- お役立ち記事
- Rapid Response and Process for Drafting Recurrence Prevention Plans in the Event of Quality Issues in Manufacturing
Rapid Response and Process for Drafting Recurrence Prevention Plans in the Event of Quality Issues in Manufacturing
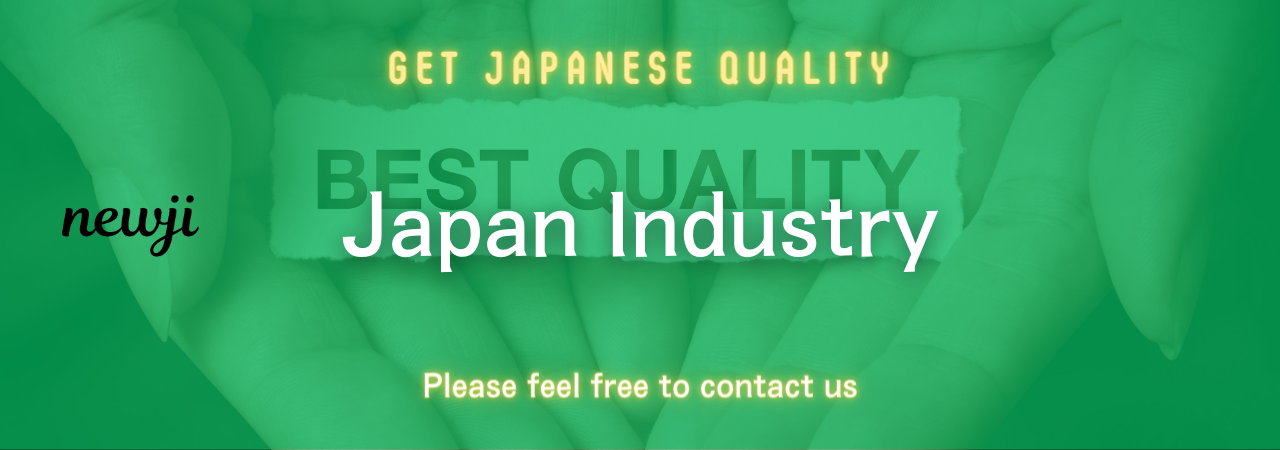
目次
Understanding Quality Issues in Manufacturing
Manufacturing is a complex process that involves multiple stages and various stakeholders.
From raw material sourcing to final product delivery, each step has its potential pitfalls.
Quality issues can arise due to factors like human error, machine malfunction, supply chain inconsistencies, or inadequate testing procedures.
When these issues go unresolved, they can lead to defective products, dissatisfied customers, and financial losses.
Rapid Response to Quality Issues
One of the most critical aspects of managing quality issues is having a rapid response system in place.
Speedy identification and immediate action can significantly reduce the impact of the problem.
Here’s how to ensure a rapid response:
Identify the Issue
The first step is to identify that there is a quality issue.
This can be done through various means such as customer complaints, routine inspections, or automated detection systems.
Early detection is vital for containing the problem promptly.
Form a Response Team
Once a quality issue is identified, it’s essential to form a response team quickly.
This team should include experts from various departments such as quality assurance, engineering, production, and supply chain management.
The team should be equipped to analyze the issue, decide on immediate actions, and communicate effectively.
Assess the Severity
Determining the severity of the issue is crucial for prioritizing actions.
Minor defects may require simple corrections, while severe issues might necessitate halting the production line and issuing product recalls.
Assessing severity helps allocate resources efficiently and minimizes downtime.
Implement Immediate Solutions
After the severity is assessed, immediate solutions should be implemented to prevent further damage.
This could involve stopping production, quarantining defective products, and informing affected stakeholders.
The goal is to control the issue quickly and prevent it from spreading.
Drafting Recurrence Prevention Plans
Once the immediate issue is contained, the next step is to draft a recurrence prevention plan.
This plan is aimed at identifying the root cause of the problem and implementing measures to ensure it does not happen again.
Root Cause Analysis
Understanding the root cause of the quality issue is essential for developing effective prevention strategies.
Root cause analysis involves detailed investigation and various methodologies, such as:
– **The Five Whys:** Asking “why” five times to drill down to the core of the problem.
– **Fishbone Diagram:** A graphical tool used to identify potential causes of a defect.
– **Failure Mode and Effects Analysis (FMEA):** A systematic approach for evaluating processes to identify where and how they might fail.
Develop Corrective Actions
After identifying the root cause, the next step is to develop corrective actions.
These actions should address the root cause effectively and ensure that it does not recur.
This may involve updating standard operating procedures, retraining employees, or upgrading equipment.
Implement Preventive Measures
Preventive measures should also be put in place to avoid potential future quality issues.
These could include enhanced quality checks, improved supplier vetting processes, and automated monitoring systems.
It’s crucial that these measures are documented and communicated across the organization.
Monitor and Review
Regular monitoring and reviewing of the implemented measures are essential to ensure their effectiveness.
Periodic audits and inspections can help identify areas for improvement and keep the recurrence prevention plan updated.
Feedback from employees and customers can also provide valuable insights for continuous improvement.
Conclusion
Managing quality issues in manufacturing is a multi-faceted task requiring rapid response and detailed planning.
By swiftly identifying and addressing issues, and implementing robust recurrence prevention plans, manufacturers can ensure high-quality products and satisfied customers.
The key lies in proactive measures, effective communication, and continuous monitoring, ensuring that quality issues are managed efficiently and do not recur.
資料ダウンロード
QCD調達購買管理クラウド「newji」は、調達購買部門で必要なQCD管理全てを備えた、現場特化型兼クラウド型の今世紀最高の購買管理システムとなります。
ユーザー登録
調達購買業務の効率化だけでなく、システムを導入することで、コスト削減や製品・資材のステータス可視化のほか、属人化していた購買情報の共有化による内部不正防止や統制にも役立ちます。
NEWJI DX
製造業に特化したデジタルトランスフォーメーション(DX)の実現を目指す請負開発型のコンサルティングサービスです。AI、iPaaS、および先端の技術を駆使して、製造プロセスの効率化、業務効率化、チームワーク強化、コスト削減、品質向上を実現します。このサービスは、製造業の課題を深く理解し、それに対する最適なデジタルソリューションを提供することで、企業が持続的な成長とイノベーションを達成できるようサポートします。
オンライン講座
製造業、主に購買・調達部門にお勤めの方々に向けた情報を配信しております。
新任の方やベテランの方、管理職を対象とした幅広いコンテンツをご用意しております。
お問い合わせ
コストダウンが利益に直結する術だと理解していても、なかなか前に進めることができない状況。そんな時は、newjiのコストダウン自動化機能で大きく利益貢献しよう!
(Β版非公開)