- お役立ち記事
- Reliability evaluation and optimal selection of parts to ensure quality during procurement and purchase of electronic parts
Reliability evaluation and optimal selection of parts to ensure quality during procurement and purchase of electronic parts
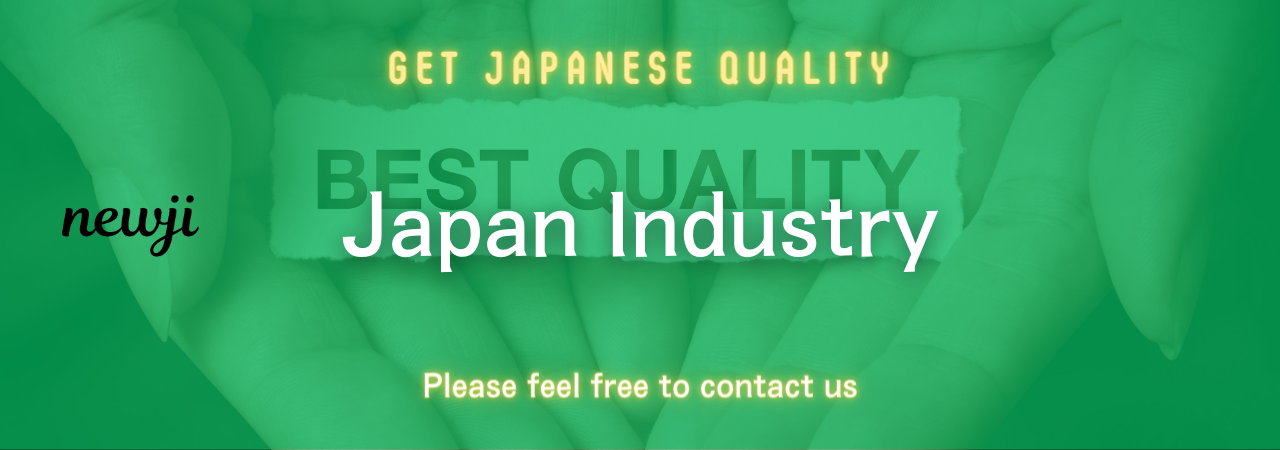
目次
Understanding Reliability in Electronic Parts
When procuring electronic parts, ensuring reliability is crucial to avoid failures and maintain quality in the final product.
Reliability in electronic components refers to the ability of a part to perform its required functions under stated conditions for a specified period.
Reliability can impact product quality, lifespan, and overall performance.
The initial step in ensuring reliability is to understand the specific requirements of the application.
Different electronic components serve different purposes and understanding these will inform the required specifications.
For example, components used in a high-temperature environment may require a higher temperature tolerance.
The Importance of Reliable Parts
Reliable electronic parts are essential for several reasons.
Firstly, they reduce the risk of product failure, which can result in costly repairs and dissatisfied customers.
Secondly, reliable parts increase the product’s lifespan, ensuring long-term customer satisfaction and reducing the frequency of replacements.
Finally, high reliability minimizes the likelihood of safety hazards, which can arise from component failures.
Evaluating Supplier Reliability
A key part of procurement is evaluating and selecting suppliers who can provide reliable electronic parts.
This involves thorough research and consideration of various factors.
Supplier Quality System
Understanding a supplier’s quality management system is crucial.
Suppliers with certified quality systems, such as ISO 9001, are likely to have processes in place that ensure the consistency and reliability of their parts.
This certification demonstrates their commitment to maintaining high standards.
Track Record and Reputation
Investigating a supplier’s track record and reputation can provide insight into their reliability.
Look for reviews, testimonials, and case studies that demonstrate past performance.
A supplier with a positive long-term reputation is more likely to supply reliable components.
Testing and Validation
Evaluate whether the supplier performs comprehensive testing and validation on their parts.
Suppliers who invest in testing processes are likely to offer more reliable products.
These tests can include stress testing, lifecycle testing, and environmental testing.
Implementing Reliability Evaluation Methods
To assess the reliability of electronic parts effectively, several evaluation methods can be implemented.
Failure Mode and Effects Analysis (FMEA)
FMEA is a systematic approach used to identify potential failures in electronic parts and their potential effects.
By recognizing and addressing these issues before procurement, the likelihood of component failure can be reduced.
Reliability Prediction
Reliability prediction involves using statistical models and historical data to estimate a component’s lifespan and performance.
By predicting potential failures, adjustments can be made in the selection process to choose more reliable components.
Accelerated Life Testing (ALT)
ALT is a method where components are subjected to stress conditions to simulate their lifespan in a short period.
This testing can identify weak points in a component’s design or material, helping to choose parts that will perform reliably under normal conditions.
Optimal Selection of Electronic Parts
The selection of electronic parts is a balancing act between cost, performance, and reliability.
An optimal selection process involves a strategic approach to ensure quality and dependability.
Performance Specifications
Begin with the performance specifications required for the application.
Identify components that meet these requirements to ensure the product performs efficiently.
Cost vs. Quality Considerations
While cost is always a consideration, it should not come at the expense of quality.
Choosing the lowest-cost component could result in unreliable performance and higher long-term costs due to repairs and replacements.
A cost-benefit analysis can help in making decisions that balance cost and quality.
Supply Chain Collaboration
Work closely with suppliers to ensure mutual understanding of requirements and expectations.
Engage in detailed discussions about their capabilities and capacities.
This collaboration can foster a more reliable supply chain and help resolve issues more efficiently.
Challenges in Ensuring Reliability
Despite best efforts, there are challenges that can arise in ensuring the reliability of electronic parts.
Rapid Technological Changes
The fast pace of technological advances can make it difficult to maintain consistent reliability.
New materials and designs may introduce unforeseen reliability issues that were not present in previous generations.
Counterfeit Components
The proliferation of counterfeit electronic parts is a significant challenge.
These parts can appear identical to genuine parts but often do not meet the same reliability standards.
To combat this, it is essential to source components from trusted suppliers with verifiable supply chains.
Conclusion
Reliability in electronic parts procurement is critical to ensuring quality and performance.
By evaluating suppliers, implementing thorough evaluation methods, and making strategic component selections, reliability can be optimized.
While challenges exist, proactive strategies can help ensure reliable parts are a cornerstone of your product development process.
資料ダウンロード
QCD調達購買管理クラウド「newji」は、調達購買部門で必要なQCD管理全てを備えた、現場特化型兼クラウド型の今世紀最高の購買管理システムとなります。
ユーザー登録
調達購買業務の効率化だけでなく、システムを導入することで、コスト削減や製品・資材のステータス可視化のほか、属人化していた購買情報の共有化による内部不正防止や統制にも役立ちます。
NEWJI DX
製造業に特化したデジタルトランスフォーメーション(DX)の実現を目指す請負開発型のコンサルティングサービスです。AI、iPaaS、および先端の技術を駆使して、製造プロセスの効率化、業務効率化、チームワーク強化、コスト削減、品質向上を実現します。このサービスは、製造業の課題を深く理解し、それに対する最適なデジタルソリューションを提供することで、企業が持続的な成長とイノベーションを達成できるようサポートします。
オンライン講座
製造業、主に購買・調達部門にお勤めの方々に向けた情報を配信しております。
新任の方やベテランの方、管理職を対象とした幅広いコンテンツをご用意しております。
お問い合わせ
コストダウンが利益に直結する術だと理解していても、なかなか前に進めることができない状況。そんな時は、newjiのコストダウン自動化機能で大きく利益貢献しよう!
(Β版非公開)