- お役立ち記事
- Reliability Evaluation and Failure Analysis Techniques for Power Semiconductors
月間76,176名の
製造業ご担当者様が閲覧しています*
*2025年3月31日現在のGoogle Analyticsのデータより
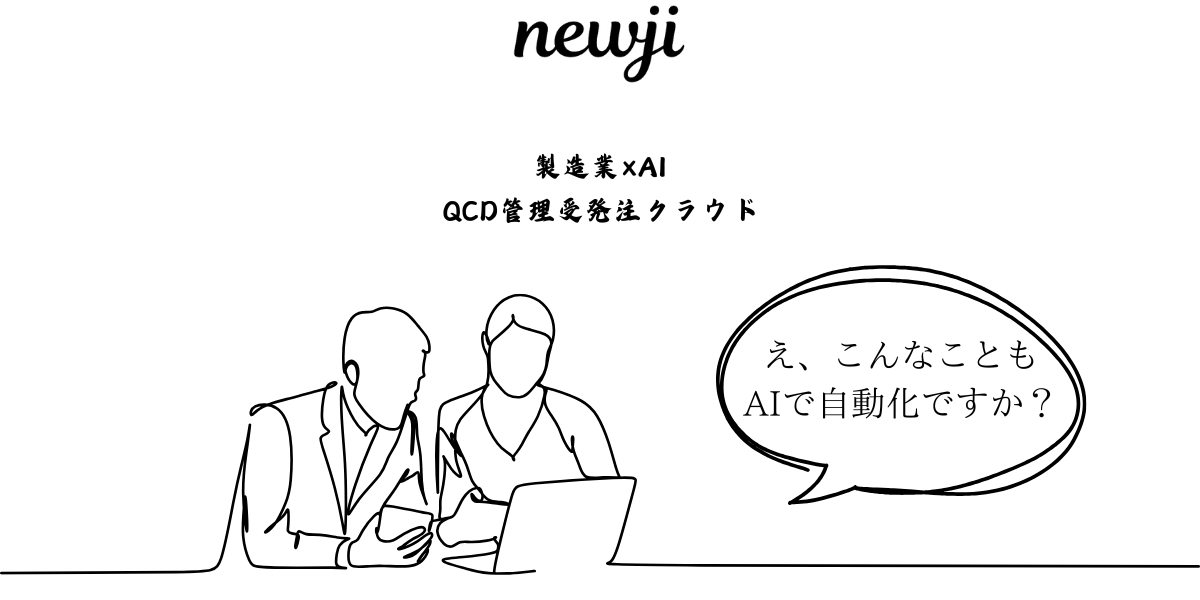
Reliability Evaluation and Failure Analysis Techniques for Power Semiconductors
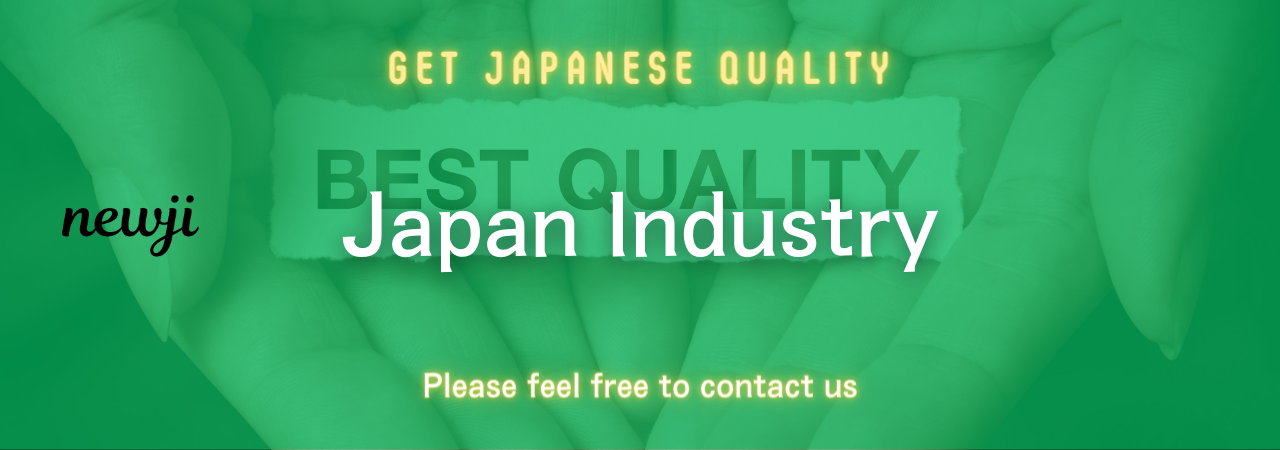
目次
Understanding Power Semiconductors
Power semiconductors are crucial components in modern electronics, responsible for managing and controlling the flow of electrical energy in devices.
These components convert high voltage and high current between different parts of an electronic circuit.
They are widely used in applications ranging from power conversion in renewable energy systems to controlling motors in industries and vehicles.
In essence, power semiconductors play a significant role in enhancing the efficiency and reliability of power electronic systems.
Understanding their operation, however, requires a deep dive into their reliability and failure mechanisms.
Importance of Reliability Evaluation
The reliability of power semiconductors is paramount because any failure can lead to significant downtime, expensive repairs, or even safety risks.
Reliability evaluation helps in predicting component behavior over time, ensuring their performance aligns with expectations.
It enables engineers to design systems that can withstand the rigors of various operational conditions.
By regularly assessing reliability, manufacturers can also improve the longevity of their products.
They can pinpoint potential failure mechanisms and apply design improvements, consequently reducing maintenance costs and enhancing customer satisfaction.
Common Failure Mechanisms
Understanding common failure mechanisms in power semiconductors is the basis for carrying out an effective reliability evaluation.
These failures can be attributed to several factors:
Thermal Stress
Power semiconductors often undergo significant thermal stress due to high power dissipation.
Repeated heating and cooling cycles can cause material degradation, leading to thermal fatigue, which is a common failure reason.
Electrical Overstress
Devices are susceptible to electrical overstress, which occurs when they are subjected to voltage or current levels beyond their design limits.
This can lead to breakdowns and, occasionally, catastrophic failures.
Material Defects
Inherent defects in materials used for power semiconductor construction can lead to operational inefficiencies and failures over time.
These defects can be introduced during the manufacturing process or manifest as a result of environmental influences.
Techniques for Reliability Evaluation
Several techniques are employed to assess the reliability of power semiconductors effectively:
Accelerated Life Testing (ALT)
Accelerated life testing involves subjecting semiconductors to elevated levels of stress to hasten the occurrence of failures.
By doing this, manufacturers can simulate long-term usage in a shorter time frame, allowing them to collect data on potential failure points efficiently.
Thermal Cycling Tests
Thermal cycling tests evaluate the component’s resistance to temperature variations.
This technique replicates the thermal stresses experienced during real-world operations, providing insights into potential thermal fatigue failures.
Failure Modes and Effects Analysis (FMEA)
FMEA is a systematic approach for identifying potential failure mechanisms and their effects on the overall system.
By probing different failure modes, engineers can prioritize those that pose the highest risk, implementing measures to prevent them.
Reliability Physics Analysis
This technique focuses on understanding the physical laws that govern the behavior and failure of power semiconductors.
It combines knowledge of material science and engineering to predict and mitigate failure mechanisms effectively.
Strategies for Failure Analysis
Once a failure is detected, the analysis comes into play to determine the root cause and strategize for future prevention:
Root Cause Analysis (RCA)
RCA involves investigating and identifying the underlying reasons for a component failure.
By understanding the root cause, manufacturers can develop targeted strategies to eliminate the cause from recurring in future designs.
Non-Destructive Testing (NDT)
NDT methods, such as X-ray or ultrasonic testing, allow engineers to inspect power semiconductors for defects without causing any damage.
This approach is invaluable for understanding internal defects that could lead to failures.
Destructive Physical Analysis (DPA)
DPA involves dismantling a failed semiconductor to conduct a thorough analysis of its physical structure and characteristics.
This method provides a comprehensive understanding of the nature of the failure, aiding improved design strategies.
Enhancing Power Semiconductor Reliability
Once the reliability evaluation and failure analysis are understood, it’s crucial to apply findings to enhance the reliability of power semiconductors:
Design Improvements
Design improvements are essential to mitigate identified weaknesses.
This includes refining the semiconductor’s design to withstand higher stress conditions and optimizing thermal management systems.
Material Selection
Choosing the right materials for semiconductor construction can significantly impact reliability.
Materials should possess adequate thermal resistance, robustness, and minimal defect rates to optimize performance.
Manufacturing Process Control
Stringent process control during manufacturing minimizes defects that could adversely affect power semiconductor reliability.
Ensuring quality at every production stage helps create more consistent and reliable components.
Conclusion
Reliability evaluation and failure analysis are indispensable in the world of power semiconductors.
By understanding common failure modes and employing rigorous evaluation techniques, manufacturers can ensure these vital components operate efficiently and safely.
Continuous improvement informed by in-depth analyses holds the key to creating robust power electronic systems that stand the test of time.
資料ダウンロード
QCD管理受発注クラウド「newji」は、受発注部門で必要なQCD管理全てを備えた、現場特化型兼クラウド型の今世紀最高の受発注管理システムとなります。
ユーザー登録
受発注業務の効率化だけでなく、システムを導入することで、コスト削減や製品・資材のステータス可視化のほか、属人化していた受発注情報の共有化による内部不正防止や統制にも役立ちます。
NEWJI DX
製造業に特化したデジタルトランスフォーメーション(DX)の実現を目指す請負開発型のコンサルティングサービスです。AI、iPaaS、および先端の技術を駆使して、製造プロセスの効率化、業務効率化、チームワーク強化、コスト削減、品質向上を実現します。このサービスは、製造業の課題を深く理解し、それに対する最適なデジタルソリューションを提供することで、企業が持続的な成長とイノベーションを達成できるようサポートします。
製造業ニュース解説
製造業、主に購買・調達部門にお勤めの方々に向けた情報を配信しております。
新任の方やベテランの方、管理職を対象とした幅広いコンテンツをご用意しております。
お問い合わせ
コストダウンが利益に直結する術だと理解していても、なかなか前に進めることができない状況。そんな時は、newjiのコストダウン自動化機能で大きく利益貢献しよう!
(β版非公開)