- お役立ち記事
- “Reducing raw material loss”—Management methods and goal setting that should be practiced at manufacturing sites
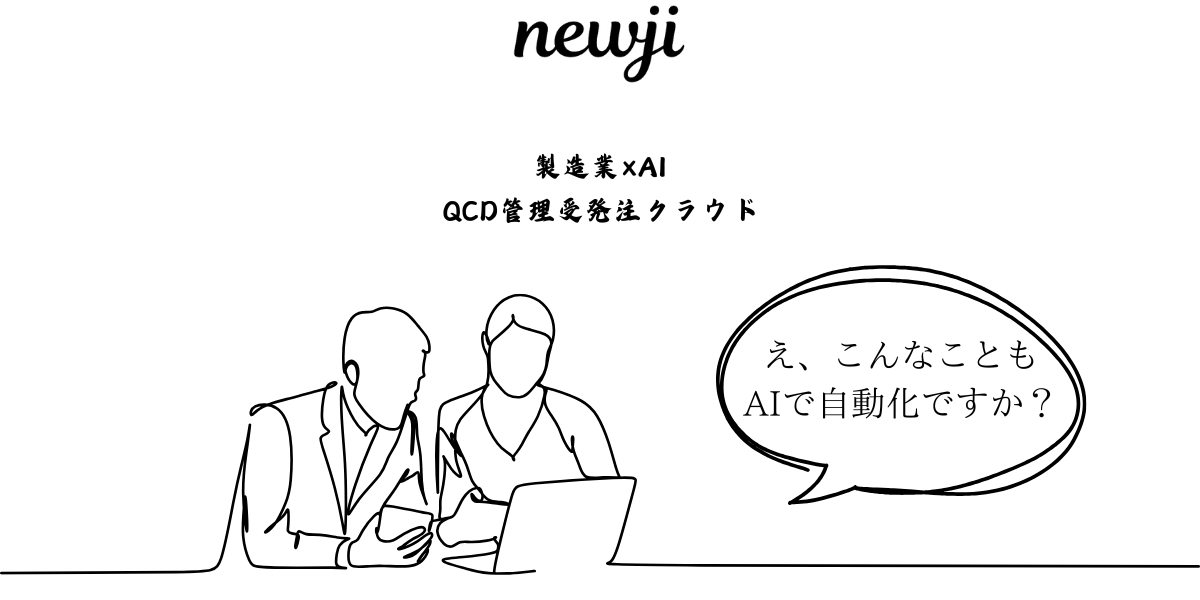
“Reducing raw material loss”—Management methods and goal setting that should be practiced at manufacturing sites
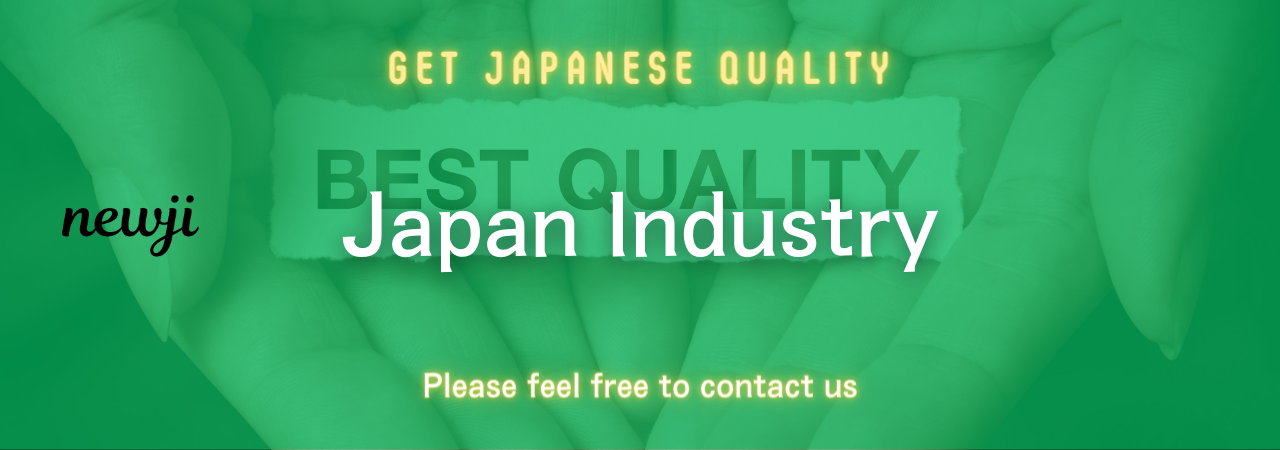
目次
Understanding Raw Material Loss in Manufacturing
Manufacturing is a complex process that involves the transformation of raw materials into finished products.
One of the significant challenges faced by manufacturers is raw material loss.
Raw material loss refers to the wastage that occurs when materials used in production do not completely make it into the final product.
This loss can happen due to various reasons, such as inefficiencies in the production line, spoilage, or mishandling of materials.
Reducing raw material loss is crucial for several reasons.
It not only impacts the cost of production but also affects the environmental footprint of the manufacturing process.
Less waste means fewer resources are needed, ultimately leading to more sustainable practices.
Strategies to Reduce Raw Material Loss
Reducing raw material loss requires strategic planning and implementation of effective management methods.
The following strategies can help manufacturers minimize wastage:
1. Implementing Process Improvements
One of the most effective ways to reduce raw material loss is by enhancing the efficiency of production processes.
Conducting regular audits and evaluations can help identify bottlenecks and areas for improvement.
Streamlining processes, upgrading equipment, and training staff can lead to fewer errors and waste.
2. Embracing Technology
Technology plays a pivotal role in minimizing raw material loss.
Investing in advanced automation and monitoring systems can help track inventory levels, monitor production lines, and predict potential issues before they occur.
Using data analytics can provide insights into patterns of waste, allowing manufacturers to make informed decisions.
3. Improved Inventory Management
Proper inventory management ensures that raw materials are used efficiently and are less likely to expire or go unused.
Utilizing inventory management software can help keep track of materials, set reorder levels, and avoid overstocking or shortages.
4. Employee Training and Engagement
Employees are the backbone of any manufacturing operation.
Properly trained employees are less likely to make mistakes that lead to waste.
Regular training programs and workshops can improve skills and ensure that everyone is on the same page regarding waste reduction goals.
5. Quality Control Measures
Instituting rigorous quality control measures can prevent substandard products from being produced, reducing the need to discard defective items.
Regular checks at various stages of production can ensure that quality standards are met.
Setting Goals for Raw Material Loss Reduction
Establishing clear goals is essential for reducing raw material loss effectively.
Here are some steps to consider when setting these goals:
1. Assess Current Loss Levels
Before setting goals, it’s essential to understand the current levels of raw material loss.
This assessment can be done through data collection and analysis of production records over a specific period.
2. Set Realistic Targets
Based on the assessment, set achievable and realistic targets for reducing material loss.
Consider using a phased approach, where smaller goals are set within short timeframes, gradually leading to more significant reductions.
3. Monitor Progress Regularly
Monitoring progress is crucial to ensure that the goals set are being met.
Regular reviews and feedback sessions can help identify areas where targets are not being met and adjust strategies accordingly.
4. Foster a Culture of Continuous Improvement
Encourage a company-wide culture that embraces continuous improvement.
Involve employees in goal setting and ask for their input on potential changes.
This engagement can result in innovative ideas and solutions that management alone might overlook.
5. Celebrate Achievements
Acknowledging and celebrating achievements when goals are met is essential for maintaining momentum.
Recognizing employees who contribute to waste reduction can motivate others and foster a sense of teamwork and ownership.
The Benefits of Reducing Raw Material Loss
There are numerous advantages to minimizing raw material loss, beyond the obvious cost savings.
1. Environmental Impact
Reducing wastage contributes to a lower environmental footprint for the manufacturing process.
This conservation of resources aligns with global sustainability efforts and can enhance a company’s reputation as an environmentally conscious organization.
2. Cost Efficiency
Less waste means that fewer materials are needed to produce the same amount of product, leading to cost savings.
These savings can then be reinvested into other areas of the business, such as research and development or marketing.
3. Improved Product Quality
By focusing on reducing raw material loss, manufacturers often implement stricter quality control measures, leading to higher quality products.
Excellent product quality can enhance customer satisfaction and lead to increased sales and brand loyalty.
4. Competitive Advantage
Companies that manage to reduce raw material waste effectively can gain a competitive edge over their rivals.
Being able to produce more efficiently can offer an advantage in pricing and market positioning.
Conclusion
In conclusion, reducing raw material loss is a critical component of modern manufacturing management.
By employing robust management methods, setting realistic goals, and embracing a culture of continuous improvement, manufacturers can significantly decrease waste.
In doing so, they not only reduce costs but also contribute positively to environmental sustainability, improve product quality, and gain a competitive market advantage.
Making raw material loss reduction a priority is not simply an operational necessity but a strategic move that aligns with broader business and environmental goals.
資料ダウンロード
QCD調達購買管理クラウド「newji」は、調達購買部門で必要なQCD管理全てを備えた、現場特化型兼クラウド型の今世紀最高の購買管理システムとなります。
ユーザー登録
調達購買業務の効率化だけでなく、システムを導入することで、コスト削減や製品・資材のステータス可視化のほか、属人化していた購買情報の共有化による内部不正防止や統制にも役立ちます。
NEWJI DX
製造業に特化したデジタルトランスフォーメーション(DX)の実現を目指す請負開発型のコンサルティングサービスです。AI、iPaaS、および先端の技術を駆使して、製造プロセスの効率化、業務効率化、チームワーク強化、コスト削減、品質向上を実現します。このサービスは、製造業の課題を深く理解し、それに対する最適なデジタルソリューションを提供することで、企業が持続的な成長とイノベーションを達成できるようサポートします。
オンライン講座
製造業、主に購買・調達部門にお勤めの方々に向けた情報を配信しております。
新任の方やベテランの方、管理職を対象とした幅広いコンテンツをご用意しております。
お問い合わせ
コストダウンが利益に直結する術だと理解していても、なかなか前に進めることができない状況。そんな時は、newjiのコストダウン自動化機能で大きく利益貢献しよう!
(Β版非公開)