- お役立ち記事
- Reliability engineering basics and testing methods that new employees in the equipment engineering department should learn
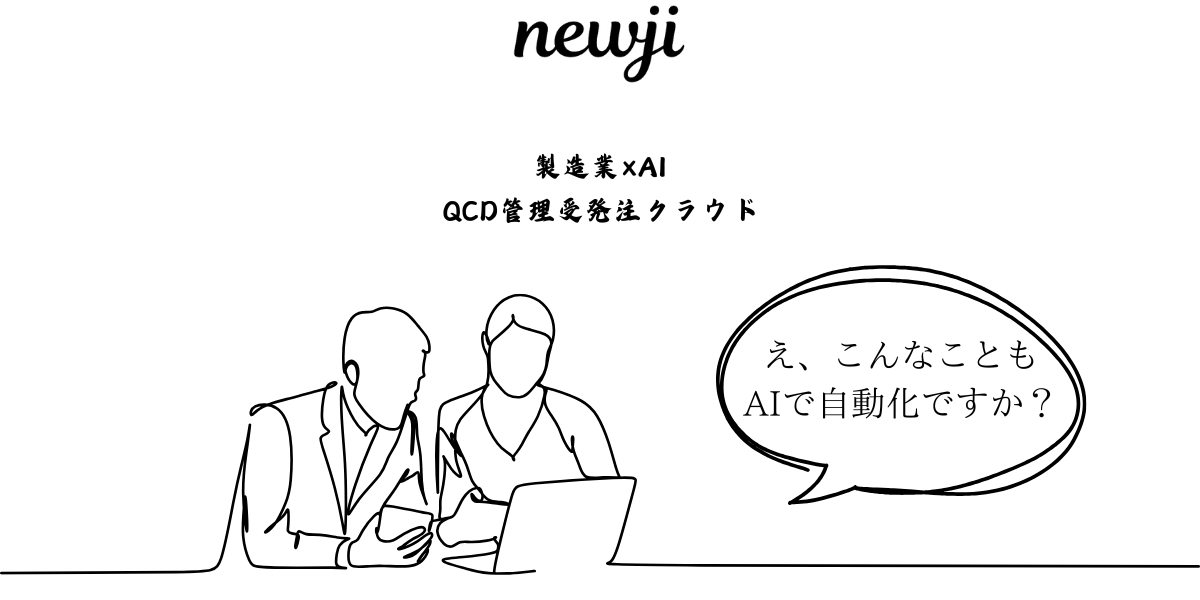
Reliability engineering basics and testing methods that new employees in the equipment engineering department should learn
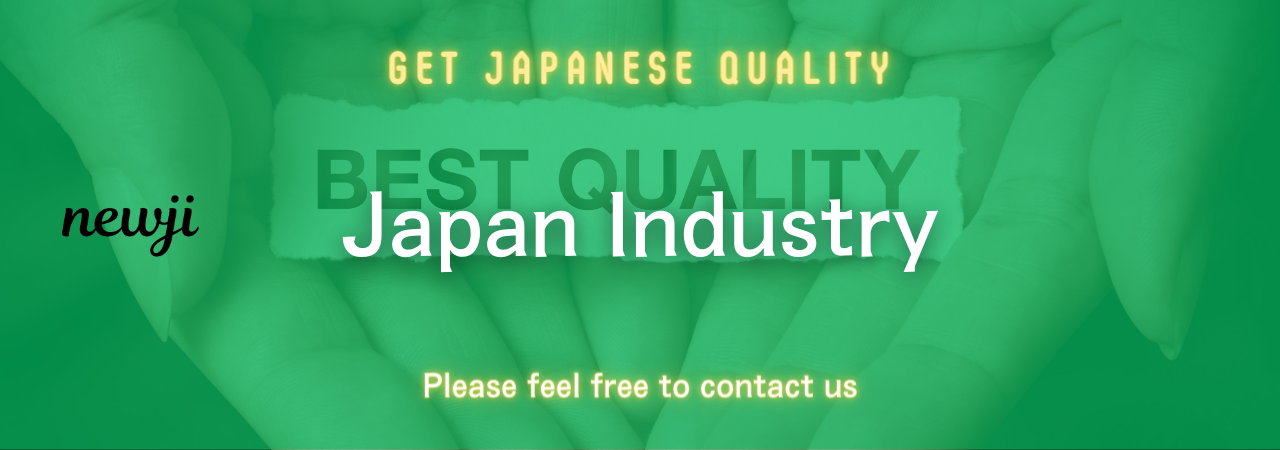
目次
What is Reliability Engineering?
Reliability engineering is a field that focuses on ensuring that systems, components, and products consistently perform their intended functions without failure over a specified period.
It is crucial in the equipment engineering department, as it helps identify potential issues that may arise over the lifespan of a product or system.
By understanding and applying reliability engineering principles, new employees can contribute to designing and maintaining equipment that is both efficient and dependable.
Reliability engineering is based on various principles and methodologies, including statistical analysis, modeling, and testing.
It aims to enhance product performance, reduce maintenance costs, and improve customer satisfaction by minimizing failures and downtime.
As new employees in the equipment engineering department, understanding these fundamentals is essential to effectively contribute to your team’s success.
Key Concepts in Reliability Engineering
To grasp reliability engineering, it is important to understand certain key concepts, including reliability, maintainability, and availability.
Reliability
Reliability refers to the probability that a system or component will perform its required function under specified conditions for a specified period.
It is often expressed as a percentage and indicates how likely a system is to function without failure.
For example, a machine with 99% reliability means that there is a 99% chance it will operate as expected for a given duration.
Achieving high reliability is a primary goal in reliability engineering, as it leads to fewer failures and higher customer satisfaction.
Maintainability
Maintainability is the ease with which a product or system can be maintained, including the ability to identify, diagnose, and repair issues.
A system with high maintainability can be quickly and efficiently restored to working condition after a failure, reducing downtime and associated costs.
To enhance maintainability, engineers often design systems with modular components, making it easier to replace or repair parts as needed.
Training new employees to understand these modular designs can help improve overall maintenance procedures and efficiency.
Availability
Availability is the measure of a system’s operational readiness, considering both its reliability and maintainability.
It is the likelihood that a system is functional and ready for use at any given time.
Availability can be improved by increasing reliability and maintainability through effective design, testing, and maintenance practices.
For example, preventive maintenance schedules and the use of high-quality components can increase system availability, ensuring it is always ready to serve its intended purpose.
Common Testing Methods in Reliability Engineering
Testing methods are critical in reliability engineering as they help identify and address potential issues before they lead to failures.
New employees should familiarize themselves with these common testing methods used to assess and improve system reliability.
Failure Modes and Effects Analysis (FMEA)
Failure Modes and Effects Analysis (FMEA) is a systematic approach to identifying and analyzing possible failure modes within a system.
It involves evaluating how failures can occur, their potential impacts, and prioritizing the risks associated with these failures.
By assessing these factors, engineers can take preemptive measures to prevent failures and improve overall system reliability.
FMEA is often used in the initial stages of product design and throughout its lifecycle, ensuring that potential issues are identified and addressed early.
New employees should learn how to perform FMEA to effectively contribute to improving equipment reliability.
Reliability Block Diagrams (RBD)
Reliability Block Diagrams (RBD) represent the functional relationships of various components within a system.
They are used to visualize the interactions between components and assess the overall system’s reliability.
By breaking down complex systems into manageable parts, RBDs help engineers identify critical components and potential failure points.
RBD is a powerful tool for analyzing and optimizing system reliability.
New employees can use RBD to gain a deeper understanding of system design and identify areas for improvement.
Environmental Testing
Environmental testing evaluates how systems and components perform under various environmental conditions, such as temperature, humidity, vibration, and pressure.
These tests help determine whether a product can withstand its intended operating environment and identify potential weaknesses.
By conducting environmental tests, engineers can ensure that components meet reliability standards and continue to perform under challenging conditions.
New employees should learn about the different types of environmental testing relevant to their industry’s equipment.
Accelerated Life Testing
Accelerated Life Testing (ALT) involves subjecting a product to extreme conditions to expedite the occurrence of failures.
By simulating prolonged use in a shorter timeframe, ALT helps engineers identify potential failure modes and predict product lifespan.
This method is valuable for identifying problems that might not be evident during routine testing.
Understanding ALT enables new employees to proactively address issues and contribute to producing more reliable equipment.
This testing method is particularly useful in industries where products are expected to operate in harsh environments.
Reliability Growth Testing
Reliability Growth Testing focuses on continuous improvement by identifying and addressing failure modes during the testing phase.
It involves iterative testing and redesigning to enhance system reliability throughout the development process.
This method promotes a proactive approach to reliability by learning from failures and making necessary adjustments.
By participating in reliability growth testing, new employees can contribute to creating more dependable systems and gain valuable insights into improving future product designs.
Implementing Reliability Engineering Principles
To effectively apply reliability engineering principles and testing methods, new employees should follow these best practices:
Understand System Requirements
To enhance equipment reliability, it is essential to clearly understand system requirements and operating conditions.
By gathering this information, employees can identify potential challenges and design systems that meet or exceed reliability expectations.
Collaborate with Cross-Functional Teams
Reliability engineering is a collaborative effort that involves working with other departments, such as design, manufacturing, and maintenance.
By fostering open communication, employees can ensure that reliability considerations are integrated into every stage of product development.
Keep Up with Industry Standards
Staying informed about industry standards and best practices is crucial for maintaining equipment reliability.
New employees should regularly update their knowledge of the latest technologies, materials, and methodologies to ensure their work aligns with current standards.
Utilize Data-Driven Insights
Data analysis is a powerful tool for identifying trends and patterns in equipment performance.
By leveraging data-driven insights, employees can make informed decisions to enhance product reliability and address potential issues before they lead to failures.
In conclusion, mastering the basics of reliability engineering and understanding common testing methods are essential skills for new employees in the equipment engineering department.
By learning and applying these concepts, new team members can contribute to designing, testing, and maintaining reliable systems that meet customer expectations.
資料ダウンロード
QCD調達購買管理クラウド「newji」は、調達購買部門で必要なQCD管理全てを備えた、現場特化型兼クラウド型の今世紀最高の購買管理システムとなります。
ユーザー登録
調達購買業務の効率化だけでなく、システムを導入することで、コスト削減や製品・資材のステータス可視化のほか、属人化していた購買情報の共有化による内部不正防止や統制にも役立ちます。
NEWJI DX
製造業に特化したデジタルトランスフォーメーション(DX)の実現を目指す請負開発型のコンサルティングサービスです。AI、iPaaS、および先端の技術を駆使して、製造プロセスの効率化、業務効率化、チームワーク強化、コスト削減、品質向上を実現します。このサービスは、製造業の課題を深く理解し、それに対する最適なデジタルソリューションを提供することで、企業が持続的な成長とイノベーションを達成できるようサポートします。
オンライン講座
製造業、主に購買・調達部門にお勤めの方々に向けた情報を配信しております。
新任の方やベテランの方、管理職を対象とした幅広いコンテンツをご用意しております。
お問い合わせ
コストダウンが利益に直結する術だと理解していても、なかなか前に進めることができない状況。そんな時は、newjiのコストダウン自動化機能で大きく利益貢献しよう!
(Β版非公開)