- お役立ち記事
- Reliability Design Basics for Mechanical Systems and Key Countermeasures
月間76,176名の
製造業ご担当者様が閲覧しています*
*2025年3月31日現在のGoogle Analyticsのデータより
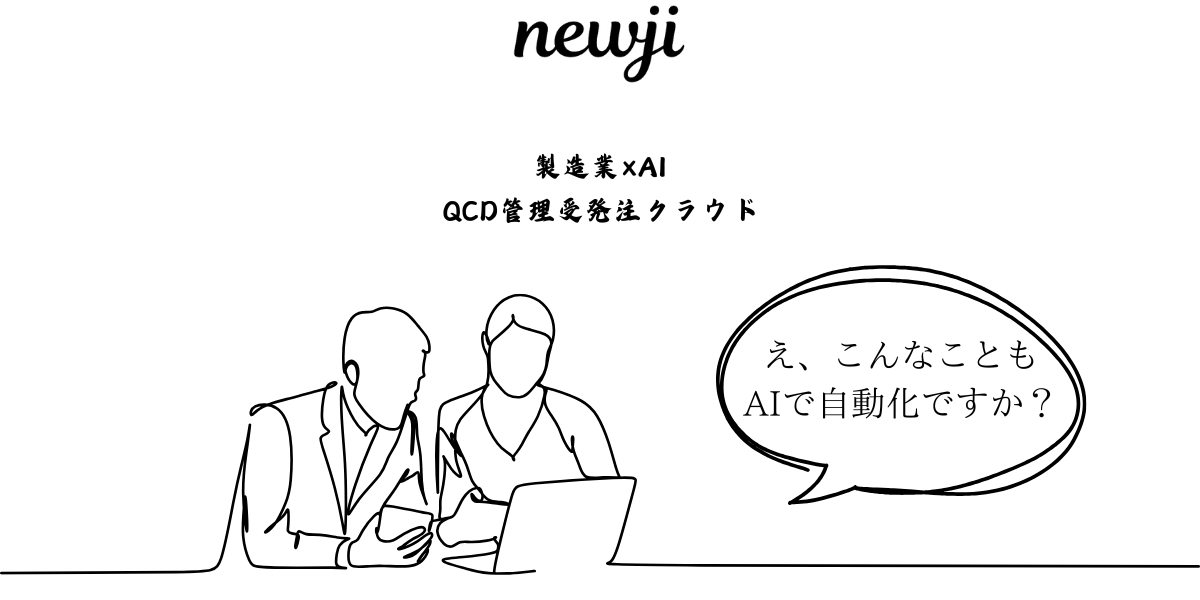
Reliability Design Basics for Mechanical Systems and Key Countermeasures
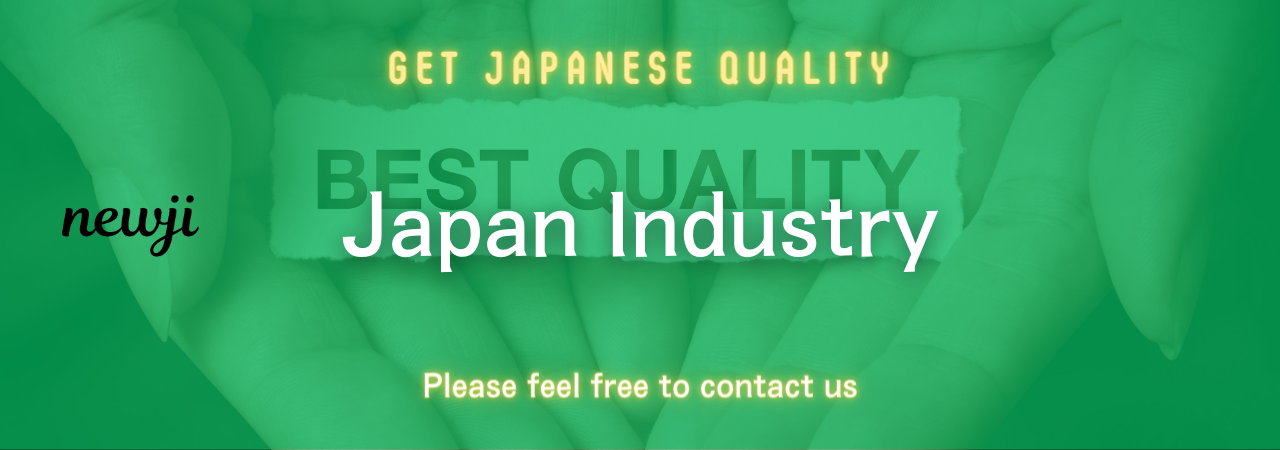
目次
Understanding Reliability Design
Reliability design in mechanical systems is a critical aspect that ensures these systems perform their intended functions consistently over time.
It involves predicting, managing, and reducing the likelihood of failures, thereby improving system dependability.
Mechanical systems can be found in everyday life, ranging from simple household appliances to complex industrial machinery.
The aim is to create a system that is not only high-performing but also durable and efficient.
The Importance of Reliability Design
The main objective of reliability design is to minimize the risk of unexpected failures.
Mechanical systems with poor reliability can lead to significant downtime, costly repairs, and even safety hazards.
By focusing on reliability, companies can save money in the long run due to reduced maintenance costs, fewer spare parts, and less unscheduled downtime.
Moreover, reliable products lead to higher customer satisfaction and reflect positively on a brand’s reputation.
Key Principles of Reliability Design
Understanding the central principles of reliability design is crucial for effective implementation.
These principles serve as the backbone for developing reliable mechanical systems.
Load Capacity and Strength
A fundamental aspect of reliability design is ensuring that components can withstand the loads they will encounter during their operation.
This involves selecting appropriate materials and geometries that can handle stress, force, and environmental factors without failure.
Redundancy
Incorporating redundancy into mechanical designs can prevent complete system failures.
By including duplicate components or pathways, the system can continue functioning even if one part fails.
This is especially important in critical applications where downtime or failure could have severe consequences.
Predictive Maintenance
Adopting predictive maintenance strategies can extend the lifespan and reliability of mechanical systems.
This involves monitoring systems to detect anomalies or wear before they lead to significant issues.
Techniques like vibration analysis, thermal imaging, and oil analysis are often employed to predict potential failures.
Steps to Achieving Reliable Mechanical Systems
Creating reliable mechanical systems is a systematic process that involves several essential steps.
Design Simulation and Analysis
Before physical prototypes are built, engineers use simulations to test and refine their designs.
Computer-aided design (CAD) software helps model the systems and simulate real-world conditions.
This allows for the identification and rectification of potential weaknesses or failure points early in the design phase.
Material Selection
Choosing the right materials is vital for ensuring durability and reliability.
Engineers must consider factors such as temperature tolerance, corrosion resistance, and strength.
Advanced materials, like composites or alloys, might offer enhanced performance but at a higher cost, necessitating a balance between reliability and budget.
Prototyping and Testing
Building prototypes and subjecting them to rigorous testing ensures that the design functions as intended under real-world conditions.
This phase helps uncover any unforeseen issues and provides an opportunity to make necessary adjustments.
Iterative testing and refinement are key to enhancing system reliability.
Quality Control
A robust quality control process during manufacturing can prevent defects and ensure consistency across products.
Implementing standardized procedures and inspections throughout production reduces variability, leading to more reliable systems.
Regular Maintenance
Once deployed, regular maintenance is crucial to sustaining system reliability.
Organizations should establish a maintenance schedule tailored to the specific needs of the mechanical system.
Regular maintenance activities include cleaning, lubricating, inspecting, and replacing worn or damaged parts.
Technological Innovations Enhancing Reliability
Modern technologies play a significant role in enhancing the reliability of mechanical systems.
Internet of Things (IoT)
IoT technology allows mechanical systems to be monitored continuously in real time.
Sensors connected through the internet collect data on performance, which can be analyzed to predict failures before they occur.
This proactive approach enhances reliability by allowing timely interventions.
Artificial Intelligence (AI)
AI algorithms assist in analyzing complex data from mechanical systems, identifying patterns, and making predictive maintenance recommendations.
This technology can process vast amounts of data quickly, leading to more accurate and efficient reliability assessments.
Advanced Manufacturing Techniques
Techniques like 3D printing and CNC machining allow for precise component fabrication, reducing the likelihood of errors and defects.
These technologies enable the creation of complex geometries and custom parts that enhance system performance and reliability.
Addressing Reliability Challenges
While reliability design offers numerous benefits, it also presents several challenges that must be addressed.
Cost Considerations
Achieving high reliability often requires additional resources, which can increase initial costs.
Organizations must weigh these upfront expenses against long-term savings from reduced maintenance and downtime.
Complexity Management
As mechanical systems grow more complex, ensuring reliability becomes more challenging.
Engineers must manage this complexity while maintaining reliability, requiring careful planning and integration of systems engineering principles.
Balancing Innovation and Reliability
Pursuing innovative designs can sometimes conflict with reliability objectives.
Striking a balance between cutting-edge features and proven reliability requires careful evaluation and compromise.
Conclusion
Reliability design is foundational to the success and sustainability of mechanical systems.
By adhering to key principles and leveraging modern technologies, engineers can develop systems that meet high reliability standards.
While challenges exist, the benefits of investing in reliability design—such as improved system performance, customer satisfaction, and cost savings—make it a vital component of any engineering strategy.
Continuous advancements in technology and methodology promise to further enhance the reliability of future mechanical systems.
資料ダウンロード
QCD管理受発注クラウド「newji」は、受発注部門で必要なQCD管理全てを備えた、現場特化型兼クラウド型の今世紀最高の受発注管理システムとなります。
ユーザー登録
受発注業務の効率化だけでなく、システムを導入することで、コスト削減や製品・資材のステータス可視化のほか、属人化していた受発注情報の共有化による内部不正防止や統制にも役立ちます。
NEWJI DX
製造業に特化したデジタルトランスフォーメーション(DX)の実現を目指す請負開発型のコンサルティングサービスです。AI、iPaaS、および先端の技術を駆使して、製造プロセスの効率化、業務効率化、チームワーク強化、コスト削減、品質向上を実現します。このサービスは、製造業の課題を深く理解し、それに対する最適なデジタルソリューションを提供することで、企業が持続的な成長とイノベーションを達成できるようサポートします。
製造業ニュース解説
製造業、主に購買・調達部門にお勤めの方々に向けた情報を配信しております。
新任の方やベテランの方、管理職を対象とした幅広いコンテンツをご用意しております。
お問い合わせ
コストダウンが利益に直結する術だと理解していても、なかなか前に進めることができない状況。そんな時は、newjiのコストダウン自動化機能で大きく利益貢献しよう!
(β版非公開)