- お役立ち記事
- Real-time monitoring using chemical plant automation and IoT
月間77,185名の
製造業ご担当者様が閲覧しています*
*2025年2月28日現在のGoogle Analyticsのデータより
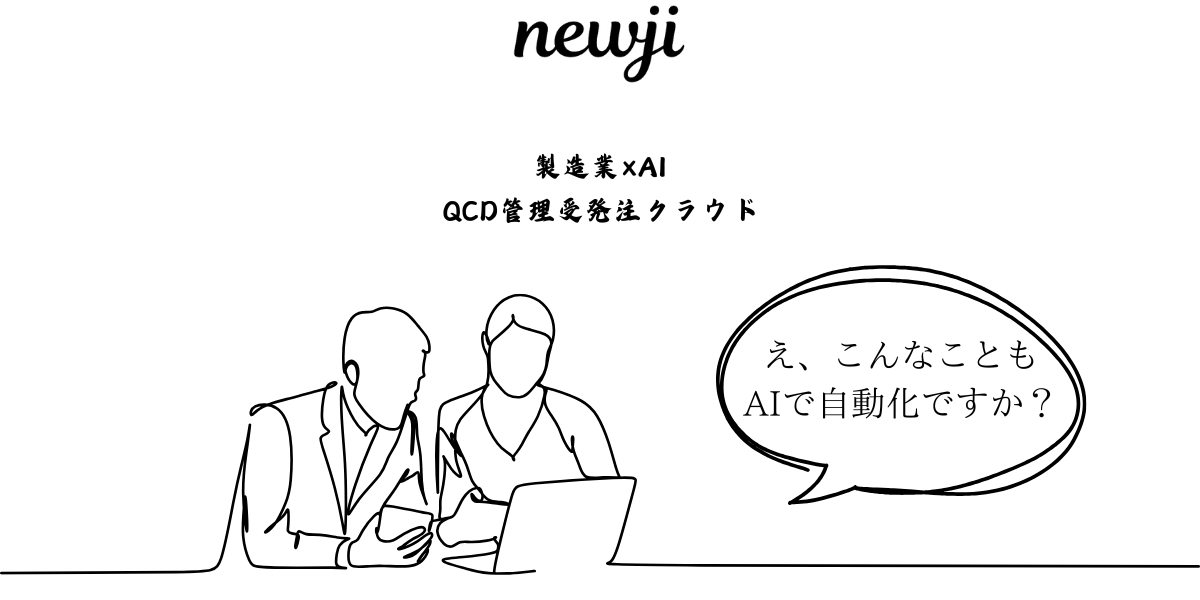
Real-time monitoring using chemical plant automation and IoT
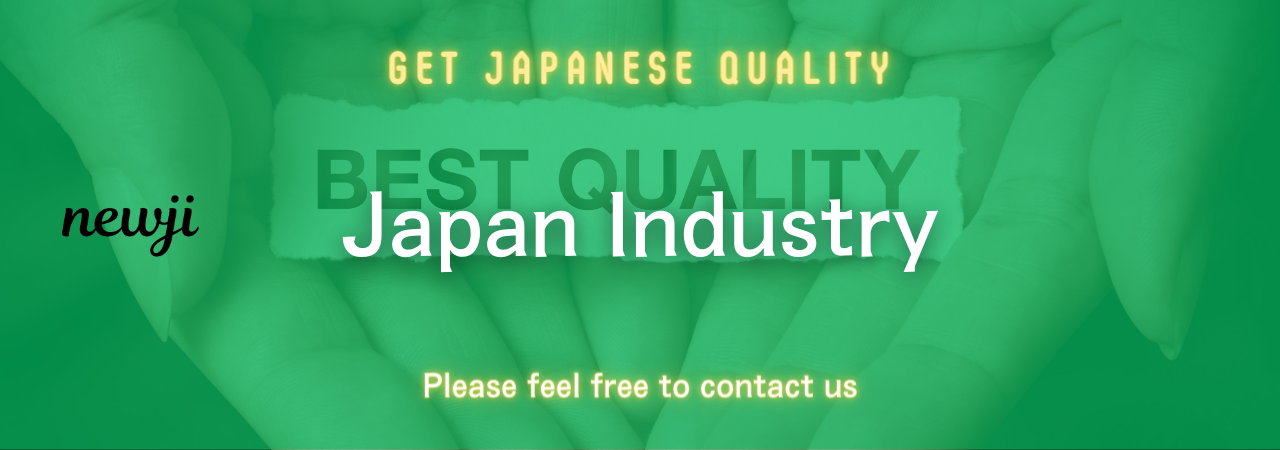
目次
Introduction to Real-Time Monitoring in Chemical Plants
The rise of automation and the Internet of Things (IoT) has revolutionized various industries, including chemical manufacturing.
In this highly competitive sector, staying ahead of the curve is essential.
Real-time monitoring using chemical plant automation and IoT provides new opportunities for efficient operations, safety improvements, and cost savings.
With these technologies in place, chemical plants can gain an unprecedented level of control over their processes, ensuring the highest standards of production quality.
What Is Real-Time Monitoring?
Real-time monitoring refers to the continuous tracking of operations and processes as they occur, providing immediate data that can be analyzed and acted upon.
In the context of chemical plants, it involves using automation and IoT to gather information about plant processes and equipment performance.
This data can be displayed on dashboards and analyzed to optimize plant operations, enhance safety protocols, and minimize downtime and energy use.
The Role of IoT in Chemical Plant Automation
IoT plays a crucial part in real-time monitoring by connecting various devices and systems within a chemical plant.
Smart sensors are embedded in equipment to gather valuable data, such as temperature, pressure, and flow rates.
These sensors communicate over networks to share information with centralized systems for analysis.
By harnessing IoT, chemical plants transform into connected ecosystems.
Streamlined data flows enable predictive analytics, which anticipates equipment maintenance needs, preventing costly breakdowns and extending the lifespan of critical infrastructure.
The vast amounts of data collected improve decision-making and lead to more intelligent and efficient plant operations.
Automation Enhances Plant Efficiency
Automation technology helps chemical plants operate with greater precision and efficiency.
Process control systems automate routine tasks, reducing the potential for human error.
They allow operators to focus on more strategic activities that require human intervention and expertise.
Automated control systems maintain optimal conditions, adjusting variables in real-time to avoid waste and ensure products meet stringent quality standards.
Robotic systems operate tirelessly, performing complex tasks with accuracy that humans may struggle to match.
They are particularly useful in managing hazardous materials, enhancing safety by minimizing human interaction with dangerous substances.
Enhancing Safety with Real-Time Monitoring
Safety is paramount in chemical plants, where hazardous substances and processes can pose significant risks.
Real-time monitoring bolsters safety measures by providing constant oversight of plant conditions.
Sensors detect anomalies such as leaks or temperature spikes, alerting operators immediately so that corrective actions can be taken before these issues escalate into emergencies.
Moreover, real-time data supports safety management systems with insights to improve safety protocols continuously.
By analyzing trends, chemical plants can identify potential risks and implement proactive safety measures.
This reduces the likelihood of accidents and contributes to a safer working environment for employees.
Cost Savings and Environmental Impact
Real-time monitoring also drives cost savings and reduces the environmental impact of chemical plant operations.
Automated systems optimize resource use, minimizing waste and energy consumption.
This leads to significant cost reductions and aligns with sustainability goals by reducing the plant’s carbon footprint.
Through predictive maintenance facilitated by IoT, chemical plants avoid unplanned shutdowns and repairs, which can add significantly to operational costs.
By preemptively addressing equipment issues, companies save on maintenance expenses and improve overall plant efficiency.
Challenges in Implementing Real-Time Monitoring
While the benefits of real-time monitoring are compelling, implementation can present its own set of challenges.
Investing in IoT devices and automation infrastructure requires substantial upfront costs.
Companies must also invest in training staff to manage and maintain these systems effectively.
Data management is another key challenge.
With vast amounts of data generated by IoT devices, chemical plants require robust data analytics and storage solutions.
Ensuring data security and protecting sensitive information from cyber threats is vital as well.
Future Prospects of IoT and Automation in Chemical Plants
The future of real-time monitoring in chemical plants looks promising, with continuous advancements in technology.
The integration of artificial intelligence (AI) and machine learning will enhance predictive analytics, offering even more profound insights into plant operations.
Emerging technologies such as digital twins—virtual replicas of physical systems—allow for real-time simulations, improving design and operational planning.
As automation and IoT technology evolve, we can expect even more innovative applications that push the boundaries of what’s possible in chemical plant management.
However, to stay ahead, companies must remain proactive, investing in research and development to harness the full potential of these technologies.
Conclusion
Real-time monitoring using chemical plant automation and IoT offers transformative benefits across safety, efficiency, cost savings, and environmental impact.
While challenges exist, they are outweighed by the opportunities for enhanced performance and competitive advantage.
By embracing these technologies, chemical plants can achieve greater operational excellence and sustainability, setting new standards for the industry and ensuring long-term success.
資料ダウンロード
QCD管理受発注クラウド「newji」は、受発注部門で必要なQCD管理全てを備えた、現場特化型兼クラウド型の今世紀最高の受発注管理システムとなります。
ユーザー登録
受発注業務の効率化だけでなく、システムを導入することで、コスト削減や製品・資材のステータス可視化のほか、属人化していた受発注情報の共有化による内部不正防止や統制にも役立ちます。
NEWJI DX
製造業に特化したデジタルトランスフォーメーション(DX)の実現を目指す請負開発型のコンサルティングサービスです。AI、iPaaS、および先端の技術を駆使して、製造プロセスの効率化、業務効率化、チームワーク強化、コスト削減、品質向上を実現します。このサービスは、製造業の課題を深く理解し、それに対する最適なデジタルソリューションを提供することで、企業が持続的な成長とイノベーションを達成できるようサポートします。
製造業ニュース解説
製造業、主に購買・調達部門にお勤めの方々に向けた情報を配信しております。
新任の方やベテランの方、管理職を対象とした幅広いコンテンツをご用意しております。
お問い合わせ
コストダウンが利益に直結する術だと理解していても、なかなか前に進めることができない状況。そんな時は、newjiのコストダウン自動化機能で大きく利益貢献しよう!
(β版非公開)