- お役立ち記事
- Regulator and servo with gain designed using optimal control theory
月間77,185名の
製造業ご担当者様が閲覧しています*
*2025年2月28日現在のGoogle Analyticsのデータより
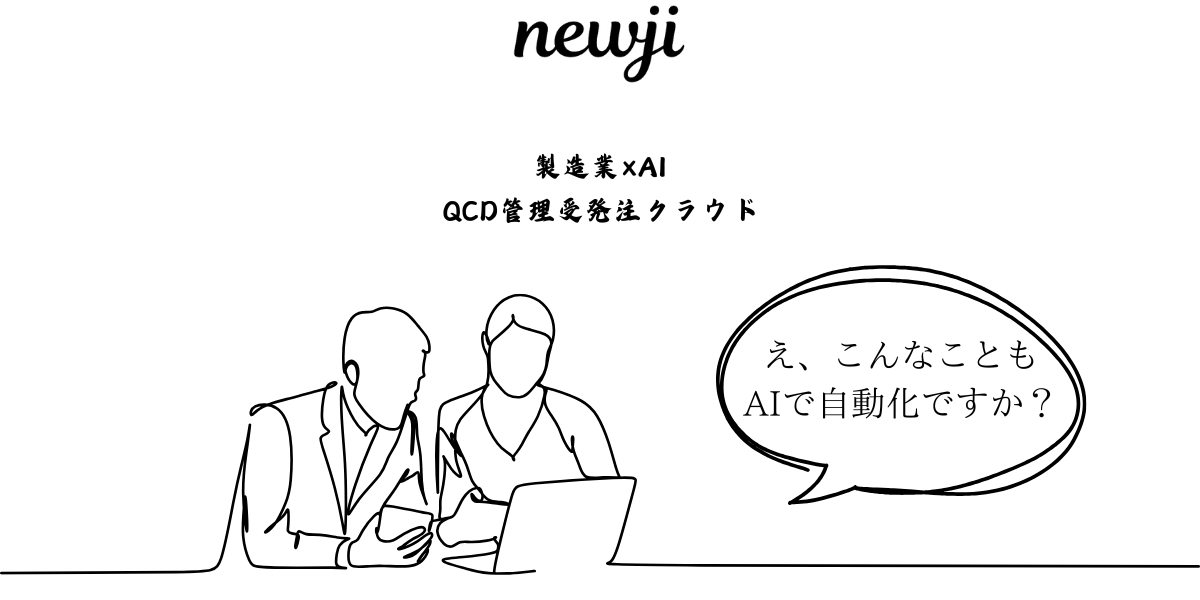
Regulator and servo with gain designed using optimal control theory
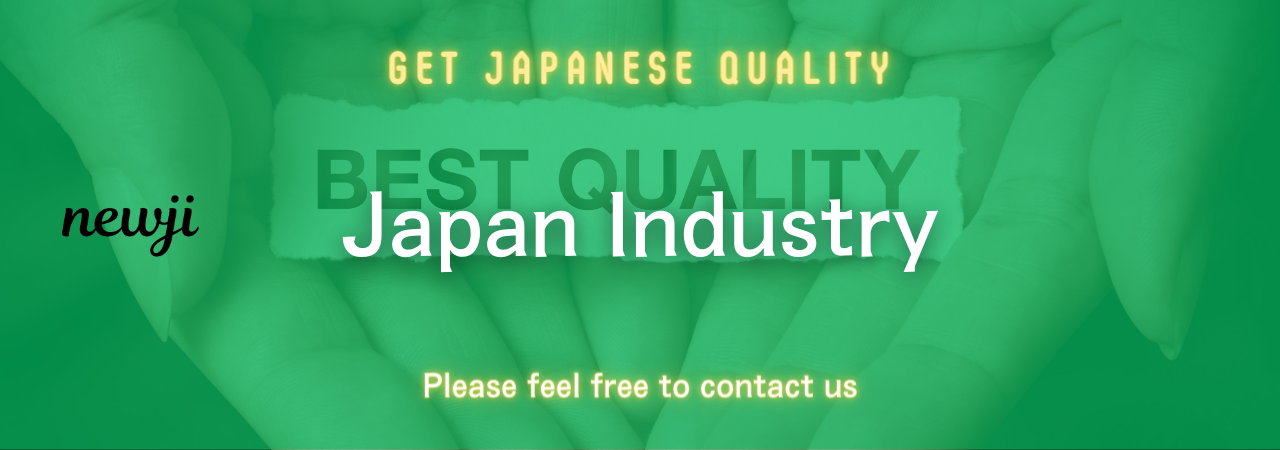
目次
Introduction to Optimal Control Theory
Optimal control theory is a multidisciplinary branch of applied mathematics that deals with the problem of finding a control policy for a dynamical system over a period of time.
This control policy aims to optimize a performance criterion, which can encompass various objectives such as minimizing energy consumption, maximizing efficiency, or enhancing stability.
The concept is widely used in engineering and economics to develop efficient and cost-effective systems.
In the realm of engineering, particularly in designing regulators and servos, optimal control theory plays a crucial role.
Understanding Regulators and Servos
What are Regulators?
Regulators are devices or systems designed to maintain a particular variable within a specified range no matter the variations in external conditions or disturbances.
They are commonly used in various applications such as voltage regulation in electrical systems, speed control in engines, and temperature control in HVAC systems.
What are Servos?
Servo systems, usually referred to as servomechanisms, are automated control systems designed to use error-sensing feedback to correct the performance of a mechanism.
They are crucial in robotics, manufacturing equipment, and other industries where precision control of movement or force is required.
Link Between Optimal Control Theory and Regulators and Servos
Optimal control theory provides a rigorous mathematical framework to design controllers that make regulators and servos more efficient and robust.
By defining a system’s dynamics and constraints, one can use optimal control techniques to derive control laws that maximize or minimize a particular performance criterion.
This ensures that the regulator or servo operates efficiently while adhering to any constraints imposed by the system or the environment.
Designing Regulators Using Optimal Control Theory
Setting Up the Objective Function
The first step in designing regulators using optimal control theory is to delineate the objective function.
Typically, the goal is to minimize a cost function that represents the difference between the desired output and the actual output of the system.
This could be integral square error for maintaining process stability, or energy consumption for energy-efficient operations.
Formulating the System Dynamics
Next, the dynamic equations representing the system need to be formulated.
These equations express how the system reacts to control inputs and disturbances over time.
A model of the system is typically created using differential equations or state-space representations.
Applying the LQR Method
One popular methodology used in the optimal control design of regulators is the Linear Quadratic Regulator (LQR).
LQR aims to minimize a quadratic cost function, which consists of terms representing both the deviation of the system state from the desired state and the control effort required.
By solving the LQR problem, one can obtain a gain matrix, which is used to derive the control policy.
Designing Servos Using Optimal Control Theory
Formulating Performance Criteria
For servo systems, the primary performance criteria often include response speed, accuracy, and stability.
The desired performance is usually captured in a cost function, similar to how it’s done for regulators.
Modeling Dynamics with Constraints
Just like regulators, servos are modeled using system dynamics, but with additional attention to actuator constraints and non-linearities that are more prevalent in servo problems.
Dynamic modeling helps predict how the servo responds under various conditions.
Gain Scheduling and Robust Control
In many cases, simple linear control methods such as LQR may not suffice for servo systems, especially if they exhibit non-linear behavior over their range of operation.
In such scenarios, gain scheduling or robust control techniques are employed within the framework of optimal control theory to address these complexities.
Advantages of Using Optimal Control Theory
Optimal control theory provides several advantages in the design of regulators and servos:
1. **Enhanced Performance** – By optimizing the control policy, systems can achieve superior performance compared to conventional control strategies.
2. **Predictive Accuracy** – Optimal control takes into account future system behavior, allowing controllers to act not only based on current states but anticipated changes.
3. **Energy Efficiency** – Through careful formulation of cost functions, systems can be designed to operate under optimal energy usage.
4. **Stability** – Optimal control designs account for variabilities and uncertainties, enhancing the overall robustness of the systems.
Challenges and Considerations
While optimal control theory offers significant benefits, there are challenges to consider:
– **Complexity in Mathematical Formulation** – The process requires the formulation of detailed mathematical models, which can be resource-intensive.
– **Computational Demand** – Solving optimal control problems can be computationally challenging, especially for high-order or non-linear systems.
– **Real-world Constraints** – Implementing control policies derived from optimal control theory can face difficulties due to real-world unpredictability and hardware limitations.
Conclusion
Optimal control theory serves as a powerful tool in designing high-performance and efficient regulators and servos.
By structuring the problem using dynamic models, objective functions, and performance criteria, engineers can develop control laws that significantly enhance system performance.
However, the application of optimal control must carefully consider computational and real-world constraints to ensure practicality and effectiveness.
資料ダウンロード
QCD管理受発注クラウド「newji」は、受発注部門で必要なQCD管理全てを備えた、現場特化型兼クラウド型の今世紀最高の受発注管理システムとなります。
ユーザー登録
受発注業務の効率化だけでなく、システムを導入することで、コスト削減や製品・資材のステータス可視化のほか、属人化していた受発注情報の共有化による内部不正防止や統制にも役立ちます。
NEWJI DX
製造業に特化したデジタルトランスフォーメーション(DX)の実現を目指す請負開発型のコンサルティングサービスです。AI、iPaaS、および先端の技術を駆使して、製造プロセスの効率化、業務効率化、チームワーク強化、コスト削減、品質向上を実現します。このサービスは、製造業の課題を深く理解し、それに対する最適なデジタルソリューションを提供することで、企業が持続的な成長とイノベーションを達成できるようサポートします。
製造業ニュース解説
製造業、主に購買・調達部門にお勤めの方々に向けた情報を配信しております。
新任の方やベテランの方、管理職を対象とした幅広いコンテンツをご用意しております。
お問い合わせ
コストダウンが利益に直結する術だと理解していても、なかなか前に進めることができない状況。そんな時は、newjiのコストダウン自動化機能で大きく利益貢献しよう!
(β版非公開)