- お役立ち記事
- Quality Improvement in Injection Molding through Cold Lag Well Optimization
Quality Improvement in Injection Molding through Cold Lag Well Optimization
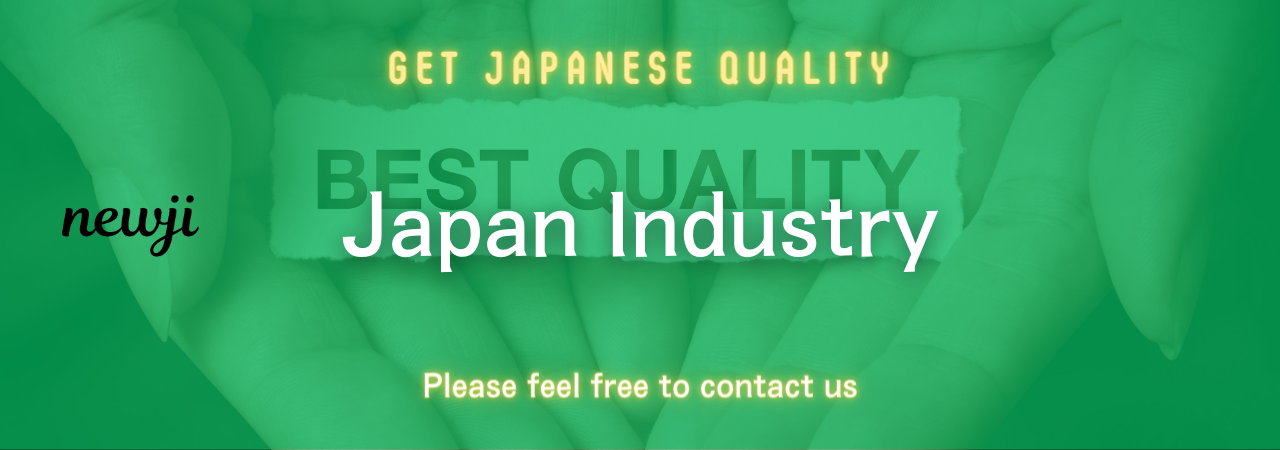
Injection molding is a widely used manufacturing process for producing plastic parts.
One key aspect of ensuring high-quality products in injection molding is the optimization of various parameters and components involved in the process.
In this article, we will delve into the importance of cold lag well optimization and how it can significantly enhance the quality of injection-molded products.
目次
What is Injection Molding?
Injection molding is a manufacturing process primarily used for producing plastic parts in large quantities.
The process involves injecting molten plastic into a mold cavity, where it cools and solidifies to form the desired shape.
This technique is commonly used for making a wide range of products, from automotive components to household items.
The Role of Cold Lag Well in Injection Molding
Understanding Cold Lag Well
The cold lag well is an essential component within the injection molding process.
It is a section in the mold where the initial molten plastic, which is often cooler and less fluid, can flow and be held temporarily.
This initial flow, known as the “cold slug,” can adversely affect the quality of the final product if not managed properly.
Importance of Cold Lag Well Optimization
Optimizing the cold lag well is crucial for several reasons.
Firstly, it helps in maintaining a consistent flow of the molten plastic, ensuring that the material fills the mold cavity evenly.
Secondly, it minimizes the presence of defects such as voids, warping, and surface imperfections.
Finally, optimizing this component can lead to improved overall cycle times, enhancing productivity.
Steps to Optimize Cold Lag Well
Material Selection
Choosing the right material for the mold and the cold lag well is fundamental.
Materials with high thermal conductivity are preferred as they can quickly transfer heat away from the molten plastic, allowing it to solidify uniformly.
This helps in reducing cycle times and improving the quality of the final product.
Design Considerations
The design of the cold lag well should be such that it effectively captures the initial cooler flow of molten plastic.
It should be strategically positioned to prevent any colder material from entering the final mold cavity.
Additionally, the size and shape of the cold lag well should be optimized to ensure efficient thermal management.
Temperature Control
Maintaining precise temperature control is vital for cold lag well optimization.
Utilizing advanced temperature monitoring systems can help in maintaining the ideal temperature within the mold.
This ensures that the molten plastic flows consistently and solidifies correctly, reducing the risk of defects.
Benefits of Optimizing Cold Lag Well
Improved Product Quality
One of the primary benefits of cold lag well optimization is the significant improvement in product quality.
By ensuring a consistent flow and uniform solidification of the molten plastic, defects such as voids and warping can be minimized.
This results in a higher quality final product that meets the desired specifications and standards.
Enhanced Efficiency
Optimizing the cold lag well also leads to enhanced efficiency in the injection molding process.
With better thermal management and material flow, cycle times can be reduced, leading to increased productivity.
This means more products can be manufactured in a shorter amount of time without compromising on quality.
Cost Savings
Improved efficiency and reduced defects translate to significant cost savings for manufacturers.
By minimizing waste and rework, production costs can be lowered.
Additionally, the optimized process can lead to reduced energy consumption, further contributing to cost savings.
Challenges in Cold Lag Well Optimization
Complexity of Design
One of the main challenges in optimizing the cold lag well is the complexity of the design.
Ensuring that the cold lag well is strategically positioned and adequately sized requires careful planning and analysis.
This often involves using advanced simulation software to predict the flow behavior and thermal characteristics of the molten plastic.
Maintaining Consistent Temperature
Another challenge is maintaining a consistent temperature within the mold.
Fluctuations in temperature can lead to uneven solidification and defects in the final product.
Implementing advanced temperature control systems can be costly and requires specialized knowledge.
Material Compatibility
Selecting materials that are compatible with the molten plastic and the mold can also be a challenge.
Materials with high thermal conductivity are preferred, but they must also be durable and able to withstand the rigors of the injection molding process.
Conclusion
In conclusion, optimizing the cold lag well is a critical aspect of enhancing the quality of injection-molded products.
Through careful material selection, strategic design, and precise temperature control, manufacturers can achieve significant improvements in product quality, efficiency, and cost savings.
While there are challenges involved in this optimization process, the benefits far outweigh the difficulties.
By focusing on the optimization of the cold lag well, manufacturers can ensure that their injection molding processes are efficient, cost-effective, and capable of producing high-quality products consistently.
資料ダウンロード
QCD調達購買管理クラウド「newji」は、調達購買部門で必要なQCD管理全てを備えた、現場特化型兼クラウド型の今世紀最高の購買管理システムとなります。
ユーザー登録
調達購買業務の効率化だけでなく、システムを導入することで、コスト削減や製品・資材のステータス可視化のほか、属人化していた購買情報の共有化による内部不正防止や統制にも役立ちます。
NEWJI DX
製造業に特化したデジタルトランスフォーメーション(DX)の実現を目指す請負開発型のコンサルティングサービスです。AI、iPaaS、および先端の技術を駆使して、製造プロセスの効率化、業務効率化、チームワーク強化、コスト削減、品質向上を実現します。このサービスは、製造業の課題を深く理解し、それに対する最適なデジタルソリューションを提供することで、企業が持続的な成長とイノベーションを達成できるようサポートします。
オンライン講座
製造業、主に購買・調達部門にお勤めの方々に向けた情報を配信しております。
新任の方やベテランの方、管理職を対象とした幅広いコンテンツをご用意しております。
お問い合わせ
コストダウンが利益に直結する術だと理解していても、なかなか前に進めることができない状況。そんな時は、newjiのコストダウン自動化機能で大きく利益貢献しよう!
(Β版非公開)