- お役立ち記事
- Reliability engineer training course: Market failure mechanisms of electronic equipment and testing and analysis techniques
月間76,176名の
製造業ご担当者様が閲覧しています*
*2025年3月31日現在のGoogle Analyticsのデータより
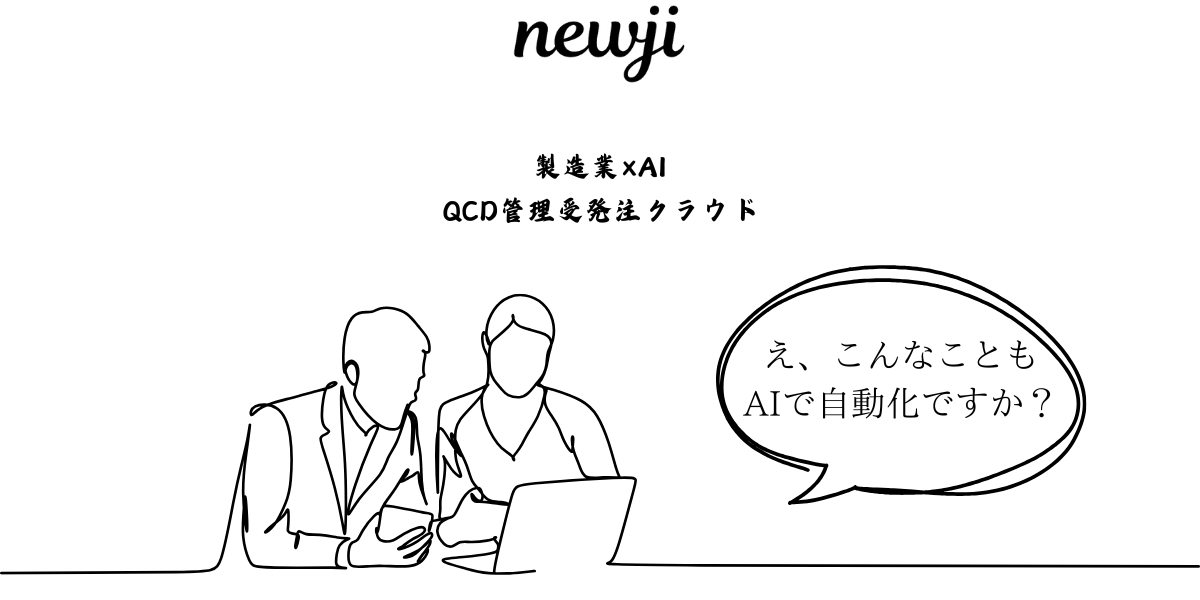
Reliability engineer training course: Market failure mechanisms of electronic equipment and testing and analysis techniques
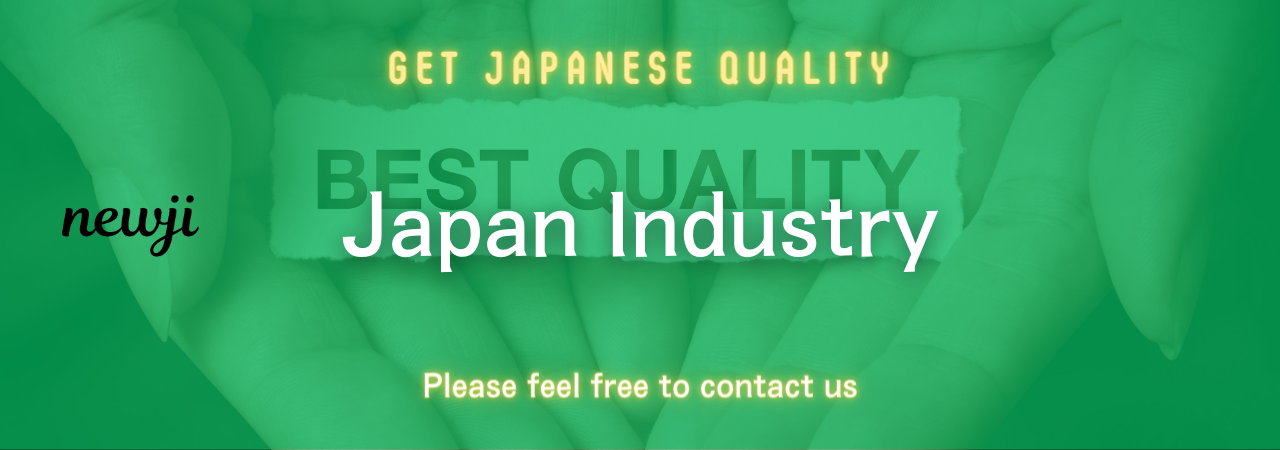
目次
Understanding Market Failure Mechanisms
Reliability engineering is a critical discipline that ensures electronic equipment functions as expected under specified conditions.
Market failure mechanisms are particular strategies and occurrences that can degrade the reliability of electronic products.
These mechanisms can manifest due to various reasons, including flawed designs, material defects, and improper testing procedures.
When electronic equipment fails, it becomes crucial to understand the mechanism behind the failure.
Failures can originate from thermal, electrical, mechanical, chemical, and environmental stressors.
A reliability engineer must identify these sources to prevent such occurrences in the future.
One primary cause of market failure is the thermal reliability concern.
Electronic components often produce heat, and without proper design and heat dissipation techniques, components like transistors and capacitors may overheat and fail.
Thermal failures can cause solder joints to crack or components to malfunction.
To mitigate these risks, reliability engineering principles encourage the use of heat sinks, thermal interface materials, and efficient circuit design.
Additionally, the use of effective thermal simulation tools can predict heat behavior and allow engineers to redesign systems for maximum reliability.
Importance of Testing and Analysis Techniques
Testing and analysis are integral aspects of reliability engineering.
Without them, identifying potential points of failure within electronic equipment would be virtually impossible.
Testing allows engineers to simulate real-life scenarios and evaluate how well the equipment continues to operate.
Several testing techniques are employed in reliability engineering, such as Highly Accelerated Life Testing (HALT) and Highly Accelerated Stress Screening (HASS).
HALT tests take electronic components to their physical limits to understand potential failure points.
Meanwhile, HASS focuses on screening out early-life failures in a production process, ensuring consistent quality.
Moreover, statistical analysis techniques such as Failure Mode and Effects Analysis (FMEA) are crucial.
FMEA identifies possible failures within a system, their causes, and their effects, helping engineers prioritize which areas need immediate attention.
Analytical tools like Weibull analysis also assist engineers in predicting system reliability and understanding life data of electronic components.
Such techniques enable engineers to understand the lifespan and reliability tendencies, ensuring that corrective measures can be employed if necessary.
Case Studies: Learning from Past Failures
Looking at past failures can provide valuable insights into the design and testing processes.
For example, the infamous case of the smartphone with an exploding battery highlights the necessity of stringent quality checks and robust testing procedures.
In this instance, the battery’s failure was due to insufficient space for the chemical reactions occurring inside, leading to thermal runaway.
Such failures emphasize the need for comprehensive testing, robust design practices, and thorough attention to material choices.
Another case involved a consumer electronics company that experienced widespread device failures because of defective capacitors.
The capacitors, sourced at a lower cost, had impurities that led to leakage and subsequent failure.
This teaches the importance of evaluating suppliers and ensuring that even cost-saving measures do not compromise reliability.
Future Trends in Reliability Engineering
As technology continues to evolve, so do the methods and strategies in reliability engineering.
One emerging trend is the integration of artificial intelligence (AI) and machine learning in reliability testing.
AI can process vast amounts of data quickly, identifying patterns and potential failure points that were previously difficult to detect.
Another trend is the increasing focus on sustainability.
Reliability engineering is aligning itself with green initiatives, ensuring that products are not only reliable but also environmentally friendly.
This includes developing biodegradable materials and reducing waste through enhanced reliability and longevity of products.
Additionally, with the growth of IoT devices, reliability engineers are tasked with ensuring connectivity and resilience in increasingly complex systems.
This involves new testing paradigms and the adaptation of current methodologies to cater to vast networks of connected devices.
Enhancing Skills Through Training
To succeed as a reliability engineer, continuous training and education are imperative.
Training courses focused on market failure mechanisms and testing techniques empower engineers with essential knowledge and skills.
Courses often involve hands-on laboratory work, where engineers can apply theoretical knowledge to practical situations.
They are also exposed to real-world problems, case studies, and the latest technological advancements.
Additionally, workshops and seminars featuring industry experts can provide valuable insights into current challenges and effective solutions used in the field.
Conclusion
Understanding market failure mechanisms and employing effective testing and analysis techniques are central to reliability engineering.
They ensure that electronic equipment meets quality standards and performs reliably over its intended lifecycle.
As technology evolves, reliability engineers must stay abreast of new developments and continuously update their skills through training and research.
By doing so, they contribute significantly to the production of durable, reliable, and sustainable electronic products.
資料ダウンロード
QCD管理受発注クラウド「newji」は、受発注部門で必要なQCD管理全てを備えた、現場特化型兼クラウド型の今世紀最高の受発注管理システムとなります。
ユーザー登録
受発注業務の効率化だけでなく、システムを導入することで、コスト削減や製品・資材のステータス可視化のほか、属人化していた受発注情報の共有化による内部不正防止や統制にも役立ちます。
NEWJI DX
製造業に特化したデジタルトランスフォーメーション(DX)の実現を目指す請負開発型のコンサルティングサービスです。AI、iPaaS、および先端の技術を駆使して、製造プロセスの効率化、業務効率化、チームワーク強化、コスト削減、品質向上を実現します。このサービスは、製造業の課題を深く理解し、それに対する最適なデジタルソリューションを提供することで、企業が持続的な成長とイノベーションを達成できるようサポートします。
製造業ニュース解説
製造業、主に購買・調達部門にお勤めの方々に向けた情報を配信しております。
新任の方やベテランの方、管理職を対象とした幅広いコンテンツをご用意しております。
お問い合わせ
コストダウンが利益に直結する術だと理解していても、なかなか前に進めることができない状況。そんな時は、newjiのコストダウン自動化機能で大きく利益貢献しよう!
(β版非公開)