- お役立ち記事
- Recurrence prevention measures and key points based on why-why analysis
月間76,176名の
製造業ご担当者様が閲覧しています*
*2025年3月31日現在のGoogle Analyticsのデータより
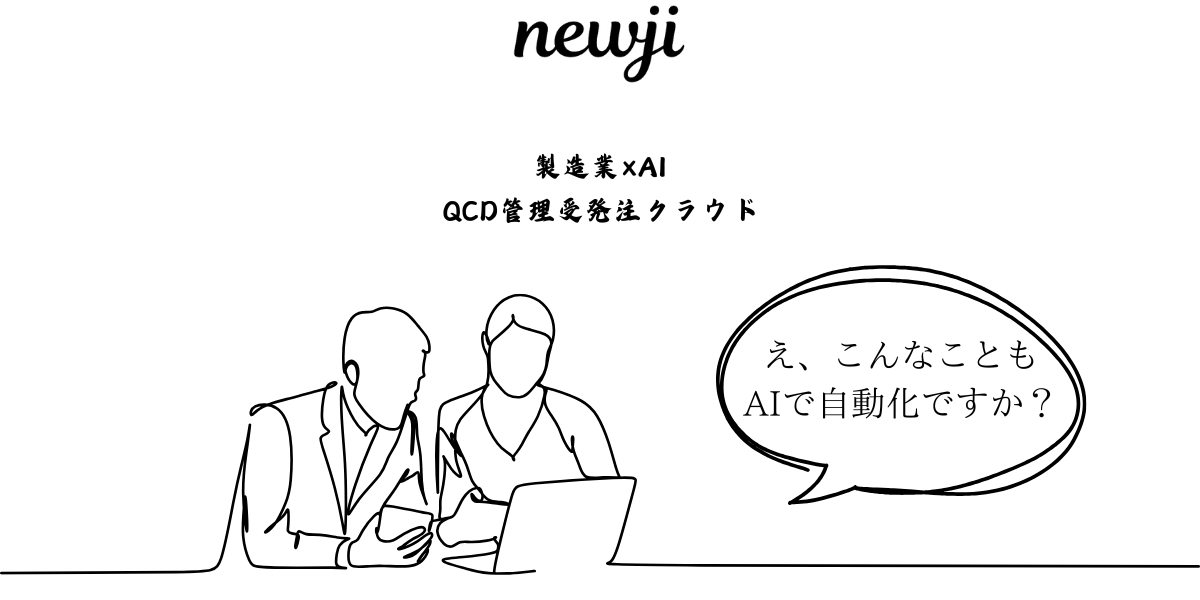
Recurrence prevention measures and key points based on why-why analysis
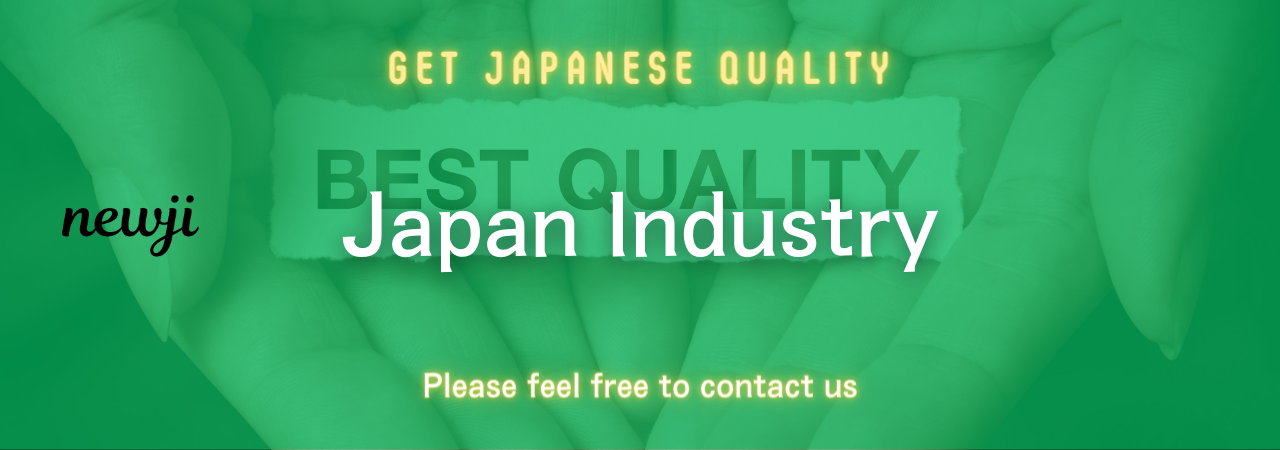
目次
Understanding Why-Why Analysis
Why-Why Analysis is a powerful tool used to identify the root causes of a problem or issue.
It is a simple yet effective method that involves asking “why” multiple times until the fundamental cause of the problem is uncovered.
The technique is particularly useful in preventing recurrence by ensuring that the real issues are addressed rather than just the symptoms.
How Does Why-Why Analysis Work?
The Why-Why Analysis process begins with the identification of a problem.
Once the problem has been clearly defined, the first “why” is asked to understand the immediate cause.
For example, if a machine stops working, the first question might be, “Why did the machine stop?”
The answer could be, “Because the engine overheated.”
Next, the next “why” question could be, “Why did the engine overheat?”
This process continues until the root cause is identified.
The aim is to reach a level where actionable solutions can be put in place to prevent the issue from occurring again.
Benefits of Using Why-Why Analysis
The Why-Why Analysis offers several key benefits, including:
– **Simplicity**: The method is straightforward and does not require any complex tools or software.
– **In-Depth Understanding**: It encourages a deeper understanding of the problem, which can lead to more effective solutions.
– **Focus on Root Causes**: By identifying the fundamental cause of a problem, it helps in implementing measures that prevent recurrence.
– **Collaboration**: This method often involves different stakeholders, leading to a more collaborative approach to problem-solving.
Common Challenges and Solutions
While Why-Why Analysis is a valuable tool, it can present certain challenges:
– **Subjectivity**: Responses can vary based on individual perspectives, potentially leading to biased conclusions.
To address this, involve a diverse team to gain multiple insights and a more balanced view.
– **Over-Simplification**: There is a risk of oversimplifying complex problems by stopping the questioning too soon.
Ensure thorough investigation by continuing to ask “why” until no more answers can be provided.
– **Inexperienced Participants**: Participants unfamiliar with the process may struggle with identifying appropriate reasons.
Provide training or guidance to ensure everyone understands how to conduct the analysis effectively.
Implementing Recurrence Prevention Measures
Once the root cause is identified through Why-Why Analysis, the next step is to develop effective recurrence prevention measures:
Create an Action Plan
An action plan should clearly outline the steps needed to address the root cause.
Include specific tasks, responsible parties, and timelines to ensure accountability and progress tracking.
Develop Standard Operating Procedures (SOPs)
Incorporate changes or improvements into Standard Operating Procedures.
SOPs will serve to institutionalize solutions and ensure that best practices are followed consistently.
Train and Communicate
Educate all relevant stakeholders on the new procedures or changes to ensure smooth implementation.
Effective communication is vital to ensure everyone understands their roles and responsibilities in the process.
Monitoring and Continuous Improvement
After implementing solutions, it is crucial to monitor progress and assess the effectiveness of the measures:
Evaluate Outcomes
Continuously evaluate the outcomes to ensure the problem does not recur.
Regular assessments can help identify any gaps or areas that require further attention.
Adjust and Improve
Feedback should be used to make necessary adjustments and improvements over time.
The process of monitoring and improving should be ongoing, allowing for a dynamic approach to problem-solving.
Conclusion
Why-Why Analysis is a valuable technique for identifying root causes and developing effective recurrence prevention measures.
By asking “why” multiple times, it facilitates a deeper understanding of problems and ensures that solutions address the underlying issues.
Implementing an action plan, developing SOPs, and engaging in continuous monitoring are essential steps in preventing recurrence and fostering a culture of continuous improvement.
資料ダウンロード
QCD管理受発注クラウド「newji」は、受発注部門で必要なQCD管理全てを備えた、現場特化型兼クラウド型の今世紀最高の受発注管理システムとなります。
ユーザー登録
受発注業務の効率化だけでなく、システムを導入することで、コスト削減や製品・資材のステータス可視化のほか、属人化していた受発注情報の共有化による内部不正防止や統制にも役立ちます。
NEWJI DX
製造業に特化したデジタルトランスフォーメーション(DX)の実現を目指す請負開発型のコンサルティングサービスです。AI、iPaaS、および先端の技術を駆使して、製造プロセスの効率化、業務効率化、チームワーク強化、コスト削減、品質向上を実現します。このサービスは、製造業の課題を深く理解し、それに対する最適なデジタルソリューションを提供することで、企業が持続的な成長とイノベーションを達成できるようサポートします。
製造業ニュース解説
製造業、主に購買・調達部門にお勤めの方々に向けた情報を配信しております。
新任の方やベテランの方、管理職を対象とした幅広いコンテンツをご用意しております。
お問い合わせ
コストダウンが利益に直結する術だと理解していても、なかなか前に進めることができない状況。そんな時は、newjiのコストダウン自動化機能で大きく利益貢献しよう!
(β版非公開)