- お役立ち記事
- Quenching process and quality control in manufacturing
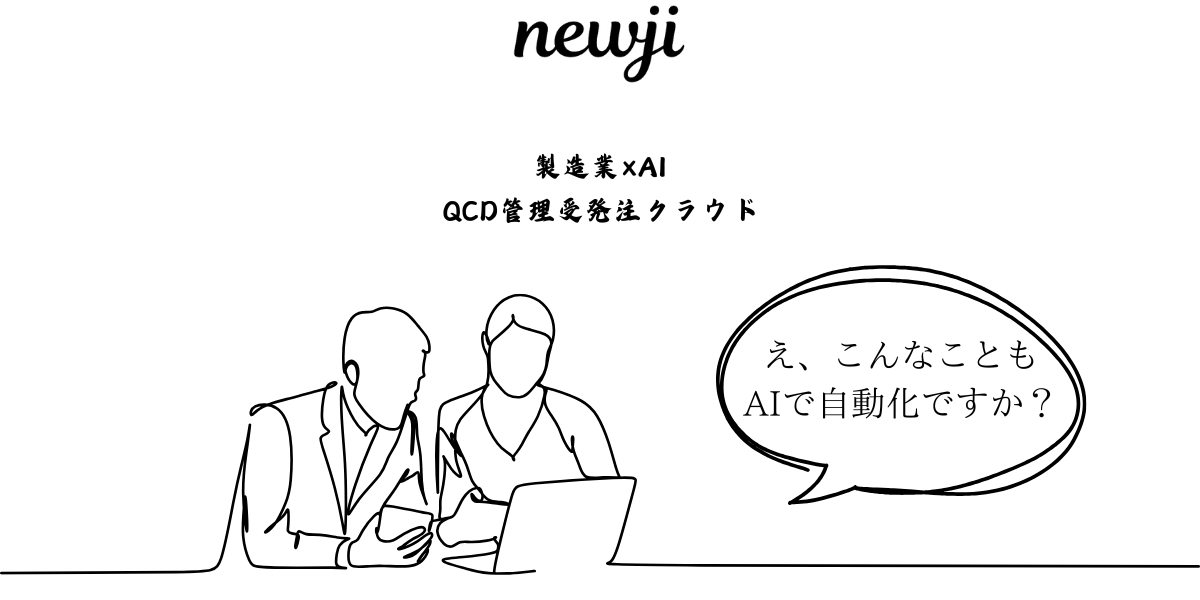
Quenching process and quality control in manufacturing
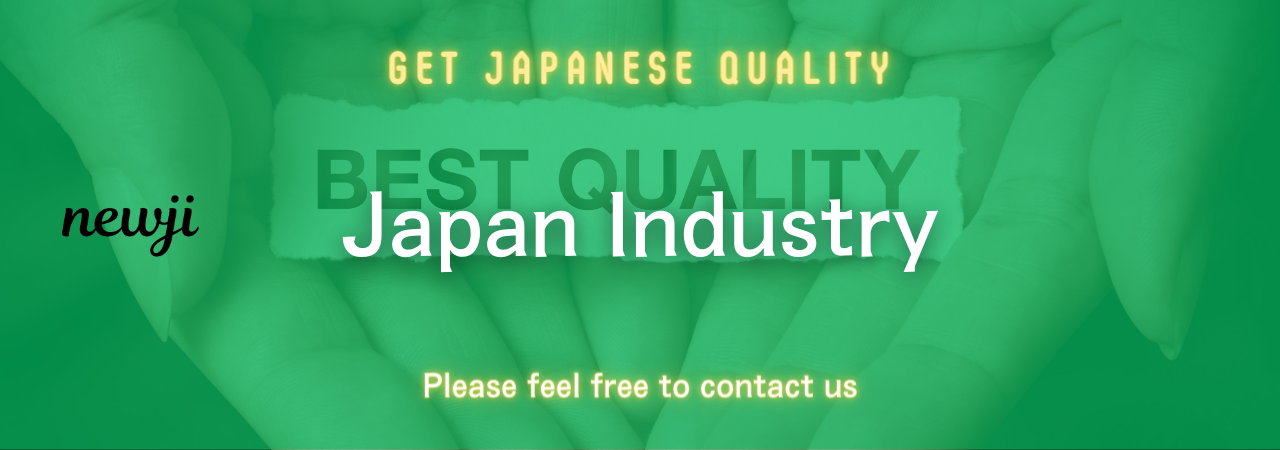
In manufacturing, a vital step known as the quenching process plays a significant role in determining the quality and performance of metal products.
Understanding this process can help us appreciate how everyday items like tools, automotive parts, and machinery are made more durable and reliable.
Let’s dive into the quenching process and the importance of quality control within this context.
目次
What is Quenching?
The quenching process is a heat treatment technique used to enhance the hardness and strength of metals.
After metal is heated to a high temperature, it is rapidly cooled using a specific medium.
Common cooling mediums include water, oil, and air.
This rapid cooling changes the metal’s microstructure, leading to improved mechanical properties.
The Basics of Heat Treatment
Heat treatment generally involves three key steps: heating, soaking, and cooling.
The heating phase brings the metal to a specific temperature.
During soaking, the metal is held at this high temperature for a period of time to allow the heat to penetrate uniformly.
Finally, the cooling or quenching phase rapidly reduces the metal’s temperature.
Why is Quenching Important?
Quenching is crucial for several reasons.
First, it transforms the microstructure, making the metal harder and stronger.
Second, it helps in achieving specific mechanical properties needed for different applications.
For example, automotive components must endure high stress and wear, requiring the toughness provided by quenching.
Industry Applications of Quenching
Quenching is used across various industries, including automotive, aerospace, and construction.
In the automotive industry, gears, axles, and engine parts undergo quenching to achieve the necessary strength and durability.
In aerospace, components like landing gears and turbine blades are quenched to handle extreme conditions and stresses.
In construction, steel beams and bolts are treated to ensure they can support heavy loads.
Types of Quenching Mediums
The choice of quenching medium significantly affects the outcome of the process.
Different mediums provide varying cooling rates and result in different material properties.
Water Quenching
Water is a common medium due to its rapid cooling properties.
It is suitable for metals that require high hardness.
However, the aggressive nature of water can sometimes lead to cracks and warping if not carefully controlled.
Oil Quenching
Oil offers a more moderate cooling rate compared to water.
It reduces the risk of cracks and deformation, making it ideal for alloy steels and complex shapes.
Air Quenching
Air quenching involves cooling the metal in an air environment.
This method provides the slowest cooling rate and is used for metals that do not require high hardness.
Air quenching minimizes the risk of distortion, making it suitable for complex and large components.
Quality Control in Quenching
Quality control is absolutely essential in the quenching process.
Ensuring each item meets specific standards prevents failures and extends the life of the product.
Temperature Control
Maintaining a consistent temperature throughout the heating and soaking phases is critical.
Variations can result in uneven hardness and compromised performance.
Advanced temperature monitoring systems help maintain the desired range, reducing the margin for error.
Monitoring Cooling Rates
Each metal requires a specific cooling rate to achieve the desired properties.
Too fast or too slow cooling can lead to defects.
By carefully selecting and controlling the quenching medium, manufacturers can achieve the right balance.
Testing and Inspection
Post-quenching, extensive testing and inspection are conducted to verify the quality of the treated metal.
Non-destructive testing methods such as ultrasonic testing, x-rays, and magnetic particle testing help detect internal and surface defects without damaging the item.
Mechanical tests like hardness testing and tensile strength measurements provide additional data on the item’s performance characteristics.
Challenges in Quenching
Despite its benefits, the quenching process poses several challenges.
Understanding these challenges helps in implementing effective solutions and achieving better outcomes.
Thermal Distortion
Rapid cooling can cause thermal distortion, leading to changes in shape and dimensions.
This issue is particularly significant in parts with complex geometries.
Using a slower cooling medium or modifying the quenching process can help mitigate this problem.
Cracking Risk
The risk of cracking is a major concern during quenching.
Cracks can form due to uneven cooling rates, internal stresses, or material properties.
Selecting the appropriate quenching medium and employing controlled cooling methods can reduce this risk.
Environmental and Safety Concerns
Quenching mediums, especially oils and some chemicals, pose environmental and safety hazards.
Employing environmentally friendly quenching techniques and ensuring proper handling and disposal of quenching fluids can address these issues.
Innovations and Future Trends
Advancements in technology continue to improve the quenching process.
Innovations focus on reducing environmental impact, enhancing efficiency, and achieving superior material properties.
Induction Quenching
Induction quenching uses electromagnetic fields to heat specific areas of a metal item before cooling it.
This method allows precise control over the heating and cooling zones, reducing distortion and achieving desired properties more effectively.
Eco-friendly Quenching Fluids
Research into eco-friendly quenching fluids aims to replace traditional oils and chemicals with biodegradable and less hazardous alternatives.
Such innovations help reduce environmental impact and improve workplace safety.
Computer Simulations
Advanced computer simulations enable manufacturers to predict and optimize the outcomes of the quenching process.
By modeling different scenarios and cooling rates, they can fine-tune the process parameters to achieve the best results with minimal trial and error.
Conclusion
The quenching process is a fundamental step in manufacturing that enhances the quality and durability of metal products.
Through careful control of the heating, soaking, and cooling phases, manufacturers can achieve specific mechanical properties required for various applications.
Quality control measures, advanced technologies, and continuous innovation ensure the reliability and safety of quenched products.
Understanding the intricacies of quenching and its role in quality control provides valuable insight into modern manufacturing’s essential practices.
資料ダウンロード
QCD調達購買管理クラウド「newji」は、調達購買部門で必要なQCD管理全てを備えた、現場特化型兼クラウド型の今世紀最高の購買管理システムとなります。
ユーザー登録
調達購買業務の効率化だけでなく、システムを導入することで、コスト削減や製品・資材のステータス可視化のほか、属人化していた購買情報の共有化による内部不正防止や統制にも役立ちます。
NEWJI DX
製造業に特化したデジタルトランスフォーメーション(DX)の実現を目指す請負開発型のコンサルティングサービスです。AI、iPaaS、および先端の技術を駆使して、製造プロセスの効率化、業務効率化、チームワーク強化、コスト削減、品質向上を実現します。このサービスは、製造業の課題を深く理解し、それに対する最適なデジタルソリューションを提供することで、企業が持続的な成長とイノベーションを達成できるようサポートします。
オンライン講座
製造業、主に購買・調達部門にお勤めの方々に向けた情報を配信しております。
新任の方やベテランの方、管理職を対象とした幅広いコンテンツをご用意しております。
お問い合わせ
コストダウンが利益に直結する術だと理解していても、なかなか前に進めることができない状況。そんな時は、newjiのコストダウン自動化機能で大きく利益貢献しよう!
(Β版非公開)