- お役立ち記事
- Reaction process simulation and optimization techniques that process management department leaders in the chemical manufacturing industry should know
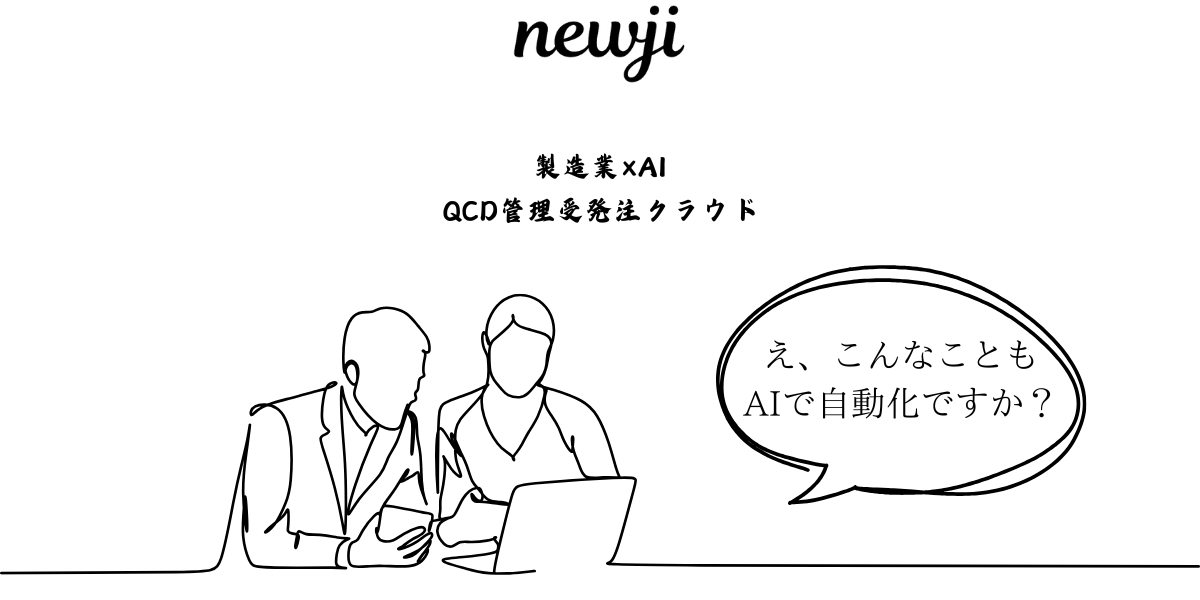
Reaction process simulation and optimization techniques that process management department leaders in the chemical manufacturing industry should know
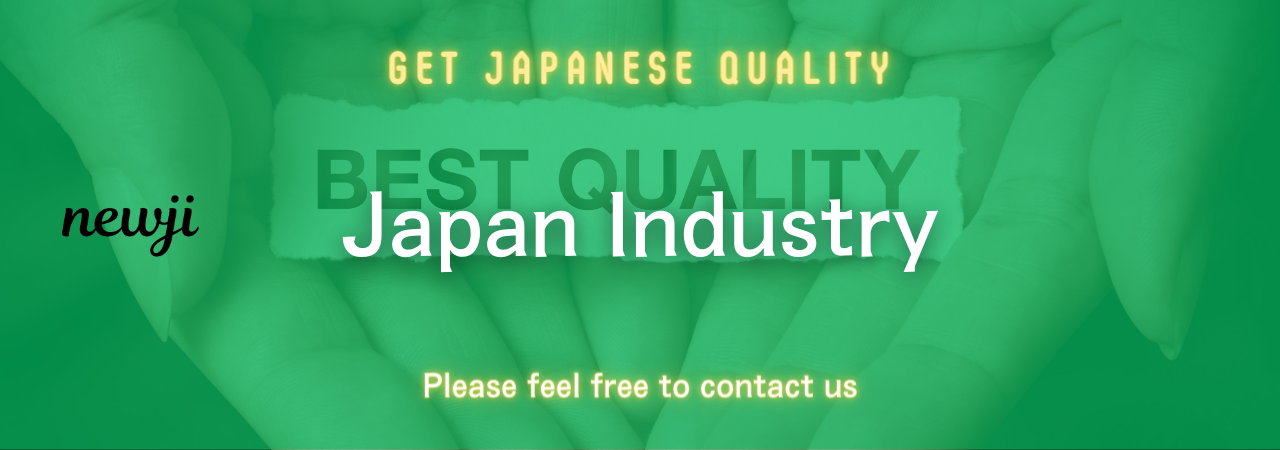
目次
Introduction to Reaction Process Simulation
In the chemical manufacturing industry, understanding and optimizing reaction processes is crucial for enhancing efficiency, reducing costs, and improving safety.
Reaction process simulation is a sophisticated tool that helps in visualizing, analyzing, and optimizing chemical reactions before they are physically executed.
By allowing department leaders to preemptively identify and mitigate potential issues, these simulations serve as a cornerstone for effective process management.
The Basics of Reaction Process Simulation
At its core, reaction process simulation involves using computer models to represent the chemical processes occurring within a reactor.
These models rely on comprehensive data inputs, including reaction kinetics, thermodynamics, and transport properties, to predict how a process will behave under varying conditions.
Simulation software can handle complex reactions, accommodating multiple variables and scenarios.
Key Benefits of Simulation in Chemical Processes
1. **Cost Reduction**: Simulating reactions allows companies to test various scenarios without the expense of physical trials.
This reduces the need for constant resource consumption and minimizes material waste.
2. **Increased Safety**: By predicting the outcomes of different chemical reactions, simulations help identify potential hazards and enable the development of safer procedures.
3. **Process Optimization**: Reaction simulations support the optimization of reaction conditions, such as temperature and pressure, to enhance yield and efficiency.
This is vital for maintaining competitive advantage in the industry.
4. **Troubleshooting**: When issues arise in manufacturing, simulations can be used to diagnose problems quickly, offering insights into potential solutions.
Optimization Techniques in Reaction Process Simulation
Optimization techniques in the context of reaction process simulation are all about fine-tuning the parameters to achieve the best possible outcomes.
Here are some techniques that are indispensable for process management leaders:
Deterministic Optimization
Deterministic optimization involves using specific mathematical models to find the best solution under given constraints.
It is precise and reliable, often used in scenarios where the relationship between variables is well-understood.
This method suits simpler reactions or well-researched chemical processes where predictability is high.
Stochastic Optimization
In contrast, stochastic optimization deals with uncertainty and variability in data.
This approach is beneficial for more complex reactions where the outcomes might be influenced by random variables.
Techniques such as Monte Carlo simulations and genetic algorithms fall under this category, providing robust solutions in uncertain conditions.
Process Control Optimization
This approach focuses on maintaining the desired output of a reaction process by adjusting process variables in real-time.
It ensures that the process remains stable, even in the face of disturbances.
Advanced Process Control (APC) techniques, such as Model Predictive Control (MPC), are often employed to optimize these adjustments.
Sensitivity Analysis
Sensitivity analysis evaluates how changes in input variables affect the output of the simulation.
By identifying which variables have the most significant impact on the reaction, process leaders can prioritize areas for improvement and focus their optimization efforts effectively.
Implementing Simulation and Optimization in Chemical Manufacturing
While the benefits of reaction process simulation and optimization are clear, implementing them in a manufacturing setting requires careful planning and execution.
Integrating Technology into Operations
Successful integration of simulation tools involves seamless incorporation into existing workflows.
This may require upgrading hardware and software infrastructure, along with ensuring that staff are adequately trained to use these new tools.
Collaboration with IT departments and software vendors is crucial to align simulation capabilities with operational needs.
Data Collection and Management
For simulation models to be accurate, they must be fed with reliable data.
This means setting up robust data collection processes, often using sensors and other data-gathering technologies, to ensure that the simulation reflects real-world conditions.
Effective data management practices are essential to maintain the integrity and usability of this information.
Continuous Improvement and Feedback Loops
Implementing simulation and optimization is not a one-time effort but a continuous process.
Establishing feedback loops where the outcomes of implemented changes are analyzed and further refinements are made is key to achieving ongoing performance enhancements.
Challenges and Considerations
While the advantages of reaction process simulation are vast, several challenges need addressing:
1. **Complexity of Models**: As processes become more complex, so do the models, necessitating advanced expertise to interpret results and implement changes.
2. **Data Security and Privacy**: Handling large volumes of data raises concerns about security and intellectual property protection.
3. **Initial Costs**: The initial investment in technology and training can be considerable, but it’s essential to view it as a long-term investment.
4. **Interdisciplinary Collaboration**: Effective simulation requires collaboration across different departments, including R&D, production, and IT.
Conclusion
For leaders in the chemical manufacturing industry, mastering reaction process simulation and optimization is a strategic necessity.
The benefits in terms of safety, efficiency, and cost savings are compelling, and the technological advancements continue to make these tools more accessible and powerful.
By embracing these techniques, process management departments can ensure they stay at the forefront of innovation and competitiveness in the chemical industry.
資料ダウンロード
QCD調達購買管理クラウド「newji」は、調達購買部門で必要なQCD管理全てを備えた、現場特化型兼クラウド型の今世紀最高の購買管理システムとなります。
ユーザー登録
調達購買業務の効率化だけでなく、システムを導入することで、コスト削減や製品・資材のステータス可視化のほか、属人化していた購買情報の共有化による内部不正防止や統制にも役立ちます。
NEWJI DX
製造業に特化したデジタルトランスフォーメーション(DX)の実現を目指す請負開発型のコンサルティングサービスです。AI、iPaaS、および先端の技術を駆使して、製造プロセスの効率化、業務効率化、チームワーク強化、コスト削減、品質向上を実現します。このサービスは、製造業の課題を深く理解し、それに対する最適なデジタルソリューションを提供することで、企業が持続的な成長とイノベーションを達成できるようサポートします。
オンライン講座
製造業、主に購買・調達部門にお勤めの方々に向けた情報を配信しております。
新任の方やベテランの方、管理職を対象とした幅広いコンテンツをご用意しております。
お問い合わせ
コストダウンが利益に直結する術だと理解していても、なかなか前に進めることができない状況。そんな時は、newjiのコストダウン自動化機能で大きく利益貢献しよう!
(Β版非公開)