- お役立ち記事
- Relationship between occurrence of chatter vibration and processing conditions
Relationship between occurrence of chatter vibration and processing conditions
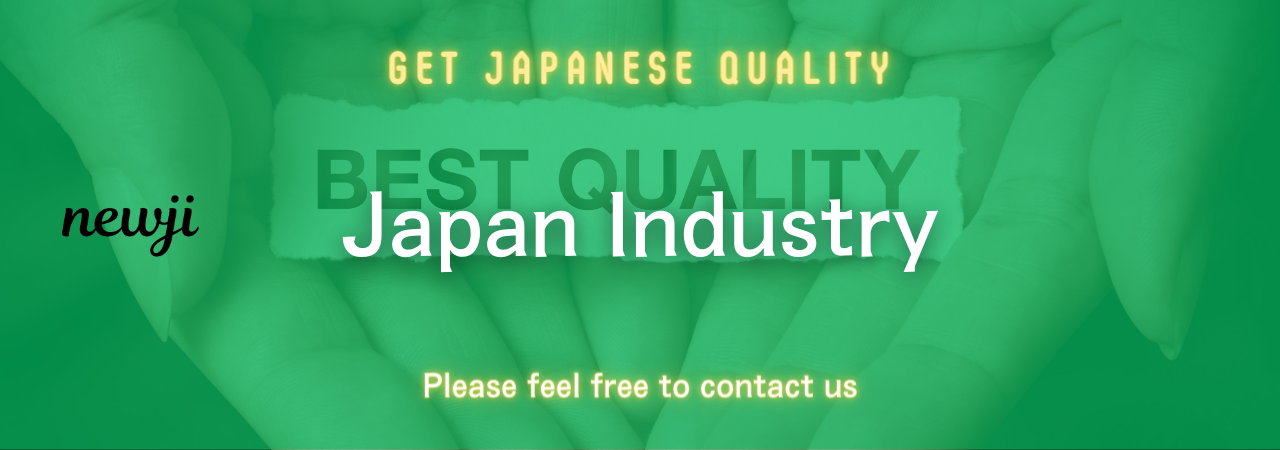
目次
Understanding Chatter Vibration
Chatter vibration is a common phenomenon in machining processes, often leading to undesirable outcomes such as poor surface finish, reduced tool life, and increased noise.
It is essential to comprehend the underlying causes and how processing conditions affect its occurrence to mitigate its impact effectively.
In simple terms, chatter is a self-excited vibration characterized by a repetitive, disruptive sound or trembling during machining operations.
Chatter vibration can occur in various machining processes, including milling, turning, drilling, and grinding.
The fundamental mechanism behind chatter is the dynamic instability that arises from the interaction between the tool and the workpiece.
This interaction leads to fluctuating cutting forces, which, in turn, cause the tool or workpiece to vibrate at specific frequencies.
The resulting vibration can be classified into different types, including primary chatter, secondary chatter, and regenerative chatter, each with distinct characteristics and effects.
The Role of Processing Conditions
The occurrence of chatter vibration is closely linked to processing conditions.
These conditions play a crucial role in either mitigating or exacerbating the likelihood and severity of chatter.
Several factors need to be considered, including cutting speed, feed rate, depth of cut, tool geometry, and material properties.
Cutting Speed and Chatter
Cutting speed significantly influences the occurrence of chatter vibration.
When the cutting speed is too low, the material removal process becomes less efficient, increasing the likelihood of chatter.
Conversely, excessively high cutting speeds can also lead to instability and chatter due to the higher energy and force interactions between the tool and workpiece.
To strike a balance, it is crucial to select an optimal cutting speed that minimizes vibration while maximizing material removal rates.
Manufacturers often refer to machinability charts or conduct experiments to determine the ideal cutting speed for specific materials and tools.
Feed Rate and Chatter
The feed rate, or the distance the tool advances per revolution or pass, is another critical factor in chatter occurrence.
Higher feed rates can lead to increased cutting forces and vibration, potentially resulting in chatter.
Conversely, lower feed rates may not provide enough cutting force to achieve a smooth operation, thus increasing the risk of chatter.
Adjusting the feed rate is important for achieving stability during machining.
Manufacturers often start with conservative feed rates and gradually increase them while monitoring for signs of chatter, ensuring an optimal balance between productivity and vibration control.
Depth of Cut and Chatter
The depth of cut refers to the thickness of the material being removed in a single pass.
Deeper cuts require more energy and force, increasing the likelihood of chatter.
Shallow cuts, on the other hand, may not induce sufficient cutting forces to prevent vibration.
Optimizing the depth of cut involves considering the relationships between material properties, tool capabilities, and desired outcomes.
Gradual changes in depth during machining can help identify the limits before chatter becomes problematic, enabling operators to find the ideal parameters for stability.
Tool Geometry and Material Properties
The geometry of the cutting tool significantly affects chatter behavior.
Factors such as tool shape, rake angle, relief angle, and edge sharpness all contribute to how the tool interacts with the workpiece, influencing the dynamic stability of the system.
Material properties of both the workpiece and the tool also play a vital role.
Materials with high toughness and elasticity are more prone to chatter due to their ability to absorb and dissipate energy.
Optimizing tool-material combinations is essential in minimizing chatter occurrence.
Measuring and Detecting Chatter
Detecting and measuring chatter is critical for mitigating its effects during machining.
Several techniques and technologies are available to operators for identifying and quantifying chatter in real-time.
Acoustic Emission Sensors
Acoustic emission sensors are a popular choice for chatter detection.
These sensors capture the high-frequency sounds and vibrations generated during machining and convert them into signals that can be analyzed by computer systems.
Real-time monitoring through acoustic emission sensors enables operators to detect the early signs of chatter and make necessary process adjustments.
Vibration Sensors
Vibration sensors, such as accelerometers, are another effective tool for measuring chatter.
These sensors attach to either the tool or the workpiece and capture vibration data during machining operations.
Through advanced algorithms, the collected data can reveal vibration patterns, allowing operators to identify chatter-prone conditions.
Visual Inspection
While less technologically advanced than other methods, visual inspection remains an important technique.
Operators can detect chatter visually by inspecting the workpiece surface for characteristic patterns, marks, or roughness caused by vibration.
Though less immediate than real-time sensors, visual inspection is valuable for assessing finished products and adjusting future machining parameters accordingly.
Prevention and Control Strategies
Preventing chatter is crucial for maintaining machining quality, reducing tool wear, and ensuring better productivity.
Employing various control strategies can help minimize the risk and impact of chatter.
Utilizing Damping Techniques
Damping is a common approach to reduce vibration in machining.
It involves using materials or devices that absorb and dissipate vibrational energy.
Operators can employ passive damping techniques, such as tuned mass dampers, or active systems that adaptively modulate damping in real-time, offering improved stability during operations.
Optimizing Tool Selection
Selecting the appropriate tool material and geometry for specific machining tasks is vital in reducing chatter risk.
Modern simulations and modeling techniques allow manufacturers to tailor tool designs based on material properties and desired results, creating an optimized cutting environment.
Advanced Control Algorithms
Technological advancements have led to the development of sophisticated control algorithms that adaptively adjust cutting parameters in response to real-time data, minimizing chatter risk.
These algorithms rely on machine learning and data analytics to optimize processing conditions, offering enhanced control over the machining process.
Concluding Remarks
The relationship between chatter vibration and processing conditions is intricate and multifaceted.
Understanding the interplay of various factors influences successful machining operations by minimizing vibration instability.
By carefully considering cutting speed, feed rate, depth of cut, tool geometry, and material properties, operators can navigate the challenges posed by chatter, achieving improved productivity and superior results.
With advancements in detection technologies and control strategies, manufacturers have powerful tools to mitigate chatter’s impact and enhance machining quality.
Equipped with this knowledge, engineers and operators can create a stable machining environment, leading to higher efficiency and longer tool life.
資料ダウンロード
QCD調達購買管理クラウド「newji」は、調達購買部門で必要なQCD管理全てを備えた、現場特化型兼クラウド型の今世紀最高の購買管理システムとなります。
ユーザー登録
調達購買業務の効率化だけでなく、システムを導入することで、コスト削減や製品・資材のステータス可視化のほか、属人化していた購買情報の共有化による内部不正防止や統制にも役立ちます。
NEWJI DX
製造業に特化したデジタルトランスフォーメーション(DX)の実現を目指す請負開発型のコンサルティングサービスです。AI、iPaaS、および先端の技術を駆使して、製造プロセスの効率化、業務効率化、チームワーク強化、コスト削減、品質向上を実現します。このサービスは、製造業の課題を深く理解し、それに対する最適なデジタルソリューションを提供することで、企業が持続的な成長とイノベーションを達成できるようサポートします。
オンライン講座
製造業、主に購買・調達部門にお勤めの方々に向けた情報を配信しております。
新任の方やベテランの方、管理職を対象とした幅広いコンテンツをご用意しております。
お問い合わせ
コストダウンが利益に直結する術だと理解していても、なかなか前に進めることができない状況。そんな時は、newjiのコストダウン自動化機能で大きく利益貢献しよう!
(Β版非公開)