- お役立ち記事
- Rapid Reform! Achieving a 30% Productivity Increase in High-Mix, Low-Volume Factories
月間76,176名の
製造業ご担当者様が閲覧しています*
*2025年3月31日現在のGoogle Analyticsのデータより
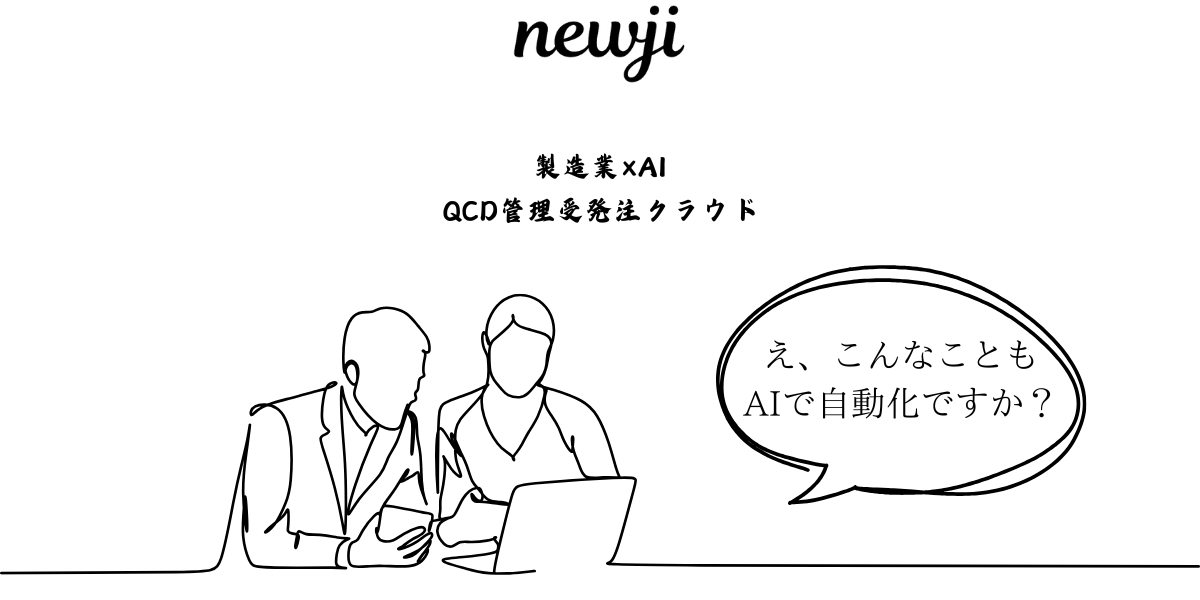
Rapid Reform! Achieving a 30% Productivity Increase in High-Mix, Low-Volume Factories
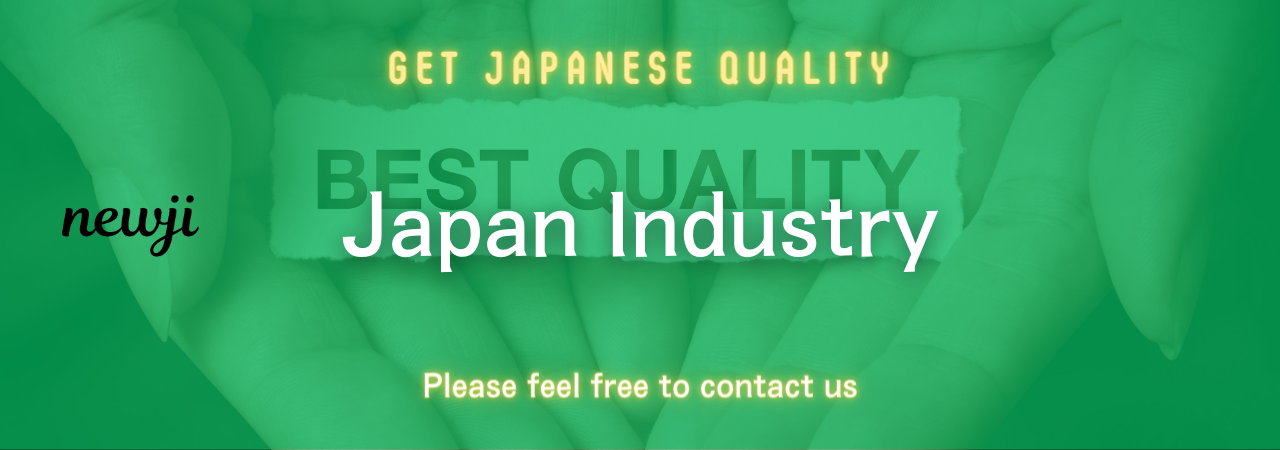
In today’s fast-paced manufacturing world, the demand for customization and flexibility is ever-increasing.
High-mix, low-volume factories face unique challenges compared to their mass-production counterparts.
To stay competitive and boost productivity, these factories need to adopt innovative strategies and technologies.
This article will outline several practical steps to achieve a 30% increase in productivity in high-mix, low-volume factories.
目次
Understanding High-Mix, Low-Volume Manufacturing
High-mix, low-volume manufacturing involves producing a variety of products in smaller quantities.
This approach contrasts with traditional mass production, which focuses on large quantities of a few products.
High-mix, low-volume manufacturing allows factories to cater to different customer requirements, offering greater flexibility and customization.
However, it also introduces complexities that demand efficient management and streamlined processes.
Implementing Lean Manufacturing Principles
Value Stream Mapping
Value stream mapping involves visualizing the steps involved in producing a product from start to finish.
By identifying value-added and non-value-added activities, factories can pinpoint areas for improvement.
Streamlining these processes eliminates waste, reduces lead times, and enhances overall efficiency.
5S Methodology
The 5S methodology—Sort, Set in Order, Shine, Standardize, and Sustain—significantly contributes to higher productivity.
Sorting removes unnecessary items from the workspace.
Setting in order organizes tools and materials systematically.
Shining ensures cleanliness, which fosters a safe working environment.
Standardizing establishes consistent practices, while sustaining focuses on continuous improvement.
Adopting Flexible Manufacturing Systems
Flexible manufacturing systems (FMS) allow for quick adjustments to changes in product type and volume.
Such systems utilize advanced machinery and automation, enabling factories to efficiently manage varied production requirements.
Investing in FMS may involve upfront costs, but the long-term benefits include reduced changeover times and enhanced adaptability.
Modular Equipment
Modular equipment offers significant flexibility.
Machines designed with interchangeable components can be quickly reconfigured to manufacture different products.
This adaptability reduces downtime typically associated with changeovers, thereby increasing productivity.
Automated Guided Vehicles (AGVs)
AGVs are robots that transport materials within the factory environment.
These vehicles minimize manual handling, reducing the risk of human error and improving material flow.
By optimizing logistics, AGVs ensure that production lines remain stocked and operational, further boosting productivity.
Enhanced Training and Skill Development
A well-trained workforce is crucial for optimizing productivity in high-mix, low-volume factories.
Regular training sessions ensure employees are proficient in using the latest technologies and methodologies.
Additionally, fostering a culture of continuous learning encourages workers to develop new skills and adapt to evolving production demands.
Cross-Training Employees
Cross-training involves educating employees to handle multiple roles within the factory.
This approach provides flexibility in workforce allocation, allowing staff to cover for absentees and adjust to dynamic production needs.
Moreover, cross-trained employees contribute to a more resilient and adaptable team.
Empowering Employees
Empowering employees involves entrusting them with responsibilities and decision-making capabilities.
When workers feel valued and involved, they are more likely to take ownership of their tasks and strive for excellence.
This sense of accountability enhances overall productivity and job satisfaction.
Leveraging Advanced Technologies
Internet of Things (IoT)
IoT technology connects devices and sensors across the factory floor, enabling real-time data collection and analysis.
By monitoring equipment performance, production status, and environmental conditions, factories can make informed decisions to optimize operations.
IoT enhances predictive maintenance, reducing downtime and preventing costly breakdowns.
Artificial Intelligence (AI) and Machine Learning
AI and machine learning algorithms analyze large datasets to identify patterns and insights.
In high-mix, low-volume factories, these technologies aid in predicting demand, optimizing inventory management, and fine-tuning production schedules.
AI-driven analytics empower factories to make data-driven decisions, enhancing efficiency and productivity.
Additive Manufacturing
Additive manufacturing, or 3D printing, allows for the rapid production of prototypes and customized components.
For high-mix, low-volume factories, this technology significantly reduces lead times and prototyping costs.
Integrating 3D printing into the manufacturing process enables quick iterations and modifications, ensuring products meet customer specifications.
Streamlining Supply Chain Management
An efficient supply chain is vital for maintaining high productivity levels.
Factories must establish strong relationships with suppliers to ensure timely delivery of raw materials and components.
Implementing just-in-time (JIT) inventory management minimizes excess stock, reducing storage costs and waste.
Vendor Collaboration
Collaborating closely with vendors fosters better communication and coordination.
By sharing production schedules and forecasts, factories can align their supply chain activities with demand fluctuations.
This approach ensures a steady flow of materials, preventing production delays and stockouts.
Supply Chain Visibility
Visibility throughout the supply chain enables factories to monitor the status of orders and shipments.
Advanced tracking technologies provide real-time updates, allowing for proactive problem-solving.
Enhanced visibility minimizes the impact of disruptions and keeps production on schedule.
Optimizing Workflow and Layout
The physical layout of a factory significantly impacts productivity.
Efficient workspace design minimizes material handling and movement, reducing production time.
Cellular Manufacturing
Cellular manufacturing groups machines and workstations into cells that handle specific product families.
This arrangement minimizes travel distances, enhances communication, and improves process flow.
By reducing setup times and facilitating parallel processing, cellular manufacturing boosts overall productivity.
Kaizen Events
Kaizen events are focused improvement initiatives aimed at resolving specific issues within the factory.
These short-term projects involve cross-functional teams working together to identify problems and implement solutions.
Kaizen events promote continuous improvement, fostering a culture of innovation and efficiency.
By implementing these strategies, high-mix, low-volume factories can achieve significant productivity gains.
Embracing lean manufacturing principles, investing in flexible systems, leveraging advanced technologies, and enhancing worker skills all contribute to a more efficient operation.
Streamlining supply chain management and optimizing workflow further solidify these improvements.
With a commitment to continuous improvement, high-mix, low-volume factories can thrive in an increasingly demanding market.
資料ダウンロード
QCD管理受発注クラウド「newji」は、受発注部門で必要なQCD管理全てを備えた、現場特化型兼クラウド型の今世紀最高の受発注管理システムとなります。
ユーザー登録
受発注業務の効率化だけでなく、システムを導入することで、コスト削減や製品・資材のステータス可視化のほか、属人化していた受発注情報の共有化による内部不正防止や統制にも役立ちます。
NEWJI DX
製造業に特化したデジタルトランスフォーメーション(DX)の実現を目指す請負開発型のコンサルティングサービスです。AI、iPaaS、および先端の技術を駆使して、製造プロセスの効率化、業務効率化、チームワーク強化、コスト削減、品質向上を実現します。このサービスは、製造業の課題を深く理解し、それに対する最適なデジタルソリューションを提供することで、企業が持続的な成長とイノベーションを達成できるようサポートします。
製造業ニュース解説
製造業、主に購買・調達部門にお勤めの方々に向けた情報を配信しております。
新任の方やベテランの方、管理職を対象とした幅広いコンテンツをご用意しております。
お問い合わせ
コストダウンが利益に直結する術だと理解していても、なかなか前に進めることができない状況。そんな時は、newjiのコストダウン自動化機能で大きく利益貢献しよう!
(β版非公開)