- お役立ち記事
- Relationship between molding pressure and powdering rate of pellet feed
月間76,176名の
製造業ご担当者様が閲覧しています*
*2025年3月31日現在のGoogle Analyticsのデータより
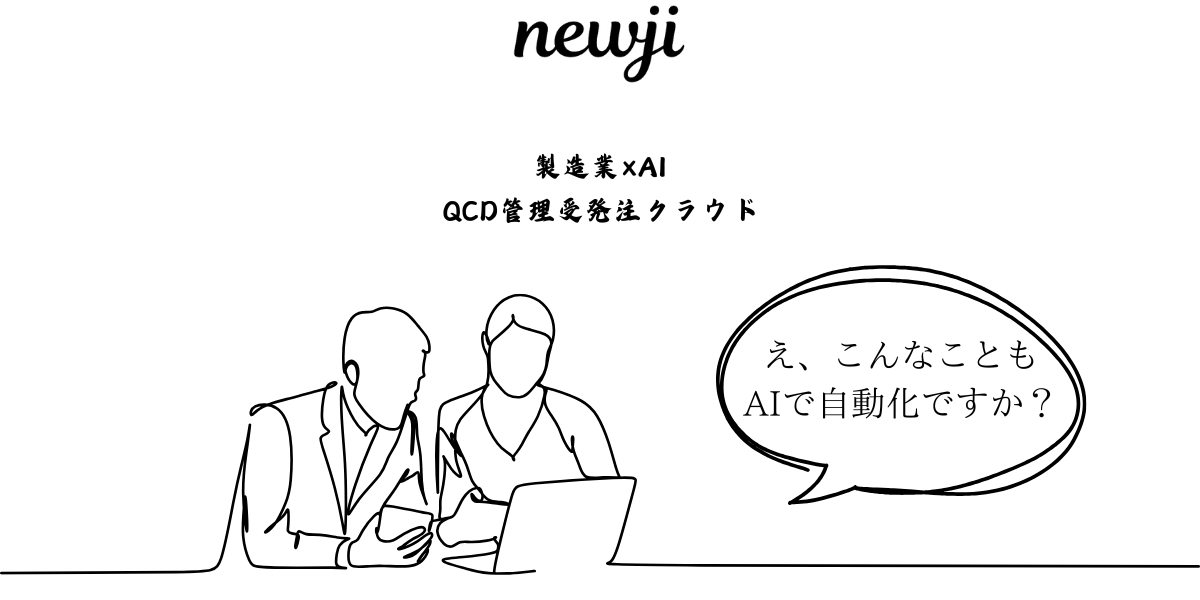
Relationship between molding pressure and powdering rate of pellet feed
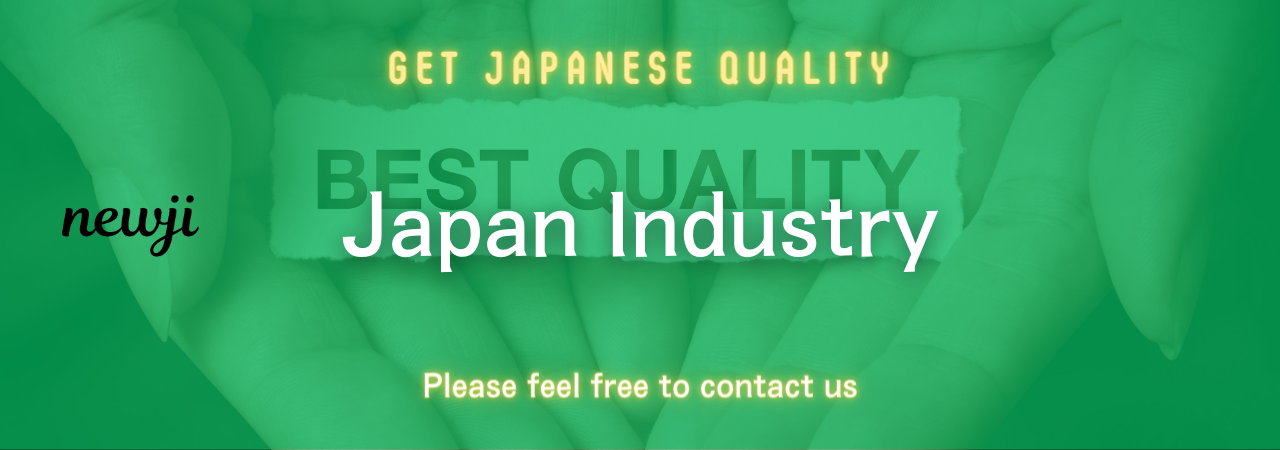
目次
Understanding the Basics of Pellet Feed
Pellet feed is a type of animal feed that is gaining popularity due to its numerous benefits.
It is a compact, versatile, and nutritious option for feeding livestock and pets alike.
Pellet feed is made by compressing powdered ingredients into small, dense pellets using a process called pelleting.
This method helps in improving the digestibility and nutrient value of the feed, making it a preferred choice for animal nutrition.
Importance of Molding Pressure in Pellet Feed Production
One of the key factors in the production of pellet feed is molding pressure.
Molding pressure is the force applied to the powdered ingredients to shape them into pellets during the pelleting process.
The right molding pressure ensures that the pellets are dense and durable, providing optimal nutrition to animals.
Molding pressure affects several aspects of pellet quality, including density, durability, and the rate at which they break down, also known as powdering.
The Concept of Powdering Rate and Its Significance
The powdering rate refers to the tendency of pellet feed to break down into smaller particles or powder.
A lower powdering rate is desirable as it ensures the pellets remain intact longer, thus providing consistent nutrition to the animals.
High powdering rates can lead to wastage and nutritional imbalances, as the powdered form may not be consumed efficiently by animals.
Factors Influencing Powdering Rate
Several factors can influence the powdering rate of pellet feed, including ingredient composition, moisture content, and molding pressure.
Understanding these factors is essential to produce high-quality pellet feed that minimizes powdering and maximizes nutritional delivery.
How Molding Pressure Affects Powdering Rate
The Relationship Between Molding Pressure and Pellet Durability
Molding pressure plays a pivotal role in determining the durability of pellet feed.
Higher molding pressure typically results in pellets that are denser and more robust, reducing the likelihood of breakage and hence, a lower powdering rate.
This is because increased pressure forces the particles of the powdered feed closer together, enhancing the binding effect and leading to stronger pellets.
The Balance Between Molding Pressure and Pellet Quality
While higher molding pressure can decrease the powdering rate, it is crucial to maintain a balance.
Excessively high pressure can lead to other issues, such as overheating of the feed ingredients, which might negatively affect the nutritional content.
It can also increase the energy consumption during production, raising costs.
Therefore, achieving an optimal molding pressure is key to producing high-quality pellet feed.
Measuring and Optimizing Molding Pressure
To optimize molding pressure, it is essential first to measure it accurately during the pelleting process.
Advanced machinery and tools are used to monitor and adjust molding pressure in real time, ensuring that the pellet feed produced meets desired quality standards.
Techniques for Optimizing Molding Pressure
1. **Trial and Error Method**: This traditional approach involves adjusting the molding pressure incrementally and testing the resulting pellet quality until the optimal level is found.
2. **Analytical Methods**: Using data and analytics, manufacturers can predict the ideal molding pressure settings based on the ingredients and desired pellet characteristics.
3. **Modern Technology**: The use of smart sensors and automated systems in pellet production lines allows for precise control over molding pressure, ensuring consistent quality.
Impact of Ingredient Composition on Molding Pressure
The composition of the feed ingredients significantly impacts how molding pressure affects the powdering rate.
Different ingredients have varying binding properties, which interact differently with applied pressure.
Role of Binding Agents
Binding agents are often added to the feed mix to enhance pellet durability and reduce powdering.
These agents can work synergistically with molding pressure to improve pellet quality.
Conclusion
Understanding the relationship between molding pressure and powdering rate is crucial for producing high-quality pellet feed.
By carefully controlling molding pressure and considering other factors like ingredient composition and moisture content, manufacturers can optimize pellet quality.
Achieving the right balance ensures that the feed remains nutritious, durable, and economical, ultimately benefiting both producers and consumers.
As the demand for pelleted feed continues to grow in the agriculture and pet food industries, continuous research and technological advancements will play a vital role in refining production processes.
This will lead to improved pellet quality and better nutritional outcomes for animals.
資料ダウンロード
QCD管理受発注クラウド「newji」は、受発注部門で必要なQCD管理全てを備えた、現場特化型兼クラウド型の今世紀最高の受発注管理システムとなります。
ユーザー登録
受発注業務の効率化だけでなく、システムを導入することで、コスト削減や製品・資材のステータス可視化のほか、属人化していた受発注情報の共有化による内部不正防止や統制にも役立ちます。
NEWJI DX
製造業に特化したデジタルトランスフォーメーション(DX)の実現を目指す請負開発型のコンサルティングサービスです。AI、iPaaS、および先端の技術を駆使して、製造プロセスの効率化、業務効率化、チームワーク強化、コスト削減、品質向上を実現します。このサービスは、製造業の課題を深く理解し、それに対する最適なデジタルソリューションを提供することで、企業が持続的な成長とイノベーションを達成できるようサポートします。
製造業ニュース解説
製造業、主に購買・調達部門にお勤めの方々に向けた情報を配信しております。
新任の方やベテランの方、管理職を対象とした幅広いコンテンツをご用意しております。
お問い合わせ
コストダウンが利益に直結する術だと理解していても、なかなか前に進めることができない状況。そんな時は、newjiのコストダウン自動化機能で大きく利益貢献しよう!
(β版非公開)