- お役立ち記事
- Reliability evaluation methods to keep in mind when selecting suppliers around the world
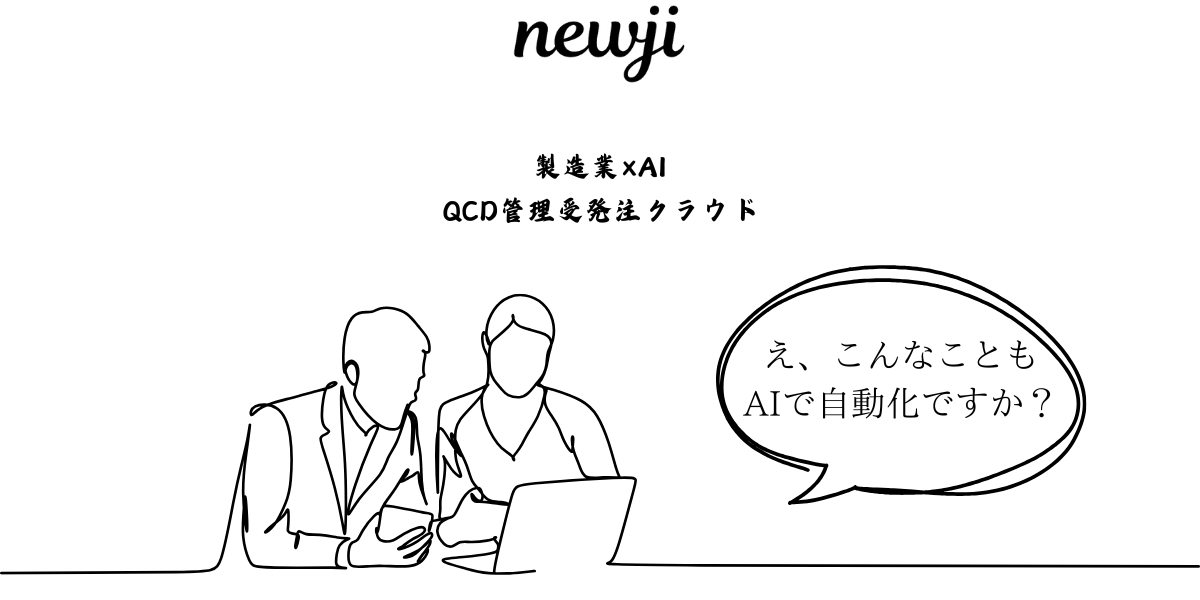
Reliability evaluation methods to keep in mind when selecting suppliers around the world
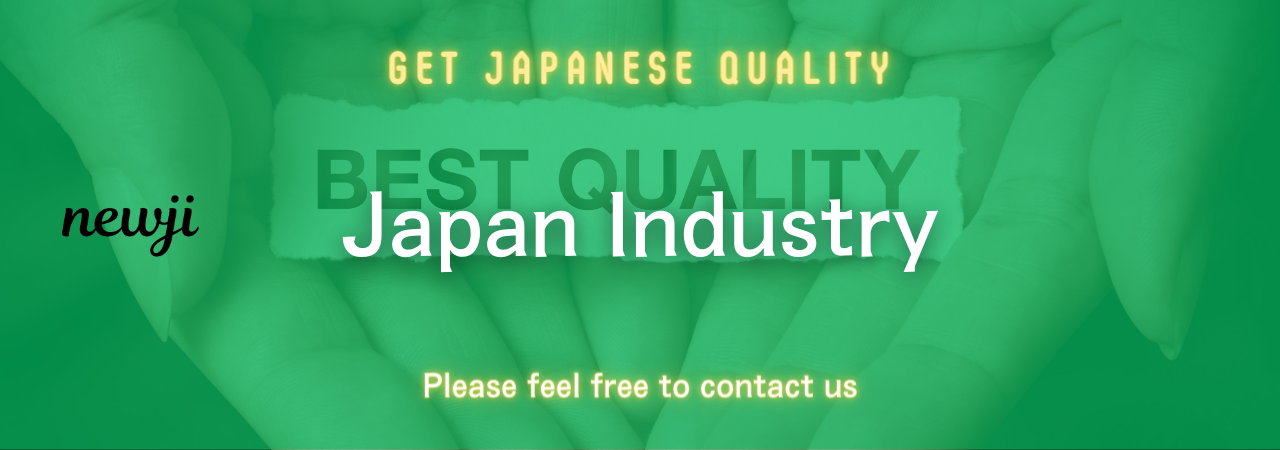
目次
Introduction to Supplier Reliability
In today’s global marketplace, businesses often rely on suppliers from different parts of the world to ensure seamless operations.
Choosing the right supplier is crucial because it affects product quality, delivery timelines, and, ultimately, customer satisfaction.
One of the most critical factors to look into is the supplier’s reliability.
By evaluating supplier reliability, companies can mitigate risks, optimize supply chain operations, and sustain their competitive edge.
Understanding Supplier Reliability
Supplier reliability refers to the consistent ability of a supplier to meet contractual obligations in terms of product quality, delivery timing, and customer service.
It ensures that there are no disruptions in the supply chain, allowing businesses to maintain smooth operations.
Reliable suppliers help in minimizing lead times, controlling costs, and providing a steady flow of products or raw materials.
Evaluating reliability requires a comprehensive approach, considering various factors such as quality, timeliness, communication, and performance history.
Importance of Evaluating Supplier Reliability
Evaluating supplier reliability is essential for reducing risks associated with supply chain disruptions, such as delays, inferior product quality, and financial losses.
Reliable suppliers contribute to a brand’s reputation by consistently meeting quality and delivery standards.
This reliability translates into better customer satisfaction and retention.
Moreover, an effective evaluation assists in making strategic decisions regarding inventory management and procurement strategies for improved business operations.
Key Reliability Evaluation Methods
1. Performance History Analysis
Examining a supplier’s performance history is a fundamental step in evaluating reliability.
Businesses can request records of past projects, including delivery timelines, quality assessments, and incident reports.
Analyzing historical data helps in understanding how frequently a supplier has met commitments and how they handled past challenges.
It gives insights into their ability to maintain consistent performance over time.
2. Quality Assessment
Quality is a core component of supplier reliability.
Conducting quality assessments involves evaluating the supplier’s processes, certifications, and product standards.
Businesses can request samples or conduct on-site audits to verify that the supplier meets their quality requirements.
Additionally, references from other clients help in gaining an understanding of the supplier’s commitment to quality.
3. Financial Stability
Financial stability is indicative of a supplier’s ability to sustain operations and meet obligations without experiencing disruptions.
Analyzing financial statements, credit ratings, and liquidity ratios enables businesses to assess whether the supplier can handle large orders and continue operations during market fluctuations.
Financially stable suppliers are less likely to default on contracts, ensuring consistent delivery and quality.
4. Delivery Performance Metrics
Timely delivery is crucial for maintaining supply chain efficiency.
Evaluating delivery performance metrics involves analyzing on-time delivery rates, lead times, and flexible handling of urgent requests.
Suppliers with a track record of timely deliveries demonstrate reliability in managing logistics and adapting to business needs.
Setting clear expectations and establishing penalties for late deliveries can further ensure consistent performance.
5. Communication and Responsiveness
Effective communication is pivotal in maintaining a healthy buyer-supplier relationship.
Assessing a supplier’s ability to communicate clearly and respond promptly to inquiries is essential.
Reliable suppliers maintain open lines of communication, keep clients informed of potential delays or issues, and promptly address concerns.
Regular communication helps in building a trustworthy partnership and smoothens any discrepancies promptly.
6. Technological Capabilities
In evaluating reliability, technological capabilities should also be considered.
Suppliers equipped with advanced technologies can enhance production efficiency, product quality, and delivery speed.
They are often better at adopting innovative solutions, optimizing supply chain operations, and minimizing costs.
Being aware of a supplier’s technological prowess allows businesses to anticipate their ability to meet current and future demands effectively.
Factors Influencing Supplier Reliability
Geographical Location
A supplier’s geographical location plays a vital role in reliability.
Proximity is beneficial for reducing shipment times, logistic costs, and potential transit risks.
However, with adequate planning and contingency measures, distant suppliers can also provide reliable services.
Understanding the supply routes and potential geopolitical or environmental risks will help in assessing a supplier’s location-related reliability.
Supplier’s Industry Reputation
A supplier’s industry reputation acts as a summary of its reliability and performance.
Researching industry reviews, customer feedback, and reputational surveys provides insights into their credibility.
A positive reputation often indicates a commitment to quality and professionalism in dealings, reinforcing confidence in their reliability.
Partnership and Cultural Fit
Building a successful long-term relationship requires assessing the partnership and cultural fit with a supplier.
Shared values, business ethics, and operational approaches can lead to smooth collaborations.
Suppliers who align with the company’s culture are more likely to provide customized solutions, adapt to changes, and maintain reliability.
Conclusion
Reliability evaluation is indispensable when selecting suppliers from around the world.
A diligent evaluation process focusing on performance history, quality, financial stability, delivery metrics, communication, and technology ensures the selection of dependable suppliers.
Such assessments support companies in minimizing supply chain risks, ensuring product consistency, and enhancing overall success.
By considering geographical factors, industry reputation, and cultural fit, businesses can establish reliable, long-term partnerships crucial for their growth and sustainability.
資料ダウンロード
QCD調達購買管理クラウド「newji」は、調達購買部門で必要なQCD管理全てを備えた、現場特化型兼クラウド型の今世紀最高の購買管理システムとなります。
ユーザー登録
調達購買業務の効率化だけでなく、システムを導入することで、コスト削減や製品・資材のステータス可視化のほか、属人化していた購買情報の共有化による内部不正防止や統制にも役立ちます。
NEWJI DX
製造業に特化したデジタルトランスフォーメーション(DX)の実現を目指す請負開発型のコンサルティングサービスです。AI、iPaaS、および先端の技術を駆使して、製造プロセスの効率化、業務効率化、チームワーク強化、コスト削減、品質向上を実現します。このサービスは、製造業の課題を深く理解し、それに対する最適なデジタルソリューションを提供することで、企業が持続的な成長とイノベーションを達成できるようサポートします。
オンライン講座
製造業、主に購買・調達部門にお勤めの方々に向けた情報を配信しております。
新任の方やベテランの方、管理職を対象とした幅広いコンテンツをご用意しております。
お問い合わせ
コストダウンが利益に直結する術だと理解していても、なかなか前に進めることができない状況。そんな時は、newjiのコストダウン自動化機能で大きく利益貢献しよう!
(Β版非公開)