- お役立ち記事
- “Revamping Japanese Manufacturing: Insights and Trends Up to October 2023”
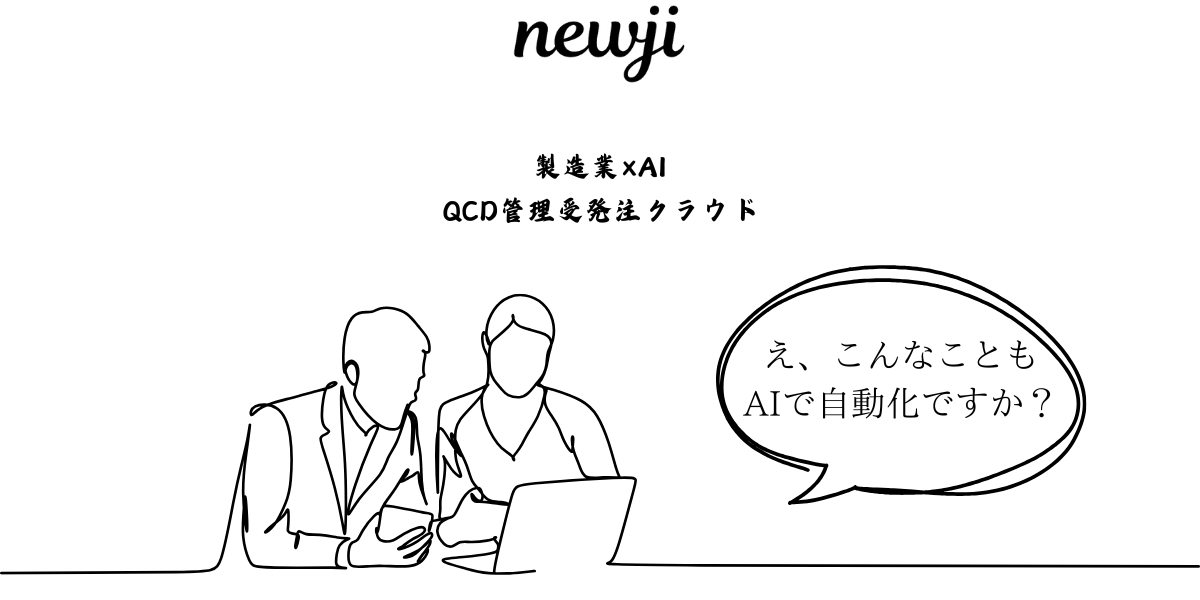
“Revamping Japanese Manufacturing: Insights and Trends Up to October 2023”
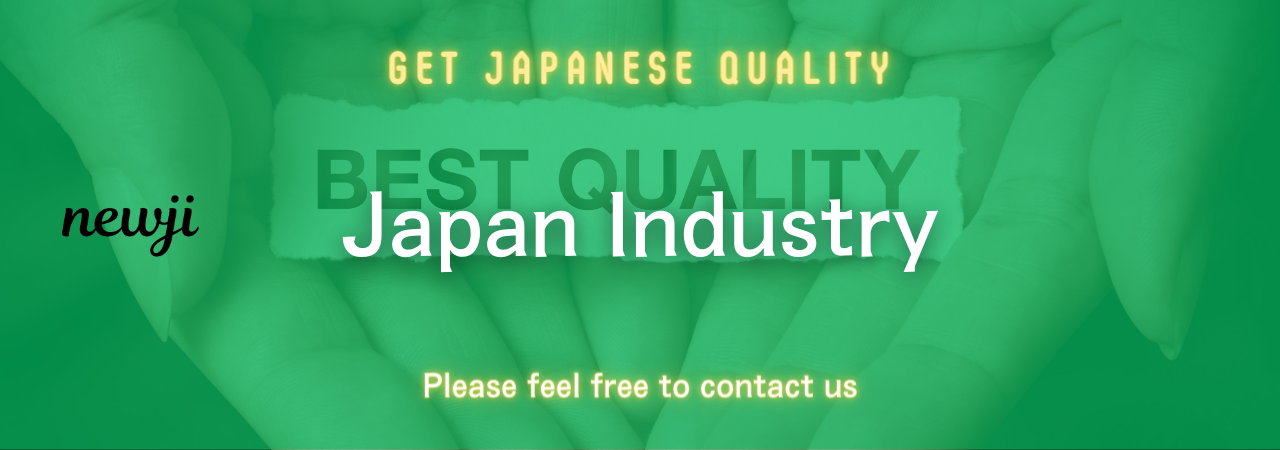
目次
Introduction to Revamping Japanese Manufacturing
The Japanese manufacturing sector has long been synonymous with quality, precision, and efficiency.
In recent years, it has undergone significant transformations to stay competitive in the global market.
This article explores the latest insights and trends in Japanese manufacturing up to October 2023.
We will delve into procurement and purchasing strategies, supplier negotiation techniques, market conditions, and best practices.
These elements are crucial for companies aiming to collaborate with Japanese suppliers and capitalize on the strengths of Japanese manufacturing.
Current Trends in Japanese Manufacturing
Embracing Industry 4.0
Japanese manufacturers are increasingly adopting Industry 4.0 technologies.
This includes the integration of Internet of Things (IoT) devices, artificial intelligence (AI), and automation in production processes.
These advancements enhance efficiency, reduce downtime, and allow for real-time monitoring and predictive maintenance.
The shift towards digitalization is a key trend, enabling manufacturers to respond swiftly to market changes and customer demands.
Sustainability Initiatives
Sustainability has become a central focus in Japanese manufacturing.
Companies are implementing eco-friendly practices such as reducing waste, minimizing energy consumption, and utilizing renewable resources.
Green manufacturing not only meets regulatory requirements but also appeals to environmentally conscious consumers.
Japanese firms are investing in technologies that support sustainable production methods and contribute to a circular economy.
Global Supply Chain Optimization
The recent global disruptions have highlighted the need for more resilient supply chains.
Japanese manufacturers are diversifying their supplier base and increasing local sourcing to mitigate risks.
There is also a greater emphasis on supply chain transparency and collaboration with suppliers to ensure reliability.
By optimizing their supply chains, Japanese companies aim to enhance their adaptability and maintain consistent production levels.
Procurement and Purchasing Strategies
Strategic Sourcing
Strategic sourcing is vital for Japanese manufacturers to secure high-quality materials at competitive prices.
This involves a comprehensive analysis of the supplier market, assessing factors such as capability, reliability, and cost-effectiveness.
By adopting strategic sourcing, companies can build long-term relationships with suppliers and ensure a stable supply of essential materials.
Cost Management
Effective cost management is crucial in procurement and purchasing.
Japanese manufacturers focus on minimizing costs without compromising quality.
This is achieved through bulk purchasing, negotiating favorable terms, and optimizing inventory levels.
Advanced analytics tools are also employed to identify cost-saving opportunities and enhance financial performance.
Risk Management
Risk management in procurement involves identifying potential disruptions and developing contingency plans.
Japanese companies assess geopolitical risks, supplier reliability, and market volatility to safeguard their supply chains.
By proactively addressing risks, manufacturers can prevent delays and maintain uninterrupted production.
Advantages and Disadvantages of Japanese Manufacturing
Advantages
Japanese manufacturing offers numerous advantages, including:
- Quality and Precision: Japanese products are renowned for their superior quality and meticulous attention to detail.
- Advanced Technology: Utilization of cutting-edge technologies enhances efficiency and product innovation.
- Strong Supplier Relationships: Long-term partnerships with suppliers ensure reliability and consistency in materials.
- Workforce Expertise: Highly skilled and disciplined workforce contributes to high productivity and low defect rates.
Disadvantages
Despite its strengths, Japanese manufacturing also faces certain challenges:
- High Labor Costs: Skilled labor comes at a premium, impacting overall production costs.
- Cultural Barriers: Differences in business practices and communication styles can pose challenges for international partners.
- Rigid Work Structures: Traditional approaches may limit flexibility and slow down decision-making processes.
- Aging Workforce: The demographic shift is leading to a shortage of young talent in the manufacturing sector.
Supplier Negotiation Techniques
Building Trust and Long-term Relationships
In Japanese business culture, trust and long-term relationships are paramount.
Negotiations focus on mutual benefits and establishing a foundation for ongoing collaboration.
Demonstrating reliability and commitment can lead to more favorable terms and stronger partnerships.
Understanding Japanese Business Etiquette
Respecting Japanese business etiquette is essential during negotiations.
This includes punctuality, exchanging business cards with both hands, and maintaining a formal demeanor.
Understanding and adhering to these cultural norms can facilitate smoother negotiations and foster respect.
Value-based Negotiation
Japanese negotiations often emphasize value over price alone.
Suppliers seek to provide solutions that add value to their partners’ businesses.
Focusing on the overall value proposition, including quality, service, and reliability, can lead to more successful negotiations.
Patience and Persistence
Patience is a critical trait in Japanese negotiations.
Decisions are made collectively and require consensus, often taking longer than in other cultures.
Being patient and persistent, while maintaining open communication, can help navigate the negotiation process effectively.
Market Conditions Affecting Japanese Manufacturing
Global Economic Environment
The global economic climate, including trade policies and economic growth rates, significantly impacts Japanese manufacturing.
Trade tensions, tariffs, and changes in consumer demand can influence production strategies and market positioning.
Japanese companies must stay agile to respond to these external factors and maintain competitiveness.
Technological Advancements
Rapid technological advancements shape the manufacturing landscape.
Japanese manufacturers must continuously invest in the latest technologies to stay ahead.
Adopting innovations such as robotics, AI, and advanced materials is essential for maintaining market leadership.
Workforce Dynamics
The availability of skilled labor is a critical factor in Japanese manufacturing.
An aging population and declining birth rates pose challenges in maintaining a robust workforce.
Companies are increasingly investing in training and automation to address labor shortages and enhance productivity.
Environmental Regulations
Strict environmental regulations in Japan require manufacturers to comply with sustainability standards.
This includes reducing emissions, managing waste, and adopting green technologies.
Compliance not only ensures regulatory adherence but also enhances the company’s reputation and appeal to eco-conscious consumers.
Best Practices in Japanese Manufacturing
Lean Manufacturing
Lean manufacturing principles are widely adopted in Japan to eliminate waste and optimize processes.
Techniques such as Just-In-Time (JIT) production and Kaizen continuous improvement contribute to high efficiency and cost-effectiveness.
Total Quality Management (TQM)
TQM emphasizes quality in every aspect of production.
Japanese manufacturers implement rigorous quality control measures and encourage employee involvement in quality improvement initiatives.
This leads to superior product quality and customer satisfaction.
Collaborative Supplier Relationships
Building collaborative relationships with suppliers is a hallmark of Japanese manufacturing.
Regular communication, joint problem-solving, and shared goals foster a cooperative environment.
This collaboration ensures a reliable supply chain and drives mutual growth.
Employee Engagement and Training
Investing in employee training and engagement enhances workforce capabilities and morale.
Japanese companies prioritize continuous learning and skill development, enabling employees to contribute effectively to the manufacturing process.
Challenges and Solutions in International Procurement
Overcoming Cultural Differences
Cultural differences can pose challenges in international procurement.
Understanding and respecting Japanese business customs and communication styles is essential for successful collaboration.
Providing cross-cultural training to procurement teams can bridge cultural gaps and improve interactions with Japanese suppliers.
Ensuring Supply Chain Resilience
Building a resilient supply chain is crucial in the face of global uncertainties.
Japanese manufacturers are diversifying their supplier base and investing in local sourcing to reduce dependency on a single source.
Implementing risk management strategies and developing contingency plans can enhance supply chain resilience.
Maintaining Competitive Pricing
Balancing cost and quality is a constant challenge in procurement.
Japanese suppliers are known for their high standards, which can come at a higher price.
Negotiating favorable terms, exploring bulk purchasing discounts, and leveraging long-term partnerships can help maintain competitive pricing.
Future Outlook for Japanese Manufacturing
Innovation and R&D
Investing in research and development is key to sustaining innovation in Japanese manufacturing.
Continued focus on developing new technologies and improving existing processes will drive future growth and competitiveness.
Global Expansion
Japanese manufacturers are expanding their global presence to tap into new markets.
Establishing manufacturing facilities abroad and forming international partnerships can help mitigate risks and increase market reach.
Adapting to Digital Transformation
The ongoing digital transformation will shape the future of Japanese manufacturing.
Embracing digital tools and data-driven decision-making will enhance operational efficiency and enable manufacturers to adapt to evolving market demands.
Conclusion
Revamping Japanese manufacturing involves embracing modern technologies, fostering sustainable practices, and optimizing procurement and purchasing strategies.
Understanding the unique advantages and addressing the challenges inherent in Japanese manufacturing can lead to successful international collaborations.
By adopting best practices, enhancing supplier relationships, and staying attuned to market conditions, companies can fully leverage the strengths of Japanese manufacturing.
As the industry continues to evolve, staying informed about the latest trends and insights will be critical for sustained success and growth.
資料ダウンロード
QCD調達購買管理クラウド「newji」は、調達購買部門で必要なQCD管理全てを備えた、現場特化型兼クラウド型の今世紀最高の購買管理システムとなります。
ユーザー登録
調達購買業務の効率化だけでなく、システムを導入することで、コスト削減や製品・資材のステータス可視化のほか、属人化していた購買情報の共有化による内部不正防止や統制にも役立ちます。
NEWJI DX
製造業に特化したデジタルトランスフォーメーション(DX)の実現を目指す請負開発型のコンサルティングサービスです。AI、iPaaS、および先端の技術を駆使して、製造プロセスの効率化、業務効率化、チームワーク強化、コスト削減、品質向上を実現します。このサービスは、製造業の課題を深く理解し、それに対する最適なデジタルソリューションを提供することで、企業が持続的な成長とイノベーションを達成できるようサポートします。
オンライン講座
製造業、主に購買・調達部門にお勤めの方々に向けた情報を配信しております。
新任の方やベテランの方、管理職を対象とした幅広いコンテンツをご用意しております。
お問い合わせ
コストダウンが利益に直結する術だと理解していても、なかなか前に進めることができない状況。そんな時は、newjiのコストダウン自動化機能で大きく利益貢献しよう!
(Β版非公開)