- お役立ち記事
- Quality Management Basics and Effective Design Review Techniques
Quality Management Basics and Effective Design Review Techniques
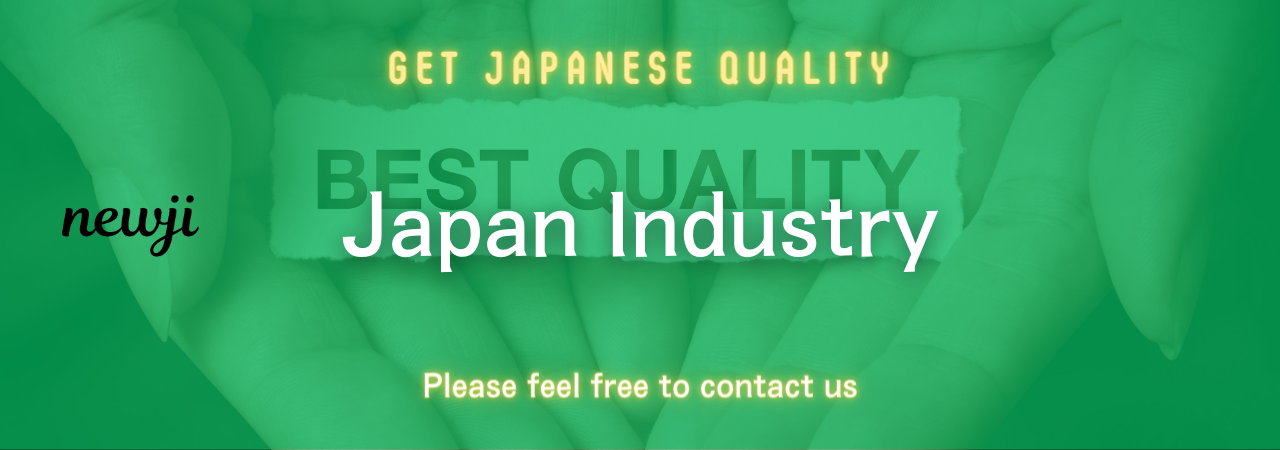
目次
Understanding Quality Management
Quality management is a crucial aspect of any successful business or organization.
It involves the processes and practices focused on ensuring that products or services meet customer expectations.
The core purpose of quality management is to enhance customer satisfaction and improve operational efficiency.
At its heart, quality management is about consistency and reliability.
It ensures that every time a product is made or a service is delivered, it meets a certain standard.
Through systematic oversight, defects and variations are minimized, and resources are used efficiently.
Key Principles of Quality Management
There are several fundamental principles that guide quality management.
These principles are designed to provide a framework for organizations to improve their processes and satisfy customer needs.
One of these principles is customer focus.
It’s essential for companies to understand their customers’ needs and expectations.
By prioritizing customer satisfaction, businesses can build loyalty and trust.
Another principle is leadership.
Strong leadership helps create an environment where people are engaged and aligned toward the organization’s goals.
Leaders motivate and guide their team, setting a clear vision and goals for quality management.
Employee involvement is also crucial.
Empowering employees by involving them in decision-making processes ensures that their knowledge and experience are utilized for the company’s benefit.
In addition, the process approach is a key principle.
By managing activities and resources as processes, organizations ensure more predictable outcomes.
This approach is integral to achieving consistent and desirable results.
Lastly, continuous improvement plays a critical role in quality management.
Organizations need to be proactive about identifying areas for improvement and making incremental changes to enhance their processes.
The Importance of Design Review in Quality Management
Design review is an essential component of quality management.
It is a structured evaluation aimed at ensuring that a product or service design will meet the necessary requirements before it goes into production.
Conducting design reviews helps identify potential issues early, avoiding costly changes later in the process.
Benefits of Effective Design Reviews
Effective design reviews bring several benefits to organizations.
Firstly, they save time and money by catching problems early in the development cycle.
By addressing issues before they escalate, design reviews reduce the need for extensive rework.
Secondly, design reviews improve product quality by ensuring that all aspects of the design meet the required standards.
This includes checking for functionality, safety, compliance, and reliability.
Additionally, design reviews enhance collaboration between different departments.
They provide a platform for cross-functional teams to share their perspectives and expertise, leading to more innovative and robust solutions.
Lastly, design reviews build confidence in stakeholders.
By demonstrating a thorough evaluation process, organizations can assure stakeholders that the product will perform as expected.
Steps for Conducting a Successful Design Review
Conducting a successful design review requires careful planning and execution.
Here are some key steps to follow:
1. **Preparation**: Before the review, gather all relevant design documents, specifications, and test results.
Ensure that all participants have a clear understanding of the design goals and criteria.
2. **Assemble the Right Team**: Include individuals with diverse expertise, such as engineers, designers, quality assurance, and marketing.
A multi-disciplinary team provides a comprehensive review from different perspectives.
3. **Structuring the Review**: Follow a structured agenda that covers all critical aspects of the design.
Clearly define the objectives and expectations for the review session.
4. **Identify and Analyze Issues**: Encourage participants to identify potential design flaws or concerns.
Analyze these issues critically to determine their impact on the final product.
5. **Document Findings**: Keep detailed records of all discussions, decisions, and action items.
This documentation serves as a reference for further design iterations and improvements.
6. **Follow-Up**: After the review, ensure that identified issues are addressed and resolved in a timely manner.
Monitor the progress of these actions to maintain accountability.
Challenges in Design Reviews and How to Overcome Them
While design reviews offer significant advantages, they also present certain challenges.
One common issue is the lack of preparation, which can lead to ineffective reviews.
To overcome this, emphasize the importance of prior preparation so all team members arrive ready.
Another challenge is insufficient participation from cross-functional team members.
Encourage an inclusive environment where everyone feels comfortable sharing their input.
Furthermore, some organizations may encounter resistance to change.
Establish a culture that values continuous improvement and embraces suggestions for better design practices.
Finally, keeping design reviews focused and within time constraints is often difficult.
To address this, set clear boundaries for discussions and prioritize critical issues to keep the review on track.
Conclusion
Quality management and effective design review techniques are essential for delivering high-quality products and services.
By understanding and implementing these principles, organizations can enhance operational efficiency, customer satisfaction, and overall success.
Design reviews, when conducted properly, ensure early detection of issues, fostering collaboration and leading to better outcomes.
Overcoming challenges through preparation, inclusivity, and structured processes strengthens the effectiveness of design reviews.
Adopting robust quality management practices and design review techniques is not just about meeting customer expectations, but it is also a commitment to continual improvement and innovation.
By focusing on quality and thorough evaluation processes, organizations lay the groundwork for sustained growth and success.
資料ダウンロード
QCD調達購買管理クラウド「newji」は、調達購買部門で必要なQCD管理全てを備えた、現場特化型兼クラウド型の今世紀最高の購買管理システムとなります。
ユーザー登録
調達購買業務の効率化だけでなく、システムを導入することで、コスト削減や製品・資材のステータス可視化のほか、属人化していた購買情報の共有化による内部不正防止や統制にも役立ちます。
NEWJI DX
製造業に特化したデジタルトランスフォーメーション(DX)の実現を目指す請負開発型のコンサルティングサービスです。AI、iPaaS、および先端の技術を駆使して、製造プロセスの効率化、業務効率化、チームワーク強化、コスト削減、品質向上を実現します。このサービスは、製造業の課題を深く理解し、それに対する最適なデジタルソリューションを提供することで、企業が持続的な成長とイノベーションを達成できるようサポートします。
オンライン講座
製造業、主に購買・調達部門にお勤めの方々に向けた情報を配信しております。
新任の方やベテランの方、管理職を対象とした幅広いコンテンツをご用意しております。
お問い合わせ
コストダウンが利益に直結する術だと理解していても、なかなか前に進めることができない状況。そんな時は、newjiのコストダウン自動化機能で大きく利益貢献しよう!
(Β版非公開)