- お役立ち記事
- Quality management and its key points in outsourcing/procurement items
月間76,176名の
製造業ご担当者様が閲覧しています*
*2025年3月31日現在のGoogle Analyticsのデータより
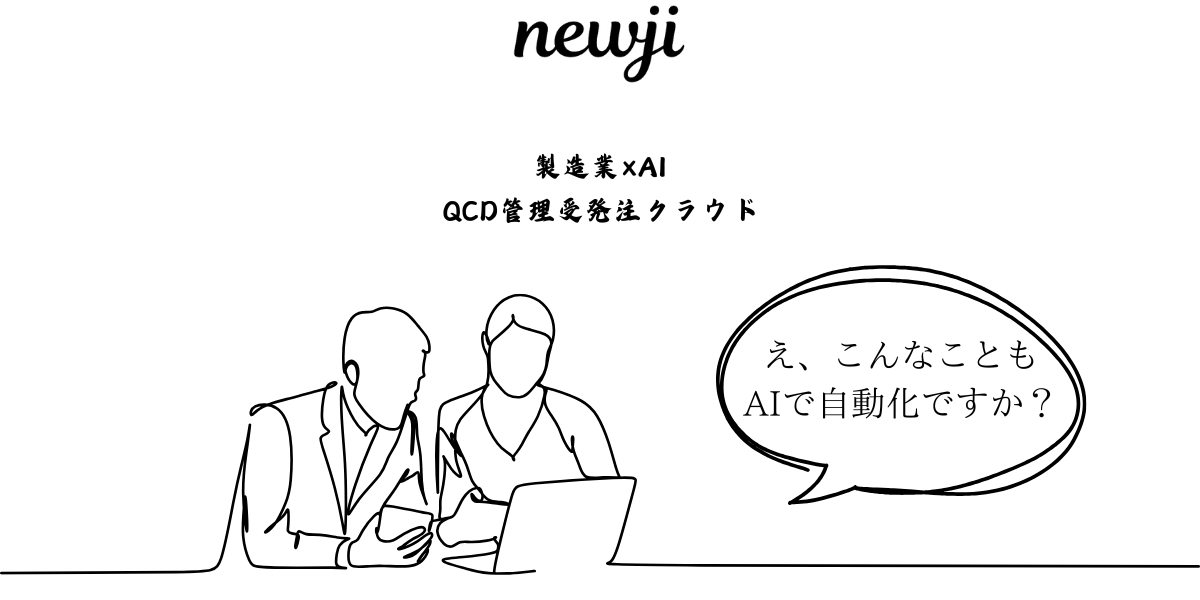
Quality management and its key points in outsourcing/procurement items
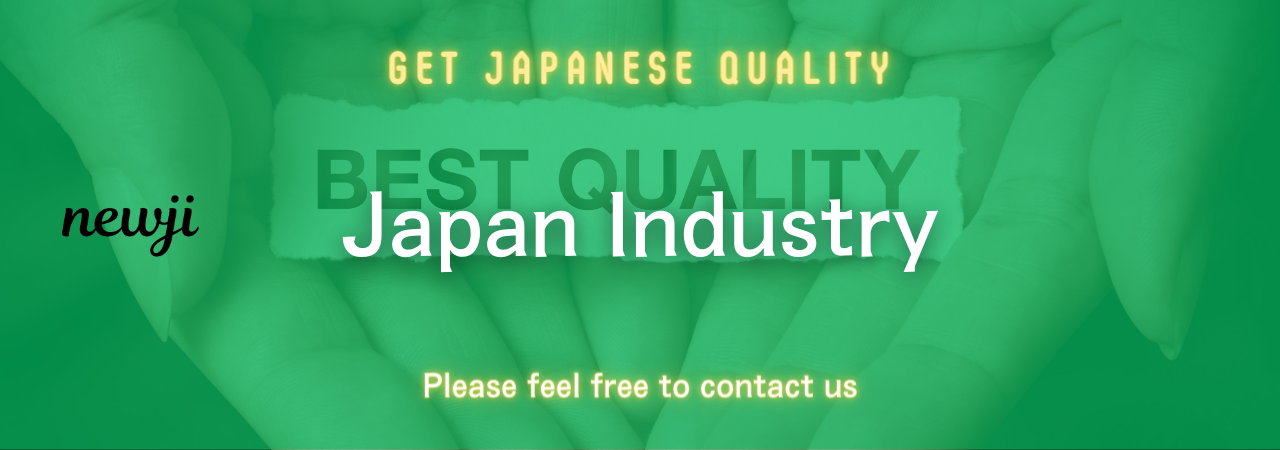
目次
Understanding Quality Management in Outsourcing
Outsourcing has become an integral part of modern business strategies.
Companies turn to outsourcing to save costs, access global talent, and improve operational efficiency.
However, with outsourcing comes the challenge of maintaining quality management.
Quality management ensures that the goods and services procured meet the required standards, ultimately satisfying the end customer.
To effectively manage quality in outsourcing, businesses must adopt a structured approach.
Defining Quality Management
Quality management refers to the processes and procedures that ensure a company’s products or services meet specific standards and customer expectations.
It encompasses various aspects such as quality planning, quality control, quality assurance, and quality improvement.
In the context of outsourcing, quality management becomes essential to bridge the gap between the client’s expectations and the supplier’s deliverables.
Importance of Quality Management in Outsourcing
For businesses that outsource, quality management is not just an option but a necessity.
Effective quality management can lead to increased customer satisfaction, enhanced brand reputation, and long-term partnerships with suppliers.
Without it, companies might face subpar product quality, which can result in customer dissatisfaction and lost sales.
Moreover, poor quality can lead to increased costs due to returns, rework, and warranty claims.
Key Points in Quality Management for Outsourced Items
Setting Clear Expectations
The first step in quality management is setting clear expectations with suppliers.
Businesses should establish comprehensive contracts and detailed service level agreements (SLAs) that outline the quality standards expected for products or services.
These documents should specify the metrics and benchmarks that will be used to evaluate quality.
Clear expectations minimize confusion and form a basis for assessing the supplier’s performance.
Supplier Evaluation and Selection
Not all suppliers are created equal.
Therefore, selecting the right supplier is crucial for maintaining quality.
Companies should conduct thorough evaluations of potential suppliers, assessing their track record, resources, and customer feedback.
It’s important to choose suppliers who have demonstrated their ability to meet quality standards consistently and have the capacity to fulfill your requirements.
Regular Audits and Reviews
Regular audits and reviews are essential to ensure ongoing compliance with quality standards.
These assessments help identify any deviations from agreed-upon quality metrics and allow for proactive adjustments.
Establishing a routine for auditing suppliers’ processes and outputs keeps them accountable and aligned with the company’s quality expectations.
Training and Development
Investing in training and development for both in-house and outsourced teams can significantly impact quality management.
Providing training on specific quality standards, techniques, and tools equips employees with the knowledge and skills needed to maintain high-quality outputs.
Additionally, encouraging a culture of continuous improvement among supplier teams can lead to innovative solutions that further enhance quality.
Challenges in Quality Management for Outsourced Items
Cultural and Language Differences
When dealing with international suppliers, cultural and language differences can pose communication barriers.
These differences can lead to misunderstandings about quality standards and expectations.
To mitigate these challenges, companies should establish clear communication channels and employ bilingual personnel where necessary.
Regular meetings and documentation can also help bridge cultural gaps.
Geographical Distance
Outsourcing often involves geographical distances, making it challenging to monitor and control quality.
Distance can lead to delays in product delivery, increased transportation costs, and difficulties in conducting on-site inspections.
To overcome this, businesses can leverage technology, such as video conferencing and real-time supply chain monitoring tools, to stay connected with suppliers despite geographical barriers.
Maintaining Consistent Standards
In outsourcing, maintaining consistent quality standards across different suppliers can be difficult.
Each supplier may have its unique processes, capabilities, and limitations.
Companies must ensure that their quality management systems are adaptable and flexible, allowing for consistency in quality regardless of the supplier.
Best Practices for Successful Quality Management
Building Strong Partnerships
Fostering strong partnerships with suppliers is a vital component of effective quality management.
Building relationships based on trust and open communication can lead to better collaboration and alignment on quality goals.
When suppliers see themselves as partners rather than mere vendors, they are more likely to invest in achieving shared objectives.
Utilizing Technology
Leveraging technology is crucial for modern quality management.
Automated quality control systems, IoT devices, and data analytics tools can provide real-time insights into supply chain processes.
This technology enables companies to track quality metrics, identify potential issues, and make data-driven decisions efficiently.
Continuous Improvement
Quality management is not a one-time effort but an ongoing process.
Adopting a continuous improvement mindset allows companies to refine their quality management practices continually.
Implementing feedback loops, conducting root cause analyses, and encouraging innovation can lead to sustained improvements in quality over time.
Conclusion
Quality management in outsourcing is a multifaceted endeavor that requires careful planning and execution.
By setting clear expectations, choosing the right suppliers, conducting regular audits, and embracing technology, businesses can effectively manage quality in outsourced items.
Despite the challenges posed by cultural differences and geographical distances, adopting best practices and focusing on continuous improvement can lead to successful quality management.
Prioritizing quality ensures that the company’s products and services meet customer expectations, ultimately contributing to the organization’s success.
資料ダウンロード
QCD管理受発注クラウド「newji」は、受発注部門で必要なQCD管理全てを備えた、現場特化型兼クラウド型の今世紀最高の受発注管理システムとなります。
ユーザー登録
受発注業務の効率化だけでなく、システムを導入することで、コスト削減や製品・資材のステータス可視化のほか、属人化していた受発注情報の共有化による内部不正防止や統制にも役立ちます。
NEWJI DX
製造業に特化したデジタルトランスフォーメーション(DX)の実現を目指す請負開発型のコンサルティングサービスです。AI、iPaaS、および先端の技術を駆使して、製造プロセスの効率化、業務効率化、チームワーク強化、コスト削減、品質向上を実現します。このサービスは、製造業の課題を深く理解し、それに対する最適なデジタルソリューションを提供することで、企業が持続的な成長とイノベーションを達成できるようサポートします。
製造業ニュース解説
製造業、主に購買・調達部門にお勤めの方々に向けた情報を配信しております。
新任の方やベテランの方、管理職を対象とした幅広いコンテンツをご用意しております。
お問い合わせ
コストダウンが利益に直結する術だと理解していても、なかなか前に進めることができない状況。そんな時は、newjiのコストダウン自動化機能で大きく利益貢献しよう!
(β版非公開)