- お役立ち記事
- Request for production of vertical (under-axis) two-pole generator and optimal manufacturing method
月間77,185名の
製造業ご担当者様が閲覧しています*
*2025年2月28日現在のGoogle Analyticsのデータより
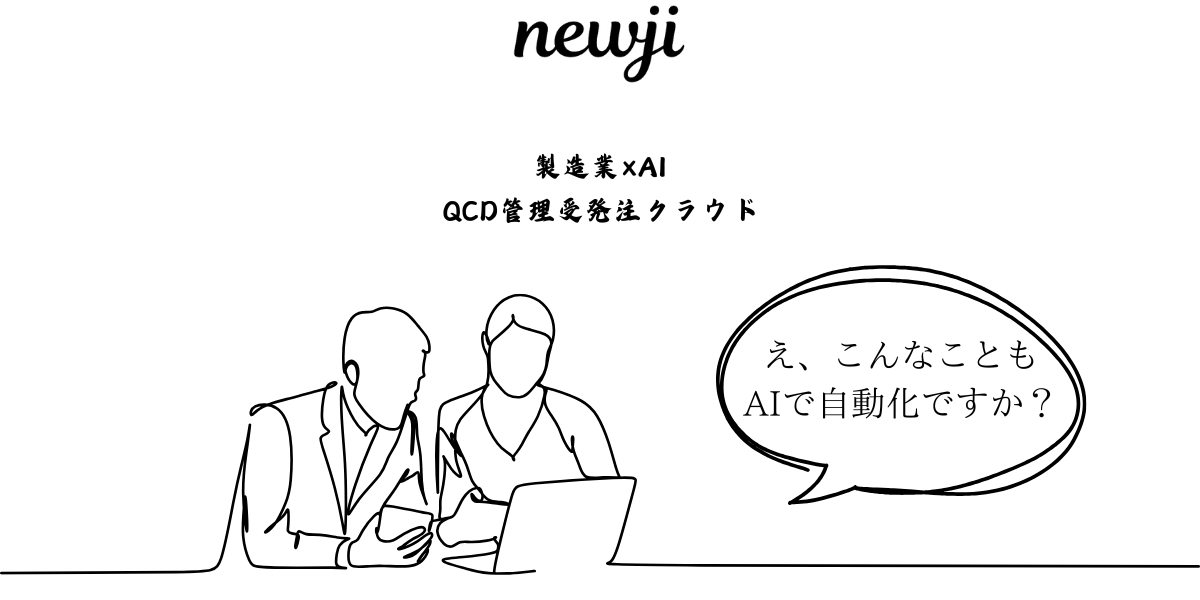
Request for production of vertical (under-axis) two-pole generator and optimal manufacturing method
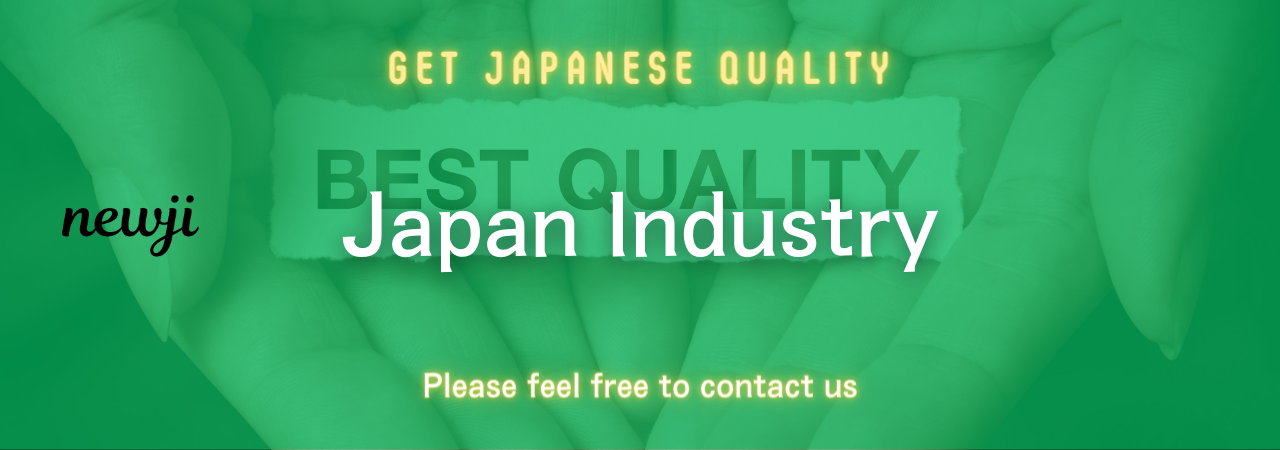
目次
Introduction to Vertical Two-Pole Generators
When it comes to generating electricity, the two-pole generator is a staple in various industrial applications.
Its simple design and efficient operation make it a preferred choice, especially when doing vertical installations.
But what is a vertical two-pole generator, and why is it so widely used?
A two-pole generator runs with a simple mechanism.
It uses a single rotating magnetic field, making it effective for generating alternating current (AC).
When positioned vertically, this type of generator can save space, making it perfect for installations where floor area is limited.
Components of a Vertical Two-Pole Generator
Before jumping into the manufacturing process, it’s essential to understand the components that make up a vertical two-pole generator.
Rotor
The rotor is the moving part of the machine.
It houses the magnets that are responsible for creating the magnetic field.
In a two-pole generator, the rotor typically contains two poles—one north and one south.
Stator
The stator is the stationary part where the electricity is generated.
It consists of coils of wire that conduct electricity as the magnetic field from the rotor cuts through them.
Mounting Frame
The mounting frame provides structural support to the generator.
For vertical installations, a robust frame is essential to maintain stability.
Bearing System
Bearings facilitate smooth rotation of the rotor.
They are critical for reducing friction and wear, which ensures the long-term efficiency of the generator.
Manufacturing Process of Vertical Two-Pole Generators
Material Selection
The first step in manufacturing a vertical two-pole generator is selecting the right materials.
Quality materials are crucial for maintaining efficiency and longevity.
Copper is commonly used for stator coils for its excellent conductivity.
Iron or steel may be used for the rotor to enhance the magnetic field.
Winding the Stator
Winding the stator requires precision and accuracy.
Coils of wire are wound onto the stator’s iron core, taking care to ensure that the windings are tight and evenly distributed.
Proper winding is essential for minimizing energy losses and maximizing efficiency.
Assembling the Rotor
The rotor assembly involves affixing the magnetic poles onto a rotating shaft.
Alignment is critical here to ensure that the magnetic field interacts optimally with the stator.
Installing the Bearing System
Bearings are installed to reduce friction between the rotor and the mounting frame.
In a vertical setup, special attention is given to axial and radial loads, as gravity can affect bearing performance over time.
Optimal Manufacturing Methods
Achieving optimal efficiency and performance in a vertical two-pole generator requires meticulous attention to detail throughout the manufacturing process.
Precision Engineering
High-precision engineering techniques are vital.
Computer Numerical Control (CNC) machines can be used to achieve the exact dimensions needed for both stator and rotor components.
This precision ensures that components fit together seamlessly, reducing noise and vibration during operation.
Quality Control
Implementing stringent quality control measures ensures that each component meets industry standards.
Regular inspections and tests are conducted at each stage of the manufacturing process.
This helps in identifying and rectifying any defects that could impair the generator’s functionality.
Customizing to Client Needs
While standard models are available, customizing generators to meet specific client requirements can significantly improve their functionality.
This customization can include modifications in the mounting frame, rotor, or stator to better suit customer applications.
Benefits of Vertical Two-Pole Generators
Vertical two-pole generators offer several advantages over their horizontal counterparts.
For one, they are space-efficient, making them suitable for areas with limited floor space.
The vertical design also allows for easier maintenance, as components are more accessible.
Furthermore, the simplicity of a two-pole system means fewer moving parts, reducing the likelihood of mechanical failure.
Conclusion
In summary, vertical two-pole generators are a reliable and efficient choice for power generation, particularly in industrial settings with space constraints.
Knowing the essential components and the optimal manufacturing methods can lead to the production of high-performance machines.
Adhering to precision engineering practices and quality control measures ensures that these generators provide optimal energy output while enjoying a long operational life.
資料ダウンロード
QCD管理受発注クラウド「newji」は、受発注部門で必要なQCD管理全てを備えた、現場特化型兼クラウド型の今世紀最高の受発注管理システムとなります。
ユーザー登録
受発注業務の効率化だけでなく、システムを導入することで、コスト削減や製品・資材のステータス可視化のほか、属人化していた受発注情報の共有化による内部不正防止や統制にも役立ちます。
NEWJI DX
製造業に特化したデジタルトランスフォーメーション(DX)の実現を目指す請負開発型のコンサルティングサービスです。AI、iPaaS、および先端の技術を駆使して、製造プロセスの効率化、業務効率化、チームワーク強化、コスト削減、品質向上を実現します。このサービスは、製造業の課題を深く理解し、それに対する最適なデジタルソリューションを提供することで、企業が持続的な成長とイノベーションを達成できるようサポートします。
製造業ニュース解説
製造業、主に購買・調達部門にお勤めの方々に向けた情報を配信しております。
新任の方やベテランの方、管理職を対象とした幅広いコンテンツをご用意しております。
お問い合わせ
コストダウンが利益に直結する術だと理解していても、なかなか前に進めることができない状況。そんな時は、newjiのコストダウン自動化機能で大きく利益貢献しよう!
(β版非公開)