- お役立ち記事
- Remote monitoring technology and real-time process optimization for chemical factories
月間77,185名の
製造業ご担当者様が閲覧しています*
*2025年2月28日現在のGoogle Analyticsのデータより
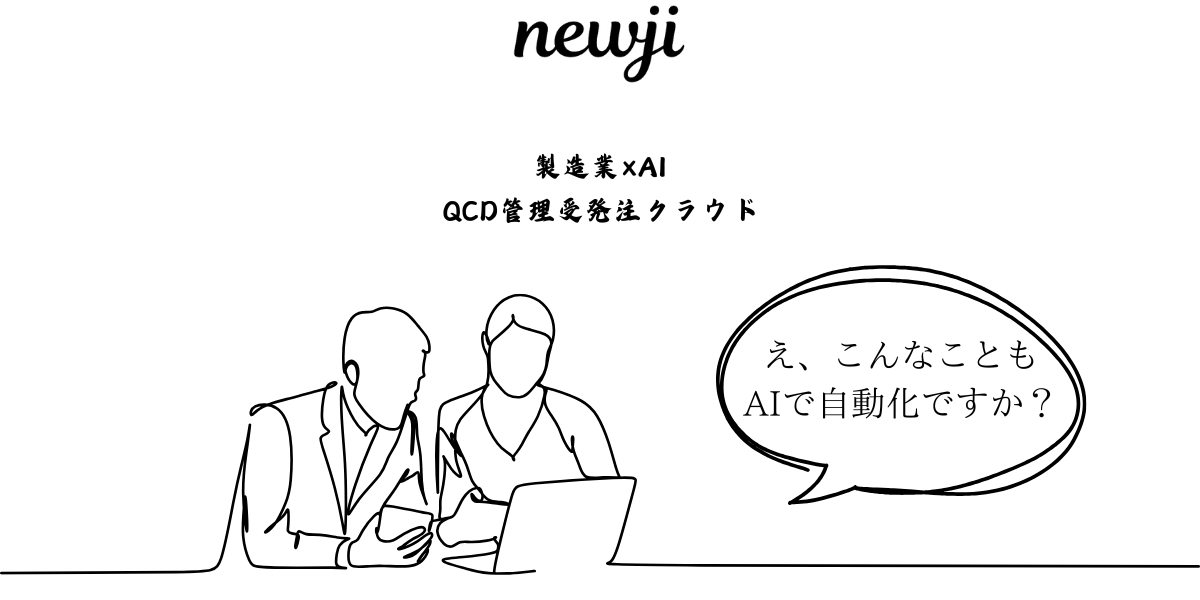
Remote monitoring technology and real-time process optimization for chemical factories
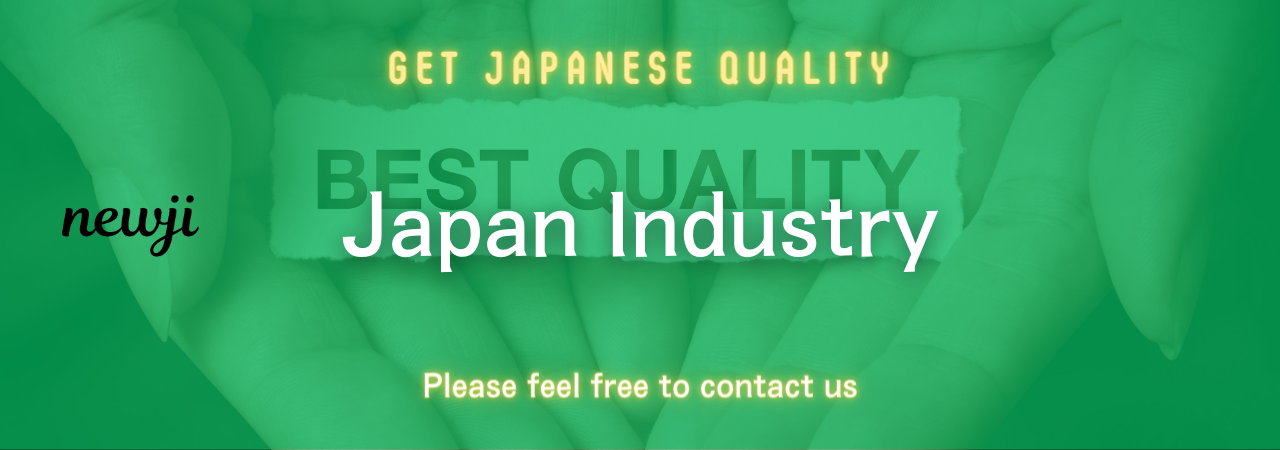
目次
Understanding Remote Monitoring Technology
Remote monitoring technology has revolutionized the way industries operate, especially in complex sectors such as chemical manufacturing.
This technology allows operators to oversee and manage industrial processes from a distance, reducing the need for physical presence on-site.
By employing sensors and advanced communication tools, it becomes possible to track every aspect of production in real-time.
At the heart of remote monitoring technology are sensors and smart devices.
These instruments are fitted within various parts of the chemical plant to collect data on temperature, pressure, flow rates, and other critical parameters.
The data is then transmitted to a centralized control system where it is analyzed and monitored for any deviations or anomalies.
This capability is invaluable for ensuring the smooth and efficient operation of chemical processes, while also enhancing safety and compliance.
The Role of Real-time Process Optimization
Real-time process optimization is a game-changer for chemical factories aiming to enhance productivity and minimize waste.
With the advent of digital technologies, factories can now adjust their operations instantly, based on real-time data.
This ensures that processes are not only efficient but also adaptable to changing conditions and demands.
In practice, real-time process optimization involves the use of advanced analytics and algorithms.
These tools assess the incoming data from remote monitoring systems and determine the optimal settings or adjustments needed for different stages of the chemical process.
For instance, if there’s a fluctuation in the quality of raw material, the system can quickly recalibrate to maintain product quality without significant downtime.
Benefits of Combining Remote Monitoring and Real-time Optimization
Integrating remote monitoring technology with real-time process optimization offers numerous benefits to chemical factories.
Firstly, it significantly improves operational efficiency.
Factories can minimize downtime by quickly identifying and addressing potential issues before they escalate.
This real-time insight helps in maintaining a steady flow of high-quality products.
Secondly, safety is tremendously enhanced.
Chemical processes can be hazardous, with risks ranging from equipment failures to hazardous spills.
Continuous monitoring ensures that any irregularities are detected promptly, allowing for immediate interventions and preventive measures.
Moreover, this integration aids in environmental compliance.
With stringent regulations governing emissions and waste in chemical industries, having a system that ensures operations align with these standards is crucial.
Remote monitoring coupled with optimization ensures that all processes are controlled precisely to reduce emissions and manage waste efficiently.
Technology Components Involved
The foundation of remote monitoring and real-time optimization includes several key technological components.
These are:
Sensors and IoT Devices
Sensors and IoT (Internet of Things) devices are essential for capturing data from various stages of the production process.
They measure parameters such as temperature, pressure, and chemical concentrations, providing a comprehensive view of the operational conditions.
Cloud Computing
The data collected from sensors is often vast and complex.
Cloud computing provides the necessary infrastructure to store, process, and analyze this data efficiently.
It enables scalability and flexibility, allowing factories to handle large volumes of data without investing in extensive local infrastructure.
Data Analytics and Machine Learning
To make sense of the data and derive actionable insights, advanced data analytics and machine learning algorithms are employed.
These tools can identify patterns and predict potential issues, facilitating proactive measures to optimize processes.
Challenges and Solutions
While the integration of remote monitoring and real-time optimization offers many benefits, it also presents several challenges.
One of the primary concerns is cybersecurity.
As more devices and systems are interconnected, the potential vulnerability to cyberattacks increases.
To address this, factories need to invest in robust cybersecurity measures, including firewalls, encrypted communications, and regular security audits.
Another challenge is the initial cost of implementing these technologies.
However, the long-term benefits, such as reduced operational costs and improved efficiency, typically outweigh the initial investment.
Many companies also offer scalable solutions tailored to different budgets, ensuring that even smaller factories can leverage these technologies.
The Future of Chemical Factories
As the chemical industry continues to evolve, the adoption of remote monitoring technology and real-time process optimization will likely become even more widespread.
Advancements in AI and machine learning will enhance predictive capabilities, providing even more accurate insights into process management.
Moreover, integrating these technologies with other innovations such as digital twins — virtual replicas of physical systems — will further optimize operations.
These developments will lead to smarter, more resilient, and sustainable chemical production systems.
In conclusion, remote monitoring technology and real-time process optimization are indispensable for modern chemical factories.
They not only enhance operational efficiency and safety but also ensure compliance with environmental regulations.
As technology continues to advance, these systems will become increasingly sophisticated, paving the way for a new era in chemical manufacturing.
資料ダウンロード
QCD管理受発注クラウド「newji」は、受発注部門で必要なQCD管理全てを備えた、現場特化型兼クラウド型の今世紀最高の受発注管理システムとなります。
ユーザー登録
受発注業務の効率化だけでなく、システムを導入することで、コスト削減や製品・資材のステータス可視化のほか、属人化していた受発注情報の共有化による内部不正防止や統制にも役立ちます。
NEWJI DX
製造業に特化したデジタルトランスフォーメーション(DX)の実現を目指す請負開発型のコンサルティングサービスです。AI、iPaaS、および先端の技術を駆使して、製造プロセスの効率化、業務効率化、チームワーク強化、コスト削減、品質向上を実現します。このサービスは、製造業の課題を深く理解し、それに対する最適なデジタルソリューションを提供することで、企業が持続的な成長とイノベーションを達成できるようサポートします。
製造業ニュース解説
製造業、主に購買・調達部門にお勤めの方々に向けた情報を配信しております。
新任の方やベテランの方、管理職を対象とした幅広いコンテンツをご用意しております。
お問い合わせ
コストダウンが利益に直結する術だと理解していても、なかなか前に進めることができない状況。そんな時は、newjiのコストダウン自動化機能で大きく利益貢献しよう!
(β版非公開)