- お役立ち記事
- Quality inspection techniques using roundness measuring machines that operators in the precision machinery industry should know
月間77,185名の
製造業ご担当者様が閲覧しています*
*2025年2月28日現在のGoogle Analyticsのデータより
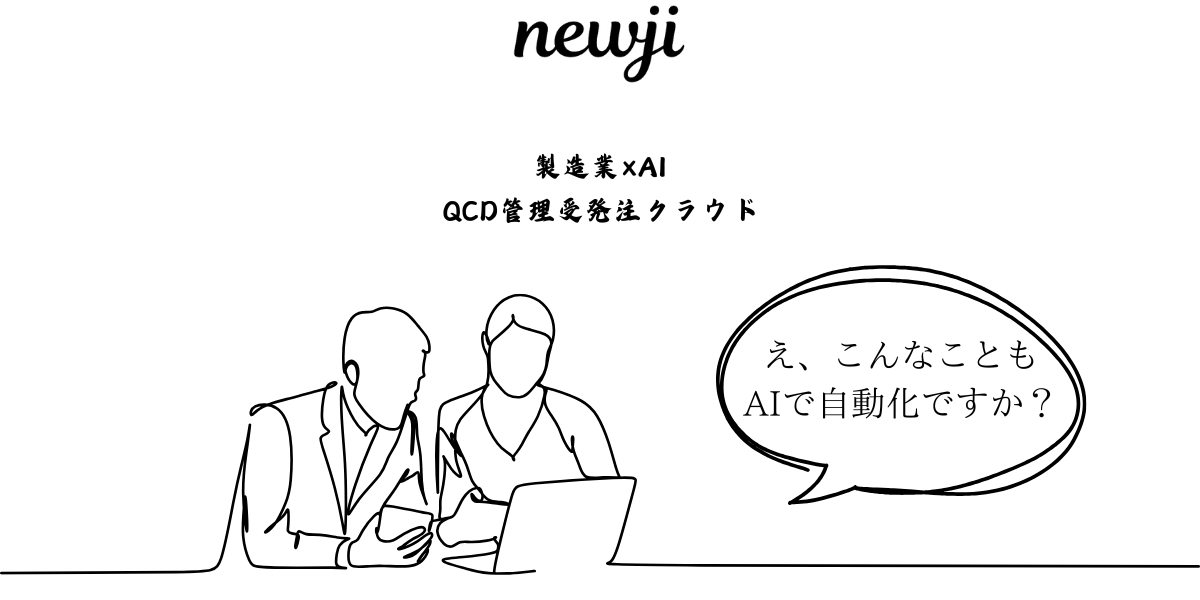
Quality inspection techniques using roundness measuring machines that operators in the precision machinery industry should know
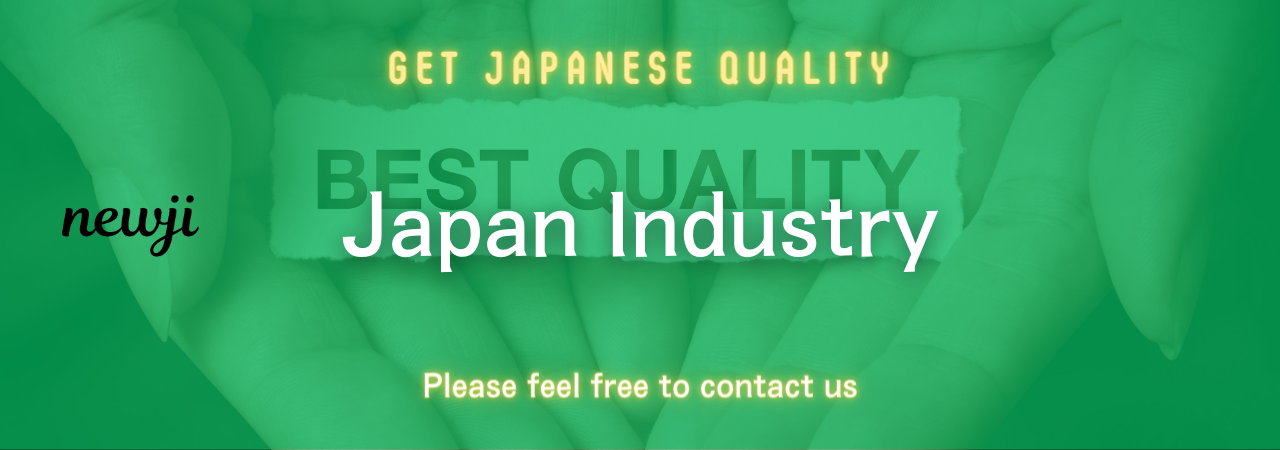
目次
Introduction to Roundness Measuring Machines
In the precision machinery industry, ensuring the quality of components is crucial for maintaining high standards.
Roundness measuring machines are essential tools that help operators verify the geometric accuracy of cylindrical, spherical, or tapered parts.
These machines are designed to measure the deviation of a surface from a perfect circle, which is critical for the functionality and performance of precision components.
With the ever-increasing demand for high-precision manufacturing, understanding how to employ roundness measuring machines effectively can significantly impact the quality assurance process.
The Importance of Roundness in Precision Components
Roundness is a fundamental parameter in the precision machining of components like bearings, gears, and shafts.
Any deviation from the ideal round shape can lead to increased wear, noise, and vibration, subsequently affecting the overall performance of the machinery.
In sectors such as aerospace, automotive, and medical devices, even a minor deviation can pose significant risks.
Therefore, maintaining roundness is not just a matter of quality but also safety and reliability.
Common Applications of Roundness Testing
Roundness measuring machines are used across various industries to inspect a wide range of components.
1. **Bearings**: Ensuring the roundness of bearings is crucial for smooth rotation and minimizing friction.
2. **Gears**: Round gears mesh better and reduce the risk of mechanical failure.
3. **Cylindrical Parts**: These include parts like pistons and shafts, where uniformity is vital.
4. **Medical Equipment**: Precision parts in medical devices require stringent roundness specifications to function correctly.
How Roundness Measuring Machines Work
Roundness measuring machines use a combination of mechanical, electronic, and software components to assess the roundness of an object.
Main Components of Roundness Measuring Machines
1. **Turntable**: The component being measured is placed on a turntable, which rotates the part to ensure a complete profile measurement.
2. **Probe or Stylus**: This sensitive component detects the variations in the surface of the part as it rotates.
3. **Amplifier**: Converts the probe’s physical movements into electrical signals for further analysis.
4. **Data System**: Software processes the signals to calculate roundness deviations and generate precise measurements.
Measuring Techniques
There are several techniques used by roundness measuring machines to assess the quality of components.
– **Two-Point Method**: Involves taking measurements at two opposite points on the component and calculating roundness. It’s a simple method used for basic checks.
– **Multi-Point Method**: Also known as the polar method, it involves taking multiple measurements at different angles to create a data set that represents the component’s roundness more accurately.
– **Least Squares Method**: This statistical technique involves fitting a least squares circle to the data points collected and determining the deviation from this circle.
Calibration and Setup
To ensure accuracy, it is important to periodically calibrate the roundness measuring machine.
Calibration involves setting the reference standards to zero and verifying that the probe, turntable, and data system work correctly.
Operators must also ensure the proper setup of the machine before measurement, including cleanliness, correct alignment of the part, and environmental conditions such as temperature and vibration control.
Ensuring Accurate Measurements
1. **Prepare the Surface**: Ensure the surface of the part is clean and free from oils, dust, or debris that can affect measurement.
2. **Proper Alignment**: Accurate alignment of the part on the turntable is crucial to avoid skewed results.
3. **Stable Environment**: Minimize vibrations and temperature variations that can impact the measuring process.
4. **Regular Calibration**: Implement a schedule for routine calibration to maintain the machine’s accuracy.
Interpreting Results of Roundness Measurement
Interpreting the data from roundness measurements requires understanding several key metrics and terms used in the industry.
Key Metrics
– **Roundness Error**: The deviation from the ideal circle, usually expressed in microns.
– **Form Error**: The overall deviation in shape from the nominal profile.
– **Concentricity and Eccentricity**: Measurements of the center alignment of circular components.
Output Formats
Roundness measuring machines generally provide visual and numerical results.
– **Polar Graphs**: Show deviations in shape, helping identify irregularities.
– **Tabular Data**: Offers precise measurements and values for statistical analysis.
Benefits of Using Roundness Measuring Machines
Employing roundness measuring machines in quality assurance processes offers numerous benefits.
1. **Increased Precision**: Ensures that components meet exact specifications consistently.
2. **Cost Efficiency**: Reduces waste and rework by identifying defects early in the production process.
3. **Improved Product Quality**: Enhances the overall quality and safety of the final product.
4. **Competitive Advantage**: Maintains the company’s reputation for high-quality precision products.
Conclusion
Operators in the precision machinery industry can greatly benefit from understanding and utilizing roundness measuring machines.
These tools play a vital role in ensuring that components adhere to strict standards, improving both functionality and reliability.
By mastering the techniques and principles of roundness measurement, companies can maintain their competitive edge and continue to produce high-quality products in today’s demanding market.
Implementing these quality inspection techniques is a key step towards excellence in precision manufacturing.
資料ダウンロード
QCD管理受発注クラウド「newji」は、受発注部門で必要なQCD管理全てを備えた、現場特化型兼クラウド型の今世紀最高の受発注管理システムとなります。
ユーザー登録
受発注業務の効率化だけでなく、システムを導入することで、コスト削減や製品・資材のステータス可視化のほか、属人化していた受発注情報の共有化による内部不正防止や統制にも役立ちます。
NEWJI DX
製造業に特化したデジタルトランスフォーメーション(DX)の実現を目指す請負開発型のコンサルティングサービスです。AI、iPaaS、および先端の技術を駆使して、製造プロセスの効率化、業務効率化、チームワーク強化、コスト削減、品質向上を実現します。このサービスは、製造業の課題を深く理解し、それに対する最適なデジタルソリューションを提供することで、企業が持続的な成長とイノベーションを達成できるようサポートします。
製造業ニュース解説
製造業、主に購買・調達部門にお勤めの方々に向けた情報を配信しております。
新任の方やベテランの方、管理職を対象とした幅広いコンテンツをご用意しております。
お問い合わせ
コストダウンが利益に直結する術だと理解していても、なかなか前に進めることができない状況。そんな時は、newjiのコストダウン自動化機能で大きく利益貢献しよう!
(β版非公開)