- お役立ち記事
- Reliability evaluation and failure analysis technology for power semiconductor products and their practical know-how
月間76,176名の
製造業ご担当者様が閲覧しています*
*2025年3月31日現在のGoogle Analyticsのデータより
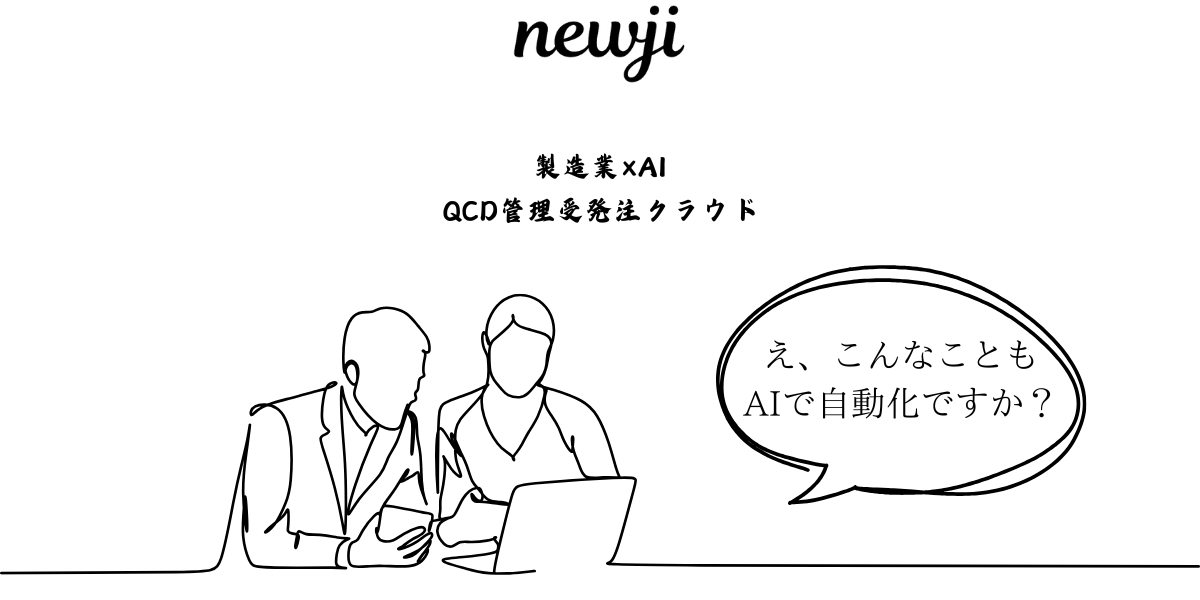
Reliability evaluation and failure analysis technology for power semiconductor products and their practical know-how
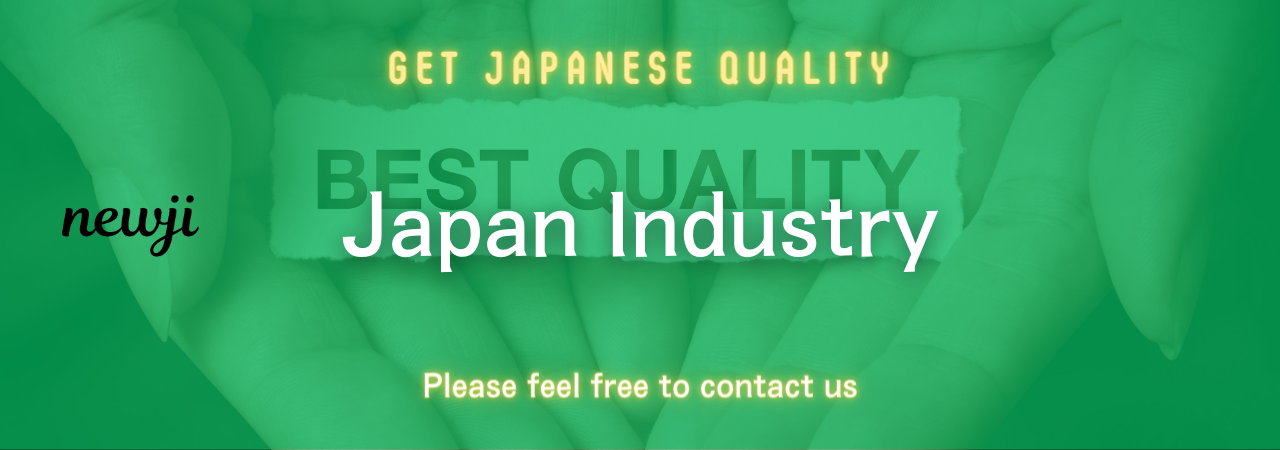
目次
Introduction to Power Semiconductor Products
Power semiconductor products are vital components in modern electronics, enabling devices to efficiently manage and convert energy.
From everyday appliances to complex industrial machinery, these components are crucial in ensuring that power is used optimally.
Thanks to power semiconductors, electricity can be controlled, converted, and transmitted with minimal loss.
Understanding their reliability and conducting failure analysis are critical aspects that help manufacturers and engineers enhance performance and lifespan.
This article will delve into the techniques and practical know-how in assessing power semiconductor products’ reliability and failure.
The Importance of Reliability in Power Semiconductors
Reliability is paramount in power semiconductors due to their widespread use in various critical applications.
Because these components play essential roles in operational systems, failures can lead to downtime, significant financial loss, or, worse, endanger human lives.
Thus, understanding and ensuring their reliability is a top priority.
Reliability evaluation provides insights into the expected performance of these components under varying conditions.
Factors Influencing Reliability
Several factors can influence the reliability of power semiconductors.
These include material quality, manufacturing processes, packaging, and assembly techniques.
External conditions, such as temperature fluctuations, vibration, humidity, and voltage stress, also significantly contribute to the reliability metrics.
By closely examining these factors, manufacturers can tailor their processes and designs to reduce potential risks.
Advanced reliability evaluation techniques also allow engineers to predict and mitigate failures before they occur.
Reliability Evaluation Techniques
Reliability evaluation is an ongoing process involving various testing methodologies to ensure the robustness of power semiconductors.
These methods focus on identifying potential failure modes and understanding the component’s behavior under stress.
Accelerated Life Testing
Accelerated Life Testing (ALT) is a primary method used to predict the lifespan of power semiconductors.
By subjecting components to controlled stress conditions, engineers can identify failure mechanisms and statistical estimations for the product’s lifetime.
This technique is pivotal in understanding how semiconductors will perform over time under normal operating conditions.
Thermal Cycling Tests
Thermal cycling tests involve subjecting power semiconductors to extreme temperature variations.
These tests help determine the components’ thermal fatigue resistance, which is critical for applications where temperature changes are frequent.
The test results offer valuable insights into the threshold limits of materials used in semiconductors.
Electrical Stress Testing
Electrical stress testing simulates conditions of electrical overload to identify potential points of failure in power semiconductors.
This type of testing is vital for determining the device’s ability to handle voltage spikes and current surges.
It aims to reveal weaknesses in the semiconductor design and suggests areas for improvement.
Failure Analysis: Understanding the Causes
Failure analysis involves investigating the reasons behind a malfunction in power semiconductor products.
This process is instrumental in improving design, manufacturing processes, and material selection.
Common Causes of Failure
The common causes for power semiconductor failures include thermal overload, mechanical stress, and electrical wear-out.
Inaccurate junction temperatures often lead to thermal overload, resulting in the weakening or breaking down of module connections.
Mechanical stress is usually caused by improper handling or vibrations, while electrical wear-out can stem from excessive current flow or voltage exposure.
Failure Analysis Techniques
To conduct a thorough failure analysis, various techniques are employed.
Non-Destructive Testing
Non-destructive testing (NDT) is crucial in failure analysis as it allows for the examination of semiconductor materials without causing damage.
Methods such as X-ray inspection and ultrasonic testing help identify internal defects and inconsistencies in power semiconductors.
Destructive Testing
Destructive testing involves physically damaging the component to examine its internal structure.
This method, while not preserving the original piece, reveals deep-seated issues within the semiconductor, such as internal electrical pathways or material inconsistencies.
Microscopic and Spectroscopic Analysis
Using a microscope and spectroscope, engineers can observe surface defects, impurities, and micro-cracks in semiconductor materials.
These analyses are integral for identifying minute causes that could lead to a significant failure.
Practical Know-How for Enhancing Reliability
Enhancing the reliability of power semiconductors starts with integrating best practices in design and manufacturing.
Robust Design Principles
Implementing robust design principles can significantly improve power semiconductor reliability.
Consider factors like conservative design margins, choosing suitable materials, and optimizing thermal management.
Investing time in the design phase can save both costs and resources later.
Process Control in Manufacturing
Strict control during the manufacturing process ensures that each step meets the highest quality standards.
Implementing advanced process control techniques can detect anomalies early, preventing defects from reaching the market.
Regular Testing and Monitoring
Continuously testing and monitoring power semiconductors post-production ensure they maintain their reliability over time.
Routine checks help identify early signs of wear and tear, allowing for timely maintenance or replacements.
Feedback Loop Systems
Establishing a feedback loop with customers helps gather data on product performance in real-world conditions.
This information is invaluable for refining designs, improving manufacturing processes, and updating reliability assessment methodologies.
Conclusion
Reliability evaluation and failure analysis are vital components in the lifecycle of power semiconductor products.
By employing various evaluation techniques and understanding the failure mechanisms, manufacturers and engineers can ensure their products meet the highest standards of reliability.
Practical know-how, including robust design, strict process control, regular testing, and customer feedback, can significantly enhance the performance and lifespan of power semiconductors, benefiting both the industry and consumers alike.
資料ダウンロード
QCD管理受発注クラウド「newji」は、受発注部門で必要なQCD管理全てを備えた、現場特化型兼クラウド型の今世紀最高の受発注管理システムとなります。
ユーザー登録
受発注業務の効率化だけでなく、システムを導入することで、コスト削減や製品・資材のステータス可視化のほか、属人化していた受発注情報の共有化による内部不正防止や統制にも役立ちます。
NEWJI DX
製造業に特化したデジタルトランスフォーメーション(DX)の実現を目指す請負開発型のコンサルティングサービスです。AI、iPaaS、および先端の技術を駆使して、製造プロセスの効率化、業務効率化、チームワーク強化、コスト削減、品質向上を実現します。このサービスは、製造業の課題を深く理解し、それに対する最適なデジタルソリューションを提供することで、企業が持続的な成長とイノベーションを達成できるようサポートします。
製造業ニュース解説
製造業、主に購買・調達部門にお勤めの方々に向けた情報を配信しております。
新任の方やベテランの方、管理職を対象とした幅広いコンテンツをご用意しております。
お問い合わせ
コストダウンが利益に直結する術だと理解していても、なかなか前に進めることができない状況。そんな時は、newjiのコストダウン自動化機能で大きく利益貢献しよう!
(β版非公開)