- お役立ち記事
- Request points for prototyping palm drone frames at low cost and achieving stable flight
月間76,176名の
製造業ご担当者様が閲覧しています*
*2025年3月31日現在のGoogle Analyticsのデータより
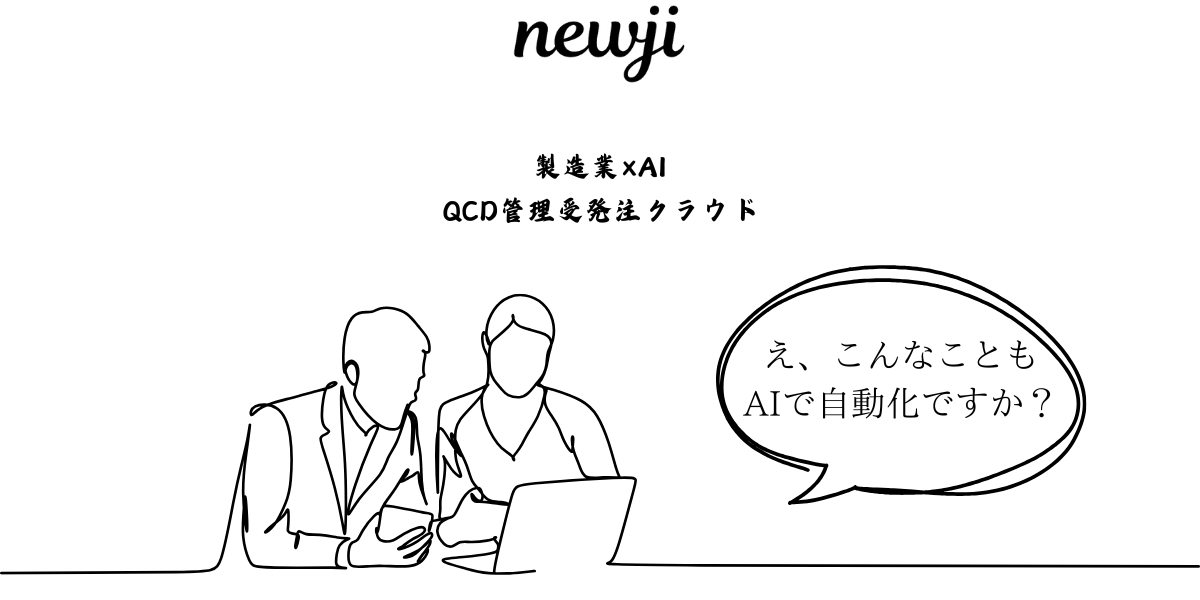
Request points for prototyping palm drone frames at low cost and achieving stable flight
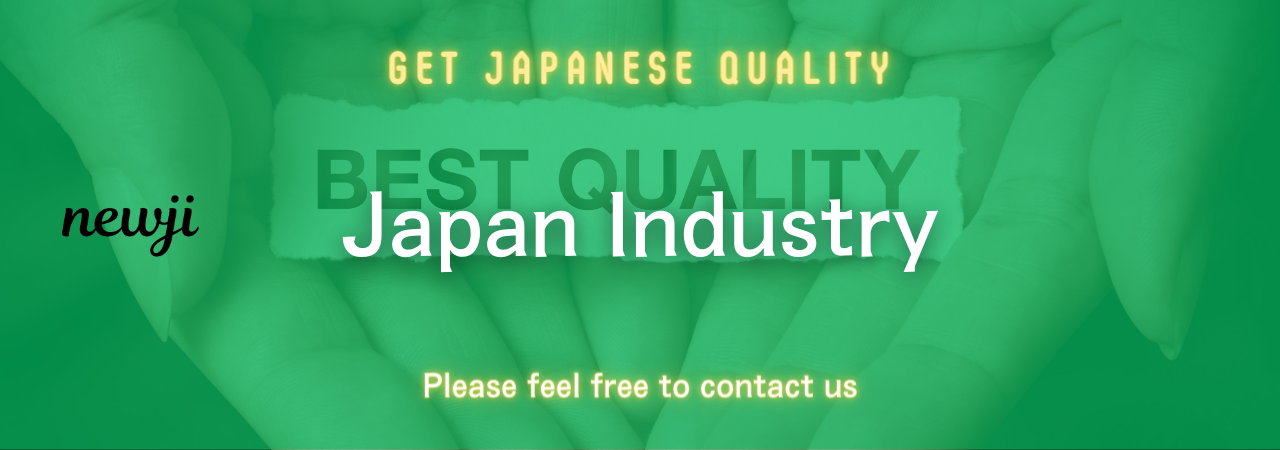
When you’re working on designing and prototyping palm-sized drone frames with cost efficiency and stable flight, it involves a variety of factors that need careful consideration. Let’s delve into the key points you need to keep in mind to achieve your goal.
目次
Understanding the Importance of Prototyping
Prototyping is a crucial step in drone development.
It allows designers and engineers to test the feasibility of concepts before committing to mass production.
In the case of palm drone frames, prototyping can help identify potential design flaws, material inadequacies, and aerodynamic issues.
Prototyping also provides an opportunity to refine and optimize the design for improved performance.
Moreover, it offers a tangible model to test for balance, center of gravity, and motor placement, all of which contribute to the drone’s stability during flight.
Choosing the Right Materials
Material choice plays a significant role in the development of drone frames.
Selecting lightweight but durable materials is essential for the stability and performance of palm-sized drones.
Common materials include carbon fiber, plastic composites, and lightweight metals like aluminum.
Carbon fiber is favored for its strength-to-weight ratio, offering durability without adding excessive weight.
On the other hand, plastic composites can be more cost-effective, though they may not provide the same level of robustness.
It’s important to conduct material testing during the prototyping phase to evaluate how different materials impact drone performance.
Design Considerations for Cost-Effective Prototyping
Keeping costs down while ensuring high-quality prototypes is a balancing act.
Here are some design considerations that can help:
Simplified Geometries
Using simplified geometries reduces complexity and manufacturing costs.
Focus on creating designs that are easy to manufacture with minimal material waste.
This not only lowers production costs but also shortens the prototyping cycle time.
Modularity
Incorporating modular designs allows for individual component testing and replacement.
This means if one part of the prototype fails, you won’t need to redo the entire frame.
Modular designs can reduce costs by allowing for easy assembly and disassembly.
Optimized Design Tools
Utilize computer-aided design (CAD) software to experiment with different frame structures and configurations.
CAD simulations can highlight potential issues before a physical prototype is created.
This not only saves time but also reduces material costs associated with physical testing.
Testing for Stable Flight
Once a prototype is developed, testing for stability is crucial to ensure the drone can achieve stable flight conditions.
Consider the following approaches:
Balancing the Frame
A well-balanced drone is essential for stable flight.
Ensure that the weight distribution across the drone is even, with components placed symmetrically relative to the center of gravity.
This enhances maneuverability and stability in the air.
Motor and Propeller Selection
Choosing the right motors and propellers can drastically influence a drone’s stability.
Opt for components that are compatible with the weight and design of your prototype.
Ensure sufficient thrust is generated to maintain stable altitude and control.
Aerodynamic Testing
Aerodynamic tests help analyze how airflows over the drone’s frame can affect flight stability.
Wind tunnel tests or digital simulations can identify areas of the design that may cause drag or instability.
Iterative Process for Enhanced Performance
Remember that prototyping is an iterative process.
After initial testing, take feedback from each version of the prototype to refine and improve the design continually.
This cycle of design, test, analyze, and improve can lead to a final product that outperforms initial expectations, both in terms of cost and flight stability.
Feedback and Refinement
Gather data from each flight test to identify any recurring issues or design shortfalls.
This feedback is invaluable in guiding future iterations of the prototype.
Addressing these issues early in the prototyping phase saves both time and resources.
Collaboration and Innovation
Consider collaborating with fellow designers and engineers to brainstorm solutions to common problems faced during prototyping.
Collaboration can lead to innovative approaches that may be more cost-effective or provide better stability performance.
Conclusion
Creating palm-sized drone frames that are both cost-effective and capable of stable flight requires attention to detail, innovative design processes, and effective materials selection.
By employing strategic prototyping practices and continuously seeking ways to refine and improve, you can achieve a successful balance between cost and performance.
Remember, each prototype brings you closer to the ideal drone frame that meets all your objectives.
資料ダウンロード
QCD管理受発注クラウド「newji」は、受発注部門で必要なQCD管理全てを備えた、現場特化型兼クラウド型の今世紀最高の受発注管理システムとなります。
ユーザー登録
受発注業務の効率化だけでなく、システムを導入することで、コスト削減や製品・資材のステータス可視化のほか、属人化していた受発注情報の共有化による内部不正防止や統制にも役立ちます。
NEWJI DX
製造業に特化したデジタルトランスフォーメーション(DX)の実現を目指す請負開発型のコンサルティングサービスです。AI、iPaaS、および先端の技術を駆使して、製造プロセスの効率化、業務効率化、チームワーク強化、コスト削減、品質向上を実現します。このサービスは、製造業の課題を深く理解し、それに対する最適なデジタルソリューションを提供することで、企業が持続的な成長とイノベーションを達成できるようサポートします。
製造業ニュース解説
製造業、主に購買・調達部門にお勤めの方々に向けた情報を配信しております。
新任の方やベテランの方、管理職を対象とした幅広いコンテンツをご用意しております。
お問い合わせ
コストダウンが利益に直結する術だと理解していても、なかなか前に進めることができない状況。そんな時は、newjiのコストダウン自動化機能で大きく利益貢献しよう!
(β版非公開)