- お役立ち記事
- Reliability evaluation of electronic components and equipment Safety design and defect prevention measures
月間77,185名の
製造業ご担当者様が閲覧しています*
*2025年2月28日現在のGoogle Analyticsのデータより
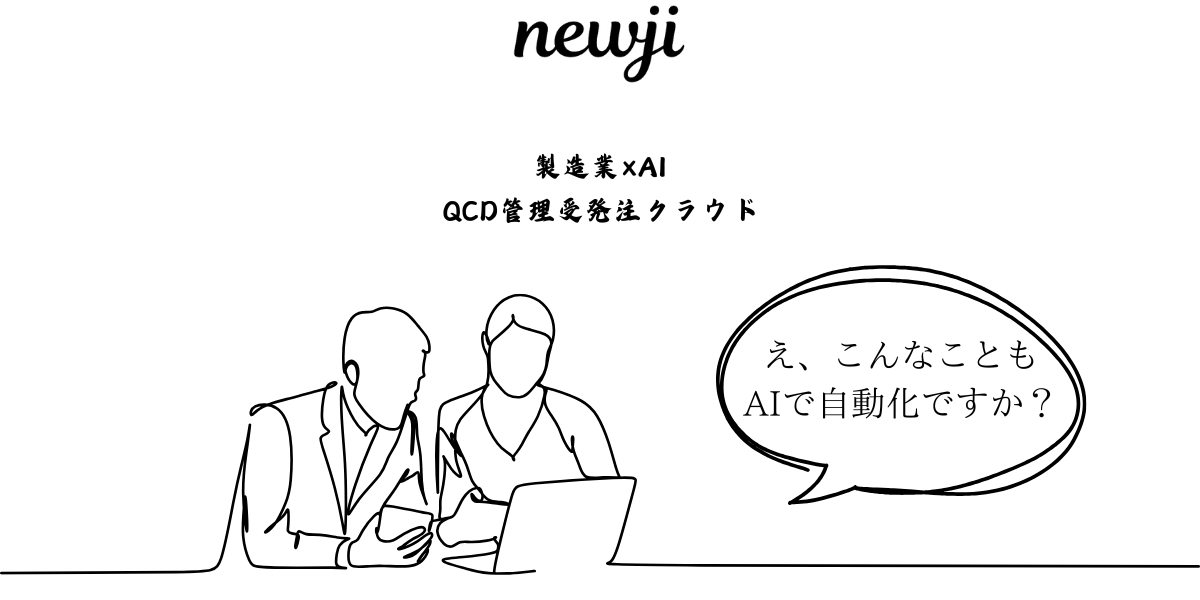
Reliability evaluation of electronic components and equipment Safety design and defect prevention measures
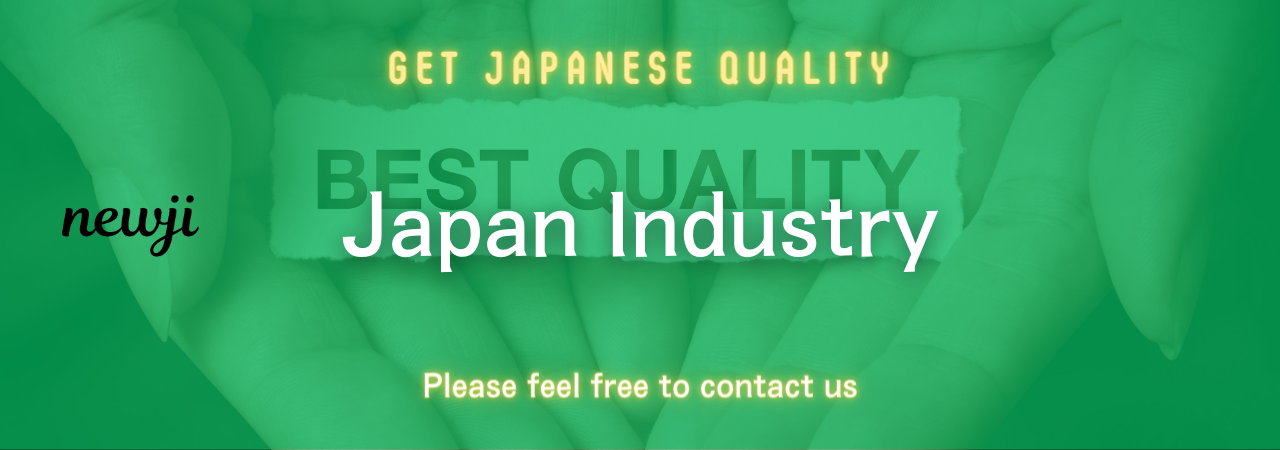
目次
Understanding Reliability Evaluation
Reliability evaluation is a critical process in the design and maintenance of electronic components and equipment.
It involves assessing how well a product can perform its intended function without failure over a specific period.
Reliability is a key factor in the safety and effectiveness of electronic devices used in various applications, from consumer gadgets to industrial machinery.
There are several methods used to evaluate the reliability of electronic components.
These include statistical analysis, life testing, and failure mode and effects analysis (FMEA).
Each method provides valuable insights into the potential weaknesses and expected lifespan of electronic equipment.
The Importance of Reliability in Design
Designing reliable electronic components is crucial for both manufacturers and consumers.
For manufacturers, a reliable product reduces the cost associated with repairs, replacements, and warranty claims.
For consumers, reliability translates to trust in a product’s performance and safety.
In the design phase, engineers must consider various factors that influence reliability.
These include material selection, manufacturing processes, environmental conditions, and expected usage patterns.
By addressing these factors early in the design process, engineers can prevent potential failures and extend the life of electronic equipment.
Safety Design Measures
Safety design measures are integral to ensuring the reliability and safety of electronic components.
These measures involve designing components in a way that minimizes the risk of failure and enhances user safety.
A common approach to safety design is the incorporation of redundant systems.
Redundancy involves using multiple components to perform a single function, so if one component fails, the others can continue to operate.
This ensures that the equipment remains functional even when a failure occurs.
Another measure is the implementation of robust testing procedures.
Testing ensures that components can withstand various stressors and conditions they will encounter during operation.
By subjecting components to rigorous testing, manufacturers can identify and address potential weaknesses before the product reaches the market.
Defect Prevention in Manufacturing
Defect prevention is a proactive approach aimed at minimizing the occurrence of defects during the manufacturing process.
By preventing defects, manufacturers can improve product reliability and reduce the cost associated with rework and repairs.
One effective method for defect prevention is Six Sigma, a data-driven approach that seeks to improve processes by identifying and eliminating causes of defects.
Six Sigma tools and techniques help manufacturers understand process variations and implement process improvements.
Implementing quality control measures is another essential strategy for defect prevention.
Regular inspections and testing during the manufacturing process can help identify defects early, allowing for corrective actions to be taken promptly.
Quality control measures ensure that only products that meet specified standards reach the end-users.
Key Factors Influencing Reliability
Several factors influence the reliability of electronic components and equipment.
One key factor is the quality of materials used in production.
High-quality materials are less likely to degrade over time, increasing the longevity of the components.
Environmental conditions also play a significant role in reliability.
Components exposed to extreme temperatures, humidity, or corrosive environments are more prone to failure.
Designing components to withstand specific environmental conditions is vital to ensuring their reliability.
Usage patterns are another factor affecting reliability.
Devices that experience frequent usage are more likely to wear out faster.
Understanding how and where products will be used helps manufacturers design devices that can endure specific usage conditions.
Testing for Reliability and Safety
Testing is an essential part of ensuring the reliability and safety of electronic components.
There are several types of tests conducted to evaluate different aspects of a product’s performance.
Accelerated life testing involves exposing components to elevated levels of stress to simulate prolonged usage.
This type of testing helps predict the product’s lifespan and identify potential failure modes.
Environmental testing evaluates how components perform under different environmental conditions, such as temperature and humidity extremes.
This testing ensures that equipment can operate reliably in the conditions they are likely to encounter in real-world applications.
Failure analysis is another critical testing method.
When a component fails, failure analysis helps identify the root cause of the failure.
By understanding the failure mechanisms, manufacturers can make improvements to prevent similar failures in future designs.
The Role of Technology in Reliability and Safety
Advancements in technology continue to play a significant role in enhancing the reliability and safety of electronic components.
For instance, the use of computer-aided design (CAD) software allows engineers to model and simulate product performance before physical prototypes are built.
This capability helps identify potential design flaws early and reduces the likelihood of defects in the final product.
Additionally, the Internet of Things (IoT) has revolutionized the way manufacturers monitor electronic equipment.
IoT-enabled devices can send real-time data on their performance and health status.
This data helps manufacturers predict failures and schedule preventive maintenance, thus extending the equipment’s lifespan.
Conclusion
Reliability evaluation, safety design, and defect prevention are critical components in the production of electronic goods that meet consumer expectations and regulatory standards.
By focusing on these aspects, manufacturers can ensure the safety, effectiveness, and longevity of their products.
Advancements in technology will continue to provide new tools and methods for enhancing reliability and safety, benefiting both manufacturers and consumers alike.
資料ダウンロード
QCD管理受発注クラウド「newji」は、受発注部門で必要なQCD管理全てを備えた、現場特化型兼クラウド型の今世紀最高の受発注管理システムとなります。
ユーザー登録
受発注業務の効率化だけでなく、システムを導入することで、コスト削減や製品・資材のステータス可視化のほか、属人化していた受発注情報の共有化による内部不正防止や統制にも役立ちます。
NEWJI DX
製造業に特化したデジタルトランスフォーメーション(DX)の実現を目指す請負開発型のコンサルティングサービスです。AI、iPaaS、および先端の技術を駆使して、製造プロセスの効率化、業務効率化、チームワーク強化、コスト削減、品質向上を実現します。このサービスは、製造業の課題を深く理解し、それに対する最適なデジタルソリューションを提供することで、企業が持続的な成長とイノベーションを達成できるようサポートします。
製造業ニュース解説
製造業、主に購買・調達部門にお勤めの方々に向けた情報を配信しております。
新任の方やベテランの方、管理職を対象とした幅広いコンテンツをご用意しております。
お問い合わせ
コストダウンが利益に直結する術だと理解していても、なかなか前に進めることができない状況。そんな時は、newjiのコストダウン自動化機能で大きく利益貢献しよう!
(β版非公開)