- お役立ち記事
- Quality Control Tips for Epoxy Resin Molding
月間76,176名の
製造業ご担当者様が閲覧しています*
*2025年3月31日現在のGoogle Analyticsのデータより
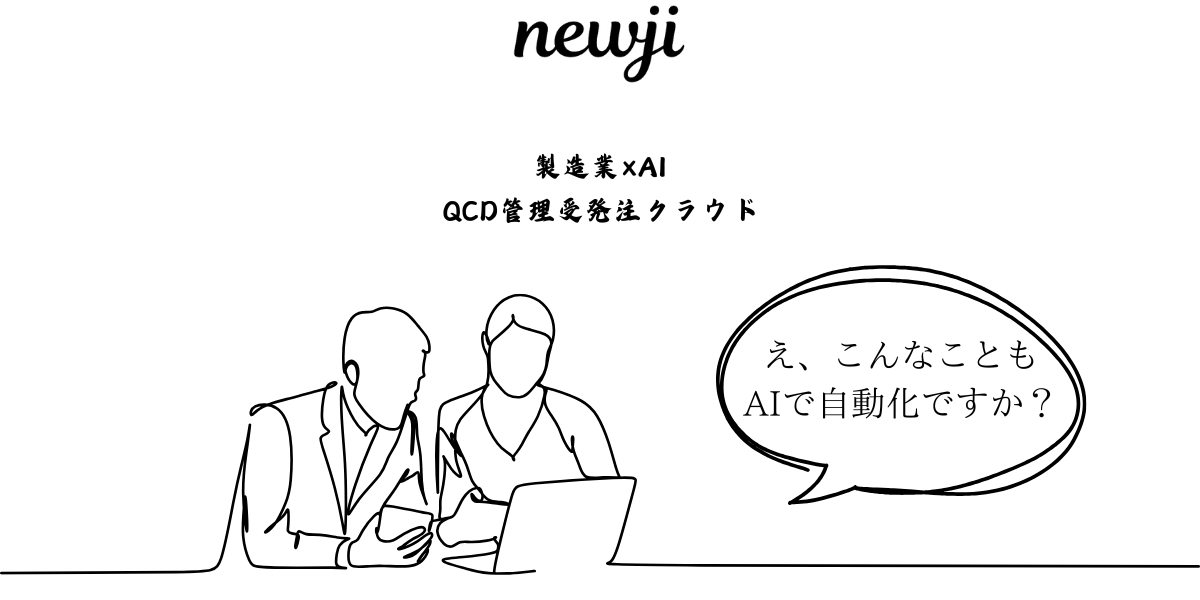
Quality Control Tips for Epoxy Resin Molding
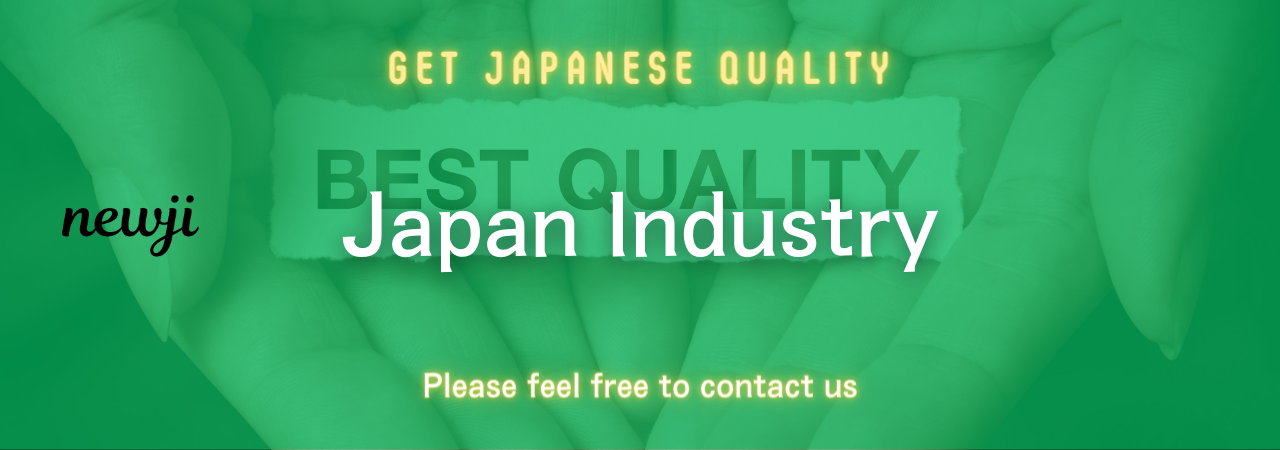
目次
Understanding Epoxy Resin Molding
Epoxy resin is an incredibly versatile and durable material commonly used in molding applications across various industries, from art and crafts to construction and electronics.
The process of epoxy resin molding involves mixing two components, the resin, and hardener, which chemically react and cure into a solid form.
This material is praised for its strong adhesive qualities, chemical resistance, and durability.
However, achieving a high-quality finish in epoxy resin molding requires attention to detail and careful quality control.
Ensuring the right techniques and conditions can dramatically affect the outcome of your epoxy work.
Importance of Quality Control
Quality control is vital in epoxy resin molding to ensure that the final product meets the desired specifications and quality standards.
Without proper quality control, epoxy castings can suffer from defects such as bubbles, uneven surfaces, or incomplete curing, which can decrease aesthetic appeal or functionality.
Implementing thorough and effective quality control measures can help identify potential problems early, ensuring a sustainable process and high-quality end products.
This begins with understanding the material itself, the working conditions, and the techniques used during the molding process.
Choosing the Right Epoxy Resin
The quality of the epoxy resin plays a significant role in determining the success of your project.
There are numerous types of epoxy resins available in the market, each with its own specific properties and applications.
When selecting an epoxy resin, consider factors such as cure time, temperature resistance, clarity, and flexibility.
For instance, a slow-curing epoxy may be more suitable for larger projects that require additional working time, while faster curing options are beneficial for projects demanding quick turnarounds.
Research and choose a resin that aligns with your project’s specific needs and expected outcomes.
Understanding Resin and Hardener Ratios
Another critical aspect of epoxy resin molding is adhering to the recommended resin and hardener mixing ratios.
Most manufacturers specify a precise ratio that must be followed to ensure the epoxy cures correctly.
Deviating from these guidelines may lead to incomplete curing or weaker final products.
It is crucial to measure both components accurately and mix them thoroughly for the chemical reaction to be successful.
Using digital scales and reliable measuring containers can help maintain accuracy and consistency in your mixes.
Temperature and Environment Control
The environment in which you work with epoxy resin is a significant factor affecting the quality of the result.
Temperature and humidity can influence how well the resin cures.
Typically, epoxy resin works best at room temperature, around 70°F (21°C).
If the temperature is too low, the curing process will slow down, potentially causing a sticky or uneven finish.
Conversely, too high a temperature can accelerate curing too much, giving you less time to work with the material.
Managing Humidity
Humidity also plays a crucial role as high humidity can introduce moisture into the epoxy.
This can create a cloudy appearance or fisheyes on the surface.
To combat this, ensure your workspace is dry and, if necessary, use a dehumidifier to control moisture levels.
By maintaining optimal environmental conditions, you can improve the quality and clarity of the final product.
Proper Mixing Techniques
Correct mixing techniques are essential to avoid introducing air bubbles into the resin, which can mar the surface finish.
When combining the resin and hardener, stir slowly and gently to minimize air entrapment.
Using a mixing tool that reaches all the container’s edges can help achieve a consistent mix.
Additionally, using a clear mixing container helps ensure all parts are fully incorporated as you can see whether there are any unmixed remnants settled at the bottom or sides.
Using Vacuum Chambers and Pressure Pots
For those committed to achieving bubble-free castings, implementing vacuum chambers or pressure pots can significantly enhance quality.
Vacuum chambers work by removing air bubbles before the curing process begins, while pressure pots compress and minimize any remaining bubbles after the mold is poured.
These tools transform the creation process and are especially beneficial for intricate molds or transparent castings where every detail matters.
Applying Release Agents
Using mold release agents is an essential step in the epoxy resin molding process.
These agents are applied to molds to prevent the resin from sticking, facilitating easy demolding and protecting the surface of the mold.
Ensure the release agent is compatible with both the mold material and the epoxy resin.
Applying the agent evenly and thoroughly will prevent defects and prolong the life of your molds.
Careful maintenance of molds and release agents ensures a smoother production cycle with consistent quality.
Curing Time and Post-Curing
Allowing sufficient curing time is critical, as moving or handling the epoxy before it is fully cured can lead to surface damage or structural flaws.
Follow the manufacturer’s guidelines for curing time based on room temperature and project size.
For projects requiring additional strength or temperature resistance, a post-curing process may be necessary.
This involves exposing the cured epoxy resin to an elevated temperature for a designated period to enhance its properties.
Check that your mold and castings can withstand this heat without compromising their structure or details.
Inspection and Testing
Once curing is complete, inspecting the epoxy castings for defects or inconsistencies is important.
Visual inspections can help identify surface issues like bubbles, irregularities, or discoloration.
For functional pieces, consider conducting tests to ensure the item meets durability, temperature resistance, and structural strength requirements.
Implementing an inspection regimen helps maintain high standards and ensures that all products are consistent and reliable.
By incorporating these quality control tips into your epoxy resin molding process, you can significantly improve the quality and reliability of your projects.
Paying attention to detail during material selection, mixing, environmental conditions, and follow-up processes will help produce professional-grade epoxy castings.
資料ダウンロード
QCD管理受発注クラウド「newji」は、受発注部門で必要なQCD管理全てを備えた、現場特化型兼クラウド型の今世紀最高の受発注管理システムとなります。
ユーザー登録
受発注業務の効率化だけでなく、システムを導入することで、コスト削減や製品・資材のステータス可視化のほか、属人化していた受発注情報の共有化による内部不正防止や統制にも役立ちます。
NEWJI DX
製造業に特化したデジタルトランスフォーメーション(DX)の実現を目指す請負開発型のコンサルティングサービスです。AI、iPaaS、および先端の技術を駆使して、製造プロセスの効率化、業務効率化、チームワーク強化、コスト削減、品質向上を実現します。このサービスは、製造業の課題を深く理解し、それに対する最適なデジタルソリューションを提供することで、企業が持続的な成長とイノベーションを達成できるようサポートします。
製造業ニュース解説
製造業、主に購買・調達部門にお勤めの方々に向けた情報を配信しております。
新任の方やベテランの方、管理職を対象とした幅広いコンテンツをご用意しております。
お問い合わせ
コストダウンが利益に直結する術だと理解していても、なかなか前に進めることができない状況。そんな時は、newjiのコストダウン自動化機能で大きく利益貢献しよう!
(β版非公開)