- お役立ち記事
- Quality Improvement in Extrusion Molding Using Thermorunner Technology
月間76,176名の
製造業ご担当者様が閲覧しています*
*2025年3月31日現在のGoogle Analyticsのデータより
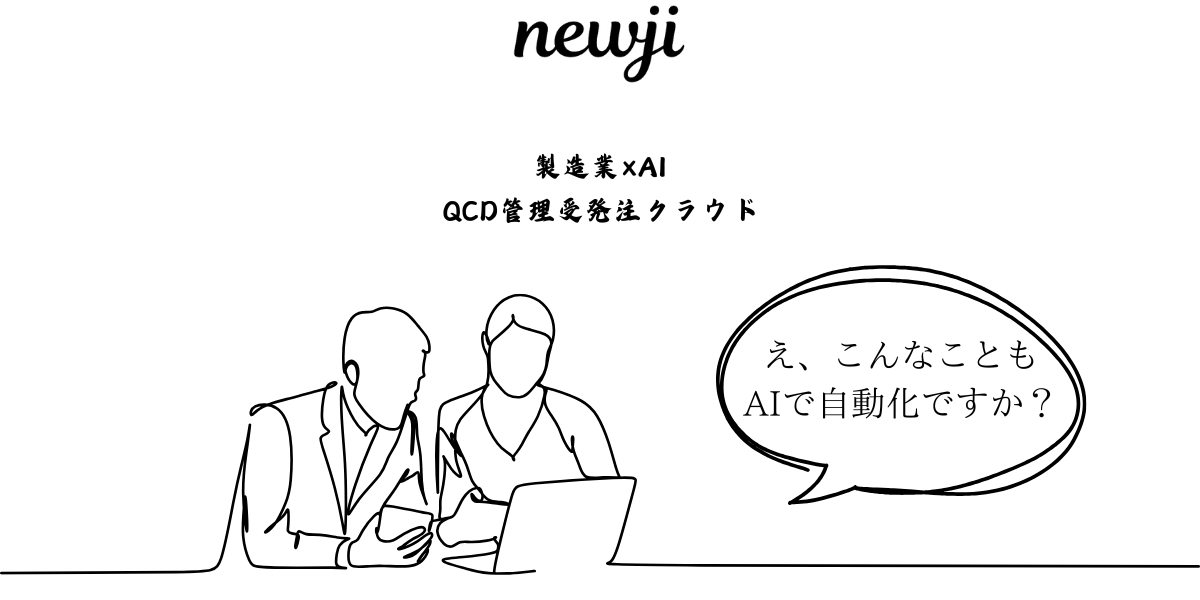
Quality Improvement in Extrusion Molding Using Thermorunner Technology
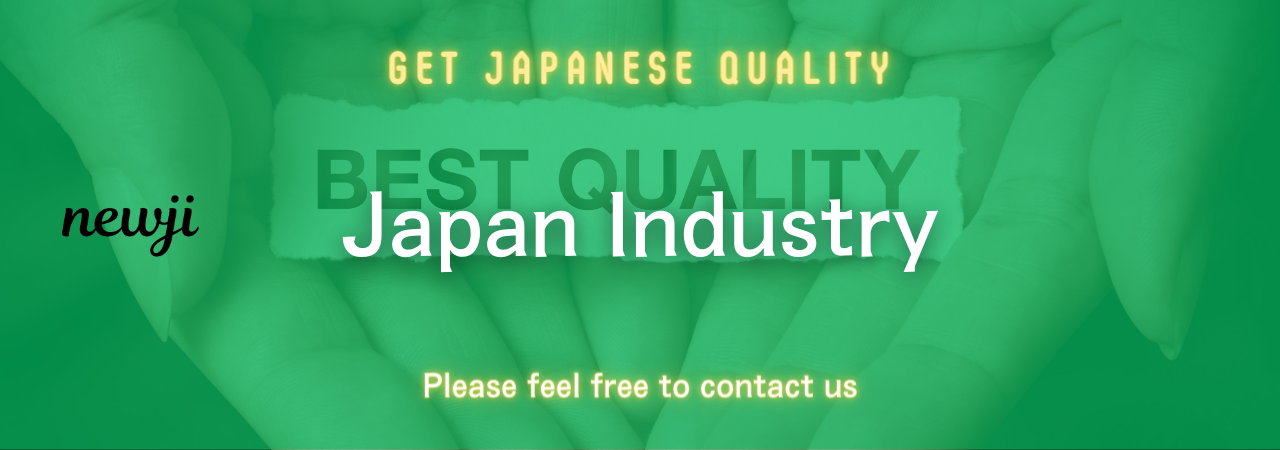
目次
Introduction to Extrusion Molding
Extrusion molding is a manufacturing process used to create objects with a fixed cross-sectional profile.
It involves pushing material, often plastic, through a mold to form shapes like pipes, tubing, and sheets.
The quality of these products is vital, especially in industries like automotive, construction, and packaging.
Importance of Quality Improvement in Extrusion Molding
Quality in extrusion molding ensures the durability, safety, and functionality of the final products.
Defects such as surface inconsistencies, dimensional inaccuracies, and improper material properties can lead to failures and rejections.
Thus, improving quality reduces waste, costs, and time, and enhances customer satisfaction.
What is Thermorunner Technology?
Thermorunner technology is an advanced method used to improve the extrusion molding process.
It focuses on controlling and optimizing the temperature profiles of the extrusion machinery.
By doing so, it ensures uniform melting, better material mixing, and consistent product quality.
This technological innovation is crucial for manufacturers aiming to meet high-standard production demands.
How Thermorunner Technology Works
Thermorunner technology operates by integrating precise temperature monitoring and control systems into extrusion equipment.
These systems can detect even minor fluctuations in temperature and make real-time adjustments.
This accurate control helps prevent overheating or underheating, which can cause material defects.
Furthermore, it enhances the overall stability and reliability of the extrusion process.
Benefits of Using Thermorunner Technology in Extrusion Molding
Enhanced Product Consistency
One of the primary benefits of using Thermorunner technology is the consistency it brings to products.
By maintaining a stable temperature throughout the extrusion process, the material properties remain uniform.
This results in products that meet exact specifications every time, reducing the variation between batches.
Reduced Material Waste
Temperature fluctuations can lead to material wastage due to defects and required reworks.
Thermorunner technology minimizes this by ensuring optimal conditions for material processing.
This reduction in waste not only helps in saving costs but also promotes environmental sustainability.
Improved Energy Efficiency
Traditional extrusion processes often consume more energy due to inefficient temperature control.
Thermorunner technology optimizes energy use by maintaining desired temperatures and reducing unnecessary energy expenditure.
This leads to lower energy bills and a smaller carbon footprint, contributing to a greener manufacturing process.
Faster Production Cycles
With precise temperature control, the extrusion process becomes more efficient.
This efficiency translates to faster production cycles as there is less downtime due to errors or defects.
Manufacturers can increase their output without compromising on quality, meeting higher market demands more effectively.
Implementation of Thermorunner Technology
Initial Assessment and Integration
Before implementing Thermorunner technology, a thorough assessment of the existing extrusion systems is essential.
Engineers analyze current processes, identify areas of improvement, and develop a customized integration plan.
This ensures a seamless transition and maximizes the benefits of the new technology.
Training and Skill Development
To fully leverage Thermorunner technology, personnel involved in the extrusion process must receive adequate training.
This training focuses on operating the new systems, understanding temperature control dynamics, and troubleshooting common issues.
Skilled operators ensure the technology is used to its full potential, maintaining high standards of quality.
Continuous Monitoring and Maintenance
Once implemented, continuous monitoring is crucial to maintain the benefits of Thermorunner technology.
Regular maintenance checks, updates, and performance evaluations help in sustaining optimal operation.
Feedback loops and data analysis also play a significant role in identifying further improvement opportunities.
Case Studies: Success Stories
Many companies have successfully integrated Thermorunner technology into their extrusion molding processes.
For instance, a leading automotive parts manufacturer reported a 20% increase in production efficiency and a 15% reduction in material waste.
Another example is a packaging company that saw a significant improvement in product consistency and a substantial decrease in defect rates.
Automotive Parts Manufacturer
This manufacturer faced issues with dimensional accuracy and surface smoothness in their products.
After adopting Thermorunner technology, they achieved precise temperature control, leading to better material flow and uniformity.
The outcome was a marked improvement in product quality and a substantial cost saving on materials.
Packaging Company
In the packaging industry, consistency and reliability are critical.
The packaging company used Thermorunner technology to stabilize their extrusion process.
This resulted in fewer product rejects, higher customer satisfaction, and a competitive edge in the market.
Future Prospects
The future of extrusion molding looks promising with continued advancements in Thermorunner technology.
As the technology evolves, we can expect even more efficient and precise control systems.
These innovations will drive further improvements in quality, energy efficiency, and overall production capacity.
Research and Development
Ongoing research in materials science and engineering will contribute to the advancement of Thermorunner technology.
Collaborations between academia and industry will lead to innovative solutions, enhancing the extrusion molding process even further.
Wider Industry Adoption
As more industries recognize the benefits of Thermorunner technology, wider adoption is inevitable.
Standardizing this technology across various sectors will set new benchmarks for quality and efficiency in extrusion molding.
Conclusion
Thermorunner technology is revolutionizing the extrusion molding industry by ensuring precise temperature control, enhancing product quality, and improving overall efficiency.
Manufacturers adopting this technology can expect significant benefits, including reduced material waste, faster production cycles, and lower energy costs.
As we look to the future, continued innovations in Thermorunner technology promise to set new standards for the industry, driving further advancements and widespread adoption.
With proper implementation and training, manufacturers can harness the full potential of Thermorunner technology, ensuring high-quality production and meeting ever-growing market demands.
資料ダウンロード
QCD管理受発注クラウド「newji」は、受発注部門で必要なQCD管理全てを備えた、現場特化型兼クラウド型の今世紀最高の受発注管理システムとなります。
ユーザー登録
受発注業務の効率化だけでなく、システムを導入することで、コスト削減や製品・資材のステータス可視化のほか、属人化していた受発注情報の共有化による内部不正防止や統制にも役立ちます。
NEWJI DX
製造業に特化したデジタルトランスフォーメーション(DX)の実現を目指す請負開発型のコンサルティングサービスです。AI、iPaaS、および先端の技術を駆使して、製造プロセスの効率化、業務効率化、チームワーク強化、コスト削減、品質向上を実現します。このサービスは、製造業の課題を深く理解し、それに対する最適なデジタルソリューションを提供することで、企業が持続的な成長とイノベーションを達成できるようサポートします。
製造業ニュース解説
製造業、主に購買・調達部門にお勤めの方々に向けた情報を配信しております。
新任の方やベテランの方、管理職を対象とした幅広いコンテンツをご用意しております。
お問い合わせ
コストダウンが利益に直結する術だと理解していても、なかなか前に進めることができない状況。そんな時は、newjiのコストダウン自動化機能で大きく利益貢献しよう!
(β版非公開)