoxy, phenolic, and melamine resins.
Quality control in thermoset resin processing requires careful attention to curing conditions and mixing ratios to prevent defects.
Importance of Raw Material Quality
Purer Resins for Better Results
The purity of raw resin significantly impacts the final product quality.
Impurities can lead to inconsistencies, defects, and reduced performance.
Ensuring the use of high-purity resins by working with reputable suppliers helps prevent processing issues.
Consistent Supply Chain
A consistent supply chain ensures that the raw materials received have uniform properties.
Variation in raw materials can disrupt the processing parameters, leading to defects.
Building strong relationships with suppliers for reliable and consistent material quality is vital.
Precise Control of Processing Parameters
Temperature Control
Maintaining the correct temperature during resin processing is crucial.
Excess heat can degrade the resin, while insufficient heat might not melt the resin properly.
Using precise temperature control systems helps achieve optimal processing conditions.
Pressure Management
Proper pressure management during molding prevents defects like voids and uneven thickness.
Controlling injection pressures, holding pressures, and cooling pressures ensures smooth resin flow and uniform filling of molds.
Consistent pressure control techniques enhance product quality.
Speed and Timing
Speed and timing are critical in resin processing.
For thermoplastic resins, swift injection and proper cycle times are necessary.
In thermoset resins, mixing and curing times must be meticulously controlled.
Monitoring and fine-tuning these parameters helps achieve uniformity and reduces processing issues.
Equipment Maintenance and Calibration
Regular Inspections
Regular maintenance and inspection of processing equipment can prevent unexpected breakdowns and inconsistencies.
Inspecting machines for wear and tear, checking calibration, and ensuring all components are functioning correctly safeguards against processing issues.
Calibration of Instruments
Calibration of measuring instruments like thermometers, pressure gauges, and timers is essential.
Accurate measurements ensure that processing parameters remain consistent.
Periodic calibration helps maintain the quality and precision of the final product.
Effective Mold Design
Optimal Gate Design
The design of the gate through which the resin enters the mold significantly impacts the quality of the molded part.
An optimal gate design ensures smooth resin flow and minimizes issues like air entrapment or weld lines.
Efficient Cooling Channels
Proper cooling channels within the mold help maintain uniform cooling.
Efficient cooling prevents warping and residual stresses in the molded parts.
Designing molds with effective cooling channels enhances the overall product quality.
Monitoring and Automation
In-Line Quality Monitoring
Implementing in-line quality monitoring systems can detect defects in real-time.
These systems can track parameters such as resin flow, temperature, and pressure.
Any deviation from set standards triggers an alert, enabling immediate corrective actions.
Automation for Consistency
Automation reduces human error and maintains processing consistency.
Robotic systems and automated controls ensure precise handling of resin and accurate execution of processing steps.
Investing in automation technology improves efficiency and product quality.
Training and Skill Development
Operator Training
Skilled operators are essential for maintaining quality in resin processing.
Regular training programs ensure that operators understand the nuances of the materials, machines, and processes they work with.
Well-trained operators can quickly identify and rectify issues, maintaining high-quality standards.
Continuous Learning
Encouraging continuous learning and staying updated with the latest advancements in resin processing technologies is beneficial.
Participating in industry conferences, workshops, and training sessions keeps the workforce knowledgeable and adept at handling new challenges.
Implementing Quality Assurance Protocols
Inspection and Testing
Regular inspection and testing of processed parts are crucial to identify defects early.
Implementing non-destructive testing methods ensures that quality is maintained without damaging the parts.
Routine testing helps in detecting issues before they become significant problems.
Documentation and Traceability
Maintaining thorough documentation and traceability of each batch of processed resin helps identify sources of issues.
Accurate records of raw materials, processing parameters, and final inspections create a robust quality assurance framework.
Ensuring high-quality outcomes in resin processing involves a combination of understanding resin characteristics, maintaining precise processing parameters, and implementing robust quality control measures.
By focusing on these key aspects, manufacturers can prevent issues and produce superior products consistently.
資料ダウンロード
QCD管理受発注クラウド「newji」は、受発注部門で必要なQCD管理全てを備えた、現場特化型兼クラウド型の今世紀最高の受発注管理システムとなります。
ユーザー登録
受発注業務の効率化だけでなく、システムを導入することで、コスト削減や製品・資材のステータス可視化のほか、属人化していた受発注情報の共有化による内部不正防止や統制にも役立ちます。
NEWJI DX
製造業に特化したデジタルトランスフォーメーション(DX)の実現を目指す請負開発型のコンサルティングサービスです。AI、iPaaS、および先端の技術を駆使して、製造プロセスの効率化、業務効率化、チームワーク強化、コスト削減、品質向上を実現します。このサービスは、製造業の課題を深く理解し、それに対する最適なデジタルソリューションを提供することで、企業が持続的な成長とイノベーションを達成できるようサポートします。
製造業ニュース解説
製造業、主に購買・調達部門にお勤めの方々に向けた情報を配信しております。
新任の方やベテランの方、管理職を対象とした幅広いコンテンツをご用意しております。
お問い合わせ
コストダウンが利益に直結する術だと理解していても、なかなか前に進めることができない状況。そんな時は、newjiのコストダウン自動化機能で大きく利益貢献しよう!
(β版非公開)