- お役立ち記事
- Quality Standards and Selection Criteria for Blanking Processing Required by Major Companies
Quality Standards and Selection Criteria for Blanking Processing Required by Major Companies
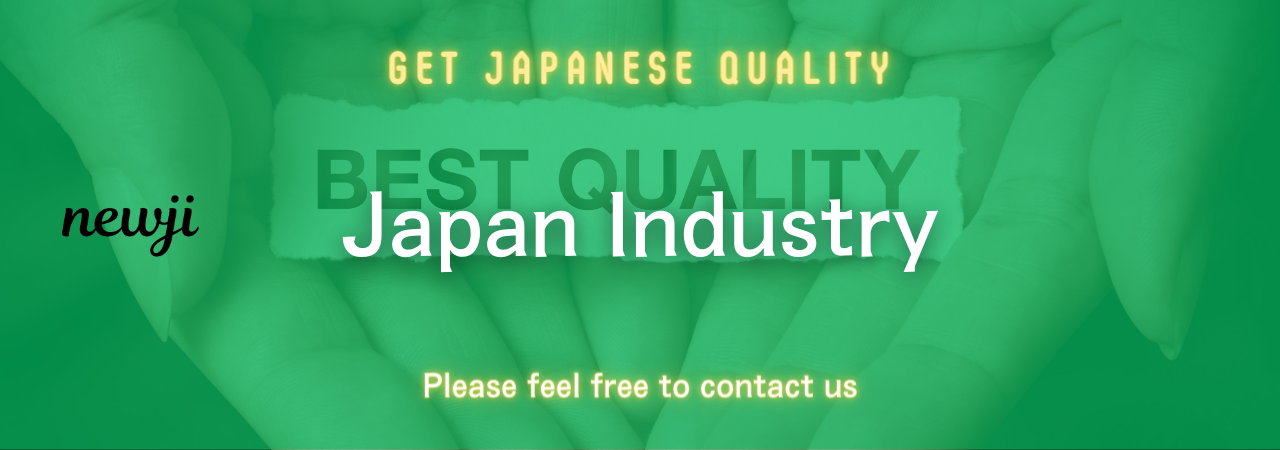
目次
Understanding Blanking Processing
Blanking processing is a critical manufacturing practice. It involves cutting a flat material, often metal, into specific shapes or components.
This technique is widely used in various industries, including automotive, aerospace, electronics, and construction.
Proper blanking processing ensures precision, efficiency, and reduced material waste.
The Importance of Quality Standards in Blanking Processing
When major companies seek blanking services, they set stringent quality standards.
These protocols ensure that the components produced meet specific dimensions, tolerances, and material integrity.
Adhering to these standards reduces the risk of defective parts, which can lead to costly recalls or product failures.
It also ensures consistency, which is vital for large-scale production.
Dimensional Accuracy and Tolerances
Dimensional accuracy is paramount in blanking processing.
Tolerances refer to the permissible variations in the part’s dimensions.
Major companies often demand tight tolerances to ensure that parts fit perfectly within assembly processes.
A deviation can lead to problems in the final product, causing misalignments and operational inefficiencies.
Material Integrity
The integrity of the material being blanked is equally important.
The material should maintain its properties without any compromises, such as cracks or deformities.
This is critical, especially for industries like aerospace and automotive, where the structural integrity of each part is paramount.
Using high-quality materials also prevents potential failures due to material fatigue or stress.
Surface Finish
The surface finish of the blanked parts is another quality standard emphasized by major companies.
A smooth and defect-free surface is necessary for both functional and aesthetic reasons.
Rough or irregular surfaces can lead to increased friction, wear, and tear in mechanical applications.
Moreover, surfaces free from scratches, burrs, or contaminants are often essential for subsequent processing stages, such as painting or coating.
Selection Criteria for Blanking Processing
Major companies follow specific criteria when selecting blanking processing services.
These criteria ensure that the service provider can meet their quality standards and production needs.
Technological Capability
The technological capability of a service provider is a primary selection criterion.
Advanced machinery and equipment are essential for high-precision blanking.
Companies typically look for providers with state-of-the-art tools, such as CNC machines and laser cutting technology.
These machines offer superior accuracy, speed, and versatility, necessary for producing complex shapes and maintaining tight tolerances.
Industry Experience and Expertise
Experience and expertise in blanking processing are crucial.
Service providers with a proven track record are more likely to deliver consistent quality.
They have insights into potential challenges and the best methods to address them.
This experience includes familiarity with different materials, techniques, and industry-specific requirements.
Quality Control Measures
Robust quality control measures are indispensable.
Major companies prefer providers who follow strict quality control protocols.
This includes regular inspections, testing, and use of quality management systems like ISO 9001.
Effective quality control ensures that all parts produced meet the required standards without exceptions.
Capacity and Scalability
Capacity and scalability are other vital factors.
The provider must be capable of handling both small and large production runs.
Scalability is essential to accommodate potential increases in demand.
Reliable providers can adjust their production capacity to meet the client’s needs without compromising on quality or delivery timelines.
Cost-Effectiveness
Cost-effectiveness is always a key consideration.
While companies focus on quality, they also seek competitive pricing.
A balance between cost and quality ensures that the blanking processing services are efficient and economical.
The Role of Communication and Collaboration
Successful partnerships in blanking processing are built on clear communication and collaboration.
Major companies value providers who maintain transparent and open communication channels.
This ensures that any issues are promptly addressed and resolved.
Regular Updates and Feedback
Regular updates on project progress and proactive feedback are critical.
It keeps both parties aligned with the production schedule and quality expectations.
Immediate feedback on any deviations allows quick corrective actions, minimizing any potential impact on the project timeline.
Collaborative Problem-Solving
Collaborative problem-solving fosters innovation and continuous improvement.
Service providers should work alongside their clients to develop efficient solutions for any challenges.
This collaborative approach often leads to innovations in the blanking process, improving overall efficiency and quality.
Future Trends in Blanking Processing
The blanking processing industry is continuously evolving, driven by technological advancements and industry demands.
Staying abreast of these trends is essential for both service providers and their clients.
Automation and Industry 4.0
Automation and the integration of Industry 4.0 technologies are at the forefront.
Automated systems and robotics enhance precision, speed, and repeatability.
Industry 4.0 technologies, such as IoT and big data analytics, enable real-time monitoring and optimization of the blanking process.
This leads to increased efficiency, reduced downtime, and better quality control.
Advanced Materials
The development of advanced materials is another trend.
Materials with superior properties, such as higher strength-to-weight ratios, are becoming more prevalent.
These materials often require specialized blanking techniques to maintain their integrity and achieve the desired quality.
Staying updated with these materials ensures that service providers can meet the evolving needs of their clients.
Sustainability and Eco-Friendly Practices
Sustainability and eco-friendly practices are gaining importance.
Companies are focusing on minimizing waste and reducing their environmental footprint.
Effective blanking processing techniques that optimize material usage and employ recycling strategies are becoming essential.
Ensuring quality standards and understanding selection criteria in blanking processing is crucial for meeting the expectations of major companies.
Adopting the latest technologies, following robust quality control practices, and fostering collaboration can lead to successful partnerships and high-quality outcomes.
By staying updated with industry trends, service providers can continue to deliver exceptional value and contribute to their client’s success.
資料ダウンロード
QCD調達購買管理クラウド「newji」は、調達購買部門で必要なQCD管理全てを備えた、現場特化型兼クラウド型の今世紀最高の購買管理システムとなります。
ユーザー登録
調達購買業務の効率化だけでなく、システムを導入することで、コスト削減や製品・資材のステータス可視化のほか、属人化していた購買情報の共有化による内部不正防止や統制にも役立ちます。
NEWJI DX
製造業に特化したデジタルトランスフォーメーション(DX)の実現を目指す請負開発型のコンサルティングサービスです。AI、iPaaS、および先端の技術を駆使して、製造プロセスの効率化、業務効率化、チームワーク強化、コスト削減、品質向上を実現します。このサービスは、製造業の課題を深く理解し、それに対する最適なデジタルソリューションを提供することで、企業が持続的な成長とイノベーションを達成できるようサポートします。
オンライン講座
製造業、主に購買・調達部門にお勤めの方々に向けた情報を配信しております。
新任の方やベテランの方、管理職を対象とした幅広いコンテンツをご用意しております。
お問い合わせ
コストダウンが利益に直結する術だと理解していても、なかなか前に進めることができない状況。そんな時は、newjiのコストダウン自動化機能で大きく利益貢献しよう!
(Β版非公開)