- お役立ち記事
- Reactor Selection for Industrial Applications
月間77,185名の
製造業ご担当者様が閲覧しています*
*2025年2月28日現在のGoogle Analyticsのデータより
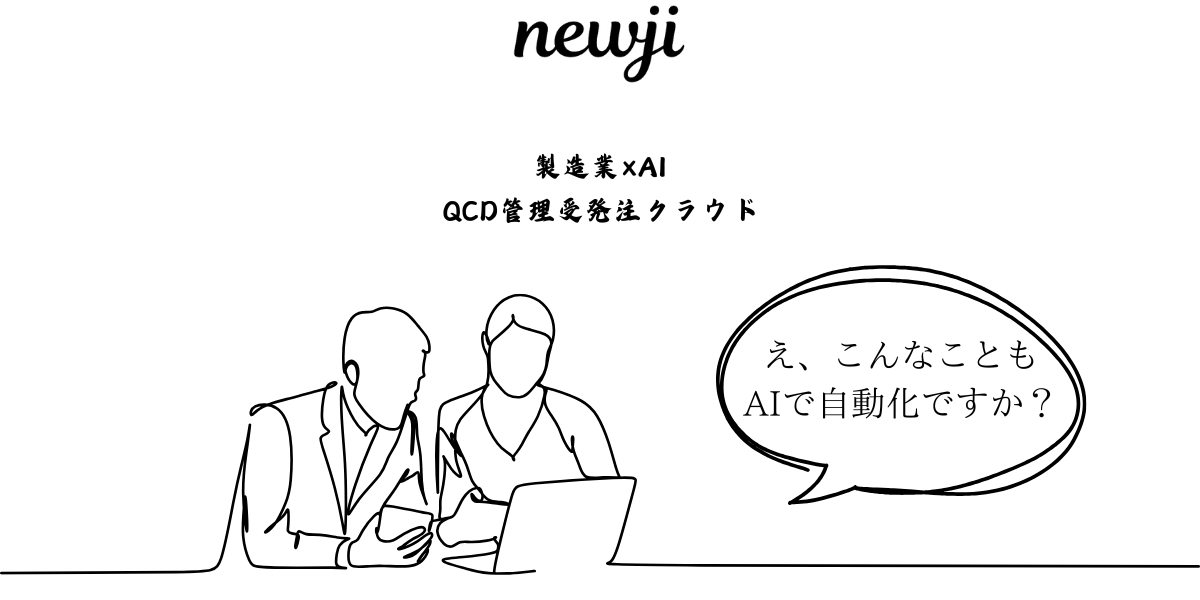
Reactor Selection for Industrial Applications
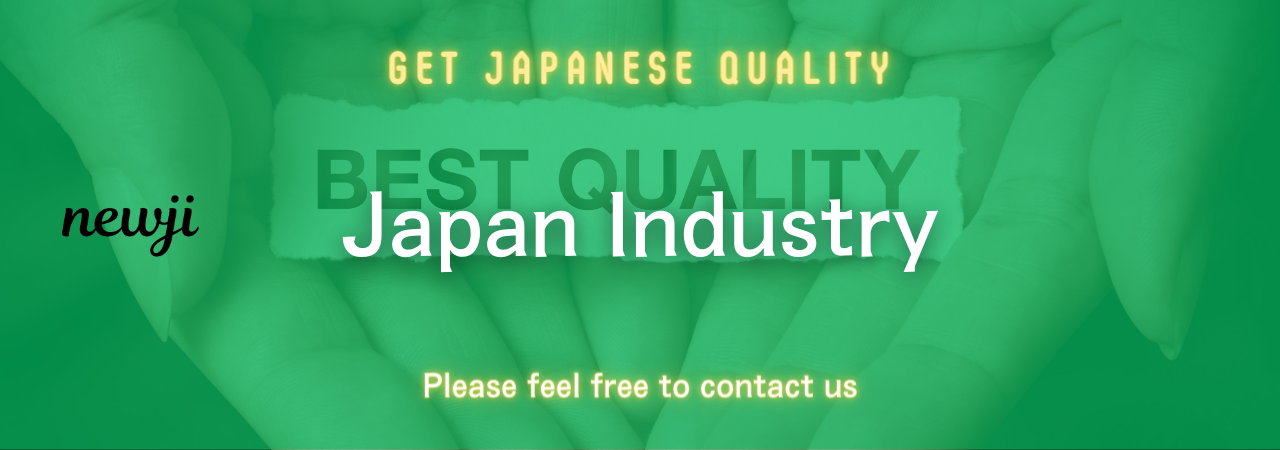
目次
Understanding Reactors in Industrial Applications
Industries that involve chemical processes rely heavily on reactors for their operations.
A reactor’s primary function is to facilitate chemical reactions efficiently and safely, making it a crucial component in sectors like pharmaceuticals, petrochemicals, food processing, and even wastewater treatment.
Choosing the right type of reactor is critical, as it can impact the quality of the end product, the cost-effectiveness of the process, and the overall success of the operation.
Types of Reactors
There are several types of reactors used in industrial applications, each designed for specific processes and outcomes.
Understanding these different types can help in making an informed decision when selecting a reactor for your needs.
Batch Reactors
Batch reactors are perhaps the most straightforward type of reactors.
They are used for processing small amounts of materials where the chemical reaction occurs in batches.
This type of reactor is ideal for processes that require precise control over reaction conditions and for producing high-quality products in limited quantities.
Batch reactors provide significant flexibility as they allow for easy switching between different processes and formulations.
They are commonly used in the pharmaceutical and specialty chemicals industries where customization and batch size variation are frequent.
CSTR (Continuous Stirred-Tank Reactors)
Continuous Stirred-Tank Reactors (CSTR) are used for reactions that require constant agitation and mixing.
These reactors maintain uniform properties throughout the reaction by continuously stirring the mixture.
CSTRs are ideal for large-scale industrial processes where consistency and a steady output are necessary.
They are commonly applied in processes where the reaction kinetics are well understood, and the production requires a continuous flow.
Applications include chemical reactions, fermentation processes, and wastewater treatment.
Plug Flow Reactors (PFR)
A Plug Flow Reactor operates on the principle that reactants are “plugged” into the reactor, flowing through it in a streamlined manner with minimal back-mixing.
These reactors are efficient as they allow for high conversion rates over shorter volumes of the reactor.
PFRs are preferred in industries requiring continuous processing and high throughput, such as in petrochemical industries.
The design helps in maintaining high efficiencies and minimizing costs, as they often require smaller volumes compared to other reactor types for the same level of production.
Packed Bed Reactors
Packed bed reactors are characterized by a fixed arrangement of catalyst particles.
They are ideal for reactions involving gaseous reactants and where high surface area contact with catalysts is required.
These reactors find applications in industries that involve catalytic processes, such as the petrochemical industry for refining processes and in environmental engineering for removing contaminants.
Fluidized Bed Reactors
Fluidized bed reactors offer advantages in terms of heat transfer and reaction rate.
In these reactors, solid catalyst particles are suspended in the fluid flow, creating a uniform mix that enhances the chemical reaction.
Industries use fluidized bed reactors for processes requiring uniform temperature control and effective catalyst usage.
They are widely utilized in the petrochemical industry, for example, in catalytic cracking processes.
Factors to Consider in Reactor Selection
Choosing the appropriate reactor for your industrial application involves various considerations:
Reaction Type
Different reactors are better suited for different types of reactions.
Consider factors such as whether the reaction is endothermic or exothermic, the desired conversion rate, and whether the reaction requires a catalyst.
Scale of Production
The production scale significantly impacts reactor selection.
For small-scale production or research purposes, batch reactors may be ideal.
Conversely, for large-scale continuous production, CSTRs or PFRs might be more suitable.
Material Properties
The physical and chemical properties of the reactants and products are critical in determining the reactor type.
For example, if you’re dealing with highly corrosive materials, selecting a reactor made from resistant materials is essential.
Process Economics
Cost-effectiveness is a primary consideration.
Assess the reactor in terms of initial installation costs, operational and maintenance expenses, and energy needs.
Choose a reactor that offers the best balance between cost and efficiency.
Safety Considerations
Safety is paramount in chemical processes.
Evaluate the reactor’s ability to contain high pressures, temperatures, and potentially hazardous reactions.
Ensure the design adheres to industry regulations and standards.
Conclusion
Selecting the correct reactor for industrial applications is a multidimensional decision that requires thorough analysis and consideration of the specific process requirements.
By understanding the types of reactors available and the distinct needs of your operation, you can make informed decisions that optimize production, ensure safety, and enhance overall efficiency.
In the ever-evolving landscape of industrial processes, making the right choice in reactor selection is a foundational step toward achieving operational success.
資料ダウンロード
QCD管理受発注クラウド「newji」は、受発注部門で必要なQCD管理全てを備えた、現場特化型兼クラウド型の今世紀最高の受発注管理システムとなります。
ユーザー登録
受発注業務の効率化だけでなく、システムを導入することで、コスト削減や製品・資材のステータス可視化のほか、属人化していた受発注情報の共有化による内部不正防止や統制にも役立ちます。
NEWJI DX
製造業に特化したデジタルトランスフォーメーション(DX)の実現を目指す請負開発型のコンサルティングサービスです。AI、iPaaS、および先端の技術を駆使して、製造プロセスの効率化、業務効率化、チームワーク強化、コスト削減、品質向上を実現します。このサービスは、製造業の課題を深く理解し、それに対する最適なデジタルソリューションを提供することで、企業が持続的な成長とイノベーションを達成できるようサポートします。
製造業ニュース解説
製造業、主に購買・調達部門にお勤めの方々に向けた情報を配信しております。
新任の方やベテランの方、管理職を対象とした幅広いコンテンツをご用意しております。
お問い合わせ
コストダウンが利益に直結する術だと理解していても、なかなか前に進めることができない状況。そんな時は、newjiのコストダウン自動化機能で大きく利益貢献しよう!
(β版非公開)