- お役立ち記事
- Residual stress generation mechanism, effective utilization method, and removal technology to prevent destruction
月間76,176名の
製造業ご担当者様が閲覧しています*
*2025年3月31日現在のGoogle Analyticsのデータより
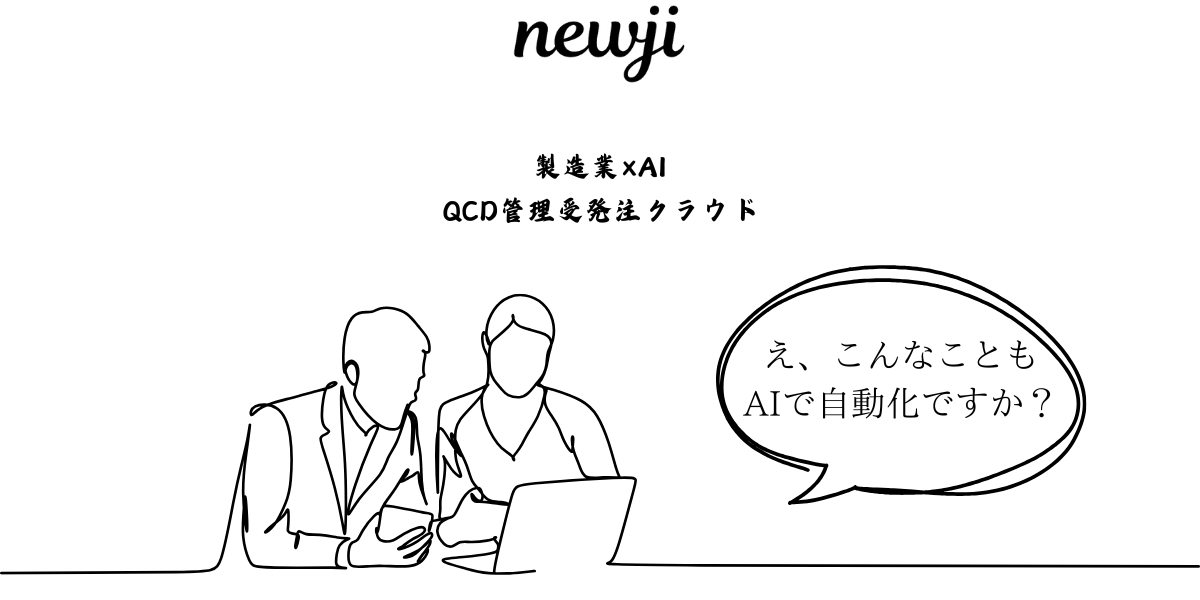
Residual stress generation mechanism, effective utilization method, and removal technology to prevent destruction
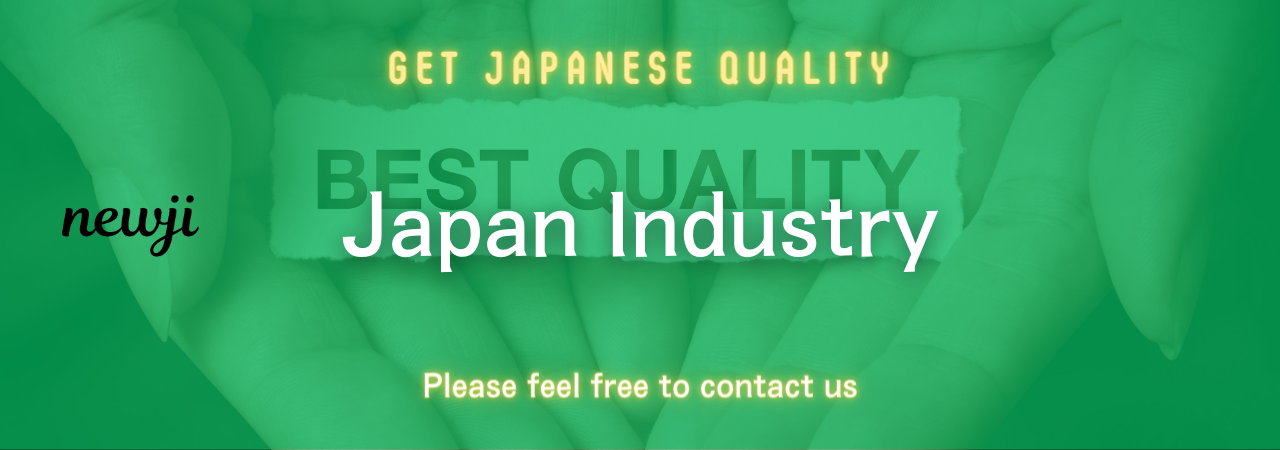
Residual stress is a key factor affecting the performance and durability of materials in various engineering applications.
Understanding how residual stress is generated, utilizing it effectively, and removing it when necessary are crucial steps in optimizing the performance of materials.
目次
What is Residual Stress?
Residual stress refers to the stress that remains in a material after the original cause of the stress has been removed.
It can originate from various manufacturing processes such as casting, welding, machining, and plastic deformation.
These stresses are locked inside the material and can significantly influence its mechanical properties.
Types of Residual Stress
Residual stress can be classified into three categories:
1. **Macrostress**: Stresses that are uniform over large areas.
2. **Microstress**: Stresses at the grain level or in a specific phase of a material.
3. **Eigenstress**: Stresses due to phase transformations or thermal effects within the material.
Generation Mechanism of Residual Stress
Residual stress is commonly generated through the following mechanisms:
Thermal Effects
During processes like welding and casting, temperature gradients lead to differential expansion and contraction.
This can cause tensional or compressive stresses within the material as it returns to a uniform temperature.
Mechanical Deformation
Processes such as forging, extrusion, and bending apply plastic deformation on the material.
This deformation may not be uniform and tends to leave residual stresses once the external forces are removed.
Phase Transformations
In materials undergoing phase transformations, the change in crystal structure can lead to volume changes resulting in residual stress.
For instance, the transformation of austenite to martensite in steels can induce significant residual stress.
Effective Utilization of Residual Stress
Not all residual stresses are detrimental.
In fact, certain applications can benefit from the existence of residual stresses.
Here are some methods to utilize residual stress effectively:
Enhancing Fatigue Life
Introducing compressive residual stress on the surface of components such as springs, gears, and shafts can significantly enhance their fatigue life.
Techniques like shot peening and surface hardening are employed to achieve this.
Stabilizing Mechanical Components
Residual stresses can stabilize mechanical components against distortion during machining or assembly.
This is particularly useful in maintaining dimensional accuracy in precision parts.
Improving Fracture Toughness
By appropriately managing residual stresses, materials can resist crack propagation better.
Residual compressive stresses on the surface work against tensile stresses that might lead to crack nucleation.
Removal and Prevention of Destructive Residual Stress
When residual stresses are likely to cause failure or deformation, removing or mitigating them becomes necessary.
Below are some methods to achieve this:
Stress Relieving Techniques
Thermal Stress Relief
This involves heating the material uniformly and then cooling it slowly.
The process allows the material to return to a stress-free state, minimizing internal stresses.
Vibratory Stress Relief
A less energy-intensive method compared to thermal processes, vibratory stress relief uses vibrations to redistribute residual stresses evenly throughout the material.
Mechanical Techniques
Overstressing
This involves deliberately overloading the material to exceed its yield strength, thus redistributing or neutralizing existing residual stresses.
Machining Adjustments
Careful planning of machining operations, such as employing symmetrical material removal, can help in mainaining stress balance and preventing distortion.
Advancements in Residual Stress Management
Technology continues to evolve, providing newer methods for managing residual stress effectively.
Advanced Computational Tools
Finite Element Analysis (FEA) provides engineers with precise insights into stress distribution within materials, enabling them to anticipate and manage potential issues effectively.
Innovative Material Design
Modern material engineering designs inherently take residual stress into account, using methods like additive manufacturing, which allows for stress control during fabrication.
Smart Monitoring Systems
Industry 4.0 technologies like real-time monitoring sensors can predict the onset of undesirable residual stresses, allowing for timely intervention during the manufacturing process.
Understanding and managing residual stress is fundamental in enhancing material performance, ensuring product reliability, and reducing manufacturing costs.
Through effective utilization techniques and smart removal strategies, industries can better harness the benefits of residual stress while mitigating its potential drawbacks.
Continued research and technological advancement in this field promise further improvements in material sciences and engineering capabilities.
資料ダウンロード
QCD管理受発注クラウド「newji」は、受発注部門で必要なQCD管理全てを備えた、現場特化型兼クラウド型の今世紀最高の受発注管理システムとなります。
ユーザー登録
受発注業務の効率化だけでなく、システムを導入することで、コスト削減や製品・資材のステータス可視化のほか、属人化していた受発注情報の共有化による内部不正防止や統制にも役立ちます。
NEWJI DX
製造業に特化したデジタルトランスフォーメーション(DX)の実現を目指す請負開発型のコンサルティングサービスです。AI、iPaaS、および先端の技術を駆使して、製造プロセスの効率化、業務効率化、チームワーク強化、コスト削減、品質向上を実現します。このサービスは、製造業の課題を深く理解し、それに対する最適なデジタルソリューションを提供することで、企業が持続的な成長とイノベーションを達成できるようサポートします。
製造業ニュース解説
製造業、主に購買・調達部門にお勤めの方々に向けた情報を配信しております。
新任の方やベテランの方、管理職を対象とした幅広いコンテンツをご用意しております。
お問い合わせ
コストダウンが利益に直結する術だと理解していても、なかなか前に進めることができない状況。そんな時は、newjiのコストダウン自動化機能で大きく利益貢献しよう!
(β版非公開)