- お役立ち記事
- Residual stress measurement and relaxation techniques for high-temperature materials that new employees in the equipment management department of the steel industry should know
月間76,176名の
製造業ご担当者様が閲覧しています*
*2025年3月31日現在のGoogle Analyticsのデータより
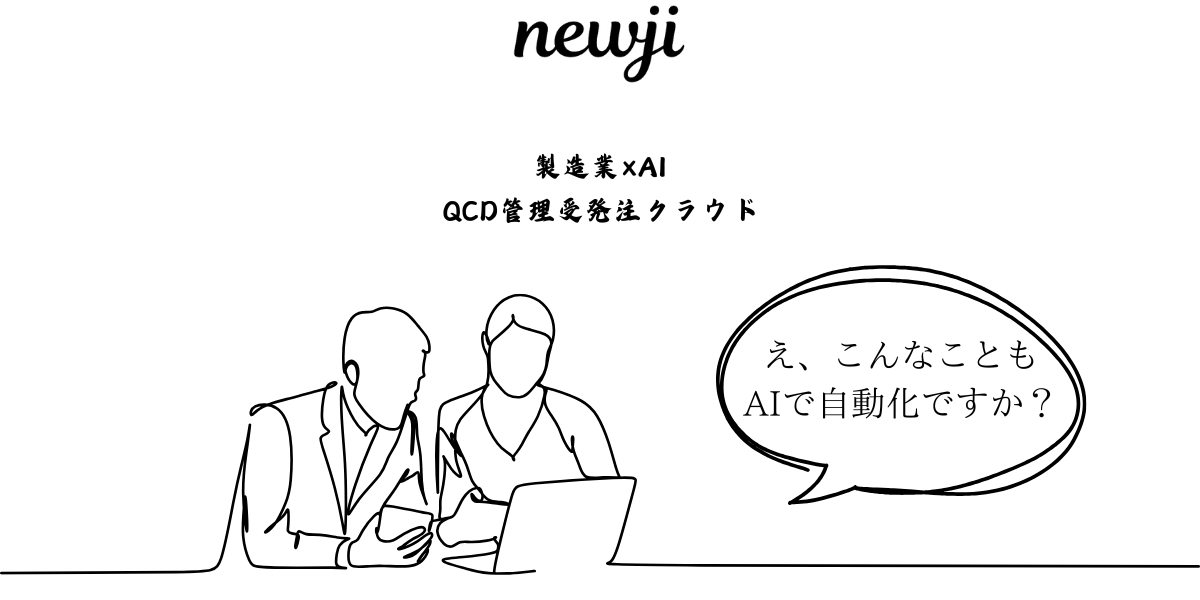
Residual stress measurement and relaxation techniques for high-temperature materials that new employees in the equipment management department of the steel industry should know
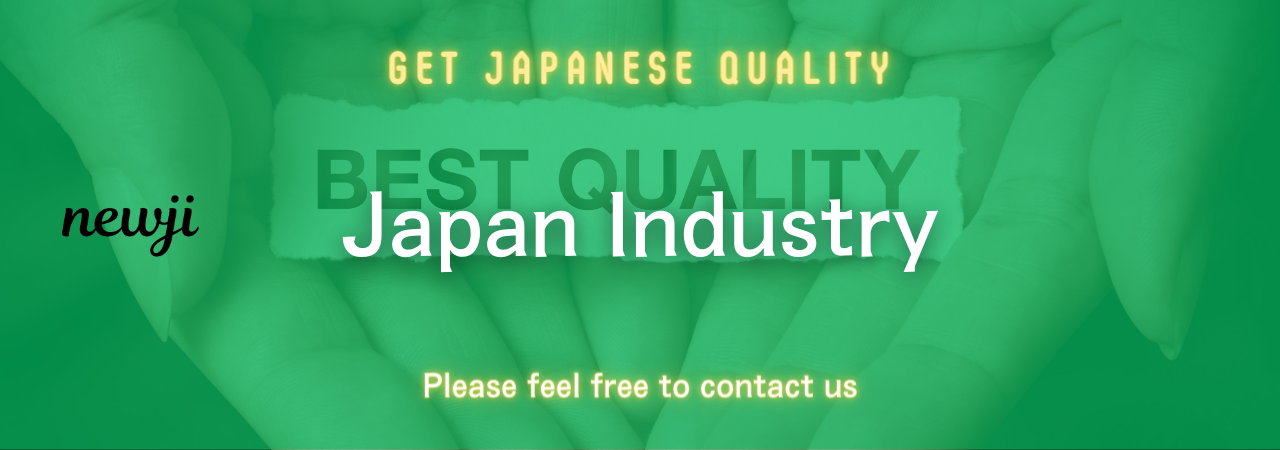
目次
Understanding Residual Stress in High-Temperature Materials
Residual stress is a common phenomenon observed in materials subjected to various manufacturing and processing techniques.
These stresses are locked within a material even when external forces are not present.
In the steel industry, specially with high-temperature materials, understanding and managing residual stress is crucial.
It affects the mechanical properties, performance, and reliability of the components.
For new employees in the equipment management department, a fundamental understanding of residual stress measurement and relaxation techniques is essential.
What Causes Residual Stress?
Residual stress can arise from multiple factors, primarily due to temperature changes, phase transformations, and mechanical processes.
When steel components are heated and then cooled rapidly, different sections of the material contract at varying rates.
This difference in contraction leads to the build-up of stress.
Similarly, welding, casting, and machining processes also introduce residual stress.
In high-temperature materials, these stresses can significantly affect the material’s structural integrity and performance.
Measurement Techniques for Residual Stress
Understanding residual stress involves accurate measurement, which can be achieved through several techniques.
The choice of method depends on factors such as the nature of the material, the size of the component, and the desired precision.
X-ray Diffraction (XRD)
X-ray diffraction is a popular non-destructive method used to measure residual stress.
It works by analyzing the diffraction pattern of X-rays passing through the crystalline lattice of the material.
By measuring the spacing of the crystal planes, residual stresses within the material can be inferred.
XRD is advantageous due to its precision and applicability to various crystalline materials.
Neutron Diffraction
Neutron diffraction is another non-destructive technique similar to XRD but uses neutrons instead of X-rays.
It is particularly useful for measuring residual stress at greater depths, which is often required in thicker materials.
Neutrons have a deeper penetration capability, offering valuable information about the internal stress distribution without damaging the component.
Hole-Drilling Method
The hole-drilling method is a semi-destructive technique where a small hole is drilled into the material.
The subsequent deformation around the hole is measured using strain gauges.
These measurements help determine the residual stress around the drilled area.
Although it is not completely non-destructive, the effects are minimal on large structures, making it suitable for practical applications.
Contour Method
The contour method involves cutting the material in half and measuring the deformation of the newly exposed surface using a coordinate measuring machine (CMM).
This technique provides a two-dimensional map of residual stress distribution across the material’s cross-section.
It is particularly useful for understanding stress across larger components.
Relaxation Techniques for Residual Stress
Once the residual stress is measured, various techniques can be employed to relax or redistribute these stresses to enhance material performance.
Heat Treatment
Heat treatment is a common method used to relieve residual stress in steel and other high-temperature materials.
Processes such as annealing, normalizing, and stress-relief annealing involve controlled heating and cooling cycles.
These cycles allow the material’s atomic structure to rearrange, reducing the internal stresses.
Vibratory Stress Relief (VSR)
Vibratory stress relief is a non-thermal method where the component is subjected to controlled vibrations.
This technique redistributes residual stresses by slightly deforming the material under vibrational loads.
VSR is advantageous when heat treatment is not feasible or could adversely affect the material properties.
Mechanical Stretching
Mechanical stretching involves the application of tensile forces to the material, effectively redistributing the residual stresses.
This method is suitable for components that can withstand mechanical deformation without affecting their function.
Ultrasonic Stress Relief
Ultrasonic stress relief uses high-frequency sound waves to relax residual stresses in materials.
This non-destructive method applies ultrasonic energy, causing localized plastic deformation and thus reducing the stress.
It is particularly effective for thin-walled or small components.
The Importance of Managing Residual Stress
In the steel industry, components are often exposed to demanding operational conditions.
Residual stress, if unmanaged, can lead to defects such as cracks, distortion, and even catastrophic failure.
By accurately measuring and managing these stresses, new employees in equipment management can ensure the reliability and longevity of steel components.
Understanding and applying appropriate stress relaxation techniques improves the overall performance and safety of structural materials.
Continuous Learning and Adaptation
For those new in the equipment management department, keeping abreast with the latest techniques in residual stress management is crucial.
Advancements in technology continuously enhance the accuracy and efficiency of stress measurement and relaxation methods.
Engaging in continuous learning, attending workshops, and collaborating with experienced professionals in the field can greatly enhance knowledge and practical skills.
In conclusion, understanding residual stress and employing effective relaxation techniques are vital skills for ensuring the structural integrity and performance of high-temperature materials in the steel industry.
By mastering these concepts, new employees can contribute significantly to operational safety and efficiency.
資料ダウンロード
QCD管理受発注クラウド「newji」は、受発注部門で必要なQCD管理全てを備えた、現場特化型兼クラウド型の今世紀最高の受発注管理システムとなります。
ユーザー登録
受発注業務の効率化だけでなく、システムを導入することで、コスト削減や製品・資材のステータス可視化のほか、属人化していた受発注情報の共有化による内部不正防止や統制にも役立ちます。
NEWJI DX
製造業に特化したデジタルトランスフォーメーション(DX)の実現を目指す請負開発型のコンサルティングサービスです。AI、iPaaS、および先端の技術を駆使して、製造プロセスの効率化、業務効率化、チームワーク強化、コスト削減、品質向上を実現します。このサービスは、製造業の課題を深く理解し、それに対する最適なデジタルソリューションを提供することで、企業が持続的な成長とイノベーションを達成できるようサポートします。
製造業ニュース解説
製造業、主に購買・調達部門にお勤めの方々に向けた情報を配信しております。
新任の方やベテランの方、管理職を対象とした幅広いコンテンツをご用意しております。
お問い合わせ
コストダウンが利益に直結する術だと理解していても、なかなか前に進めることができない状況。そんな時は、newjiのコストダウン自動化機能で大きく利益貢献しよう!
(β版非公開)