- お役立ち記事
- Reliability engineer training course: Techniques for building reliability of electronic devices and parts from design and development to manufacturing and investigating causes of market failures
Reliability engineer training course: Techniques for building reliability of electronic devices and parts from design and development to manufacturing and investigating causes of market failures
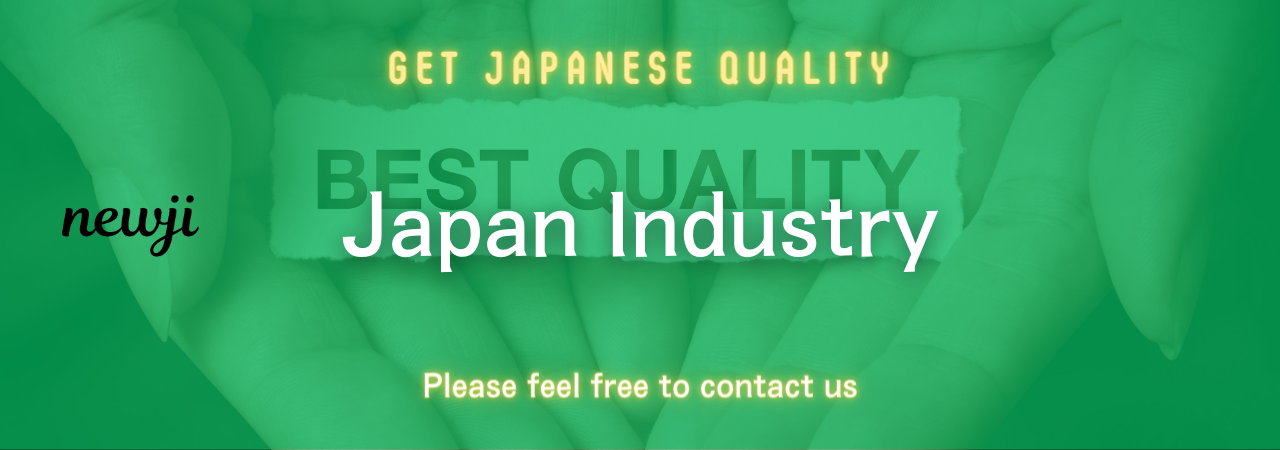
目次
Understanding the Role of a Reliability Engineer
Reliability engineers play a crucial role in the life cycle of electronic devices and components.
Their primary objective is to ensure that products function consistently and without failure throughout their expected life span.
From the initial design phase through development, manufacturing, and beyond, reliability engineers apply specialized techniques to anticipate potential issues and enhance product durability.
Organizations today are increasingly investing in reliability engineering training courses to equip their engineering teams with the necessary skills and knowledge.
These courses are designed to teach engineers how to boost the reliability of electronic devices by implementing structured methodologies and best practices.
Techniques for Enhancing Reliability in Design and Development
The design and development phases are critical stages in building the reliability of electronic devices.
During these stages, engineers utilize various strategies to foresee and mitigate potential failures.
Some of the key techniques include:
Design for Reliability (DfR)
Design for Reliability is a proactive approach where reliability is integrated into the design process from the very beginning.
By prioritizing reliability at the onset, engineers can consider potential risks and address them before they evolve into problems.
This might include selecting robust materials, designing redundancy into systems, and simplifying complex components to reduce potential failure points.
Failure Modes and Effects Analysis (FMEA)
FMEA is a systematic process used to identify potential failure modes within a system, assess their impact, and prioritize the risks they pose.
Reliability engineers use this analysis to pinpoint where failures are most likely to occur and develop strategies to prevent them.
The insights gained from FMEA can lead to more informed design choices and improved overall reliability of the product.
Environmental Testing
Environmental testing simulates the conditions a product will face during its lifetime, including variations in temperature, humidity, and vibration.
By exposing prototypes to these conditions, engineers can predict how real-world stresses will impact the product and make necessary adjustments.
This type of testing helps ensure that devices will perform reliably in diverse environments, thus minimizing the likelihood of market failures.
The Importance of Reliability in Manufacturing
Once the design and development phases are complete, the focus shifts to manufacturing.
Reliability engineers are vital in maintaining the integrity of production processes to ensure that each unit meets the defined reliability criteria.
Process Optimization
Process optimization involves fine-tuning manufacturing processes to reduce variability and defects in production.
This can be achieved by employing techniques such as Six Sigma or Lean Manufacturing, which aim to improve quality and efficiency.
By optimizing processes, reliability engineers help minimize risks associated with variability and ensure consistent product reliability.
Supplier Quality Management
A product’s reliability is heavily dependent on the quality of its components and materials.
Therefore, sound supplier quality management is crucial.
Reliability engineers evaluate and select suppliers based on their ability to consistently provide high-quality materials.
They may also implement rigorous testing protocols for incoming components to prevent defects that could compromise the final product.
Reliability Testing During Production
Ongoing reliability testing during production helps ensure the product continues to meet quality standards.
This may include random sampling and stress testing of products to detect any deviations from expected performance.
By catching and addressing issues early in the manufacturing process, engineers can prevent larger problems down the line.
Investigating Causes of Market Failures
Despite best efforts in design, development, and manufacturing, products may still fail in the market.
Identifying the root causes of these failures is essential for future improvements.
Root Cause Analysis (RCA)
Root Cause Analysis is a methodical approach used to investigate failures and determine their underlying causes.
By understanding why a failure occurred, reliability engineers can develop solutions to prevent its recurrence in future products.
Common techniques used in RCA include fishbone diagrams, the 5 Whys, and fault tree analysis.
Customer Feedback and Field Data
Collecting and analyzing customer feedback and field data offers valuable insights into how products perform in real-world conditions.
Reliability engineers use this information to identify any patterns of failure and areas where product improvements are needed.
Implementing changes based on customer feedback can significantly enhance the reliability of subsequent product generations.
Continuous Improvement Initiatives
Continuous improvement is a philosophy that emphasizes the ongoing enhancement of products and processes.
Reliability engineers play a key role in fostering a culture of continuous improvement within an organization.
By consistently reviewing performance data and implementing improvements, companies can increase the reliability of their products over time.
The Value of Reliability Engineering Training
Investing in reliability engineering training is a strategic move for any company looking to enhance the durability and dependability of its products.
These training programs offer a comprehensive foundation in essential techniques and methodologies for building reliable electronic devices.
By developing a team of skilled reliability engineers, organizations can reduce the risk of market failures, improve customer satisfaction, and gain a competitive edge in the marketplace.
Ultimately, this leads to higher-quality products that better meet the needs and expectations of consumers.
With the knowledge gained through training, engineers are well-equipped to anticipate potential issues and create robust designs that stand the test of time.
資料ダウンロード
QCD調達購買管理クラウド「newji」は、調達購買部門で必要なQCD管理全てを備えた、現場特化型兼クラウド型の今世紀最高の購買管理システムとなります。
ユーザー登録
調達購買業務の効率化だけでなく、システムを導入することで、コスト削減や製品・資材のステータス可視化のほか、属人化していた購買情報の共有化による内部不正防止や統制にも役立ちます。
NEWJI DX
製造業に特化したデジタルトランスフォーメーション(DX)の実現を目指す請負開発型のコンサルティングサービスです。AI、iPaaS、および先端の技術を駆使して、製造プロセスの効率化、業務効率化、チームワーク強化、コスト削減、品質向上を実現します。このサービスは、製造業の課題を深く理解し、それに対する最適なデジタルソリューションを提供することで、企業が持続的な成長とイノベーションを達成できるようサポートします。
オンライン講座
製造業、主に購買・調達部門にお勤めの方々に向けた情報を配信しております。
新任の方やベテランの方、管理職を対象とした幅広いコンテンツをご用意しております。
お問い合わせ
コストダウンが利益に直結する術だと理解していても、なかなか前に進めることができない状況。そんな時は、newjiのコストダウン自動化機能で大きく利益貢献しよう!
(Β版非公開)