- お役立ち記事
- Quality risk management in multinational procurement Measures that purchasing departments should take
Quality risk management in multinational procurement Measures that purchasing departments should take
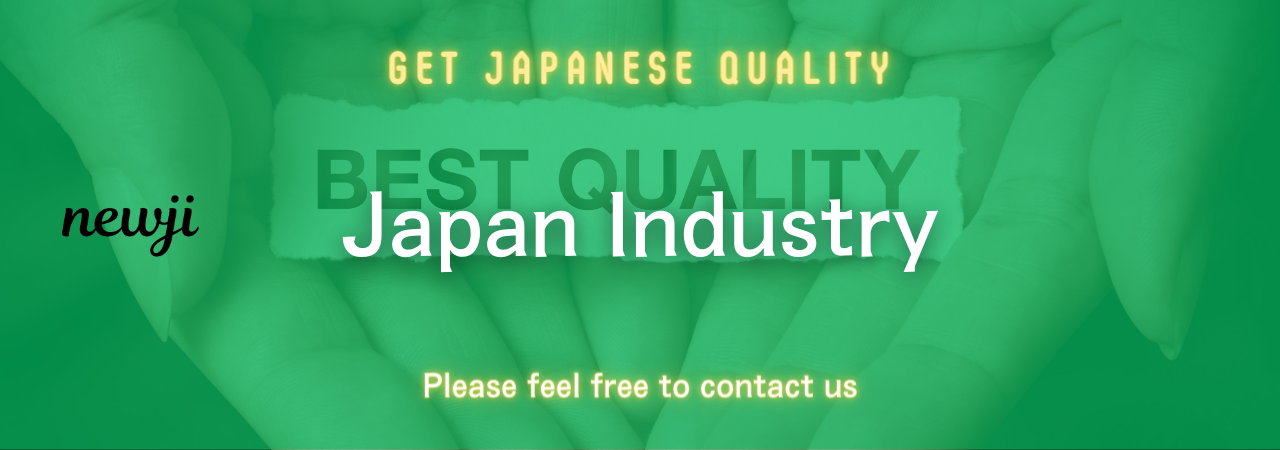
Understanding Quality Risk Management in Procurement
Quality risk management plays a crucial role in the procurement process, especially in multinational corporations where the stakes and complexities are high.
By effectively managing risks associated with quality, companies can safeguard their supply chain integrity, ensure compliance with regulatory standards, and enhance their brand reputation.
For purchasing departments, adopting robust quality risk management strategies is paramount to maintaining a competitive edge and ensuring the seamless delivery of goods and services.
The Importance of Quality Risk Management
In multinational procurement, the diversity of suppliers and the geographical spread of operations present unique challenges.
Quality risk management helps to identify, assess, and mitigate risks that can impact product quality and, consequently, customer satisfaction.
When quality risks are overlooked, it might result in product recalls, loss of customers, increased costs, and damage to the company’s reputation.
Thus, integrating quality risk management within the procurement process helps mitigate these risks and ensures a consistent supply of high-quality products.
Identifying Key Quality Risks
The first step in quality risk management is to identify potential risks that might affect the business.
These risks can include substandard materials, delayed deliveries, non-compliance with international standards, and communication barriers due to cultural and language differences.
Other risks might involve sudden changes in regulatory requirements across different countries, affecting product specifications and supplier capabilities.
By identifying these risks early, purchasing departments can take proactive steps to manage them effectively.
Assessing and Evaluating Risks
Once identified, the next step involves assessing these risks to understand their potential impact on the procurement process.
The risk assessment process involves evaluating the likelihood of a risk occurring and the severity of its impact.
This step is vital because it helps prioritize the risks that require immediate attention versus those that can be managed over time.
For instance, risks that could disrupt supply chains or lead to major compliance issues should take precedence over others.
Effective risk assessment provides a clear picture of the potential challenges and aids in crafting strategic solutions.
Strategies for Managing Quality Risks
To manage quality risks effectively, purchasing departments should implement a combination of strategies tailored to their specific needs.
One key strategy is supplier qualification and audit. It’s essential to vet potential suppliers thoroughly and perform regular audits to ensure they meet quality standards.
Collaborating with suppliers to establish clear quality benchmarks and expectations is also crucial.
Another strategy is to develop contingency plans that outline actions to be taken in case of quality failures or supply chain disruptions.
Moreover, leveraging technology like data analytics and blockchain can provide real-time insights into the supply chain, improving transparency and traceability.
This technological integration helps in detecting quality issues early, thus allowing timely corrective actions.
Training and Development
A well-trained procurement team is essential for effective quality risk management.
Investing in training programs ensures that team members are updated on the latest industry standards, tools, and techniques related to quality risk management.
Such training enables them to identify risks quickly, assess situations accurately, and implement solutions efficiently.
Additionally, fostering a culture of continuous improvement and awareness within the procurement department emphasizes the importance of quality in every transaction and interaction.
Collaboration with Cross-functional Teams
Quality risk management is most effective when purchasing departments collaborate with other departments within the organization.
Working closely with teams like operations, logistics, and compliance allows the sharing of critical risk information and fosters a holistic approach to quality management.
Regular cross-departmental meetings and updates ensure that everyone is on the same page regarding quality objectives and risk mitigation strategies.
Such collaboration also helps in aligning procurement goals with organizational objectives, leading to better overall performance.
Continuous Monitoring and Improvement
In multinational procurement, the risk landscape is constantly evolving, necessitating continuous monitoring and adaptation of risk management strategies.
Implementing a system for regular risk reviews helps in staying ahead of potential quality issues.
Such reviews should analyze past performance, investigate any deviations, and adjust strategies accordingly.
Encouraging feedback from both suppliers and internal teams is also crucial for identifying improvement areas.
By fostering a culture of learning and agility, companies can enhance their quality risk management processes, leading to more resilient procurement operations.
Conclusion
Quality risk management is essential to the procurement process, especially within multinational corporations.
By identifying, assessing, and strategically managing potential risks, purchasing departments can ensure the continuous delivery of high-quality products and services.
Investing in training, collaboration, technology, and continuous improvement efforts allows organizations to stay competitive in a rapidly changing global market.
Ultimately, robust quality risk management not only protects an organization’s brand and reputation but also contributes positively to its bottom line, ensuring long-term success.
資料ダウンロード
QCD調達購買管理クラウド「newji」は、調達購買部門で必要なQCD管理全てを備えた、現場特化型兼クラウド型の今世紀最高の購買管理システムとなります。
ユーザー登録
調達購買業務の効率化だけでなく、システムを導入することで、コスト削減や製品・資材のステータス可視化のほか、属人化していた購買情報の共有化による内部不正防止や統制にも役立ちます。
NEWJI DX
製造業に特化したデジタルトランスフォーメーション(DX)の実現を目指す請負開発型のコンサルティングサービスです。AI、iPaaS、および先端の技術を駆使して、製造プロセスの効率化、業務効率化、チームワーク強化、コスト削減、品質向上を実現します。このサービスは、製造業の課題を深く理解し、それに対する最適なデジタルソリューションを提供することで、企業が持続的な成長とイノベーションを達成できるようサポートします。
オンライン講座
製造業、主に購買・調達部門にお勤めの方々に向けた情報を配信しております。
新任の方やベテランの方、管理職を対象とした幅広いコンテンツをご用意しております。
お問い合わせ
コストダウンが利益に直結する術だと理解していても、なかなか前に進めることができない状況。そんな時は、newjiのコストダウン自動化機能で大きく利益貢献しよう!
(Β版非公開)