- お役立ち記事
- Real-time monitoring to reduce defective rates that new leaders of quality control departments in the plastic molding industry should address
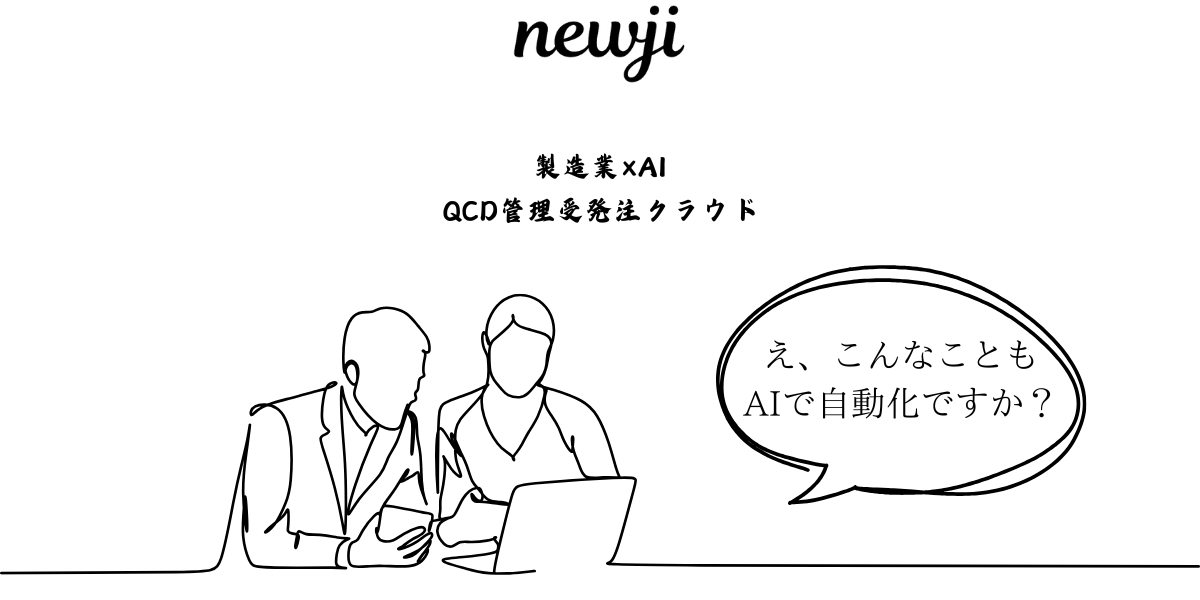
Real-time monitoring to reduce defective rates that new leaders of quality control departments in the plastic molding industry should address
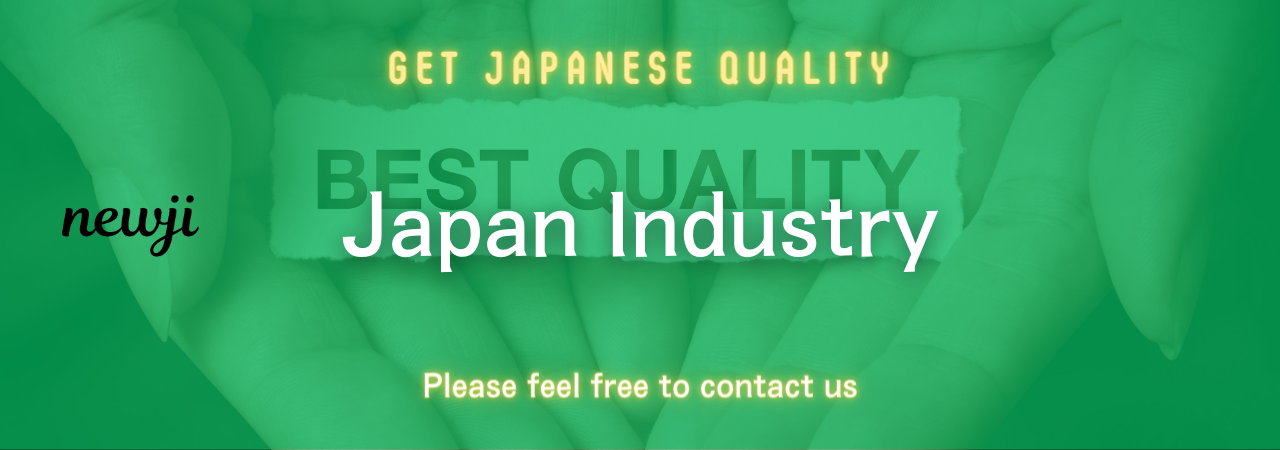
目次
Understanding Real-Time Monitoring in Quality Control
Real-time monitoring is an advanced technological approach used in various industries to enhance quality control processes.
In the plastic molding industry, quality control is essential to ensure the production of defect-free products.
By adopting real-time monitoring, the new leaders of quality control departments can significantly reduce defective rates and improve overall product quality.
Real-time monitoring involves the continuous observation and analysis of production processes through digital tools.
This continuous stream of data allows for immediate feedback and intervention, enabling companies to quickly identify and rectify any issues that may arise during the manufacturing process.
Advantages of Real-Time Monitoring
The primary advantage of real-time monitoring in quality control is the ability to detect defects as they occur.
This immediate detection enables a rapid response, reducing the number of defective products produced.
It also helps prevent costly recalls and rework, saving both time and money for the business.
Another advantage is improved efficiency.
With real-time monitoring, production teams can optimize processes based on data-driven insights.
This data helps in identifying bottlenecks, understanding machine performance, and scheduling maintenance before a significant breakdown occurs.
Additionally, real-time monitoring aids in maintaining consistency in product quality.
Consistent quality is critical in the plastic molding industry, where even minor deviations can lead to significant functionality and safety issues.
By ensuring consistency, companies can meet customer expectations and maintain a strong reputation in the market.
Implementing Real-Time Monitoring Systems
For new leaders in quality control, implementing a real-time monitoring system may seem daunting.
However, with the right approach, it can be achieved successfully.
The first step is to select the appropriate monitoring tools and software that align with the company’s specific needs and resources.
These tools should be capable of capturing and analyzing relevant data streams from various stages of the manufacturing process.
Once the tools are selected, the next step is to ensure that the equipment and machinery are integrated with the monitoring system.
This integration allows for seamless data flow and accurate analysis, which is crucial for effective monitoring.
Training staff to work efficiently with real-time monitoring systems is also vital.
Employees need to understand how to interpret data and utilize it to make informed decisions quickly.
Training should also emphasize the importance of quick responses to the alerts generated by the monitoring system.
Tackling Challenges in Real-Time Monitoring Implementation
Despite its benefits, implementing real-time monitoring can present several challenges.
One of the biggest challenges is the cost of setting up the system.
New monitoring tools and software can be expensive, which may be a concern for companies with limited budgets.
However, it is essential to view this investment as a long-term cost-saving measure, as the reduction in defective rates and waste will ultimately outweigh the initial expenditure.
Another challenge is the potential resistance to change from staff.
Employees may be accustomed to traditional quality control methods, and transitioning to a new system could be met with apprehension.
Leaders should address these concerns by communicating the benefits of real-time monitoring and providing adequate training and support during the transition phase.
Data security is another concern that can’t be overlooked.
As real-time monitoring systems collect vast amounts of data, it is crucial to ensure that stringent security measures are in place to protect sensitive information from breaches and cyber threats.
The Role of Data Analysis in Real-Time Monitoring
Data analysis plays a significant role in the success of real-time monitoring.
The ability to convert raw data into actionable insights is what makes real-time monitoring a powerful tool for quality control leaders.
Advanced data analysis techniques, such as machine learning and artificial intelligence, can predict defects before they occur, allowing proactive measures to be taken.
Furthermore, data analysis helps in understanding trends and patterns in production processes.
By analyzing historical data, companies can identify factors that have contributed to defects in the past and develop strategies to prevent them in the future.
This proactive approach not only improves quality control but also enhances overall operational efficiency.
Conclusion: Embracing Real-Time Monitoring for Quality Improvement
In conclusion, real-time monitoring is a valuable asset for new leaders of quality control departments in the plastic molding industry.
It offers numerous benefits, including defect reduction, improved efficiency, and consistency in product quality.
While the initial implementation may present challenges, the long-term advantages far outweigh the difficulties.
By investing in appropriate tools, integrating systems, training staff, and securing data, companies can fully utilize the potential of real-time monitoring.
Embracing this technology will not only enhance current manufacturing processes but also pave the way for future innovations and quality improvements in the plastic molding industry.
資料ダウンロード
QCD調達購買管理クラウド「newji」は、調達購買部門で必要なQCD管理全てを備えた、現場特化型兼クラウド型の今世紀最高の購買管理システムとなります。
ユーザー登録
調達購買業務の効率化だけでなく、システムを導入することで、コスト削減や製品・資材のステータス可視化のほか、属人化していた購買情報の共有化による内部不正防止や統制にも役立ちます。
NEWJI DX
製造業に特化したデジタルトランスフォーメーション(DX)の実現を目指す請負開発型のコンサルティングサービスです。AI、iPaaS、および先端の技術を駆使して、製造プロセスの効率化、業務効率化、チームワーク強化、コスト削減、品質向上を実現します。このサービスは、製造業の課題を深く理解し、それに対する最適なデジタルソリューションを提供することで、企業が持続的な成長とイノベーションを達成できるようサポートします。
オンライン講座
製造業、主に購買・調達部門にお勤めの方々に向けた情報を配信しております。
新任の方やベテランの方、管理職を対象とした幅広いコンテンツをご用意しております。
お問い合わせ
コストダウンが利益に直結する術だと理解していても、なかなか前に進めることができない状況。そんな時は、newjiのコストダウン自動化機能で大きく利益貢献しよう!
(Β版非公開)