- お役立ち記事
- Resin selection criteria and molding conditions for plastic molding [Must-see for industry engineers]
月間77,185名の
製造業ご担当者様が閲覧しています*
*2025年2月28日現在のGoogle Analyticsのデータより
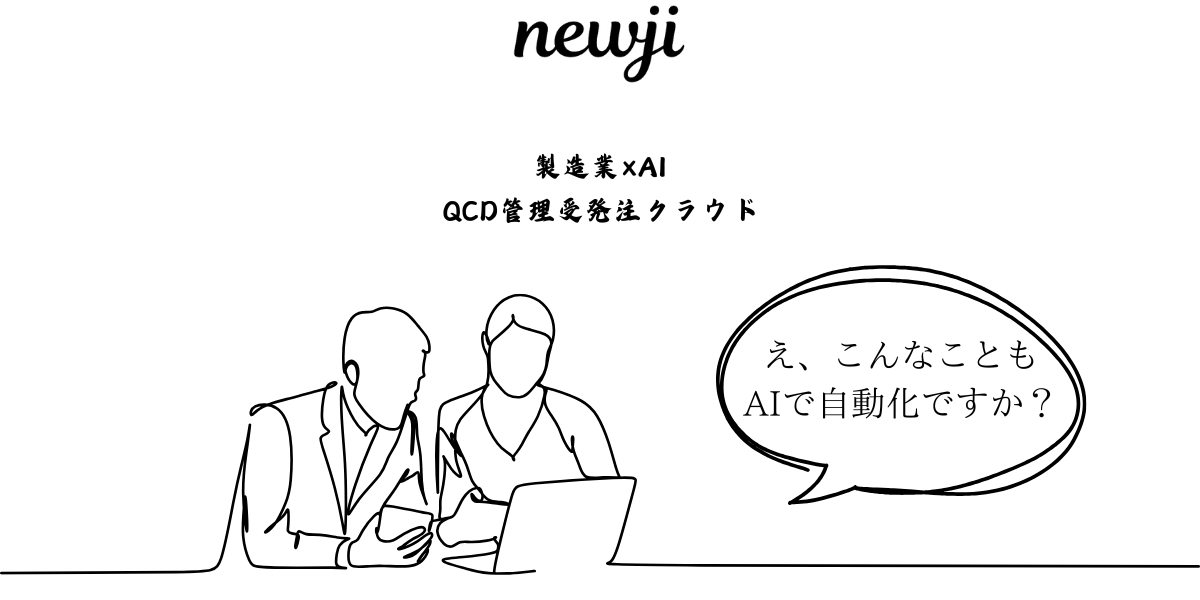
Resin selection criteria and molding conditions for plastic molding [Must-see for industry engineers]
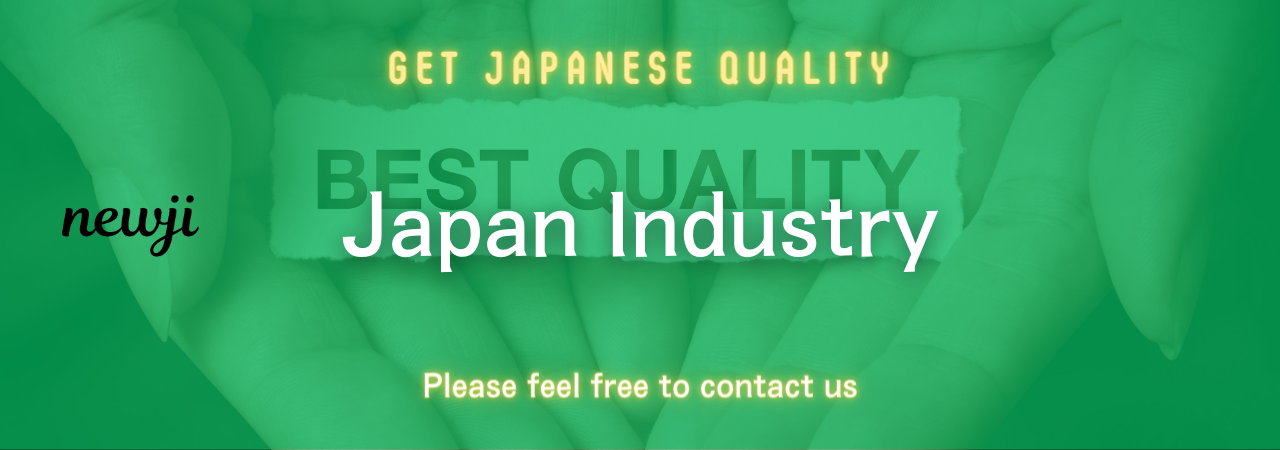
目次
Understanding Resin Selection for Plastic Molding
Plastic molding is a versatile manufacturing process employed in a variety of industries, from automotive to consumer goods.
Selecting the right resin is critical to achieving the desired properties and performance in the final product.
In this article, we will explore the criteria for choosing the appropriate resin for plastic molding, as well as the molding conditions that can impact the quality and functionality of the finished product.
Factors Influencing Resin Selection
When selecting a resin for plastic molding, engineers must consider several key factors to ensure optimal results.
These include the application’s requirements, the resin’s mechanical properties, thermal stability, chemical resistance, and cost.
1. Application Requirements
The first step in selecting a resin is understanding the specific requirements of the application.
These requirements may include factors such as strength, flexibility, color, and aesthetic appeal.
For instance, a resin used in an automotive part may need high impact resistance, while a resin used in consumer electronics might prioritize thermal stability and flame retardancy.
By clearly defining these requirements, engineers can narrow the choice of resins to those that best meet the application’s demands.
2. Mechanical Properties
Mechanical properties are a critical consideration in resin selection.
This includes aspects such as tensile strength, elongation, modulus, and impact resistance.
For applications that require robust performance under stress, resins with high tensile strength and stiffness are preferable.
On the other hand, if flexibility is key, resins with higher elongation may be more suitable.
The mechanical demands of the application will directly impact which resin is the most appropriate choice.
3. Thermal Stability
Thermal stability refers to a resin’s ability to maintain its properties under high temperatures.
This factor is particularly important in applications where heat exposure is prevalent, such as in automotive engines or electrical components.
Engineers must carefully evaluate the glass transition temperature and heat deflection temperature of the resin to ensure it can withstand the anticipated thermal conditions without deforming or losing its mechanical integrity.
4. Chemical Resistance
In some applications, plastic components may come into contact with harsh chemicals or solvents.
Therefore, chemical resistance is another crucial factor when selecting a resin.
A resin must show good compatibility with the chemical environment in which the product will operate.
Selecting a resin with poor chemical resistance can lead to product degradation, failure, or safety hazards over time.
5. Cost and Availability
Cost and availability are always important considerations in any manufacturing process, and plastic molding is no exception.
While it might be tempting to select a high-performance resin, budget constraints may dictate the final decision.
Engineers must balance the desired properties with the project’s financial limitations.
Additionally, the availability of the resin and any potential supply chain issues should be taken into account to prevent production delays.
Optimizing Molding Conditions
Once the right resin is selected, the next step is to establish the appropriate molding conditions.
These conditions, including temperature, pressure, and cycle time, significantly affect the quality of the molded product.
1. Temperature Control
Temperature is a critical factor in plastic molding that must be carefully controlled.
The molding temperature affects the viscosity of the resin, its flow into the mold, and the final properties of the product.
Too high a temperature can cause degradation, while too low a temperature might lead to incomplete filling or surface defects.
Understanding the melting and solidification behavior of the chosen resin is essential for setting the correct temperature range throughout the molding process.
2. Pressure Parameters
Pressure is another crucial aspect, as it influences the filling and packing of the resin within the mold.
Adequate pressure is necessary to ensure the resin completely fills the mold cavities, replicating the intricate details of the mold design.
If the pressure is insufficient, it may lead to voids or incomplete formation, while excessive pressure can cause flashing, where excess material flows outside the intended design space.
Balancing these parameters is crucial for achieving a high-quality molded component.
3. Cycle Time Optimization
Cycle time refers to the duration of the entire molding process, including injection, cooling, and ejection.
Optimizing cycle time is essential for enhancing productivity and reducing costs.
A shorter cycle time can increase output, but it should not compromise the quality of the finished product.
Factors like cooling time must be optimized to ensure the part solidifies adequately without introducing stresses or distortion.
Additionally, the reusability of the mold without excessive wear must be considered.
Conclusion
Selecting the right resin and optimizing molding conditions are critical steps in the plastic molding process.
By carefully considering the application’s requirements, resin properties, and molding conditions, engineers can produce high-quality molded products that meet performance standards and regulatory requirements.
A well-thought-out approach to resin selection and process optimization not only ensures product integrity but also contributes to operational efficiency and cost-effectiveness in plastic manufacturing.
By understanding these principles, industry engineers can continually enhance their processes and successfully tackle emerging challenges in the field of plastic molding.
資料ダウンロード
QCD管理受発注クラウド「newji」は、受発注部門で必要なQCD管理全てを備えた、現場特化型兼クラウド型の今世紀最高の受発注管理システムとなります。
ユーザー登録
受発注業務の効率化だけでなく、システムを導入することで、コスト削減や製品・資材のステータス可視化のほか、属人化していた受発注情報の共有化による内部不正防止や統制にも役立ちます。
NEWJI DX
製造業に特化したデジタルトランスフォーメーション(DX)の実現を目指す請負開発型のコンサルティングサービスです。AI、iPaaS、および先端の技術を駆使して、製造プロセスの効率化、業務効率化、チームワーク強化、コスト削減、品質向上を実現します。このサービスは、製造業の課題を深く理解し、それに対する最適なデジタルソリューションを提供することで、企業が持続的な成長とイノベーションを達成できるようサポートします。
製造業ニュース解説
製造業、主に購買・調達部門にお勤めの方々に向けた情報を配信しております。
新任の方やベテランの方、管理職を対象とした幅広いコンテンツをご用意しております。
お問い合わせ
コストダウンが利益に直結する術だと理解していても、なかなか前に進めることができない状況。そんな時は、newjiのコストダウン自動化機能で大きく利益貢献しよう!
(β版非公開)