- お役立ち記事
- Rectifier DC power supply technology and implementation examples in the industrial equipment market
月間77,185名の
製造業ご担当者様が閲覧しています*
*2025年2月28日現在のGoogle Analyticsのデータより
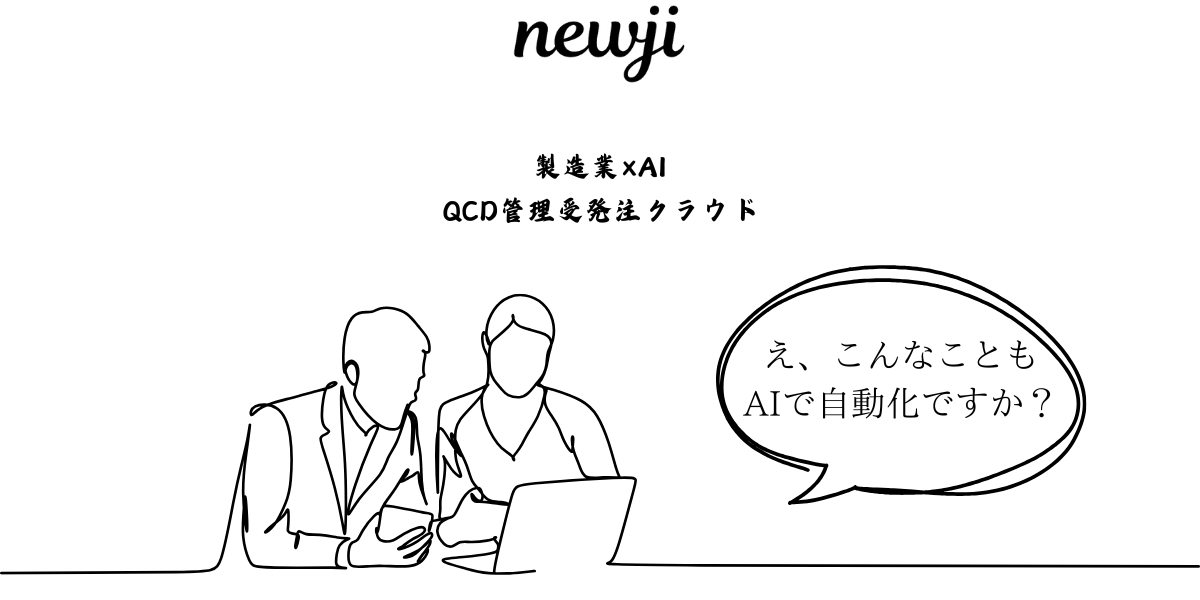
Rectifier DC power supply technology and implementation examples in the industrial equipment market
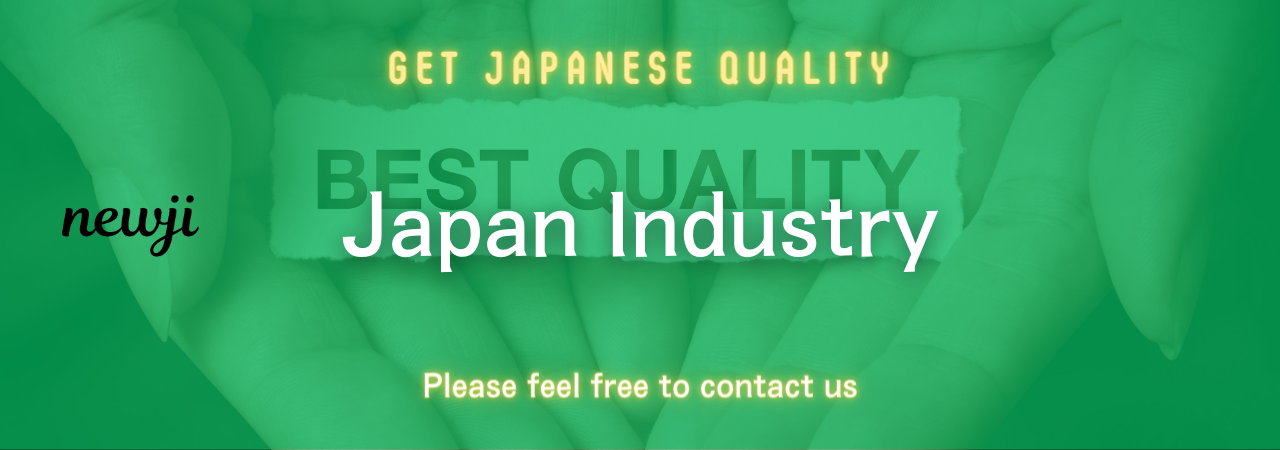
目次
Introduction to Rectifier DC Power Supply
In the ever-evolving industrial equipment market, rectifier DC power supply technology plays a crucial role by converting alternating current (AC) into direct current (DC).
This conversion process is vital for powering various industrial machinery and electronic devices that require a stable and consistent DC supply.
Typically, AC power is the standard for transmission and distribution, but many applications need DC power to function effectively.
Importance of DC Power Supply in Industrial Markets
In industries ranging from manufacturing to telecommunications, the need for reliable DC power sources can’t be understated.
Applications that require DC power include battery charging systems, electroplating, and electric vehicles, among others.
These diverse applications demonstrate the essential nature of a stable DC power input derived from effective rectifier technology.
Supporting Technological Advancements
The rapid pace of technological advancements in industrial equipment has increased the demand for high-quality rectifier DC power supplies.
As more devices become automated and integrated with advanced electronics, ensuring they receive the correct power input is becoming increasingly complex, hence the heightened interest in improved rectifier technology.
Basic Principles of Rectifier DC Power Supply
The process of converting AC power to DC involves several essential components and principles.
The standard method employs diodes, which allow current to pass in only one direction, thus rectifying the AC waveform into a unidirectional flow.
Diode Technology
Diodes form the backbone of rectifier technology.
They are semiconductor devices that only permit electrical current to flow in a single direction, effectively blocking any current that tries to move in the opposite direction.
This property is utilized in converting AC, which alternates direction, into DC, which flows uniformly in one direction.
Types of Rectifiers
There are three primary types of rectifiers used in industrial applications: half-wave, full-wave, and bridge rectifiers.
– Half-wave rectifiers utilize a single diode, which allows only half of the AC waveform to pass through, resulting in a significant loss of energy.
However, they are simple and cost-effective for low-power applications.
– Full-wave rectifiers, on the other hand, use more complex circuits to convert the entire AC waveform into DC.
This type is more efficient and suitable for higher-power applications.
– Bridge rectifiers employ four or more diodes arranged in a bridge configuration.
They provide full-wave rectification without the need for a center-tapped transformer and are frequently used due to their efficiency and ease of implementation.
Implementing Rectifier DC Power Supply in Industries
The implementation of rectifier DC power supplies in industrial settings involves a careful selection of rectifier types and configurations based on specific application needs.
Customization for Industry Needs
Industries often require customized power supply solutions tailored to their operational requirements.
For instance, battery manufacturing industries might use controlled rectifiers that offer precise current control, crucial for ensuring the quality and longevity of batteries.
Examples of Industrial Applications
Many industries rely heavily on rectifiers for their operations:
– **Electroplating**: The process of coating metals requires a steady and reliable DC power supply to ensure uniform deposition of material.
– **Welding Equipment**: For welding processes, rectifiers provide the necessary DC power to facilitate smooth and efficient operation.
– **Railway Systems**: Rectifiers are crucial in converting AC from overhead lines into DC for railway traction systems.
These examples illustrate the broad utility and necessity of rectifier DC power supplies across different industrial sectors.
Challenges and Solutions in Rectifier Technology
Innovations and improvements in rectifier technology are continuously driven by challenges such as efficiency, heat management, and minimizing power loss.
Efficiency Improvement
One significant challenge is enhancing the conversion efficiency of AC to DC, minimizing energy waste.
Modern rectifiers aim to maximize efficiency through improved materials and design, such as incorporating high-efficiency diodes and advanced semiconductor technologies.
Heat Management
Rectifiers dissipate heat as a byproduct of converting AC to DC.
Managing this heat is critical to prevent damage and maintain longevity.
Innovations in heat sink designs and cooling systems have provided effective solutions in dissipating excess heat.
Regulatory Compliance
Rectifier systems must comply with varying international standards and regulations.
These requirements can influence the design and implementation of power supplies, demanding constant adaptation to new guidelines and advancements in standards.
Future Trends in Rectifier DC Power Supply
The demand for efficient rectifier DC power supplies is predicted to grow, driven by developments in renewable energy and electric vehicles.
Integration with Renewable Energy
The rise of renewable energy sources like solar and wind power, which generate DC output, presents opportunities for integrating advanced rectifier systems to optimize energy usage and storage.
Electric Vehicle Applications
Electric vehicles require reliable and efficient DC power supplies.
Advancements in rectifier technology significantly contribute to the rapidly expanding EV market by enhancing vehicle charging systems and energy management.
Conclusion
Rectifier DC power supply technology remains a vital component in the industrial equipment market.
Its applications are vast, spanning several crucial sectors.
By continually adapting to technological advancements and industry needs, rectifiers will continue to be integral to powering the future of industrial and technological growth.
資料ダウンロード
QCD管理受発注クラウド「newji」は、受発注部門で必要なQCD管理全てを備えた、現場特化型兼クラウド型の今世紀最高の受発注管理システムとなります。
ユーザー登録
受発注業務の効率化だけでなく、システムを導入することで、コスト削減や製品・資材のステータス可視化のほか、属人化していた受発注情報の共有化による内部不正防止や統制にも役立ちます。
NEWJI DX
製造業に特化したデジタルトランスフォーメーション(DX)の実現を目指す請負開発型のコンサルティングサービスです。AI、iPaaS、および先端の技術を駆使して、製造プロセスの効率化、業務効率化、チームワーク強化、コスト削減、品質向上を実現します。このサービスは、製造業の課題を深く理解し、それに対する最適なデジタルソリューションを提供することで、企業が持続的な成長とイノベーションを達成できるようサポートします。
製造業ニュース解説
製造業、主に購買・調達部門にお勤めの方々に向けた情報を配信しております。
新任の方やベテランの方、管理職を対象とした幅広いコンテンツをご用意しております。
お問い合わせ
コストダウンが利益に直結する術だと理解していても、なかなか前に進めることができない状況。そんな時は、newjiのコストダウン自動化機能で大きく利益貢献しよう!
(β版非公開)